Help with a stuck torx bolt
Discussion
I am trying to remove the front of an Audi S4
A couple of years ago my mechanic warned me about some stuck bolts that stopped him being able to investigate further on the air-conditioning, he wasn't very clear which ones but I think I have now found them.
I got 1 off that was a bit loose but the rest would not budge.
There are plastic bits so I don't think heat was an option.
I used a cold spray to try and get them to break free and lots of penetrating oil but even that didn't help.
I had a 170nm impact driver and it wasn't able to make them budge.
I tried the breaker bar, but the torx head on the tool snapped and now I have this
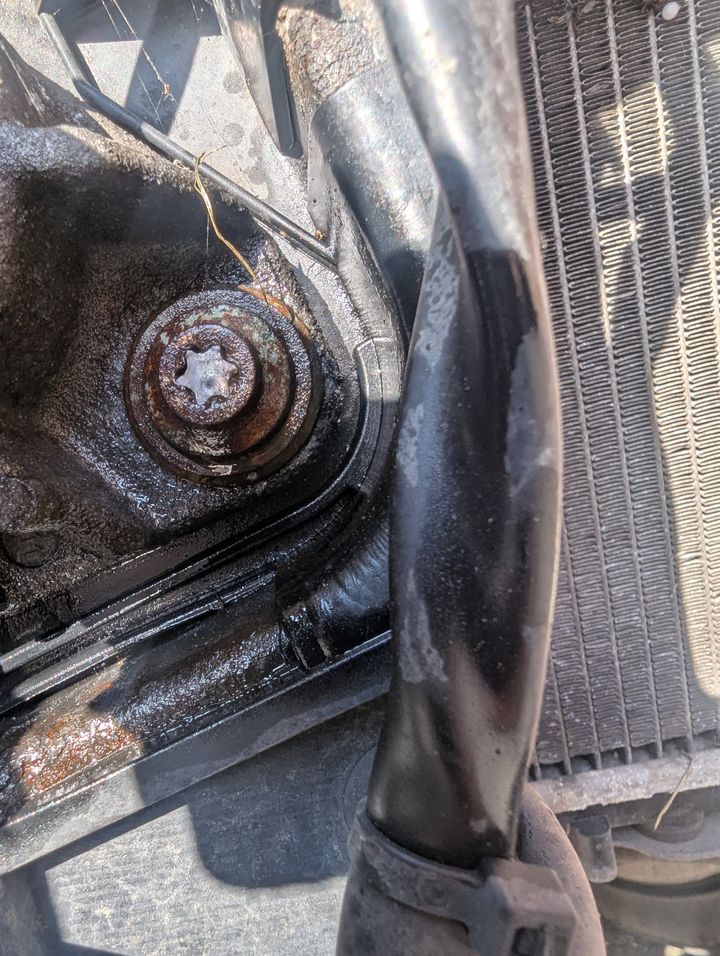
Any idea what I should do to get that out and then what I should do about these bolts?
Do I need to get it out carefully and try again with a stronger tool or am I just going to get the same out come?
A couple of years ago my mechanic warned me about some stuck bolts that stopped him being able to investigate further on the air-conditioning, he wasn't very clear which ones but I think I have now found them.
I got 1 off that was a bit loose but the rest would not budge.
There are plastic bits so I don't think heat was an option.
I used a cold spray to try and get them to break free and lots of penetrating oil but even that didn't help.
I had a 170nm impact driver and it wasn't able to make them budge.
I tried the breaker bar, but the torx head on the tool snapped and now I have this
Any idea what I should do to get that out and then what I should do about these bolts?
Do I need to get it out carefully and try again with a stronger tool or am I just going to get the same out come?
If you tap that with a hammer & centre-punch it will likely come out, then you definitely need heat to make the job as easy as possible.
Either that or get something like these
https://www.ebay.co.uk/itm/405601418782?_skw=bahco...
on the outside of the bolt just to get it to move, you would be astonished at the amount of torque you can get on a fairly fine point with them.
Either that or get something like these
https://www.ebay.co.uk/itm/405601418782?_skw=bahco...
on the outside of the bolt just to get it to move, you would be astonished at the amount of torque you can get on a fairly fine point with them.
e-honda said:
Is the part the bolt goes through plastic? If not, and it's just a case of plastic parts being dangerously close, you can use wet rags to protect the plastics. Just get them soaking wet and drape them over the plastics wherever they need protection.You can also get a special gel that you paint on, never used it myself though.
Another thought, would one of those old school percussion impact drivers do any better? I noticed the one in Halfords costs about the same as a random eBay one.
If that fails, in a similar approach to the stilson-like pliers, I wonder if a stud removal tool might do the trick. This sort of thing:
https://www.gsfcarparts.com/products/stud-remover-...
That will only work if the head of the fastener is smaller than the aperture for studs, but tools like this bite down with toughened teeth (much like the special pliers) and get tighter the more torque you apply.
If that fails, in a similar approach to the stilson-like pliers, I wonder if a stud removal tool might do the trick. This sort of thing:
https://www.gsfcarparts.com/products/stud-remover-...
That will only work if the head of the fastener is smaller than the aperture for studs, but tools like this bite down with toughened teeth (much like the special pliers) and get tighter the more torque you apply.
e-honda said:
Thanks the center punch had it straight out
Works every time if the head is in reasonable condition, well done.As someone else implied above, all that will be holding it is likely a coating of rust on the threads causing extra stiction.
Using the same centre-punch give the torx head a few whacks at the bottom of the hole to see if you can break the hold of the rust.
Edited by E-bmw on Saturday 12th April 08:37
e-honda said:
I am going to get a more powerful impact driver and a stronger bit.
That combined with the over night it's had to let the oil penetrate will either be enough or I'll strip the head or snap another tool.
