Help with my hydraulic Clutch
Discussion
Hi all, I need help! I'm pulling my hair out here and starting to think about just stripping the whole car and getting rid of the problem all together. Some background...
Saxo Turbo, makes 300lbft trq.
I was running a 184mm lightweight flywheel on 7.25" twin plate Tilton clutch. 400lb release pressure, rated to 400lbft trq. No issues with this setup but it was poor for refinement and driveability. It was rattly and unsprung so harsh pullaways, juddering etc. I wanted to really improve on this to get the general driveability better and stop that darn twin plate rattle! Clutch release was via cable. Heavy ish but perfectly fine in terms of pedal weight.
I made the call to remove the twin plate and move to a 200mm single plate Helix clutch and suitable 200mm flywheel (little or no rattle expected here) and sprung clutch (better driveability). However, moving to single plate means I need a much higher clamp load. 790lb release load to be precise. You don't need to be a genius to know this is nearly double the old clutch and pedal feel would be terrible.
So in theory a logical step to remove the two issues at the sacrifice of a massive increase in release load (pedal effort).
To combat that I thought i'd look at changing to hydraulic actuation. However, it's a road car. I don't want a hydraulic pedal box in the car. Additionally, to fit this it's no small job and likely an engine out job/interior strip etc. I came up with what I thought was a clever idea. Why not use the cable to actuate a master cylinder which drives the slave.
