Scotchloks or something else?
Discussion
donkmeister said:
scotchloks are the common approach.
I'd dispute that they're a common approach. They provide a terrible solution which damages the wiring, leaves it vulnerable to corrosion and fatigue damage, and gives a mediocre connection. The only people who use them are bodgers.If you want to splice into a circuit then cut it and use a butt splice connector to insert your wire.
There are many ways of doing what you want & back in the 70's scotchloks were widely used as an answer & they were then & always have been the worst possible way to do the job for all of the above reasons & more.
Many will argue the merits of their way of doing it but my personal method would be to use a soldered joint for something permanent.
Many will argue the merits of their way of doing it but my personal method would be to use a soldered joint for something permanent.
I'm starting to wonder if Wago 221s would be effective. My only fear is that as they aren't designed for automotive use, will they vibrate their way free over the years?
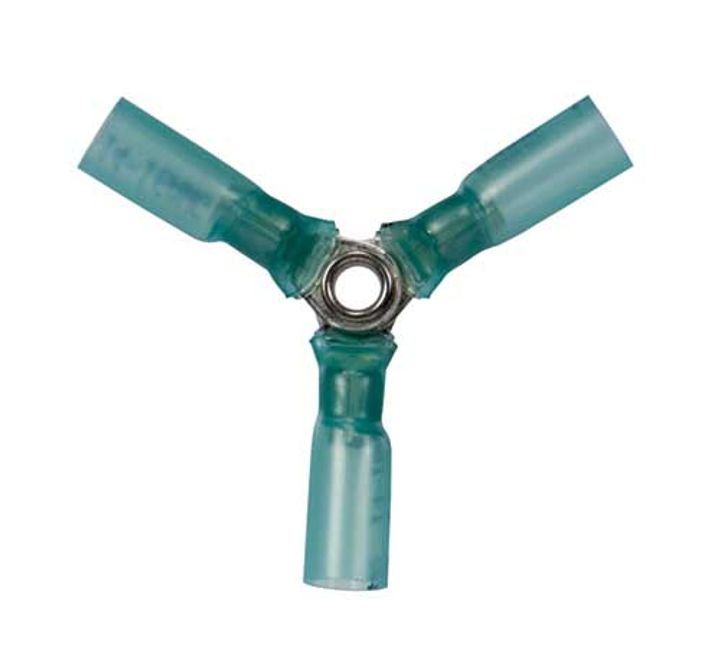
I've used piggyback spade connectors in the past but wasn't too keen on them for neatness.
GreenV8S said:
If you want to splice into a circuit then cut it and use a butt splice connector to insert your wire.
I'm a dab-hand with a ratchet crimper, but are three-way butt splices any good? I confess I didn't know these were a thing but I've googled it and I'm not convinced that I will be able to heatshrink the central portion particularly well. I've used piggyback spade connectors in the past but wasn't too keen on them for neatness.
E-bmw said:
Many will argue the merits of their way of doing it but my personal method would be to use a soldered joint for something permanent.
Solder is a big no-no on automotive harness applications due to the brittleness of a wire-to-wire solder joint. It would be the easiest way for these joints!jfdi said:
My Adria caravan wiring makes extensive use of wago connectors and I'm sure that gets plenty of vibration when being towed. Wagos hold the wire with spring tension so should be better than any other mechanical connector.
That's reassuring. I'll use Wagos and ensure to put it somewhere I can inspect easily enough. If I get a whiff of movement I can replace with something else.donkmeister said:
I'm a dab-hand with a ratchet crimper, but are three-way butt splices any good? I confess I didn't know these were a thing but I've googled it and I'm not convinced that I will be able to heatshrink the central portion particularly well.
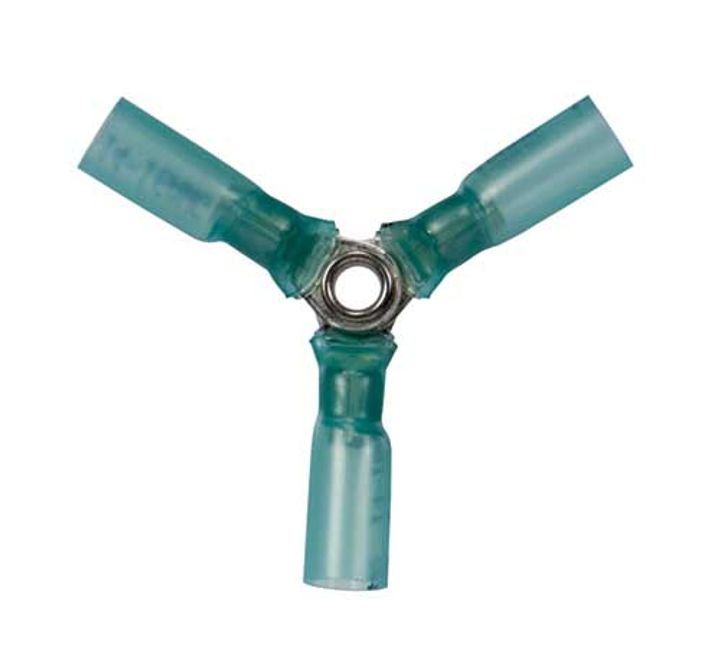
I've used piggyback spade connectors in the past but wasn't too keen on them for neatness.
