Cracked bell housing installing clutch
Discussion
I decided to replace the clutch on my smart roadster.
It was going well, there were great guides on how to get the gearbox off but basically nothing on reassembly.
I got the gearbox back on but it wasn't seated perfectly, I don't really know how you line up the output shaft with the spline but assumed it would just pull itself into place as it was already close enough to get the bolts started.
I went round doing them up a little bit at a time to bring it together smoothly. I could hear it creaking as I tightened things up but I assumed that was normal
I was using a normal sized hand ratchet, I wasn't really heaving it either so thought everything would be ok.
There was a little crack then it seemed to go together a bit more but turned out the clutch has smashed through the bell housing on the engine side.
Is this an expected risk when installing a gearbox if your not careful about lining up the output shaft or was I really unlucky/ maybe there was an existing crack / fault?
Do I take it that it is not repairable?
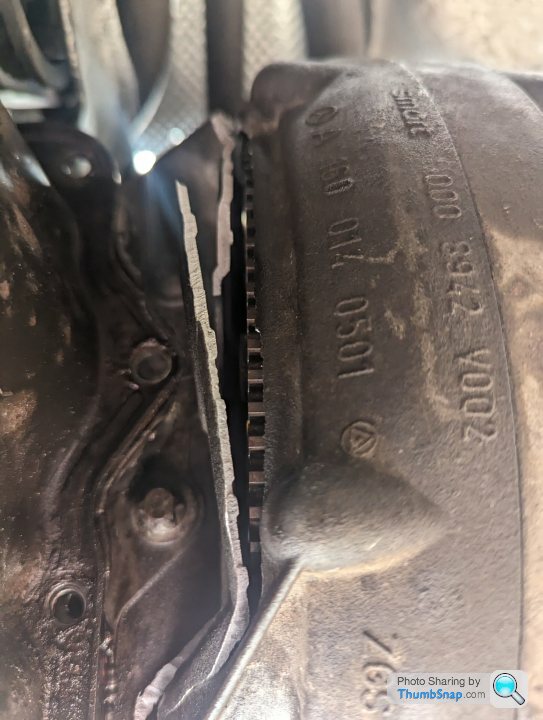
It was going well, there were great guides on how to get the gearbox off but basically nothing on reassembly.
I got the gearbox back on but it wasn't seated perfectly, I don't really know how you line up the output shaft with the spline but assumed it would just pull itself into place as it was already close enough to get the bolts started.
I went round doing them up a little bit at a time to bring it together smoothly. I could hear it creaking as I tightened things up but I assumed that was normal
I was using a normal sized hand ratchet, I wasn't really heaving it either so thought everything would be ok.
There was a little crack then it seemed to go together a bit more but turned out the clutch has smashed through the bell housing on the engine side.
Is this an expected risk when installing a gearbox if your not careful about lining up the output shaft or was I really unlucky/ maybe there was an existing crack / fault?
Do I take it that it is not repairable?
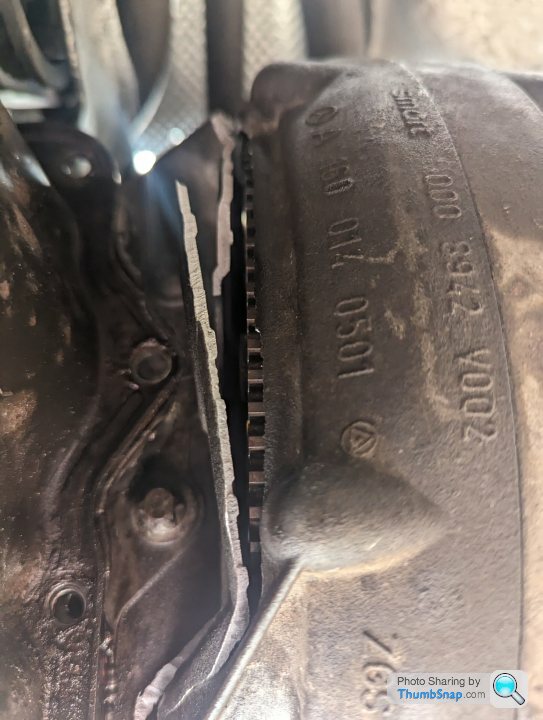
e-honda said:
Is this an expected risk when installing a gearbox if your not careful about lining up the output shaft
The bolts are to hold it in place, not pull it into place. The bell housing is a thin casting and typically not very tough.e-honda said:
maybe there was an existing crack / fault?