I developed a prototype based on some existing bracketry in which the pull action cable drives a master cylinder. I've done the maths on master cylinder volume and slave volume for the required travel and a 0.75 master is just fine. Also backed up by quite a lot of other people in the same field using the same slave. Wilwood pull type.
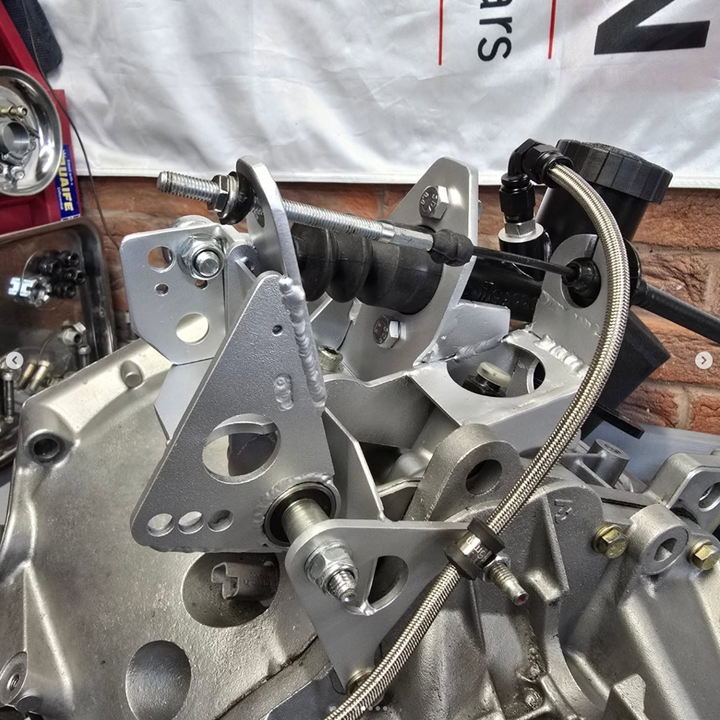
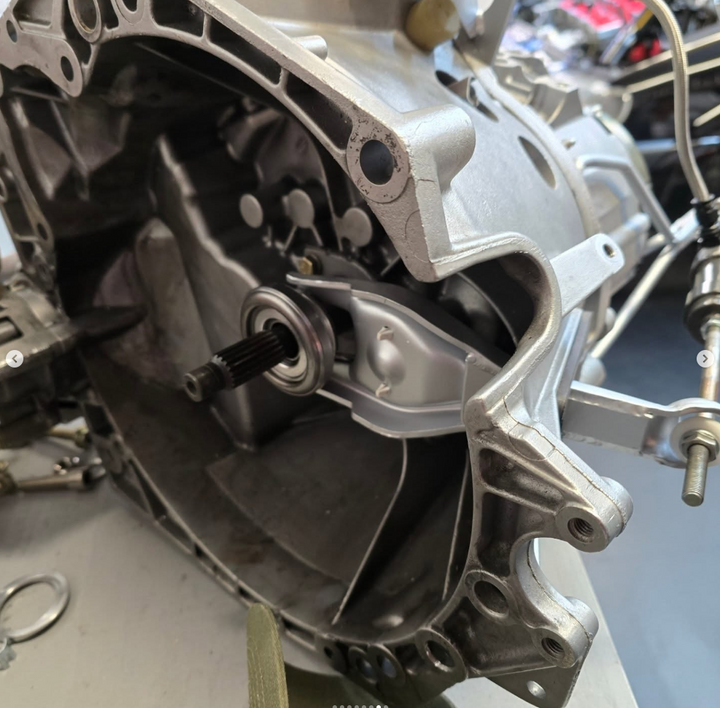
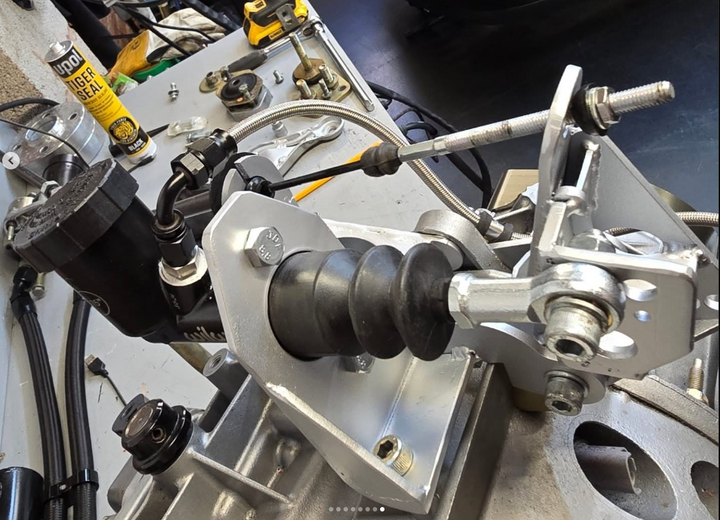
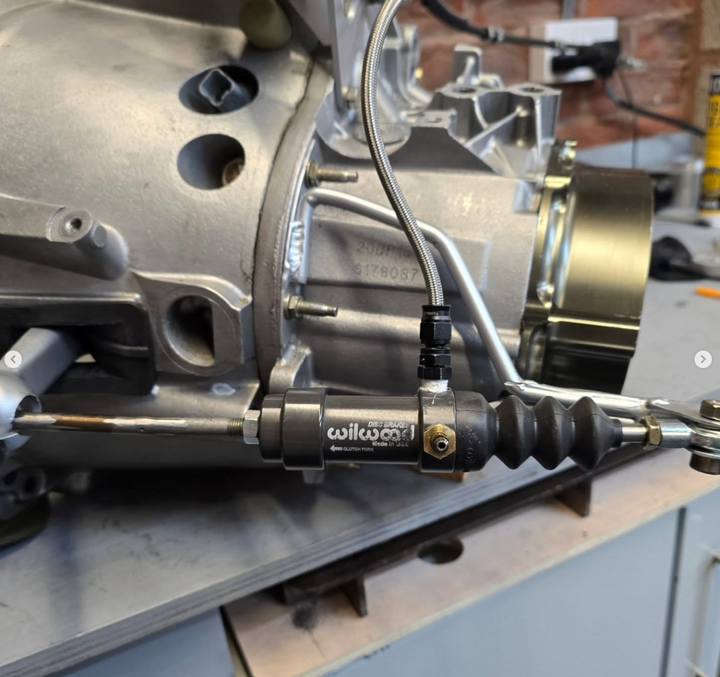
So installing this setup I have two problems:
1. Travel at the slave cylinder is too small, therefore the fork doesn't move enough to depress the clutch. I've bled the system 3 or 4 times, in isolation the travel at the slave is ~30mm when not attached to a load. I've tried a 0.75 and a 1.0 master and both behave the same. I've tried a longer clutch fork for more leverage but no matter what I do, the hydraulic setup just cannot depress the clutch. I get some movement, just not enough.
2. Pedal feel is really really really heavy! I can combat that a little by raising the height of the cable actuation over the master cylinder but this means I don't then depress the master cylinder all the way which means not enough travel at the slave.
So right now...i can get a good pedal but not enough travel at the slave, or heavy pedal and not enough travel at the slave.
