540HP NA 7L V12 3 seater
Discussion
I am working on a homebuild project that I thought might interest some of you - but it is very unconventional so, like marmite, you are going to like it or hate it. But as I am only building it for myself and I like marmite.....
My ultimate car is the Mclaren F1 road car, I think it is the best packaging exercise carried out to date. However I doubt I will ever own a real one as the values are climbing a thousand times faster than my income. And then I got to thinking, would I really ever want to actually own a real one? They are beautifully styled, aerodynamic, have a superb powerplant and would be enormous fun to drive, but they are becoming so valuable that the enjoyment of them as a car is diminishing, and they are becoming a victim of their own success. As the recent Autocar Mclaren Ultimate series review stated only a handful of them are actually being used in anger, the rest are like jewels locked in a vault. A great pity but totally understandable.
So after more than 25 years of pondering and deliberating and realising that a real F1 is out of my reach I am embarking on a homebuild project that incorporates the ethos of the F1, and the title of the thread gives the highlights. I did not want to style my own car as that is a task very few homebuilders achieve with success, however I am quite comfortable designing a chassis and powerplant configuration that meets both my goals and the NZ LVVTA regulations to put this thing on the road.
My longstanding puzzle was how do you economically combine a large capacity V12 engine and manual transmission? Mclaren brilliantly devised a longitudinal V12 with a transverse gearbox to minimise length, however all the V12's I have seen available were not "bargains". Since I am going to drive this vehicle very hard the engine and gearbox maintenance costs have to be minimised, ideally using "off the shelf" components. The power and torque levels I am using are always challenging for midengined car builders as the transaxle options available are limited.
So we arrive at my solution, which is the marmite moment;
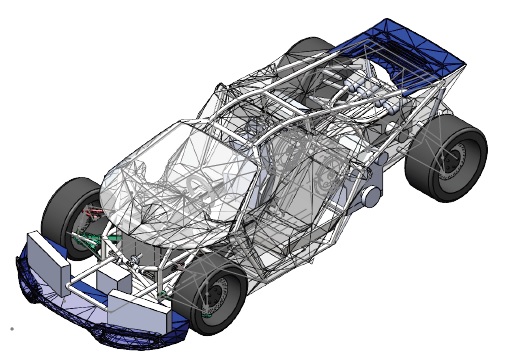
I have a pair of transversely mounted honda J35Z2 engines (stock 270hp and 344Nm of torque each), each with a standard dual mass clutch, that will drive a spiral bevel pinion that is in constant mesh with a common crownwheel at a 1:1 ratio. The crownwheel is coupled directly to the input shaft of a C6 Corvette transaxle (TR6060). I am using 2 ECU's as I can disconnect one motor while driving around on the other for improved economy - I like long road trips and the South Island has some beautiful roads but not many petrol stations.
Using this configuration I have some major benefits
- 3.5L V6 engines are reliable, cheap and plentiful - they are plug and play items
- TR6060 has a torque limit of 800Nm, wheelspin is most likely the torque limiter for this setup
- the weight is rear biased but not excessively, split as modelled is currently 43F/57R
- due to the space between the engines I have direct access to the standard corvette gearbox shift linkage - so direct "like a rifle bolt" shifts are easy to achieve
- I can also run the front bank exhausts through the same gap
Suspension and brakes are C6 corvette items, J55 brake option (Z51). Leaf springs are replaced by coilovers.
Spaceframe is all 4130 tubing, interior bulkheads and outer skin panels are composite material. Currently I am working on the surfacing models for the body panels, here is a snapshot of my progress to date - still a long way to go.
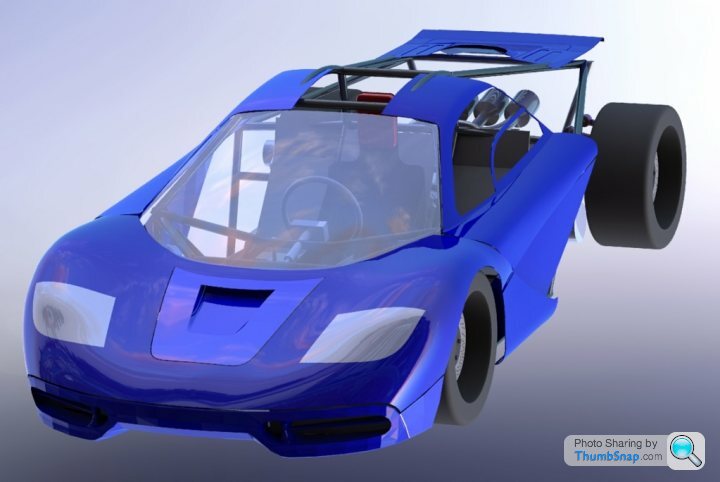
Target weight will be 1300Kg, mainly because this is the first car I have built from scratch so I am trying to be realistic. A full carbon composite chassis is not in my budget and is also harder to get road compliance with - but I will shave off weight wherever possible. Performance will still be good at that porky weight, however I can in the future change the cams and porting to get 350HP each, still natually aspirated. Turbo charging is also possible, the AR35TT uses the same block and heads and gives 550HP each, but 1100 is too much for the road. The gearbox life would most likely be shortened unacceptably at the level also. This is a daily driver & grand touring car, not a racecar and thus does not need bragging right HP numbers.
