Headscratcher Of Seized Engine Mount Bolt
Discussion
Good Afternoon,
First of all apologies if this is better suited in a different section of the forum - and mods feel free to move.
More of a lurker rather than a poster, although I'm hoping someone might be able to assist with suggestions to safely remove a seized bolt.
I passed my module one in October last year, and have since been recommissioning a Royal Enfield Electra EFI ready for the summer. The last part of the mini restoration was what should of been a simple oil change. Although it ended in needing to split the casings due to a loosing a helicoil in the sump area.
It has been a major headache removing the engine due to the bottom engine mount bolt being seized solid, although what is baffling me is that it is the unthreaded area of the bolt that has seized and its a steel bolt going through the aluminium casing it has been seized enough to being able to snap both ends of the bolt trying to free it. The engine is now out and the casing as split although the bolt still seems fairly seized in one half of the case. I've tried heat to remove and it isn't working although I don't want to warp the casings with too much heat. A hammer and punch doesn't seem to be working either. It has taken hours to get this far and the bolt seems to be hardened steel and only an angle grinder seems to work on it, or rotary tungston burr bits (this is very slow and they blunt out quite quickly) the sharp end of the bolt seen below was around 2 hours of grinding and I think the heat from grinding might of hardened the bolt further.
Just seeing if anyone has come across similar before and any suggestions to remove without damaging the casing. The bolt is unthreaded hardened steel which seems to have a coating on it. The main reason for the recommission was due to the previous owner storing the bike outside so I think water ingress might of got in. The length of the bolt left in the engine is probably around 8 CM.
Any help would be appreciated, Kind Regards Ed
Edit: the image below is the bolt, although soaking in WD40 so it might make it look like the two areas are joint together
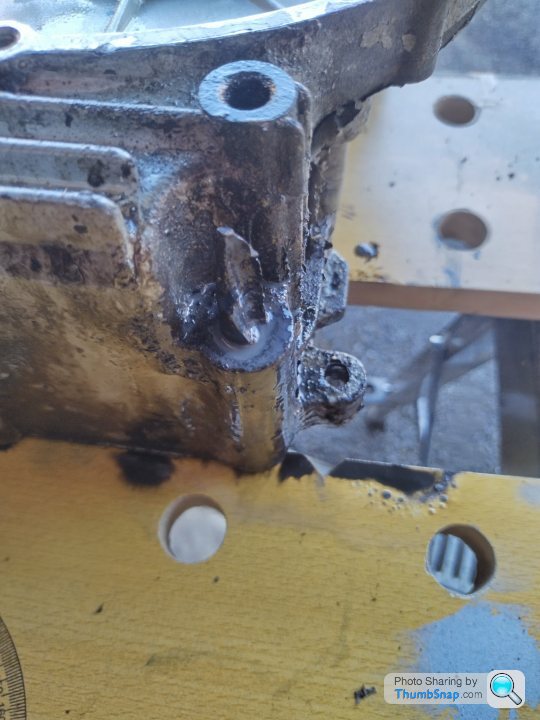
First of all apologies if this is better suited in a different section of the forum - and mods feel free to move.
More of a lurker rather than a poster, although I'm hoping someone might be able to assist with suggestions to safely remove a seized bolt.
I passed my module one in October last year, and have since been recommissioning a Royal Enfield Electra EFI ready for the summer. The last part of the mini restoration was what should of been a simple oil change. Although it ended in needing to split the casings due to a loosing a helicoil in the sump area.
It has been a major headache removing the engine due to the bottom engine mount bolt being seized solid, although what is baffling me is that it is the unthreaded area of the bolt that has seized and its a steel bolt going through the aluminium casing it has been seized enough to being able to snap both ends of the bolt trying to free it. The engine is now out and the casing as split although the bolt still seems fairly seized in one half of the case. I've tried heat to remove and it isn't working although I don't want to warp the casings with too much heat. A hammer and punch doesn't seem to be working either. It has taken hours to get this far and the bolt seems to be hardened steel and only an angle grinder seems to work on it, or rotary tungston burr bits (this is very slow and they blunt out quite quickly) the sharp end of the bolt seen below was around 2 hours of grinding and I think the heat from grinding might of hardened the bolt further.
Just seeing if anyone has come across similar before and any suggestions to remove without damaging the casing. The bolt is unthreaded hardened steel which seems to have a coating on it. The main reason for the recommission was due to the previous owner storing the bike outside so I think water ingress might of got in. The length of the bolt left in the engine is probably around 8 CM.
