Earth bolt under Rad snapped....
Discussion
Hi everyone,
Despite me hitting the bolt with a hammer before attempting to loosen it (something a mechanic once taught me to "shock" the threads) the head on that 17mm bolt under the rad came clean off
I think drilling and tapping another thread will be a right PITA given where it is - has this happened to anyone else?
Where else could I earth those two fairly beefy wires with the ring connectors? (Which were very very rusty by the way)
Despite me hitting the bolt with a hammer before attempting to loosen it (something a mechanic once taught me to "shock" the threads) the head on that 17mm bolt under the rad came clean off

I think drilling and tapping another thread will be a right PITA given where it is - has this happened to anyone else?
Where else could I earth those two fairly beefy wires with the ring connectors? (Which were very very rusty by the way)
Cheers people. I was thinking about using the lower anti roll bar bolt as home for those two fat earth ring connectors, but if I have to tap a new thread on the original bolt so the body stays on (!) I may as well just use the original point under that rad.
The bolt (and earth connections) were totally rotten. Using penetrating oil (I usually use GT85 or plusgas) *sometimes* works for a heavily rusted bolt, but in my experience not always - I've found a good sharp whack with a hammer (sometimes using a metal bar if space is tight) to be more effective.
But yes, the position as an earthing point is questionable given it's basically under the rad and in a water trap- the ring connectors only "just" reach to that bolt, so if a better location is an option, the ring connectors will need to be extended.
Mine is a MK2 with the middle bar across the grill, so going in from the front (so to speak
) won't be an option - also, there is a fiberglass lip on the bottom (for the rad) which would prevent "front entry" anyway - and the "tradesman's entrance" isn't an option either ...
I'll get my coat
The bolt (and earth connections) were totally rotten. Using penetrating oil (I usually use GT85 or plusgas) *sometimes* works for a heavily rusted bolt, but in my experience not always - I've found a good sharp whack with a hammer (sometimes using a metal bar if space is tight) to be more effective.
But yes, the position as an earthing point is questionable given it's basically under the rad and in a water trap- the ring connectors only "just" reach to that bolt, so if a better location is an option, the ring connectors will need to be extended.
Mine is a MK2 with the middle bar across the grill, so going in from the front (so to speak

I'll get my coat

At this stage I’d be talking to a TVR specialist for his advice removing that bolt.
There is a Bush bonded to the body that bolt goes through and is effectively what your bolt nips upto.
If it’s impossible to get at or you can’t get a drill to line up squarely to that now broken bolt centre line I’m starting to think the only way to remove it is by lifting the body a few inches to get at it from underneath the front valance.
That adds more risk as many more bolts need to be removed to facilitate a partial body lift.
Unless someone else has a clear and obvious solution and before going to those extremes talk to a good TVR man.
Matt Smith would be my preferred choice on this one.
My only other thought would be to go through rad opening using a grinder ( if it fits) and cut out a section of the body around that bolt releasing the bush forwards and away.
As the bushing is about 6-8 mm thick or there abouts and depending where the bolt has sheared off once that section with bush is removed you might have good access to soak the bolt over many days and repeated attempts to force oil down the remaining shank and so threads and that might allow you to undo the bolt with grips but the more I talk about it the less confident I am that’s actually going to work.
You then have to re glass your removed section back in place which is all a big bodge.
As these two bolts at the front are the only ones holding the body in place until you reach the front of your outriggers there must be a clear risk of body lift at speed without the front being secured properly.
Twist or a lifting motion is going to be transmitted right the way back to around your windscreen area which is roughly inline with your front rigger bolts.
Though the wings themselves feel meaty the front of the body is actually very light and imho would be at risk of lift.
The one bolt still in place might stop that to some extent but twist effect as in cornering coupled with wind speed hitting the car could easily flex the side with no bolt and cause both it and the bonnet to twist out of line.
Sadly there is no other option but getting that bolt out.
Wrecking the threads in the chassis the bolt fits into is also not an option so drilling it out has to be very precise.
I honestly can’t think of a reasonable way to effect this repair without lifting the body so you can gain clear access from below.
I await others responses in hope there’s another easier solution.
I broke the same bolt when in the process of taking my body off for a chassis resto. Luckily it didn’t really matter as I was going to be replacing all body fixing bolts and once body was off it was a relatively easy task to drill out the front chassis bolt.