I would be careful with an impact driver on that, the head looks quite rounded from your pics, can you get to the other end off the bolt in any way, if you can a wire brush on the threads and lots of lube on them might help.That combined with the over night it's had to let the oil penetrate will either be enough or I'll strip the head or snap another tool.
If not then as said previously pipe grips might work.
Snapped another bit today
Heads are still good enough i just can't find a bit strong enough, but i suspect once i do it will round the heads off.
There is a big flange surface and i think it is against aluminum so galvanic corrosion will have basically welded them in place
I was considering something like this
https://www.toolstation.com/minotaur-bolt-grip-nut...
I don't know it it will have enough to grip into but its not super thin so it should work if these sort of things are any good
If that doesn't work I am thinking of getting a mobile welder to weld some bigger nuts on then the combination of a bigger head and heat from the weld should make them come off easy.
Heads are still good enough i just can't find a bit strong enough, but i suspect once i do it will round the heads off.
There is a big flange surface and i think it is against aluminum so galvanic corrosion will have basically welded them in place
I was considering something like this
https://www.toolstation.com/minotaur-bolt-grip-nut...
I don't know it it will have enough to grip into but its not super thin so it should work if these sort of things are any good
If that doesn't work I am thinking of getting a mobile welder to weld some bigger nuts on then the combination of a bigger head and heat from the weld should make them come off easy.
e-honda said:
If that doesn't work I am thinking of getting a mobile welder to weld some bigger nuts on then the combination of a bigger head and heat from the weld should make them come off easy.
I thought you said you couldn't get heat on it 
If you think there's room to weld without melting your plastics, I'd give serious consideration to the wet rags on the plastics and a blowtorch.
Were you using impact grade torx bits?
That and a big breaker bar with a bit of patience and "lefty loosey, righty tighty" wiggling might serve. Especially if you have given it enough PlusGas or similar.
Also I wouldn't worry too much about very localised heat damage to the plastic. You can always make it up with a big stainless penny washer.
Good luck.
That and a big breaker bar with a bit of patience and "lefty loosey, righty tighty" wiggling might serve. Especially if you have given it enough PlusGas or similar.
Also I wouldn't worry too much about very localised heat damage to the plastic. You can always make it up with a big stainless penny washer.
Good luck.
donkmeister said:
I thought you said you couldn't get heat on it 
If you think there's room to weld without melting your plastics, I'd give serious consideration to the wet rags on the plastics and a blowtorch.
If I put a blow torch on it I don't think I'd get away with it even if I put the flame right on the head there will be a lot of heat spreading, a welder would be a lot more focused on the exact spot and for a very short time.
If you think there's room to weld without melting your plastics, I'd give serious consideration to the wet rags on the plastics and a blowtorch.
I might give wet rags a go, although I am a bit worried about what bits of plastic or on the other side or even sandwiched in the middle.
Error_404_Username_not_found said:
Were you using impact grade torx bits?
That and a big breaker bar with a bit of patience and "lefty loosey, righty tighty" wiggling might serve. Especially if you have given it enough PlusGas or similar.
Also I wouldn't worry too much about very localised heat damage to the plastic. You can always make it up with a big stainless penny washer.
Good luck.
The one I bought today was an impact driver one.That and a big breaker bar with a bit of patience and "lefty loosey, righty tighty" wiggling might serve. Especially if you have given it enough PlusGas or similar.
Also I wouldn't worry too much about very localised heat damage to the plastic. You can always make it up with a big stainless penny washer.
Good luck.
I used a 190nm DeWalt impact driver held it down for a good 5 seconds a couple of times on each bolt after giving them all a good few smacks with with a hammer, they just weren't budging.
Gave the big breaker bar a go and it just snapped the end off again, and I am not really surprised, it's a huge amount of force going into what is probably no more than 5mm at the tip of it
How to get very localised heat in the bolt.
Do you have a stick welder? Preferably an old AC hobby-buzzbox type. Maybe you can borrow one or find one on FB or something.
If you were local I'd lend you the one under my bench that I no longer use.
Put a big electrode in it, wind the amps up to max and whack the end of the stick into the hollow.
It will immediately stick. Hold it there 10 seconds or so, ignoring any sympathy you might have for the welder. Then shut off the power.
This will heat the bolt from the core outwards way more than the surrounding plastic.
It's chancy because you absolutely need to get it unscrewed before any more damage happens.
I've released sheared head studs from A series engines (horrible things) several times like this. Broken taps too. But it's a bit all or nothing.
Otherwise, spark erosion. That can basically hollow the bolt out until fatally weakened. It's DIY do-able but best left to a specialist.
Edit: PS; try going the wrong way with the chatter gun for a second first. But I'd prefer the breaker bar and patience approach personally.
Do you have a stick welder? Preferably an old AC hobby-buzzbox type. Maybe you can borrow one or find one on FB or something.
If you were local I'd lend you the one under my bench that I no longer use.
Put a big electrode in it, wind the amps up to max and whack the end of the stick into the hollow.
It will immediately stick. Hold it there 10 seconds or so, ignoring any sympathy you might have for the welder. Then shut off the power.
This will heat the bolt from the core outwards way more than the surrounding plastic.
It's chancy because you absolutely need to get it unscrewed before any more damage happens.
I've released sheared head studs from A series engines (horrible things) several times like this. Broken taps too. But it's a bit all or nothing.
Otherwise, spark erosion. That can basically hollow the bolt out until fatally weakened. It's DIY do-able but best left to a specialist.
Edit: PS; try going the wrong way with the chatter gun for a second first. But I'd prefer the breaker bar and patience approach personally.
Edited by Error_404_Username_not_found on Saturday 12th April 22:28
Gassing Station | Home Mechanics | Top of Page | What's New | My Stuff