I think that suffices as an introduction, now for your comments...
My ultimate car is the Mclaren F1 road car, I think it is the best packaging exercise carried out to date. However I doubt I will ever own a real one as the values are climbing a thousand times faster than my income. And then I got to thinking, would I really ever want to actually own a real one? They are beautifully styled, aerodynamic, have a superb powerplant and would be enormous fun to drive, but they are becoming so valuable that the enjoyment of them as a car is diminishing, and they are becoming a victim of their own success. As the recent Autocar Mclaren Ultimate series review stated only a handful of them are actually being used in anger, the rest are like jewels locked in a vault. A great pity but totally understandable.
So after more than 25 years of pondering and deliberating and realising that a real F1 is out of my reach I am embarking on a homebuild project that incorporates the ethos of the F1, and the title of the thread gives the highlights. I did not want to style my own car as that is a task very few homebuilders achieve with success, however I am quite comfortable designing a chassis and powerplant configuration that meets both my goals and the NZ LVVTA regulations to put this thing on the road.
My longstanding puzzle was how do you economically combine a large capacity V12 engine and manual transmission? Mclaren brilliantly devised a longitudinal V12 with a transverse gearbox to minimise length, however all the V12's I have seen available were not "bargains". Since I am going to drive this vehicle very hard the engine and gearbox maintenance costs have to be minimised, ideally using "off the shelf" components. The power and torque levels I am using are always challenging for midengined car builders as the transaxle options available are limited.
So we arrive at my solution, which is the marmite moment;
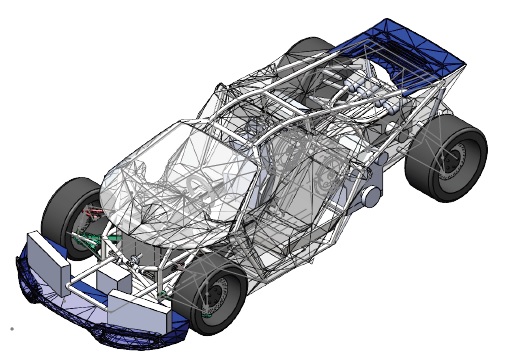
I have a pair of transversely mounted honda J35Z2 engines (stock 270hp and 344Nm of torque each), each with a standard dual mass clutch, that will drive a spiral bevel pinion that is in constant mesh with a common crownwheel at a 1:1 ratio. The crownwheel is coupled directly to the input shaft of a C6 Corvette transaxle (TR6060). I am using 2 ECU's as I can disconnect one motor while driving around on the other for improved economy - I like long road trips and the South Island has some beautiful roads but not many petrol stations.
Using this configuration I have some major benefits
- 3.5L V6 engines are reliable, cheap and plentiful - they are plug and play items
- TR6060 has a torque limit of 800Nm, wheelspin is most likely the torque limiter for this setup
- the weight is rear biased but not excessively, split as modelled is currently 43F/57R
- due to the space between the engines I have direct access to the standard corvette gearbox shift linkage - so direct "like a rifle bolt" shifts are easy to achieve
- I can also run the front bank exhausts through the same gap
Suspension and brakes are C6 corvette items, J55 brake option (Z51). Leaf springs are replaced by coilovers.
Spaceframe is all 4130 tubing, interior bulkheads and outer skin panels are composite material. Currently I am working on the surfacing models for the body panels, here is a snapshot of my progress to date - still a long way to go.