I remember now having to use a thin cutting disc from underneath the car to cut through the remaining part of the bolt that was still stuck in that bush as it was stopping me lift the body. A royal pita
I feel your pain
ETA as my post sounds so negative ( knowing how difficult access is) maybe a small angle drill might fit in there.
There is a Bush bonded to the body that bolt goes through and is effectively what your bolt nips upto.
If it’s impossible to get at or you can’t get a drill to line up squarely to that now broken bolt centre line I’m starting to think the only way to remove it is by lifting the body a few inches to get at it from underneath the front valance.
That adds more risk as many more bolts need to be removed to facilitate a partial body lift.
Unless someone else has a clear and obvious solution and before going to those extremes talk to a good TVR man.
Matt Smith would be my preferred choice on this one.
My only other thought would be to go through rad opening using a grinder ( if it fits) and cut out a section of the body around that bolt releasing the bush forwards and away.
As the bushing is about 6-8 mm thick or there abouts and depending where the bolt has sheared off once that section with bush is removed you might have good access to soak the bolt over many days and repeated attempts to force oil down the remaining shank and so threads and that might allow you to undo the bolt with grips but the more I talk about it the less confident I am that’s actually going to work.
You then have to re glass your removed section back in place which is all a big bodge.
As these two bolts at the front are the only ones holding the body in place until you reach the front of your outriggers there must be a clear risk of body lift at speed without the front being secured properly.
Twist or a lifting motion is going to be transmitted right the way back to around your windscreen area which is roughly inline with your front rigger bolts.
Though the wings themselves feel meaty the front of the body is actually very light and imho would be at risk of lift.
The one bolt still in place might stop that to some extent but twist effect as in cornering coupled with wind speed hitting the car could easily flex the side with no bolt and cause both it and the bonnet to twist out of line.
Sadly there is no other option but getting that bolt out.
Wrecking the threads in the chassis the bolt fits into is also not an option so drilling it out has to be very precise.
I honestly can’t think of a reasonable way to effect this repair without lifting the body so you can gain clear access from below.
I await others responses in hope there’s another easier solution.
I broke the same bolt when in the process of taking my body off for a chassis resto. Luckily it didn’t really matter as I was going to be replacing all body fixing bolts and once body was off it was a relatively easy task to drill out the front chassis bolt.
I remember now having to use a thin cutting disc from underneath the car to cut through the remaining part of the bolt that was still stuck in that bush as it was stopping me lift the body. A royal pita
I feel your pain

ETA as my post sounds so negative ( knowing how difficult access is) maybe a small angle drill might fit in there.
Edited by BritishTvr450 on Tuesday 18th June 09:09
Edited by BritishTvr450 on Tuesday 18th June 09:25
Totally agree with speaking to a specialist, depends where you are in the country, but I have spoken to the helpful folk at Str8six a couple of times for a point of view on things.
Is it a matter of getting the radiator out for access, then work out what to do from there?
Body lift is no small feat...
I honestly don't know what the access is like, but we must consider that bolt had to be accessed to be tightened when fitting the body to the car, and that may have been done after a number of objects had been fitted to the chassis (including engine and steering rack) - so surely you can just remove that last thing or two to get to that bolt?
If drilling out a bolt, use a handful of new, sharp drill bits, maybe with an angle adapter like one of these:
https://www.toolstation.com/milwaukee-shockwave-cd...
Follow that by getting a decent extractor tool - this is the type you gently hammer into the drill stud and wind out by hand - do not use a drill to wind out.
https://www.toolbuyer.co.uk/5pc-screw-extractor-re...
I know this journey because I had to pay my local indie mechanic around £400 to extract a sheared bolt form my engine block after my confidence faded.
I would not hesitate to try again with sharp and better tools if I needed to again.
But all of this is potentially irrelevant if you can't get access.
