Maxi ball joints above or below arms?
Discussion
My kit uses the 'classic' maxi lower ball joint, transit drag link upper.
The instructions say to mount above the arm yet my mind says do that and 1/4 of the weight of the car is all is on two piddly little bolts (plus greater than the weight of the car when it hits a bump).
Mount it below and instead of trying to snap two bolts the force is spread over the entire flange of the ball joint, the bolts then only providing a stop against any inertia if the wheel is fully unloaded which to my mind is *much* better.
The haynes book is unclear (I'm not building a locost/haynes roadster but the arms are similar). I haven't found any pictures of it mounted below, only above. Then again I've found precious few even of that.
What does everyone else think?
The instructions say to mount above the arm yet my mind says do that and 1/4 of the weight of the car is all is on two piddly little bolts (plus greater than the weight of the car when it hits a bump).
Mount it below and instead of trying to snap two bolts the force is spread over the entire flange of the ball joint, the bolts then only providing a stop against any inertia if the wheel is fully unloaded which to my mind is *much* better.
The haynes book is unclear (I'm not building a locost/haynes roadster but the arms are similar). I haven't found any pictures of it mounted below, only above. Then again I've found precious few even of that.
What does everyone else think?
I've pondered this one before now as well. Don't think I came to any earth shattering conclusion really. The only slight change that would happen would be to effectively raise the shock mounting point ever so slightly. Can't see that having much impact TBH.
Impressive collection of Monodex swarf there
Impressive collection of Monodex swarf there

Will it even fit below the wishbone? It wouldn't on the arms I bought a while back, though could probably have been made to with a bit of filing. I know where you are coming from though, it doesn't look 'right'.
I'm still not convinced the Maxi balljoint is a good choice for this application, even though numerous '7' style kit cars use them. In the Maxi these joints are loaded in compression, and the joint sits in a properly machined part of the upright so neither the flange nor the ball and housing suffer the pull-out forces they will see when used like this.
I'm still not convinced the Maxi balljoint is a good choice for this application, even though numerous '7' style kit cars use them. In the Maxi these joints are loaded in compression, and the joint sits in a properly machined part of the upright so neither the flange nor the ball and housing suffer the pull-out forces they will see when used like this.
I think the powercoat would need removing on the lip but it should fit.
As a counterpoint TVR seem to have used both below

as well as above
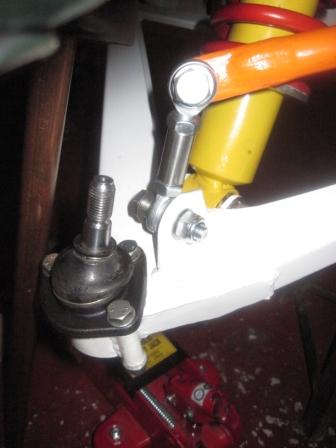
The TVR ones use 3-4 bolts though.
It is a slight worry the force on them, the argument is in the case of the locost that its a lightwight car, that doesn't wash quite so much when you get V8 powered versions and cars that are up to (or over) a ton.
If you look at the way mainstream manufacturers do it such as for example Mazda on the MX-5/RX-8 they reverse the ball joint, the force is then trying to push the ball in rather than pull it out.

As a counterpoint TVR seem to have used both below

as well as above
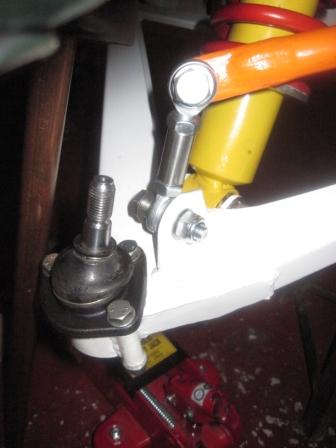
The TVR ones use 3-4 bolts though.
It is a slight worry the force on them, the argument is in the case of the locost that its a lightwight car, that doesn't wash quite so much when you get V8 powered versions and cars that are up to (or over) a ton.
If you look at the way mainstream manufacturers do it such as for example Mazda on the MX-5/RX-8 they reverse the ball joint, the force is then trying to push the ball in rather than pull it out.

GinG15 said:
old thread, but interesting for me:
most seven-ish kitcars have mounted them above the wishbone
mounting them below the wishbone, the pivot point would also move donwards, which would be better for the general geometry and settings..or not?

It would probably be better to mount them as designed, rather than introduce random geometry changes.most seven-ish kitcars have mounted them above the wishbone
mounting them below the wishbone, the pivot point would also move donwards, which would be better for the general geometry and settings..or not?

Edited by GinG15 on Sunday 3rd December 08:58
GinG15 said:
old thread, but interesting for me:
most seven-ish kitcars have mounted them above the wishbone
mounting them below the wishbone, the pivot point would also move donwards, which would be better for the general geometry and settings..or not?

Mounting under or over will only slightly change the effective installed height of the spring/damper, which you can likely adjust for. The geometry is set by the relationship between the balljoint ball centre (which is in turn defined by upright and wheel/tyre) and the suspension bracket on the chassis. The wishbone itself just holds those parts at the desired location, what matters is the virtual straight line that joins chassis bracket to balljoint centre.most seven-ish kitcars have mounted them above the wishbone
mounting them below the wishbone, the pivot point would also move donwards, which would be better for the general geometry and settings..or not?

