The Mini CNC Router / Engraver Thread
Discussion
As we have a 3D Printer thread, I thought it was about time we had a mini CNC engraver / router thread.
Having just bought the world's smallest 3018 (?) CNC router (second hand), I'm now trying to get to grips with it. I already have a 3D printer and diode laser engraver and am used to working with G code etc as my father used to have a precision engineering business and I helped him with his 'full size' CNC machine, so it is not working completely in the dark for me.
My table size / work area is about 160mm x 105mm x 60mm (yes, it is postage stamp sized almost!) and has a tiny 775 (?) motor. I know it can't do much but at least it helps me get to grips with the necessary software, hardware, setup, calibration etc until I get myself a bit more of a proper machine with better capabilities, but if I break this, it is not the end of the world, so it is a useful learning tool.
At the moment, I'm trying to use a mixture of Fusion360, Easel, Candle GRBL...
Is there anything like https://teachingtechyt.github.io/index.html for mini CNC machines?
I know there are one or two of you out there with far more capable machines (I'm looking at you crmcatee!), so show us what you've got and let's spread some knowledge!
Oh, the wee beastie ->
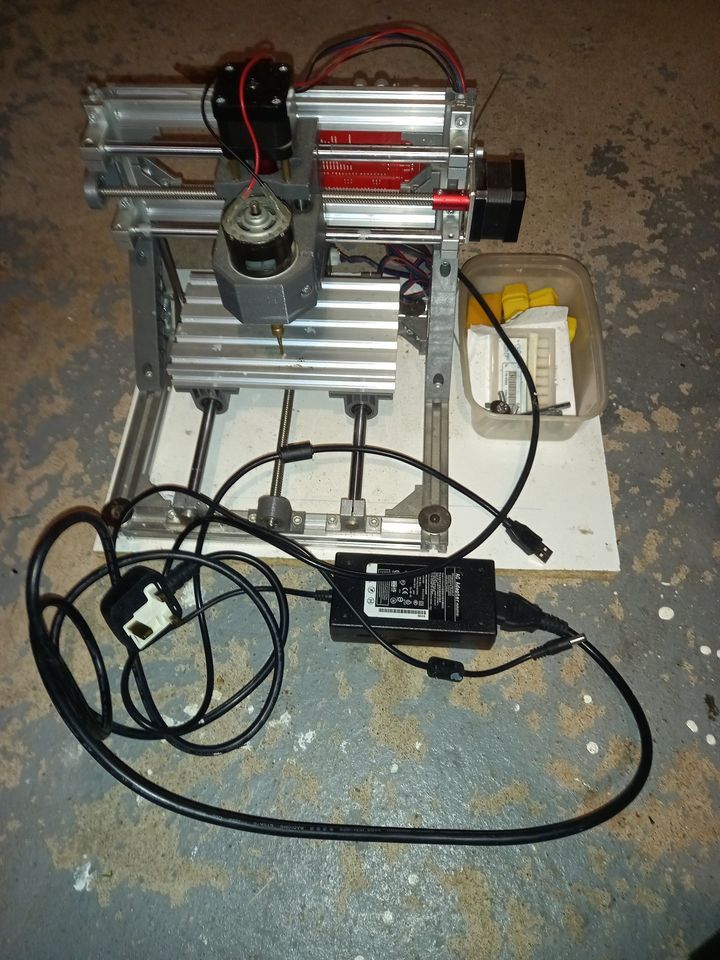
Having just bought the world's smallest 3018 (?) CNC router (second hand), I'm now trying to get to grips with it. I already have a 3D printer and diode laser engraver and am used to working with G code etc as my father used to have a precision engineering business and I helped him with his 'full size' CNC machine, so it is not working completely in the dark for me.
My table size / work area is about 160mm x 105mm x 60mm (yes, it is postage stamp sized almost!) and has a tiny 775 (?) motor. I know it can't do much but at least it helps me get to grips with the necessary software, hardware, setup, calibration etc until I get myself a bit more of a proper machine with better capabilities, but if I break this, it is not the end of the world, so it is a useful learning tool.
At the moment, I'm trying to use a mixture of Fusion360, Easel, Candle GRBL...
Is there anything like https://teachingtechyt.github.io/index.html for mini CNC machines?
I know there are one or two of you out there with far more capable machines (I'm looking at you crmcatee!), so show us what you've got and let's spread some knowledge!
Oh, the wee beastie ->
The Bungard looks a nice little machine! I can't see prices on their website though.