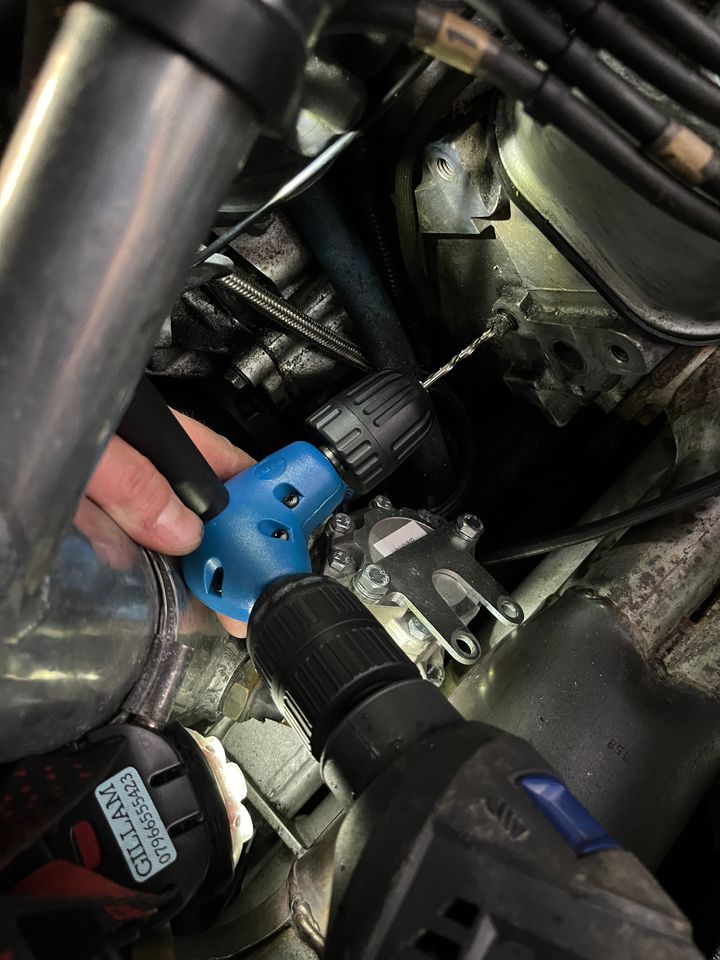
Is it a matter of getting the radiator out for access, then work out what to do from there?
Body lift is no small feat...
I honestly don't know what the access is like, but we must consider that bolt had to be accessed to be tightened when fitting the body to the car, and that may have been done after a number of objects had been fitted to the chassis (including engine and steering rack) - so surely you can just remove that last thing or two to get to that bolt?
If drilling out a bolt, use a handful of new, sharp drill bits, maybe with an angle adapter like one of these:
https://www.toolstation.com/milwaukee-shockwave-cd...
Follow that by getting a decent extractor tool - this is the type you gently hammer into the drill stud and wind out by hand - do not use a drill to wind out.
https://www.toolbuyer.co.uk/5pc-screw-extractor-re...
I know this journey because I had to pay my local indie mechanic around £400 to extract a sheared bolt form my engine block after my confidence faded.
I would not hesitate to try again with sharp and better tools if I needed to again.
But all of this is potentially irrelevant if you can't get access.
Many thanks for the replies everyone - they provide a glimmer of hope. The tricky thing is that bolt is only literally 1.5 possibly 2cm off the bottom of the radiator floor, making going in with a drill straight and true tricky unless I can find a drill with a very thin casing meaning I could use it on its side or possibly upside down - this would mean cutting out a section of the radiator lip to make room the drill. The excellent idea of one of those side/right angular drills may make things much easier, I might have to get one - they're cheap enough...