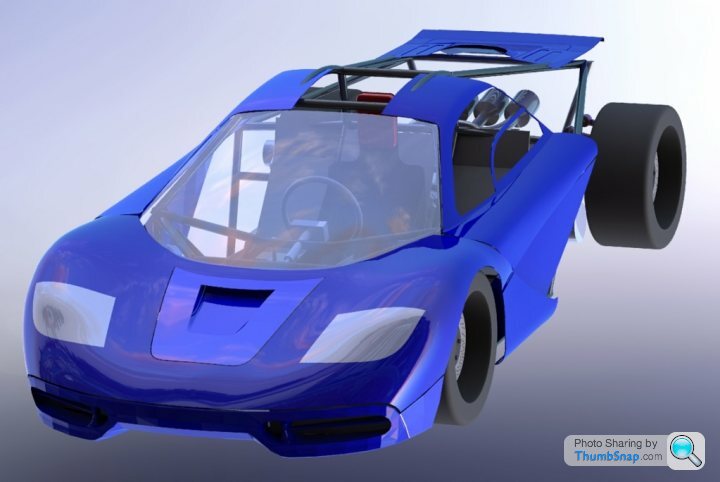
Target weight will be 1300Kg, mainly because this is the first car I have built from scratch so I am trying to be realistic. A full carbon composite chassis is not in my budget and is also harder to get road compliance with - but I will shave off weight wherever possible. Performance will still be good at that porky weight, however I can in the future change the cams and porting to get 350HP each, still natually aspirated. Turbo charging is also possible, the AR35TT uses the same block and heads and gives 550HP each, but 1100 is too much for the road. The gearbox life would most likely be shortened unacceptably at the level also. This is a daily driver & grand touring car, not a racecar and thus does not need bragging right HP numbers.
I think that suffices as an introduction, now for your comments...
Edited by F1natic on Saturday 18th July 08:03
Great plans!
Have a look at the 1GZ-FE engine. There's one for sale at the moment on fleabay for 2.8k.
Quite sophisticated for their time and lots of gearbox options are available. Not going to get to your power level NA, but they sound amazing with throttle bodies, or add a turbo setup to get your HP goals. Apparently a lot in common with 2 x 1/2JZ engines.
Have a look at the 1GZ-FE engine. There's one for sale at the moment on fleabay for 2.8k.
Quite sophisticated for their time and lots of gearbox options are available. Not going to get to your power level NA, but they sound amazing with throttle bodies, or add a turbo setup to get your HP goals. Apparently a lot in common with 2 x 1/2JZ engines.
Thanks guys, I assure you that this one will not be treated gently. Mad Mike Whiddett is based at the track (Hampton Downs) that I will be doing my initial reliability and system testing - so I can't imagine him resisting an offer to test it.
The crank harmonics between the engines is a real unknown, it is kind of experimental but like most things in engineering something similar has been done before - however in the link below they only achieved a 4000 Hp setup.
https://oldmachinepress.com/2017/04/20/ ... ft-engine/
In my setup both engines run completely independant of each other, and when 30 degrees out of synchronisation they may sound like a V12, however getting 2 ECU's to talk to each other and lag one to match the primary signal is uncharted territory. Would hate for it to sound like a poorly tuned V6, but it will be what it will be. I have also been told that clutches can walk so synch may be lost anyway, especially at higher horsepower levels. I love the sound of formula one engines on the rev limiter, like at Goodwood FOS. The roughness added a raw edge I quite liked the sound of. ECU's are Speeduino units designed in Australia by Josh Stewart - worth checking out if you like working with tunerstudio.
Currently I have the 2 factory standard V6's (1 still installed in my daily driver 2008 accord which I use to analyse the factory ECU parameters), all suspension control arms, spindles, rotors and calipers plus a porsche 911 steering rack, which is the only road car rack with a perpendicular pinion that i have found, however it is too short and needs to be lengthed to avoid bump steer with the C6 spindles. Currently have been given concept approval (4A) from LVVTA to complete the detail design drawings and submit for build permission (4B). Once that is done (next couple of months the way things are progressing) I can start cutting tubing, 3D printing my casting patterns (I have full access to an investment casting foundry with CMM, CNC mill and router, lathe etc) up to 120 Kg.
Got to clear a few things out of the rented workshop first. Build time for the rolling chassis is going to be a couple of years due to paycheck limits, and the body work will be a big stretch financially, but once I have the chassis sorted and proven then I can have plenty of fun while making the bodywork.
Glazing is currently my biggest hurdle, and using a windscreen from a genuine is out and nothing is even close as far as I have been able to tell so probably going to have to put a couple of sheets of flat glass on a CNC mould and drape it in a big kiln. A subcontractor I am talking with has successfully draped 40mm thick glass, I have a scale test run sheduled for early November.
The J35's have headifolds (more marmite anyone?) but that makes my fabrication job easier, pipes are same length front and back due and have to run through cats for compliance.
My testing plan is Thrash-Break-Fix-Repeat. The whole rear section will be on a subframe to allow easy removal for Tbox inspection and maintenance.