I used to have access to a Leadwell TDC450 with 10 toolchange that my dad owned but he's since retired and the CNC was well and truly worn out! He used Camwrite CADCAM, but I don't think they are still in existence. I have the disks and dongle so I could use it but I don't think it has a GRBL post processor (FANUC/Heidenheim and Meldas - as that's what his controller was)
I used to have access to a Leadwell TDC450 with 10 toolchange that my dad owned but he's since retired and the CNC was well and truly worn out! He used Camwrite CADCAM, but I don't think they are still in existence. I have the disks and dongle so I could use it but I don't think it has a GRBL post processor (FANUC/Heidenheim and Meldas - as that's what his controller was)
S6PNJ said:
The Bungard looks a nice little machine! I can't see prices on their website though.
It was probably 15 years ago; I think with the cabinet, extractor (vacuum cleaner with HEPA bags!), software, training, and a starter set of tools and board blanks it was about six grand.I keep meaning to sell it for the space but never get far - it's nit worth a huge amount any more and needs new software, but it's a great machine.
I was thinking about starting such a thread probably a couple of days before you! I've also made the switch from 3D printing to CNC machining (mainly because I was getting fed up with having to take into account too many variables for getting a good print of sufficient strength).
In the late noughties, I made two CNC machines in order to make a buck for a mould for a new kit car design (it didn't happen) - the first was too large, and the second I ended up selling to someone who turned it into a CNC plasma cutter.
In 2017, I bought a 3018 kit off Amazon - I used this for PCB drilling and milling. It was nothing special; it could just about mill perspex, and drill aluminium - it had a 12V spindle that ran at about 1,200 RPM. I did upgrade the controller to GRBL 1.1.
In 2021, I wanted to make something that could mill aluminium, so over a year, I bought the parts to make something approaching 6024 (I wanted to mill 4U panels), with a 100V spindle. I made the interface circuit board, and stuck GRBL 1.1 on it. So my 4th CNC machine was born, and it did its first aluminium work earlier this year. I used the 3rd CNC machine to make / mark the main parts for it, and 3D printed the motor mounts (which happened to be the same motors I used for the 1st machine).
But it wasn't good enough - it's an MDF / aluminium frame construction, and when it's drilling down into aluminium, it sorta hunkers itself when it's doing the initial penetration (ooh err, missus!). It's also quite slow. The spindle will do 12,000 RPM, but the stepper motors aren't meaty enough.
So I'm in the process of making my 5th CNC machine. I designed it in 3D CAD, using some large 30120 aluminium channels that were going to be thrown out at work, and got lots of alumium bar and plate and the 4th machine marked out a lot of the drill holes and machined some pockets for the bolts.
When I put it together, it just bolted in place - and was perfectly square. I was gobsmacked. There was one hole which I'd accidentally machined in the wrong place, but apart from that, it was just worked.
Unfortunately, my wife stipulated that the new machine couldn't be bigger than the last one, so it's still a 6024 - but I'm now using closed loop stepper motors @ 60V and a 2.2KW 3-phase water cooled spindle (the spindle itself is 3KW, but I derated the VFD - which is just as well, since it managed to blow a fuse an hour ago when the work got too hot (there's no MDF in it, so I'll be adding some coolant mechanism later on). The bed is a little bigger (750mm wide), but the useable area is 600mm wide. I've also used square linear rails, rather than circular ones - and also a 6-axis controller (for future upgrade potential)
It's currently doing its first upgrade on itself - an improved spindle mount so I can align (tram) it properly. I've also got plans to increase my Z-axis work capability by about 40mm.
I'm quite pleased with the results - although there's now a whole new level of controls I can do (feed / spin rates) which I'll need to master.
In the late noughties, I made two CNC machines in order to make a buck for a mould for a new kit car design (it didn't happen) - the first was too large, and the second I ended up selling to someone who turned it into a CNC plasma cutter.
In 2017, I bought a 3018 kit off Amazon - I used this for PCB drilling and milling. It was nothing special; it could just about mill perspex, and drill aluminium - it had a 12V spindle that ran at about 1,200 RPM. I did upgrade the controller to GRBL 1.1.
In 2021, I wanted to make something that could mill aluminium, so over a year, I bought the parts to make something approaching 6024 (I wanted to mill 4U panels), with a 100V spindle. I made the interface circuit board, and stuck GRBL 1.1 on it. So my 4th CNC machine was born, and it did its first aluminium work earlier this year. I used the 3rd CNC machine to make / mark the main parts for it, and 3D printed the motor mounts (which happened to be the same motors I used for the 1st machine).