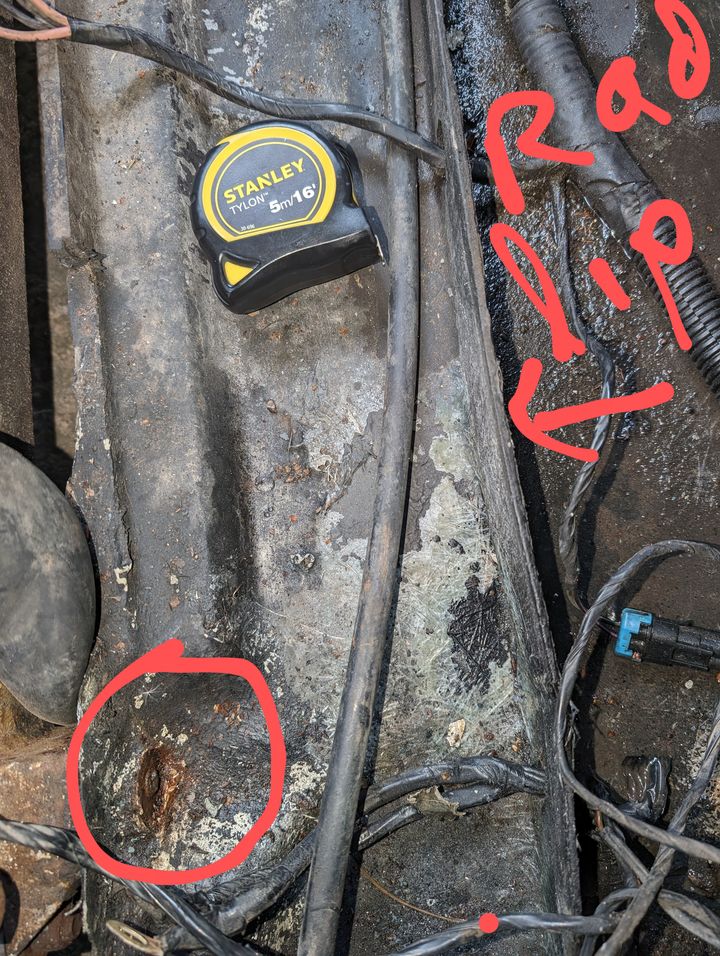
It will be very tight getting a grinder in there to get at what's left of the bolt. The grinder,like the sea, is a good servant but a cruel master...
It will be very tight getting a grinder in there to get at what's left of the bolt. The grinder,like the sea, is a good servant but a cruel master...
Edited by THEDAVINATOR on Tuesday 18th June 17:20
Have broken many of those bolts but that was during body off chassis restos so no biggy.
You will not get a drill in there with the body on..
Do not try the 'easyout' it will just break off in the hole and you will be worse off than before because they are very hard..
The route would be a body lift giving the chance to work under the front of the body.
Or
And, I'm not sure I should advocate this, but having removed plenty of bodies I do know the front end (and back end) are very flexible so it may be possible to remove the other bolt and lift the front of the body just enough to drill, re-tap or fit a thread insert.
When we had a body removed it was placed on a dolly with 6X4 timbers supporting the whole body whist in storage otherwise it would sag.
Steve
You will not get a drill in there with the body on..
Do not try the 'easyout' it will just break off in the hole and you will be worse off than before because they are very hard..
The route would be a body lift giving the chance to work under the front of the body.
Or
And, I'm not sure I should advocate this, but having removed plenty of bodies I do know the front end (and back end) are very flexible so it may be possible to remove the other bolt and lift the front of the body just enough to drill, re-tap or fit a thread insert.
When we had a body removed it was placed on a dolly with 6X4 timbers supporting the whole body whist in storage otherwise it would sag.
Steve
It’s a risk only the owner can be prepared to take.
I also noticed when my body was on an A frame I could lift the front independently of the rear so yes it will flex, how far and how safe you can go is another question.
You will need to lift body at the front by at least 2 inches but more like 3 to gain a clear sight of the bolt and allowing enough room for a compact drill to not rub on the lower front body valance.
Long reach drill bits might help.
I’d be inclined to remove the bonnet as it’s quite heavy. This will allow the front to flex more imo.
You will have to use a cutting disc to go between lower body and chassis rail to chop off the part of the bolt that’s still stuck in the body or you’ll not be able to lift it.
This is likely to graze both the body and chassis slightly.. both unsighted with body on.
just dress up and re paint both before you drop body back down.
If you do this job very carefully and squared up this should result in a clean cut and your bolt should be shorter and much easier to dot punch it’s centre line for drilling.
As it stands your bolt is still in place and looking at your picture almost fully through the body bush.
In essence it’s still trapping the body in place.
If you were to leave it over time or maybe straight away I can see a time when the broken bolt will either loosen or constant body movement over bumps and such like will cause the bush to wear or even start to break out of the body. I’d expect to start hearing creaking or tapping sounds if that was to be the case.
It might also put strain on your radiator!
You’ll need axle stands etc etc a big block of wood and a trolley Jack to lift the body uniformly.
All this would be easier using a ramp so if a TVR man would do it for you I’d be inclined to let them do it. Even if it is at your agreed risk.
If you are comfortable with your skills to do it then the advice here is as accurate as I can remember from facing this issue.
