Bolt removal from rear hub carriers
Discussion
So just stripping the wishbones off to get them blasted along with the chassis. Slow going as everything is seized. Much releasing oil, blow torching etc required. 
Been trying to take the long lower bolts out of the rear aluminium hub carriers but they are stuck fast. Heating is difficult as the casting is big and I need to heat both sides at the same time, where the threaded rod passes through the casting and is probably seized.
This looks as if it could be a common issue given the design, anyone discovered a good technique to get these out without damaging the casting?
Cheers
Rob

Been trying to take the long lower bolts out of the rear aluminium hub carriers but they are stuck fast. Heating is difficult as the casting is big and I need to heat both sides at the same time, where the threaded rod passes through the casting and is probably seized.
This looks as if it could be a common issue given the design, anyone discovered a good technique to get these out without damaging the casting?
Cheers
Rob
The trouble is the bolt shank inside the casting swells with rust , pretty much making them impossible to get out.
I think there are people who will take the hub, get/ drill/ machine the old one out, drill and Bush the casting and supply and fit a new bolt/ rod.
I did my own, but I work/ worked in engineering so had people with the correct machine facilities.
It is doable DIY, but great care is needed.
You can crack the casting.
I think there are people who will take the hub, get/ drill/ machine the old one out, drill and Bush the casting and supply and fit a new bolt/ rod.
I did my own, but I work/ worked in engineering so had people with the correct machine facilities.
It is doable DIY, but great care is needed.
You can crack the casting.
Edited by GAjon on Monday 15th February 22:57
Speak to Neil if the job is beyond your workshop facilities

https://www.facebook.com/Transportation-and-Vehicl...
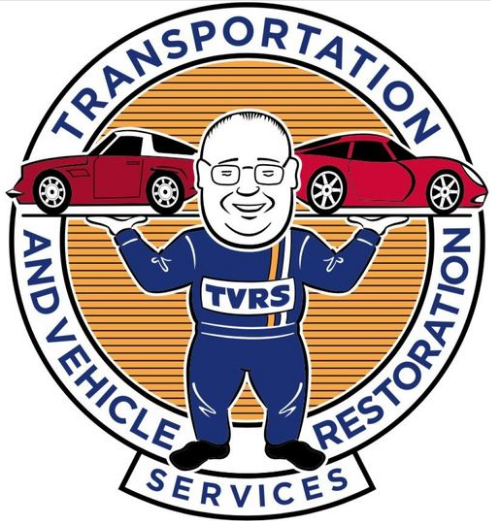
Cheers for the advice thus far.
Thinking about it, I suspect even if I could get those long bolts out it would end up damaging the hole in the casting, as pointed out above the bolts will have expanded with rust and will damage the casting hole on removal, then I'd have to get it machined/sleeved anyways.
I see on Facebook timeline of the specialist posted above they are doing this exact job by drilling out the hole bigger and using a thicker metric bolt which has been turned down and threaded UNC. Quite a nice solution.
Meantime I'm taking my chassis in for blasting, suspension components will need to be done later. I want to see what I have to deal with on the chassis repair side of things
Cheers
Rob
Thinking about it, I suspect even if I could get those long bolts out it would end up damaging the hole in the casting, as pointed out above the bolts will have expanded with rust and will damage the casting hole on removal, then I'd have to get it machined/sleeved anyways.
I see on Facebook timeline of the specialist posted above they are doing this exact job by drilling out the hole bigger and using a thicker metric bolt which has been turned down and threaded UNC. Quite a nice solution.
Meantime I'm taking my chassis in for blasting, suspension components will need to be done later. I want to see what I have to deal with on the chassis repair side of things

Cheers
Rob
Hi Rob,
do you think the Pivot Spindles are seized in the Alloy or seized in the Bonded Bushes.
I imagine the Bonded Bushes have a steel Tube in the middle. Maybe the biggest part of the problem is the Steel Tube in the Bonded Bushes that is rusted to the Pivot Spindle. With some heat on the Bonded Bush it will burn away the Rubber.
Alan
do you think the Pivot Spindles are seized in the Alloy or seized in the Bonded Bushes.
I imagine the Bonded Bushes have a steel Tube in the middle. Maybe the biggest part of the problem is the Steel Tube in the Bonded Bushes that is rusted to the Pivot Spindle. With some heat on the Bonded Bush it will burn away the Rubber.
Alan
plasticpig1972 said:
Hi Rob,
do you think the Pivot Spindles are seized in the Alloy or seized in the Bonded Bushes.
I imagine the Bonded Bushes have a steel Tube in the middle. Maybe the biggest part of the problem is the Steel Tube in the Bonded Bushes that is rusted to the Pivot Spindle. With some heat on the Bonded Bush it will burn away the Rubber.
Alan
Alan. Don't guess mate. you have either done them or you haven't do you think the Pivot Spindles are seized in the Alloy or seized in the Bonded Bushes.
I imagine the Bonded Bushes have a steel Tube in the middle. Maybe the biggest part of the problem is the Steel Tube in the Bonded Bushes that is rusted to the Pivot Spindle. With some heat on the Bonded Bush it will burn away the Rubber.
Alan