Any help would be appreciated, Kind Regards Ed
Edit: the image below is the bolt, although soaking in WD40 so it might make it look like the two areas are joint together
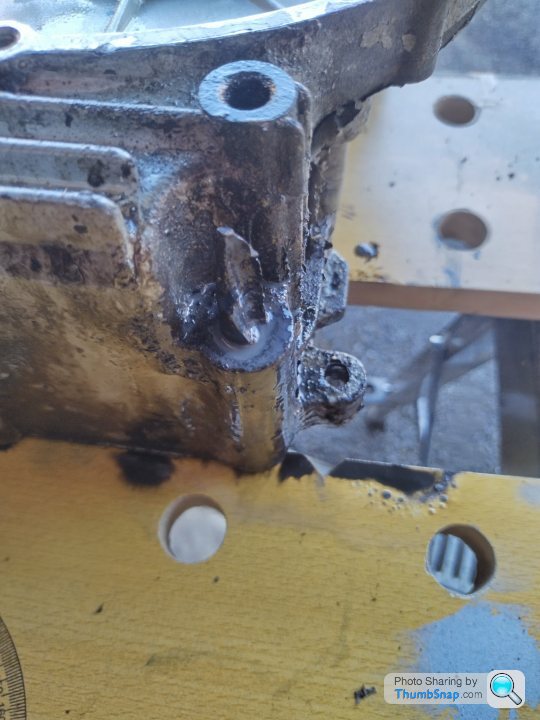
Im not an engineer, but experience tells me this is potentially tricky. Difficult to drill out because the bolt is steel and the casing soft aluminium. So big risk of damaging the casing. Options could be weld a nut on the end of the snapped bolt and see if it can be turned. Might be best to take it to an engineering works and see what they say. They are often used to dealing with this sort of thing. I had a stainless steel
M 6 bolt snapped off in an aluminium alloy outboard motor leg. Engineering workshop milled it out, cost £ 50 quid i think.
Best of luck
M 6 bolt snapped off in an aluminium alloy outboard motor leg. Engineering workshop milled it out, cost £ 50 quid i think.
Best of luck
Many moons ago I had a summer job at a small EDM workshop (long since closed) and we used to do this sort of thing as a foreigner for beer money…
http://www.apautodiagnostics.com/spark-erosion
http://www.apautodiagnostics.com/spark-erosion
I have done similar in the past and would do the following.
Cut flush so you have a flat surface. Centre punch then use a high quality cobalt drill to drill a small hole.
Then two choices. Use a stud extractor to remove the stud or use a larger drill followed by a tap to re thread
If using the stud extractor WD40 isn’t really good enough maybe something like plus gas and some gentle well controlled heat
But if you are not confident then a small engineering place would be best.
Good luck
Cut flush so you have a flat surface. Centre punch then use a high quality cobalt drill to drill a small hole.
Then two choices. Use a stud extractor to remove the stud or use a larger drill followed by a tap to re thread
If using the stud extractor WD40 isn’t really good enough maybe something like plus gas and some gentle well controlled heat
But if you are not confident then a small engineering place would be best.
Good luck
I had a similar situation the other day, looking at what you’ve got there you’ve got nothing to lose buy cutting the bolt down a bit and welding a nut on, I’d be surprised if this didn’t work. If not I’d cut it flush and drill it out, if you’re accurate enough you could keep the original threads if you take your time.
Steel bolt into alloy is the problem here.
Steel bolt into alloy is the problem here.
Thank you everyone for your replies, Sogra the casing isn't threaded so wouldn't need to be re tapped it seems to be two smooth surfaces that have seemed to have fused themselves together - colbat drill bits don't really seem to touch it either. I will have a look for local engineering shops and see if they can assist, I've come this far without causing any damage so will be a shame to damage something now. Thanks again everyone
Edited by Mk3Ed on Monday 1st May 21:09
WelshRich said:
Many moons ago I had a summer job at a small EDM workshop (long since closed) and we used to do this sort of thing as a foreigner for beer money…
http://www.apautodiagnostics.com/spark-erosion
+1 on the spark erosion.http://www.apautodiagnostics.com/spark-erosion
IMHO - More Heat.
I'd expect the cost of EDM-ing that out would be no different (possibly more) than TIG-ing on a new lump of Ali and re-drilling.
It's a hefty lump of Aluminium there, if it was mine I'd heat it, spray Plus-Gas or similar in it, and repeat a few times. WD-40 is junk as a release agent compared to others. After repeating a few times, heat and give it a tap and a turn or two and soak again.
Heat is your friend tbh Ali loves expanding!
I'd expect the cost of EDM-ing that out would be no different (possibly more) than TIG-ing on a new lump of Ali and re-drilling.
It's a hefty lump of Aluminium there, if it was mine I'd heat it, spray Plus-Gas or similar in it, and repeat a few times. WD-40 is junk as a release agent compared to others. After repeating a few times, heat and give it a tap and a turn or two and soak again.
Heat is your friend tbh Ali loves expanding!