The crank harmonics between the engines is a real unknown, it is kind of experimental but like most things in engineering something similar has been done before - however in the link below they only achieved a 4000 Hp setup.
https://oldmachinepress.com/2017/04/20/ ... ft-engine/
In my setup both engines run completely independant of each other, and when 30 degrees out of synchronisation they may sound like a V12, however getting 2 ECU's to talk to each other and lag one to match the primary signal is uncharted territory. Would hate for it to sound like a poorly tuned V6, but it will be what it will be. I have also been told that clutches can walk so synch may be lost anyway, especially at higher horsepower levels. I love the sound of formula one engines on the rev limiter, like at Goodwood FOS. The roughness added a raw edge I quite liked the sound of. ECU's are Speeduino units designed in Australia by Josh Stewart - worth checking out if you like working with tunerstudio.
Currently I have the 2 factory standard V6's (1 still installed in my daily driver 2008 accord which I use to analyse the factory ECU parameters), all suspension control arms, spindles, rotors and calipers plus a porsche 911 steering rack, which is the only road car rack with a perpendicular pinion that i have found, however it is too short and needs to be lengthed to avoid bump steer with the C6 spindles. Currently have been given concept approval (4A) from LVVTA to complete the detail design drawings and submit for build permission (4B). Once that is done (next couple of months the way things are progressing) I can start cutting tubing, 3D printing my casting patterns (I have full access to an investment casting foundry with CMM, CNC mill and router, lathe etc) up to 120 Kg.
Got to clear a few things out of the rented workshop first. Build time for the rolling chassis is going to be a couple of years due to paycheck limits, and the body work will be a big stretch financially, but once I have the chassis sorted and proven then I can have plenty of fun while making the bodywork.
Glazing is currently my biggest hurdle, and using a windscreen from a genuine is out and nothing is even close as far as I have been able to tell so probably going to have to put a couple of sheets of flat glass on a CNC mould and drape it in a big kiln. A subcontractor I am talking with has successfully draped 40mm thick glass, I have a scale test run sheduled for early November.
The J35's have headifolds (more marmite anyone?) but that makes my fabrication job easier, pipes are same length front and back due and have to run through cats for compliance.
My testing plan is Thrash-Break-Fix-Repeat. The whole rear section will be on a subframe to allow easy removal for Tbox inspection and maintenance.
Edited by F1natic on Wednesday 21st August 14:02
Edited by F1natic on Wednesday 21st August 20:17
Wow, so much to appreciate here... wishing you all the best for the huge amount of work ahead. What an achievement it will be. Have you got as far as door seals? Having spent hundreds on them for an E46 coupe and what with Singer spending >$100billion on theirs, i’d hate for details like that to scupper your plans. Masses of good luck to you, please keep us updated.
Edited by anonymous-user on Wednesday 21st August 16:33
RelentlessForwardProgress said:
Have you got as far as door seals? Having spent hundreds on them for an E46 coupe and what with Singer spending >$100billion on theirs, i’d hate for details like that to scupper your plans. Masses of good luck to you, please keep us updated.
Thanks, and good question. I have a few options for extruded rubber seals suitable for a door system- www.pararubber.co.nz. -automotive clip on door seals. I may take a standard profile and cut most of the clip on section away and bond the remainder into a recess moulded into the door aperture. The F1 had a lot of thought gone into this critical detail, nothing worse than opening a dihedral door and dumping a bunch of water into the interior. NVH are another tricky matter and manufacturers spend millions lowering them (my LS400 is a superb example). Lots of sound deadening on the rear bulkhead and exhaust bandage over the exhausts should help.Edited by RelentlessForwardProgress on Wednesday 21st August 16:33
Oddly the doors are the first thing I am building on the test mule exterior, since i need to build an MDF seating buck to check my interior dimensions are comfortable before I committ them to steel. I am mocking up in full scale as much as possible since CAD is not always the most time effective solution. This buck will then be used as the mould for the carbon fiber interior. Plus in those gumption robbing phases of the build (we all have those) I will be able to sit in the buck and make car noises, which is actually important for positive visualisation and motivation. I might even hook up my PS3 and play GT6 in it, as I have setup the car parameters in the game and it is great fun to drive around the nurburgring virtually,.
Due to the unconventional nature of this build it is far easier to start with a clean slate and have all the critical parts in their final positions, then stitch everything together with tubing.
Edited by F1natic on Wednesday 21st August 18:51
Utterly epic and I salute you for doing this. I only have one negative though. Please don't try to make it look exactly like a F1. The engineering project that you are undertaking is so fantastic that I feel it would be a real shame for it to be written off as pastiche of the F1. By all means, the F1 should serve as inspiration and provide styling cues, but as you have gone your own way on the engineering, maybe go your own way on the styling. Make it truly yours.
Just my unqualified 2p's worth.
Just my unqualified 2p's worth.
Gassing Station | Readers' Cars | Top of Page | What's New | My Stuff