But it wasn't good enough - it's an MDF / aluminium frame construction, and when it's drilling down into aluminium, it sorta hunkers itself when it's doing the initial penetration (ooh err, missus!). It's also quite slow. The spindle will do 12,000 RPM, but the stepper motors aren't meaty enough.
So I'm in the process of making my 5th CNC machine. I designed it in 3D CAD, using some large 30120 aluminium channels that were going to be thrown out at work, and got lots of alumium bar and plate and the 4th machine marked out a lot of the drill holes and machined some pockets for the bolts.
When I put it together, it just bolted in place - and was perfectly square. I was gobsmacked. There was one hole which I'd accidentally machined in the wrong place, but apart from that, it was just worked.
Unfortunately, my wife stipulated that the new machine couldn't be bigger than the last one, so it's still a 6024 - but I'm now using closed loop stepper motors @ 60V and a 2.2KW 3-phase water cooled spindle (the spindle itself is 3KW, but I derated the VFD - which is just as well, since it managed to blow a fuse an hour ago when the work got too hot (there's no MDF in it, so I'll be adding some coolant mechanism later on). The bed is a little bigger (750mm wide), but the useable area is 600mm wide. I've also used square linear rails, rather than circular ones - and also a 6-axis controller (for future upgrade potential)
It's currently doing its first upgrade on itself - an improved spindle mount so I can align (tram) it properly. I've also got plans to increase my Z-axis work capability by about 40mm.
I'm quite pleased with the results - although there's now a whole new level of controls I can do (feed / spin rates) which I'll need to master.
Edited by tribbles on Saturday 28th September 17:13
tribbles said:
....lots of good stuff.
Sounds fab, maybe you should start a build thread to help us along?and
tribbles said:
....but the stepper motors aren't meaty enough.
I've watched a few self-build CNC You Tube clips (one project is still ongoing...) and it seems 'simple' enough (I'm an engineer at heart!) but how do you know what size steppers to go for? I'm only looking at building a small CNC, probably using 3030 and 6060 V/T slot extrusion but do I need 1.5, 4, 8Nm servos? Machining aluminium would be great, not needed, but desired. Wood would probably be the most common material (Oak mainly), but how do I know how much grunt I need?S6PNJ said:
tribbles said:
....lots of good stuff.
Sounds fab, maybe you should start a build thread to help us along?and
tribbles said:
....but the stepper motors aren't meaty enough.
I've watched a few self-build CNC You Tube clips (one project is still ongoing...) and it seems 'simple' enough (I'm an engineer at heart!) but how do you know what size steppers to go for? I'm only looking at building a small CNC, probably using 3030 and 6060 V/T slot extrusion but do I need 1.5, 4, 8Nm servos? Machining aluminium would be great, not needed, but desired. Wood would probably be the most common material (Oak mainly), but how do I know how much grunt I need?Here's a picture I took earlier though:
In my case, it was "how much can I afford?" I budgeted about £2k for the machine, and ripped through that by quite some margin (I'm thinking nearer £4k). The spindle I'd bought the year before as an upgrade to the V4 machine, but there was no way it was going to mount it!
I've used NEMA 34 closed loop steppers (I have a feeling my 2nd machine was larger; they ran at 110V AC). They were about £340 for the three including the drivers (the 2nd machine was nearer £1600 for four). Each motor has its own 500W PSU which was about £100 for the three. The spindle I have a feeling was around £500.
The table / trolley was one I'd built for the previous machine, with the panels engraved by that earlier machine. I'll redo them later on; the wiring at the back - while not untidy, can be improved (again, I got these from work when they were going to be thrown out). Since I design industrial equipment at work, I've got a background in safety - the emergency stop, for example, was a prototype I'd made for something at work.
There are some 3D printed parts on it - such as the end stop switch mounts, but everything else is pretty much aluminium and steel.
I would like a larger model, but I'd need to set up a workshop, rather than having it in our study (which will be turned into a bathroom in a couple of years time).
tribbles said:
..... on my web site
Oooo - lots of new reading! Your CNC4 with NEMA 23 is around what I was thinking.VERY early days for me, probably won't get around to this for a year or two, so lots of time to plan, think, rethink, replan etc etc,
Considering something like these - https://www.aliexpress.com/item/1005005412229180.h...