N.
plasticpig1972 said:
Hi Rob,
do you think the Pivot Spindles are seized in the Alloy or seized in the Bonded Bushes.
I imagine the Bonded Bushes have a steel Tube in the middle. Maybe the biggest part of the problem is the Steel Tube in the Bonded Bushes that is rusted to the Pivot Spindle. With some heat on the Bonded Bush it will burn away the Rubber.
Alan
Yea It's sized in the casting for sure. Steel bolts into aluminium is never a good move, super longs ones even more so. Factor in 40 years of road salt and they may as well have welded them in there. However I'm not beaten yet, my next move is to soak (immerse) the thing is a rust remover that's safe on aluminium (once it arrives) then releasing oil and a bit of heat. Then I'll be beaten!do you think the Pivot Spindles are seized in the Alloy or seized in the Bonded Bushes.
I imagine the Bonded Bushes have a steel Tube in the middle. Maybe the biggest part of the problem is the Steel Tube in the Bonded Bushes that is rusted to the Pivot Spindle. With some heat on the Bonded Bush it will burn away the Rubber.
Alan
I weld some flat bar onto the pivot rod to make it easier to grip in the vice. I suppose that the conducted heat of the welding might also help to break the galvanic corrosion between the pivot rod and the alloy casting. Then with the pivot rod clamped in the vice, I bolt a long bar onto the upright so that I can lever it back and forth. I then locally heat the casting around the pivot rod and use my long bar to put torsional stress on the joint until it (hopefully) eventually frees up. It’s risky but usually works.
calum62 said:
Yea It's sized in the casting for sure. Steel bolts into aluminium is never a good move, super longs ones even more so. Factor in 40 years of road salt and they may as well have welded them in there. However I'm not beaten yet, my next move is to soak (immerse) the thing is a rust remover that's safe on aluminium (once it arrives) then releasing oil and a bit of heat. Then I'll be beaten!
DO NOT DO ANY OF THE ABOVE 
N.
Right an update! I'm going to have to admit defeat on removal of the long bolts out of the hub carriers.
I filled the void inside the castings with Aluminium friendly rust remover and soaked it for 2 days. So that took most of the rust of the bolts (no noticeable effect on Al) . I then rinsed it out and dried it before filling it with diesel, I blow torched the outside where the bolts went through until they were good and hot and the diesel for near smoking. Idea being the aluminium would expand quicker than the steel and the diesel would wick into the bit sticking the bolt.
So gave the long bolts (the shock one and the bottom wishbone one) a bit of hammering with a medium faced mallet. No movement. So I used a MIG welder to put a blog of weld on the heads of the nuts for 2 sec to put some serious heat into them. Tried mallet again - no luck. Getting frustrated I dug out a small air hammer I have with a bolt chapping bit on it and gave the bolts a good rattle both sides alternating. No movement. I took it easy and had the thing dialed down for obvious reasons.
So stick a fork in me I'm done, will contacting a specialist (possibly the one above) to get them out, I could raise the stakes again and weld on the nuts proper and try and use them to turn the bolts and break them free but I dont think it's worth the risk of breaking the casting.
Plenty other battles to fight on the car and it's a learning curve so onwards and upwards
Regards
Rob
I filled the void inside the castings with Aluminium friendly rust remover and soaked it for 2 days. So that took most of the rust of the bolts (no noticeable effect on Al) . I then rinsed it out and dried it before filling it with diesel, I blow torched the outside where the bolts went through until they were good and hot and the diesel for near smoking. Idea being the aluminium would expand quicker than the steel and the diesel would wick into the bit sticking the bolt.
So gave the long bolts (the shock one and the bottom wishbone one) a bit of hammering with a medium faced mallet. No movement. So I used a MIG welder to put a blog of weld on the heads of the nuts for 2 sec to put some serious heat into them. Tried mallet again - no luck. Getting frustrated I dug out a small air hammer I have with a bolt chapping bit on it and gave the bolts a good rattle both sides alternating. No movement. I took it easy and had the thing dialed down for obvious reasons.
So stick a fork in me I'm done, will contacting a specialist (possibly the one above) to get them out, I could raise the stakes again and weld on the nuts proper and try and use them to turn the bolts and break them free but I dont think it's worth the risk of breaking the casting.
Plenty other battles to fight on the car and it's a learning curve so onwards and upwards

Regards
Rob
Gassing Station | TVR Classics | Top of Page | What's New | My Stuff