As far as I'm aware you will be the first to try lifting only the front of the body this way!
If it works out ok you will be adding a valuable piece of knowledge to the group.
The front does flex a lot so there’s a reasonable chance this will work. I’m pretty sure I could lift the front a good few inches without the cab or main body section moving at all when my body sat on an A frames and blocks of wood.
In fact I remember now when it came to putting my body back onto chassis using a ramp to raise chassis up to body I had to lift the front of the car ( by hand) to clear the chassis rails at the front so it definitely flexes a few inches. How far is really the only question.
It’s a well known fact when you remove your body you have to support the cars weight under the front and boot as the rear section is heavy and door gaps will open up if you don’t which shows the body flexes or sags easily. I’d keep a close eye on those door gaps when doing any lifting. Open doors if they show signs of closing up.
So you do have some wiggle room here.
Good luck.
I also noticed when my body was on an A frame I could lift the front independently of the rear so yes it will flex, how far and how safe you can go is another question.
You will need to lift body at the front by at least 2 inches but more like 3 to gain a clear sight of the bolt and allowing enough room for a compact drill to not rub on the lower front body valance.
Long reach drill bits might help.
I’d be inclined to remove the bonnet as it’s quite heavy. This will allow the front to flex more imo.
You will have to use a cutting disc to go between lower body and chassis rail to chop off the part of the bolt that’s still stuck in the body or you’ll not be able to lift it.
This is likely to graze both the body and chassis slightly.. both unsighted with body on.
just dress up and re paint both before you drop body back down.
If you do this job very carefully and squared up this should result in a clean cut and your bolt should be shorter and much easier to dot punch it’s centre line for drilling.
As it stands your bolt is still in place and looking at your picture almost fully through the body bush.
In essence it’s still trapping the body in place.
If you were to leave it over time or maybe straight away I can see a time when the broken bolt will either loosen or constant body movement over bumps and such like will cause the bush to wear or even start to break out of the body. I’d expect to start hearing creaking or tapping sounds if that was to be the case.
It might also put strain on your radiator!
You’ll need axle stands etc etc a big block of wood and a trolley Jack to lift the body uniformly.
All this would be easier using a ramp so if a TVR man would do it for you I’d be inclined to let them do it. Even if it is at your agreed risk.
If you are comfortable with your skills to do it then the advice here is as accurate as I can remember from facing this issue.
As far as I'm aware you will be the first to try lifting only the front of the body this way!
If it works out ok you will be adding a valuable piece of knowledge to the group.
The front does flex a lot so there’s a reasonable chance this will work. I’m pretty sure I could lift the front a good few inches without the cab or main body section moving at all when my body sat on an A frames and blocks of wood.
In fact I remember now when it came to putting my body back onto chassis using a ramp to raise chassis up to body I had to lift the front of the car ( by hand) to clear the chassis rails at the front so it definitely flexes a few inches. How far is really the only question.
It’s a well known fact when you remove your body you have to support the cars weight under the front and boot as the rear section is heavy and door gaps will open up if you don’t which shows the body flexes or sags easily. I’d keep a close eye on those door gaps when doing any lifting. Open doors if they show signs of closing up.
So you do have some wiggle room here.
Good luck.
Edited by BritishTvr450 on Wednesday 19th June 08:00
Belle427 said:
Could you get a mig or even stick welder in there to blob on what's left?
I'm thinking the heat may help wind it out, if you got a decent blob on there you could then weld on a small nut.
I'm thinking the heat may help wind it out, if you got a decent blob on there you could then weld on a small nut.
Yeah stating the bleeding obvious sounds like a good shout.
I wish I’d thought of that.

There’s plenty of bolt there to blob too.
I’d definitely try that idea first.
What’s the worst that can happen, you would still have to cut through the bolt if it fails in any case so your weld won’t stop you knocking it out of the bush from behind.
Is the bush made from brass.
My only concern would be how much welding heat might effect it.
Good afternoon everyone,
I thought I'd give an update on this incase it helps anyone else...
I had an old friend come round who is very experienced with working on old cars (original minis are his thing and he's just finished building a mini sprint from scratch, so rusted bolts are not a new thing for him)
So he comes round and says "this will be no problem - get decent 3.5mm, 6.5mm and 8.5mm (for the M10 1.5 tap) drill bits and a nice new M10 tap, and I'll do it for you...