They also do them as a kit - https://www.aliexpress.com/item/1005006973754263.h...
which should be able to be controlled by something like this - https://www.aliexpress.com/item/1005007249791243.h... . This controller would control the Stepper driver rather than the stepper directly, so its power rating isn't that important, its the grbl capabilities that I'd need.
S6PNJ said:
Oooo - lots of new reading! Your CNC4 with NEMA 23 is around what I was thinking.
VERY early days for me, probably won't get around to this for a year or two, so lots of time to plan, think, rethink, replan etc etc,
Considering something like these - https://www.aliexpress.com/item/1005005412229180.h...
They also do them as a kit - https://www.aliexpress.com/item/1005006973754263.h...
which should be able to be controlled by something like this - https://www.aliexpress.com/item/1005007249791243.h... . This controller would control the Stepper driver rather than the stepper directly, so its power rating isn't that important, its the grbl capabilities that I'd need.
Those parts will be fine - and the motors will be better than the one's I've got on my V4. The controller looks identical to the one I used when I replaced the one provided with the 3018 machine I have (V3).VERY early days for me, probably won't get around to this for a year or two, so lots of time to plan, think, rethink, replan etc etc,
Considering something like these - https://www.aliexpress.com/item/1005005412229180.h...
They also do them as a kit - https://www.aliexpress.com/item/1005006973754263.h...
which should be able to be controlled by something like this - https://www.aliexpress.com/item/1005007249791243.h... . This controller would control the Stepper driver rather than the stepper directly, so its power rating isn't that important, its the grbl capabilities that I'd need.
I went with my own controller for V4 because I wanted to do use isolated connections as much as possible.
btw, the spindle I have is similar to this one: https://www.aliexpress.com/item/1005003627809131.h...
You'll need a converter to generate 0-10V as an input to the spindle in order to control its speed. I think this'll do: https://www.aliexpress.com/item/1005006582755517.h...
The only problem I had is that even at 0V it still wanted to move very very slowly. I had to make my own circuit to cut the power to the spindle directly - since it's my own circuit, I can't tell you where to get that. However, YMMV!
ETA: Just reading a bit more: The controller does seem to drive a spindle up to 60V - however, I never tried it at a variable speed; I just had it either on or off. It might be okay with a 60V spindle, which means you probably don't need to have a PWM converter.
You'll need a converter to generate 0-10V as an input to the spindle in order to control its speed. I think this'll do: https://www.aliexpress.com/item/1005006582755517.h...
The only problem I had is that even at 0V it still wanted to move very very slowly. I had to make my own circuit to cut the power to the spindle directly - since it's my own circuit, I can't tell you where to get that. However, YMMV!
ETA: Just reading a bit more: The controller does seem to drive a spindle up to 60V - however, I never tried it at a variable speed; I just had it either on or off. It might be okay with a 60V spindle, which means you probably don't need to have a PWM converter.
Edited by tribbles on Saturday 28th September 20:14
Cheers for the spindle links - 
I'm using this build (amongst others) for inspiration, though mine won't be as robust (ie big)!
Part 1 - https://www.youtube.com/watch?v=t7yjEYOrYFo
Part 2 - https://www.youtube.com/watch?v=wyulG9NFw7U
Part 3 - https://www.youtube.com/watch?v=LACC_XJ1RvM - as of 11 days ago so a bit of a wait for the next instalment...

I'm using this build (amongst others) for inspiration, though mine won't be as robust (ie big)!
Part 1 - https://www.youtube.com/watch?v=t7yjEYOrYFo
Part 2 - https://www.youtube.com/watch?v=wyulG9NFw7U
Part 3 - https://www.youtube.com/watch?v=LACC_XJ1RvM - as of 11 days ago so a bit of a wait for the next instalment...
S6PNJ said:
Cheers for the spindle links - 
I'm using this build (amongst others) for inspiration, though mine won't be as robust (ie big)!
Part 1 - https://www.youtube.com/watch?v=t7yjEYOrYFo
Part 2 - https://www.youtube.com/watch?v=wyulG9NFw7U
Part 3 - https://www.youtube.com/watch?v=LACC_XJ1RvM - as of 11 days ago so a bit of a wait for the next instalment...
A similar design to mine, although his is possibly a little more stronger that mine (I think I've got better stability in the X-axis as I'm using two 30120 sections instead of a single 8080 - but his won't flex as much in the Y direction (although the linear rails definitely help). I tried to keep the separation between the rails as large as possible to prevent twisting.