I've spent an obscene amount of money to switch flywheel and clutch plus all the hydro kit and hoses etc so im keen to get this working. But right now Ive got a car that won't engage gear.
Going back to the cable actuation is still possible but the pedal is just silly heavy, bordering on undriveable.
Please help before I burn it to the ground!?
Saxo Turbo, makes 300lbft trq.
I was running a 184mm lightweight flywheel on 7.25" twin plate Tilton clutch. 400lb release pressure, rated to 400lbft trq. No issues with this setup but it was poor for refinement and driveability. It was rattly and unsprung so harsh pullaways, juddering etc. I wanted to really improve on this to get the general driveability better and stop that darn twin plate rattle! Clutch release was via cable. Heavy ish but perfectly fine in terms of pedal weight.
I made the call to remove the twin plate and move to a 200mm single plate Helix clutch and suitable 200mm flywheel (little or no rattle expected here) and sprung clutch (better driveability). However, moving to single plate means I need a much higher clamp load. 790lb release load to be precise. You don't need to be a genius to know this is nearly double the old clutch and pedal feel would be terrible.
So in theory a logical step to remove the two issues at the sacrifice of a massive increase in release load (pedal effort).
To combat that I thought i'd look at changing to hydraulic actuation. However, it's a road car. I don't want a hydraulic pedal box in the car. Additionally, to fit this it's no small job and likely an engine out job/interior strip etc. I came up with what I thought was a clever idea. Why not use the cable to actuate a master cylinder which drives the slave.
I developed a prototype based on some existing bracketry in which the pull action cable drives a master cylinder. I've done the maths on master cylinder volume and slave volume for the required travel and a 0.75 master is just fine. Also backed up by quite a lot of other people in the same field using the same slave. Wilwood pull type.
So installing this setup I have two problems:
1. Travel at the slave cylinder is too small, therefore the fork doesn't move enough to depress the clutch. I've bled the system 3 or 4 times, in isolation the travel at the slave is ~30mm when not attached to a load. I've tried a 0.75 and a 1.0 master and both behave the same. I've tried a longer clutch fork for more leverage but no matter what I do, the hydraulic setup just cannot depress the clutch. I get some movement, just not enough.
2. Pedal feel is really really really heavy! I can combat that a little by raising the height of the cable actuation over the master cylinder but this means I don't then depress the master cylinder all the way which means not enough travel at the slave.
So right now...i can get a good pedal but not enough travel at the slave, or heavy pedal and not enough travel at the slave.
I've spent an obscene amount of money to switch flywheel and clutch plus all the hydro kit and hoses etc so im keen to get this working. But right now Ive got a car that won't engage gear.
Going back to the cable actuation is still possible but the pedal is just silly heavy, bordering on undriveable.
Please help before I burn it to the ground!?
You need to get a sense of the force and travel required at the clutch to release and engage it, and what you want that to translate to at the pedal.
How much of the stroke of the original clutch pedal were you using to actually engage and release the clutch?
If you're trying to double the force at the clutch over the same travel you need to increase either the working stroke or the force at the pedal. If it was previously only using a small part of the overall stroke, you may be able to achieve that. But if you were already using the whole pedal stroke, something else will have to give.
By introducing the extra mechanism and bushes and bearings and so on in your cable-to-hydraulic hybrid you've introduced more flexibility, which will increase the travel required at the pedal for a given travel at the clutch. It's hard to see how much flex and friction that mechanism will cause, but it might be significant.
How much of the stroke of the original clutch pedal were you using to actually engage and release the clutch?
If you're trying to double the force at the clutch over the same travel you need to increase either the working stroke or the force at the pedal. If it was previously only using a small part of the overall stroke, you may be able to achieve that. But if you were already using the whole pedal stroke, something else will have to give.
By introducing the extra mechanism and bushes and bearings and so on in your cable-to-hydraulic hybrid you've introduced more flexibility, which will increase the travel required at the pedal for a given travel at the clutch. It's hard to see how much flex and friction that mechanism will cause, but it might be significant.
Not force, but they will be using up travel - hence making it less likely the clutch will release fully if you are marginal on travel.
How much of the pedal travel is actually being used to operate the clutch?
In other words, looking at the range of clutch actuator travel from no contact on release bearing to clutch fully released, where does that lie on the range of travel of the pedal?
How much of the pedal travel is actually being used to operate the clutch?
In other words, looking at the range of clutch actuator travel from no contact on release bearing to clutch fully released, where does that lie on the range of travel of the pedal?