No reason to think so.e-honda said:
not repairable?
Not repairable, sorry. 
e-honda said:
So I should have backed it out and and tried to rotate the engine until it slotted together better?
The procedure would usually involve checking / replacing the spigot bearing as necessary, using a clutch aligning tool to align the clutch plate(s) with each other and the spigot, carefully offering up the 'box, using a couple of long bolts loosely in place to keep it aligned while you push it home, and getting the mating surfaces touching all round before you clamp anything up. You need to twist the 'box around the input shaft or rotate either the crank or the 'box output to get the splines to engage, but if you used the aligning tool then once you get the splines engaged everything else should line itself up.And of course you'll be replacing the release bearing.
gazza285 said:
“On the engine side…”
So it’s not the bellhousing that’s broken, it’s the mounting flange that’s part of the engine casting, so you have potentially scrapped the engine there. Also, where are the sump bolts?
In the postSo it’s not the bellhousing that’s broken, it’s the mounting flange that’s part of the engine casting, so you have potentially scrapped the engine there. Also, where are the sump bolts?
I was replacing the sump as it was rusty, with it removed you can access the bolts on the back of fly wheel without a special tool, I put the old one back in place with a couple of the old bolts just to avoid accidentally bashing the oil pickup, not an issue now it seems.
If I get the clutch back out I'll have everything I need to replace the clutch on my next roadster if I get one, I might take it to a garage though.
The splines on the shaft that sticks out of the gearbox (the gearbox input shaft) need to engage with the splines of the driven plate (the thing with the friction material on it that's clamped between the cover assembly (the thing that bolts to the flywheel and has the things that look like fingers on the side nearest the gearbox) and the flywheel.
The end of the shaft after passing through the plate sits in & is supported by a bearing in either the flywheel or the rear centre of the crankshaft.
www.ebay.co.uk/itm/185818041360 cover assy on the left, driven plate on the right. (These would need an alignment tool to hold the driven plate centred while you do up the bolts that hold the cover to the flywheel. If they aren't aligned then you won't be able to get the box back on as the shaft won't be able to pass through).
Can be a fiddle but if they aren't & the gearbox & engine aren't pushed up snug to each other without any gap & you try to pull it together with the bolts that's what can happen.
ETA I also think that's the engine casting you've broken, the visible teeth being the starter ring gear. In which case unless you can find a good welder who's prepared to take it on it's replacement engine time.
The end of the shaft after passing through the plate sits in & is supported by a bearing in either the flywheel or the rear centre of the crankshaft.
www.ebay.co.uk/itm/185818041360 cover assy on the left, driven plate on the right. (These would need an alignment tool to hold the driven plate centred while you do up the bolts that hold the cover to the flywheel. If they aren't aligned then you won't be able to get the box back on as the shaft won't be able to pass through).
Can be a fiddle but if they aren't & the gearbox & engine aren't pushed up snug to each other without any gap & you try to pull it together with the bolts that's what can happen.
ETA I also think that's the engine casting you've broken, the visible teeth being the starter ring gear. In which case unless you can find a good welder who's prepared to take it on it's replacement engine time.
Edited by paintman on Sunday 27th August 20:48
Panamax said:
e-honda said:
I could hear it creaking as I tightened things up but I assumed that was normal. I was using a normal sized hand ratchet, I wasn't really heaving it either so thought everything would be ok.