I'm using this build (amongst others) for inspiration, though mine won't be as robust (ie big)!
Part 1 - https://www.youtube.com/watch?v=t7yjEYOrYFo
Part 2 - https://www.youtube.com/watch?v=wyulG9NFw7U
Part 3 - https://www.youtube.com/watch?v=LACC_XJ1RvM - as of 11 days ago so a bit of a wait for the next instalment...
My gantry is held quite a bit better because I drilled all the way through the extrusion, and also put a pocket for the bolt head (which is 12.6 grade). But I had it straight because these had all been CNC machined on V4

I also don't really like having the screw on one side - V2 had this for the Y axis, and I found that at extreme fast movement back and forth, one end oscillated wildly. I ended up having to add another screw and motor to that rail, so now I always put the screw in the middle. Note that V2 also had linear slide rails - just 1.8m apart instead of 60mm!
Cheers, all good reference notes!
Someone somewhere (I've read so much I lose track) said their first build was expected to be circa £1.5k and ended up being £2k or more, and pricing bits up, the budget can soon get stretched - but Oh! to have the room (and 3-phase) to have this £6k's worth of machine (others are available at lower prices I'm sure) - just down the road from me...
A bit more than a mini CNC mill though....
https://www.facebook.com/marketplace/item/10280018...

Someone somewhere (I've read so much I lose track) said their first build was expected to be circa £1.5k and ended up being £2k or more, and pricing bits up, the budget can soon get stretched - but Oh! to have the room (and 3-phase) to have this £6k's worth of machine (others are available at lower prices I'm sure) - just down the road from me...
A bit more than a mini CNC mill though....
https://www.facebook.com/marketplace/item/10280018...

I'm still getting to grips with my mini CNC (not yet used in anger) - I'm using Candle to do the G-Code control, but when I connect to the grbl controller board, the Candle software 'loads' the work coordinates as 95.248, 10.000, -1.000 I then do a G92 X0 Y0 Z0 to set them to zero.
This happens no matter where the table is positioned when it is switched on, and it's not within the settings.ini for Candle, so I'm guessing it is being read from the grbl firmware - but how can I change / update it so that it reads 0, 0, 0 (I manually position the axis at the zero point before I switch off - or at least I'm trying to get into the habit...)
I tried using UGS (in place of Candle) but it seemed to take so long to start up, and was not very responsive, that I soon gave up on it. It also loaded work coordinates, but they were different to the Candle loaded co-ords (I can't remember what they were but X was around -13....).
Any clues? Or any other suggestions for controller software?
This happens no matter where the table is positioned when it is switched on, and it's not within the settings.ini for Candle, so I'm guessing it is being read from the grbl firmware - but how can I change / update it so that it reads 0, 0, 0 (I manually position the axis at the zero point before I switch off - or at least I'm trying to get into the habit...)
I tried using UGS (in place of Candle) but it seemed to take so long to start up, and was not very responsive, that I soon gave up on it. It also loaded work coordinates, but they were different to the Candle loaded co-ords (I can't remember what they were but X was around -13....).
Any clues? Or any other suggestions for controller software?
Yup, there are 4 user programmable macros, so I've set one to do the necessary command (though I've used it to set my Z to +15 as when I 'make' in Fusion, the offsets for tool clearance from workpiece etc, seem to (currently) use +15 as the safety distance.
I'm sure as I play with both the controller and Fusion, I'll get to grips with what works best and how to configure it all...... maybe.....
I'm sure as I play with both the controller and Fusion, I'll get to grips with what works best and how to configure it all...... maybe.....
I've been watching more YouTube clips to learn and have also 3D printed myself a (very) rudimentary pen holder, so I can use it as a plotter to test my 'playing' activities. I've managed to get a svg picture to plot repeatedly and am more happy with the control / Fusion side of things, though there is still a long way to go. I'm now looking at a basic beginners machine (before I possibly do a home build of something more substantial) and have found the TTC 450 via 3DJake https://www.3djake.uk/twotrees/ttc450-cnc-milling-... but having read some reviews, it seems that support from TTC is next to nothing and some / many / a few people have had issues from the outset (but then you'll possibly get that with any machine).
Any other recommendations for machines around the same bed size and around the same cost I should be looking into?
Any other recommendations for machines around the same bed size and around the same cost I should be looking into?
Gassing Station | Computers, Gadgets & Stuff | Top of Page | What's New | My Stuff