I've never seen one of those before but I don't like it due to the centre. I've used piggyback spade connectors in the past but wasn't too keen on them for neatness.
My preferred method is a straight butt connector, with 2 wires in one side and 1 in the other. I like a mechanical crimp and heat shrink (with adhesive/sealant inside) over . I prefer to use the uninsulated butt connectors with separate heat shrink.
Soldering can be fine too but this depends on location. In the centre of a loom (where the joint will be supported by other cables) it won't be a problem. In an unsupported section of loom (particularly one that moves) connected to a rigid component I wouldn't trust it. If someone isn't technically minded enough to assess the difference then they would be better off sticking to mechanical crimps everywhere. I think this may be where the aversion to soldered joints comes from.
For permanent connections into a wiring harness soldering is far and away the best option. just be aware that the soldered joint is vulnerable to vibration failure so the best way to avoid any issues is to twist the wires together including both stripped ends where the solder will go and also 10mm of the insulation as well. After soldering cover the joint with heat shrink tuning.
Tye Green said:
For permanent connections into a wiring harness soldering is far and away the best option.
It used to be commonly thought that a good solder joint was better than a good crimped joint, but even organisations, such as NASA which used to be the definitive source for best practice for soldered joints, no longer recommend soldered joints at all. No main stream car manufacturers use soldered joints these days and I understand they are also never used on aircraft.For permanent connections into a wiring harness a properly crimped and sealed joint is far and away the best option.
GreenV8S said:
Tye Green said:
For permanent connections into a wiring harness soldering is far and away the best option.
It used to be commonly thought that a good solder joint was better than a good crimped joint, but even organisations, such as NASA which used to be the definitive source for best practice for soldered joints, no longer recommend soldered joints at all. No main stream car manufacturers use soldered joints these days and I understand they are also never used on aircraft.For permanent connections into a wiring harness a properly crimped and sealed joint is far and away the best option.
Every circuit board in the world has soldered components, even those on the shuttle and the spaceships sent to the far ends of the galaxies…
A crimped joint or a soldered joint can be either good or crap it’s just a question of making the joint suited to the environment (=the definition of quality). In a car, which is the OPs environment, there is e.g. a need for resilience against moisture ingress and vibration resistance. A soldered joint with heat shrink as I described earlier would meet those objectives.
In the real world of diy car work you’ll usually find that it’s easier to make a good reliable soldered joint than it is to make a good crimped joint. That’s because good crimped joints typically require good crimps and good tools specific to wire size in question whereas good soldered joints just require a bit of solder and basic skills . Crimping is used by car manufacturers because it can be automated whilst still meeting design criteria regarding the environment the harness must work in.
Tye Green said:
Every circuit board in the world has soldered components
We're talking about connecting wires to terminals, not soldering components to PCBs.Soldered wire connections have fallen out of favor because they are prone to fail mechanically when exposed to sustained movement or vibration.
GreenV8S said:
We're talking about connecting wires to terminals
you may be talking about that but the OP isn't. OP asked about " tapping into light circuits for a towing relay box"
and for that application the best solution for a diy person who asks about this matter is almost certainly to solder and support the soldered joint to mitigate any vibration that it might see rather than spend money on crimping tools.
even for one who is experienced in such matters and possesses a wide range of crimping and soldering equipment like me, the soldered and properly supported joint is still preferable.
if the OP was asking about connecting wires to terminals then that's a different situation .
I can see the plus points of either depending where you are doing it but remember this.
Most people will crimp at home using these plasticine efforts.
https://www.ebay.co.uk/itm/335610970330?_skw=cheap...
In which case even blu-tac is preferrable!
Yes, there is always the weak-point when soldering if vibration/movement exists, however where the OP is talking about I personally would always use a soldered joint as there won't be any.
Most people will crimp at home using these plasticine efforts.
https://www.ebay.co.uk/itm/335610970330?_skw=cheap...
In which case even blu-tac is preferrable!
Yes, there is always the weak-point when soldering if vibration/movement exists, however where the OP is talking about I personally would always use a soldered joint as there won't be any.
Gassing Station | Home Mechanics | Top of Page | What's New | My Stuff