Torque wrench.They should have been torqued to 20nm and my torque wrench doesn't go that low but to get above 20nm with my normal wrench I have to be giving it a fairly good heaving which I wasn't doing so I thought I was fairly safe against over torquing. So I suspect maybe it was weaker than it should have been, but then it is 20 years old.
Nothing whatsoever to do with an old or weak casing.
You've not aligned & engaged the splines & pushed the engine & box together correctly.
If they were then the gearbox housing and the engine casting would have been in full contact with each other with no gaps before you put the bolts in & it couldn't happen.
Simple user error.
You've not aligned & engaged the splines & pushed the engine & box together correctly.
If they were then the gearbox housing and the engine casting would have been in full contact with each other with no gaps before you put the bolts in & it couldn't happen.
Simple user error.
Edited by paintman on Sunday 27th August 21:42
paintman said:
Nothing whatsoever to do with an old or weak casing.
You've not aligned & engaged the splines & pushed the engine & box together correctly.
If they were then the gearbox housing and the engine casting would have been in full contact with each other with no gaps & it couldn't happen.
Simple user error.
Yeah but if everything was the right design strength shouldn't I have been able to go up to 20nm on each of these bolts before it punched through the casing? Or is that torque just to guarantee it doesn't stretch the bolts / threads?You've not aligned & engaged the splines & pushed the engine & box together correctly.
If they were then the gearbox housing and the engine casting would have been in full contact with each other with no gaps & it couldn't happen.
Simple user error.
e-honda said:
Yeah but if everything was the right design strength shouldn't I have been able to go up to 20nm on each of these bolts before it punched through the casing? Or is that torque just to guarantee it doesn't stretch the bolts / threads?
The torque rating relates to the bolt/thread when the two mating surfaces are flush together! You should never draw components like that together using the bolts, by doing that you're asking the casting to potentially flex, in a way it's not designed to take the load, hence the failure you've now experienced.
Edited by The Road Crew on Sunday 27th August 22:03
It's very annoying, I would have tried backing it out and rotating the fly wheel a little but I was more worried about the weight of the gearbox ending up stripping the threads or bending the bolts, And l thought it wasn't really possible for it to get as close as it was without the shaft being aligned,
I think it was because the frame that holds the fly wheel in place is quite thin so would have just been bending under the pressure allowing the clutch/ flywheel to move back and is what I could hear creaking, fairly obvious in hindsight but unfortunately not something mentioned on any of the guides I was using and not something I would ever have thought about
I think it was because the frame that holds the fly wheel in place is quite thin so would have just been bending under the pressure allowing the clutch/ flywheel to move back and is what I could hear creaking, fairly obvious in hindsight but unfortunately not something mentioned on any of the guides I was using and not something I would ever have thought about
An expensive lesson. To quote Al Stewart "if it does n't come naturally, then leave it", There are very few components where substantial force is necessary to put them together. The combined force you applied using all of those bolts was pretty substantial. As to worries regarding the weight - this is a very small, light engine, I've had lawnmowers with larger engines!
Next time either get competent help or do you research properly - it is an awful lot cheaper.
Next time either get competent help or do you research properly - it is an awful lot cheaper.
It's not cost me too much, I bought it very cheap as spares or repairs last year and it was cat N, fixed a few bits and got some use out of it before the clutch finally let go.
If I hadn't tried to replace the clutch I probably would have scrapped it.
But it might cost me a lot I've decided I really liked the roadster, so now plan to buy a decent one to replace it.
If I hadn't tried to replace the clutch I probably would have scrapped it.
But it might cost me a lot I've decided I really liked the roadster, so now plan to buy a decent one to replace it.
e-honda said:
Yeah but if everything was the right design strength shouldn't I have been able to go up to 20nm on each of these bolts before it punched through the casing? Or is that torque just to guarantee it doesn't stretch the bolts / threads?
torque is completely and utterly irrelevant, when you've tried to install something incorrectly, or incorrectly aligned.torque is not the problem.
Gassing Station | Engines & Drivetrain | Top of Page | What's New | My Stuff