I graceously accepted his kind offer, but things didn't quite go to plan - the 6.5mm drill bit broke and I went and and got another one (all cobalt drill bits) but the drill bits either broke or barely touched the snapped bolt.
He said the bolt is extremely hard steel and recommended I just leave it as it is because the bolt is so rusted to the brass insert bush, that it ain't going anywhere.
It looks as though the brass insert bush which the bolt goes through is threaded - is this the case?
I mentioned just putting a big washer over the exposed bit of bolt and welding an "X" over the washer and (end of) bolt, but he started sucking air through his teeth and said fiberglass burns rather quickly and wouldn't risk a welder anywhere near the car...
I thought I'd give an update on this incase it helps anyone else...
I had an old friend come round who is very experienced with working on old cars (original minis are his thing and he's just finished building a mini sprint from scratch, so rusted bolts are not a new thing for him)
So he comes round and says "this will be no problem - get decent 3.5mm, 6.5mm and 8.5mm (for the M10 1.5 tap) drill bits and a nice new M10 tap, and I'll do it for you...
I graceously accepted his kind offer, but things didn't quite go to plan - the 6.5mm drill bit broke and I went and and got another one (all cobalt drill bits) but the drill bits either broke or barely touched the snapped bolt.
He said the bolt is extremely hard steel and recommended I just leave it as it is because the bolt is so rusted to the brass insert bush, that it ain't going anywhere.
It looks as though the brass insert bush which the bolt goes through is threaded - is this the case?
I mentioned just putting a big washer over the exposed bit of bolt and welding an "X" over the washer and (end of) bolt, but he started sucking air through his teeth and said fiberglass burns rather quickly and wouldn't risk a welder anywhere near the car...
Having just lifted the body on my 1996 Griffith 500 I can confirm that none of the brass bushes ( Bobbins) through which the body securing bolts pass are threaded, Motoclan sell them.Fortunately all my bolts undid without issue, I did however forget the earth leads under the nearside dash while lifting the body that caused the bobbin to rip out of the body, so had to re glass fibre it back, not an easy job with limited access.
I agree with the above post. As Steve has extensive knowledge regarding both the cars and body off just get it to a Tvr man.
They’ll get that bolt out.
The Mini man is wrong to tell you to leave it as it is. Very poor advice imo.
Going from a 3.5 bit to a 6.5mm bit is to big a step.
If he got through with the 3.5 i’d then go to 4.2 and slowly increase drill size as you go.
I’d use plenty of cutting oil to keep bits cool but it sounds like he’s given up.
Did you take the advice to cut through the bolt between the body and Chassis.
If not your drilling though a bolt possibly 50% longer which makes it very difficult and time consuming.
Cutting through the bolt is likely to dislodge the section stuck in the bush and make it easier to remove that section of it.
Tvr men have faced this problem many times so don’t give up but it’s probably time to let a Tvr man take the job on.
Send pictures and gain there advice before doing anything else would be my next move.
Goodluck
There is nothing special about the bolt and it’s certainly not hardened. Ignore that idea!
It simply takes patience and allocate plenty of time but it will drill out as I’ve done at least 3 including this very bolt.
They’ll get that bolt out.
The Mini man is wrong to tell you to leave it as it is. Very poor advice imo.
Going from a 3.5 bit to a 6.5mm bit is to big a step.
If he got through with the 3.5 i’d then go to 4.2 and slowly increase drill size as you go.
I’d use plenty of cutting oil to keep bits cool but it sounds like he’s given up.
Did you take the advice to cut through the bolt between the body and Chassis.
If not your drilling though a bolt possibly 50% longer which makes it very difficult and time consuming.
Cutting through the bolt is likely to dislodge the section stuck in the bush and make it easier to remove that section of it.
Tvr men have faced this problem many times so don’t give up but it’s probably time to let a Tvr man take the job on.
Send pictures and gain there advice before doing anything else would be my next move.
Goodluck
There is nothing special about the bolt and it’s certainly not hardened. Ignore that idea!
It simply takes patience and allocate plenty of time but it will drill out as I’ve done at least 3 including this very bolt.
Edited by BritishTvr450 on Friday 28th June 07:40
Gassing Station | Chimaera | Top of Page | What's New | My Stuff