Heat it in an oven at 200C if you can as it will avoid distorting the cases and will be easier than trying to heat the local area. Hopefully the casing will expand sufficiently to enable it to be removed without too much violence.
If that doesn't work then spark erosion is the answer.
If that doesn't work then spark erosion is the answer.
Edited by archie456 on Monday 1st May 23:26
I had a similar issue on my CZ. The centrestand was missing it's spring and for some reason had been refitted without. 30 years in a garden and the steel bolt had seized solid. I managed to drill it out after about 4 or 5 hours (including a snapped cobalt drill bit).
Personally, I'd take it to a machine shop (ask on your local Facebook biker groups as well as you never know who has machinery for this in their garage!)
Personally, I'd take it to a machine shop (ask on your local Facebook biker groups as well as you never know who has machinery for this in their garage!)
I have no quick solution, as suggested machine shop or eroding would be my choice,
the reason for the stuck bolt seems to be chemical corrosion between the alu case and the steel bolt.
There is no need for a thread between these two materials, just a small gap, add salt water and time,
and the two metals are almost like welded together.
Better explanation here :
https://www.totalmateria.com/page.aspx?ID=CheckArt...
Good luck with that bugger.
the reason for the stuck bolt seems to be chemical corrosion between the alu case and the steel bolt.
There is no need for a thread between these two materials, just a small gap, add salt water and time,
and the two metals are almost like welded together.
Better explanation here :
https://www.totalmateria.com/page.aspx?ID=CheckArt...
Good luck with that bugger.
Benni said:
I have no quick solution, as suggested machine shop or eroding would be my choice,
the reason for the stuck bolt seems to be chemical corrosion between the alu case and the steel bolt.
There is no need for a thread between these two materials, just a small gap, add salt water and time,
and the two metals are almost like welded together.
Better explanation here :
https://www.totalmateria.com/page.aspx?ID=CheckArt...
Good luck with that bugger.
This.the reason for the stuck bolt seems to be chemical corrosion between the alu case and the steel bolt.
There is no need for a thread between these two materials, just a small gap, add salt water and time,
and the two metals are almost like welded together.
Better explanation here :
https://www.totalmateria.com/page.aspx?ID=CheckArt...
Good luck with that bugger.
The bolt should/would have had a coating on it to stop a reaction but the bolt may have been changed or the coating somehow removed through wear or corrosion.
Make a mxture of half acetone and half automatic transmission fluid and apply that for a couple of days. This is about the best penetrating fluid I have found.
Just done a similar job on a BSA where the stud had been seizing in since 1971
Still needed heat though.
However if I was you I’d get an engineering shop to machine it out, less risk of damage and potentially cheaper in the end.
Just done a similar job on a BSA where the stud had been seizing in since 1971
Still needed heat though.
However if I was you I’d get an engineering shop to machine it out, less risk of damage and potentially cheaper in the end.
Looks to be not that much of it left to weld a nut onto but that's what I'd try first.
I've recently had a few similar (though maybe not quite as bad) on an ongoing Land Rover rebuild and, so far it's worked - cut it flat and weld a nut onto it, filling the hollow of the nut with a pool of weld, the heat of the weld will help and you may shift it, worst case it'll break flush with (or even below) the casing, if so I'd try to drill it out. Failing that probably spark erosion though I've no experience with that so can't really comment.
Can you get at it from the other side of the case or is it a blind hole?
I've recently had a few similar (though maybe not quite as bad) on an ongoing Land Rover rebuild and, so far it's worked - cut it flat and weld a nut onto it, filling the hollow of the nut with a pool of weld, the heat of the weld will help and you may shift it, worst case it'll break flush with (or even below) the casing, if so I'd try to drill it out. Failing that probably spark erosion though I've no experience with that so can't really comment.
Can you get at it from the other side of the case or is it a blind hole?
Thank you again everyone, and also I had no idea steel seizing in aluminium was an issue before all the comments so it's good to see its not just myself who has experienced similar issues. The bolt is accessible from both sides although I think by the time I mess around soaking it and trying everything else I might be better off taking it to an engineering shop I've found a few near me who do spark erosion so hopefully one of them can help, one of my concerns is that I will end up damaging it and causing a bigger issue so it is better left to a professional. Just glad the weather hasn't quite got too warm yet so I'm not missing much riding time. Thank you all again much appreciated
ridds said:
IMHO - More Heat.
......
Heat is your friend tbh Ali loves expanding!
This is the right answer. ......
Heat is your friend tbh Ali loves expanding!

I've never yet had a seized steel bolt in an aluminium housing that hasn't come free with enough heat... You need to get what is left of that bolt proper red hot, then leave it to cool. Then heat the aluminium the bolt runs through and it should tap out with a hammer and punch.
Gassing Station | Biker Banter | Top of Page | What's New | My Stuff