Ok so I've perhaps realised something in raising this topic. Which in itself is a good thing. I really appreciate the input from you guys.
I need to measure to make sure but I think that 100% travel at the pedal = a fully depressed master cylinder. 1:1 ratio of cable pull:master cyl depression.
As sad earlier this meant a very heavy pedal. The reason I went to a 1.0" bore (knowing it would make pedal heavier) is because;
When attempting to reduce pedal input force I raised the clutch cable over the master cylinder. Essentially creating a bigger lever to pull it. The pedal feel went from impossible to "normal". But it came at the cost of not depressing the master all the way. My logic here was that to achieve the slave travel i needed, it cooud be achieved with a larger bore master and simply not using all it's travel.
My sums said that 0.75 master would yield 0.92" of movement at the slave.
A 1.0 master would yield 1.63" of movement at the slave.
Given the slave would max out at 1.25" of stroke i therefore wouldn't need to press the master all the way.
Going to a smaller bore Master wouldn't provide the fluid volume to move the slave. This was my first thought but fluid volume was the issue. I need around 25mm of slave travel.
However, even with a raised cable and not using the full stroke of the master (still 100% pedal) It's still really heavy.
Ive checked the bearing heights a hundred times
Bled the system numerous times
Greased everything
Various lengths of clutch fork to provide bigger or shorter levers.
I need to measure to make sure but I think that 100% travel at the pedal = a fully depressed master cylinder. 1:1 ratio of cable pull:master cyl depression.
As sad earlier this meant a very heavy pedal. The reason I went to a 1.0" bore (knowing it would make pedal heavier) is because;
When attempting to reduce pedal input force I raised the clutch cable over the master cylinder. Essentially creating a bigger lever to pull it. The pedal feel went from impossible to "normal". But it came at the cost of not depressing the master all the way. My logic here was that to achieve the slave travel i needed, it cooud be achieved with a larger bore master and simply not using all it's travel.
My sums said that 0.75 master would yield 0.92" of movement at the slave.
A 1.0 master would yield 1.63" of movement at the slave.
Given the slave would max out at 1.25" of stroke i therefore wouldn't need to press the master all the way.
Going to a smaller bore Master wouldn't provide the fluid volume to move the slave. This was my first thought but fluid volume was the issue. I need around 25mm of slave travel.
However, even with a raised cable and not using the full stroke of the master (still 100% pedal) It's still really heavy.
Ive checked the bearing heights a hundred times
Bled the system numerous times
Greased everything
Various lengths of clutch fork to provide bigger or shorter levers.
Evo Sean said:
I'd be keen to see what they've done? Could you share it?
I think the bits are here: https://www.retrofication.co.uk/MK1DIYHydro.htmlEvo Sean said:
I'd be keen to see what they've done? Could you share it?
I think the bits are here: https://www.retrofication.co.uk/MK1DIYHydro.htmlGreenV8S said:
Fiddling with the mechanical versus hydraulic leverage doesn't change the fundamental problem of force times distance.
In the current set-up, where in the range of pedal travel does the release bearing contact the clutch fingers and where does it fully release the clutch?
The clutch requires 7.5mm of depression to release. I have the release bearing with around 1-2mm of free travel. In the range of the pedal, the release bearing is in contact almost straight away. To be able to depress the clutch spring i'd need full travel of the pedal. Which I probably understand is quite poor?In the current set-up, where in the range of pedal travel does the release bearing contact the clutch fingers and where does it fully release the clutch?
Evo Sean said:
The clutch requires 7.5mm of depression to release. I have the release bearing with around 1-2mm of free travel. In the range of the pedal, the release bearing is in contact almost straight away. To be able to depress the clutch spring i'd need full travel of the pedal. Which I probably understand is quite poor?
Hmm. I take it you have ruled out increasing the clutch pedal travel. Roughly how much travel do you have currently? Roughly how much force does the pedal take? My single plate clutch (on a RV8) takes more torque than that - it's a pretty heavy clutch pedal but completely usable as a daily drive. You've already used the whole pedal travel and don't seem to have any wasted travel at the clutch, so all the easy options are off the table. You may be able to arrange the non-linear leverage effects so the pedal gets lighter around the engagement area, but mainly you'd be hoping to eliminate flex and friction now.
Gassing Station | Home Mechanics | Top of Page | What's New | My Stuff