Edited by GinG15 on Sunday 3rd December 08:58
Ideally, mount the joint in the same way it was intended to be on the donor car, so the loads are applied as intended. Basically, is it supposed to hang from the joint, or sit on top of it.
Edited by Chris-S on Tuesday 5th December 14:34
Paul Drawmer said:
It would probably be better to mount them as designed, rather than introduce random geometry changes.
so tell me how they are desinged?in the maxi they are functioning as upper and lower all joint...so not really compareable in terms of fixing
Edited by GinG15 on Wednesday 6th December 20:48
If it's any help, the Westfield has them on top of the wishbone platform, so the car hangs from the joint, the weight carried by those two bolts. An 8.8 M8 bolt has a proof rating of 3.4T if I read the data correctly. Should be good for the front of a 7.
It's a few years since I messed with balljoints on the Westy so I can't recall for sure...but, I think there is an obviously flat machined face and a not so obviously flat one. One would expect the joint to sit on the properly flat face. Also, the boot could make it awkward if not impossible to fit it under the wishbone.
Using the same joints top and bottom though, that could be misleading, as the upper wishbone has very little vertical load in it, so Austin probably didn't see a need to use a different joint - assuming(!) that the joint is even sensitive to the direction that loads are applied. I honestly don't know if they are or not.
I 'think' that the joint has a lower small cup and a spring that keeps the ball pressed against the main upper cup - that squares with the notion that it is designed to take loads that try to pull the ball out of the top, rather than press it into the bottom.
Hope that helps??
It's a few years since I messed with balljoints on the Westy so I can't recall for sure...but, I think there is an obviously flat machined face and a not so obviously flat one. One would expect the joint to sit on the properly flat face. Also, the boot could make it awkward if not impossible to fit it under the wishbone.
Using the same joints top and bottom though, that could be misleading, as the upper wishbone has very little vertical load in it, so Austin probably didn't see a need to use a different joint - assuming(!) that the joint is even sensitive to the direction that loads are applied. I honestly don't know if they are or not.
I 'think' that the joint has a lower small cup and a spring that keeps the ball pressed against the main upper cup - that squares with the notion that it is designed to take loads that try to pull the ball out of the top, rather than press it into the bottom.
Hope that helps??
Chris-S said:
Using the same joints top and bottom though, that could be misleading, as the upper wishbone has very little vertical load in it, so Austin probably didn't see a need to use a different joint - assuming(!) that the joint is even sensitive to the direction that loads are applied. I honestly don't know if they are or not.
In the Maxi the heavily loaded ball joint is on the upper wishbone, and is therefore loaded in compression only. The joint on the lower wishbone sees no pull-out forces. This is why they are not a good choice for a conventional double wishbone style suspension like the 7 has. OTOH the Cortina balljoint is designed to be used in this position.Mr2Mike said:
Chris-S said:
Using the same joints top and bottom though, that could be misleading, as the upper wishbone has very little vertical load in it, so Austin probably didn't see a need to use a different joint - assuming(!) that the joint is even sensitive to the direction that loads are applied. I honestly don't know if they are or not.
In the Maxi the heavily loaded ball joint is on the upper wishbone, and is therefore loaded in compression only. The joint on the lower wishbone sees no pull-out forces. This is why they are not a good choice for a conventional double wishbone style suspension like the 7 has. OTOH the Cortina balljoint is designed to be used in this position.As since I posted the original however I utterly changed my mind on the front suspension and have re-designed it with new uprights. A change to Cortina balljoints located in their original design locations might be a good change to make as well before I commit the lower arms to metal.
I am not aware of any bottom ball joint bolts failing, despite them taking the load in tension.
We need to consider where the load was intended to be applied by the original designer of the ball joint.
I am guessing that we don't hear of issues as kit cars tend not to do high miles and don't suffer the same level of fatigue that would be considered and designed around production tin tops. Kit cars do not carry the same mass on the ball joints so even upside down and fully loaded there appears to be no issue.
The lower ball joint is upside down on kit cars compared to the pictures below. The load on a Mini is on the top arm pushing it down not on the bottom one pushing it down against the ball fixings as we generally see on kit cars.
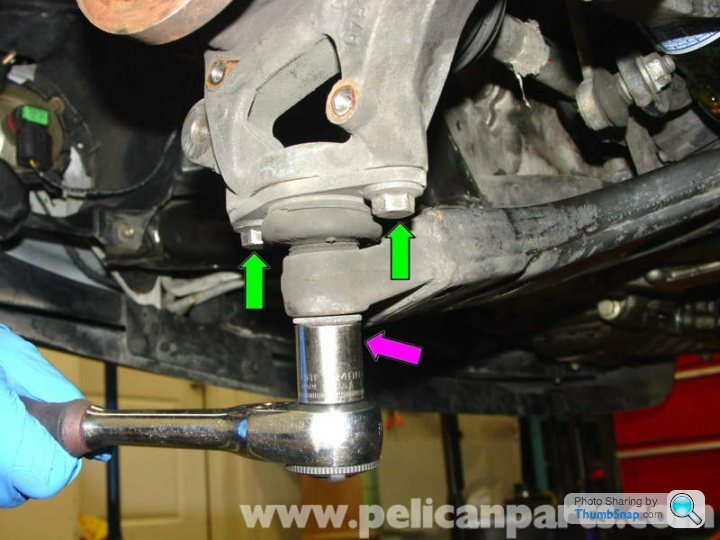
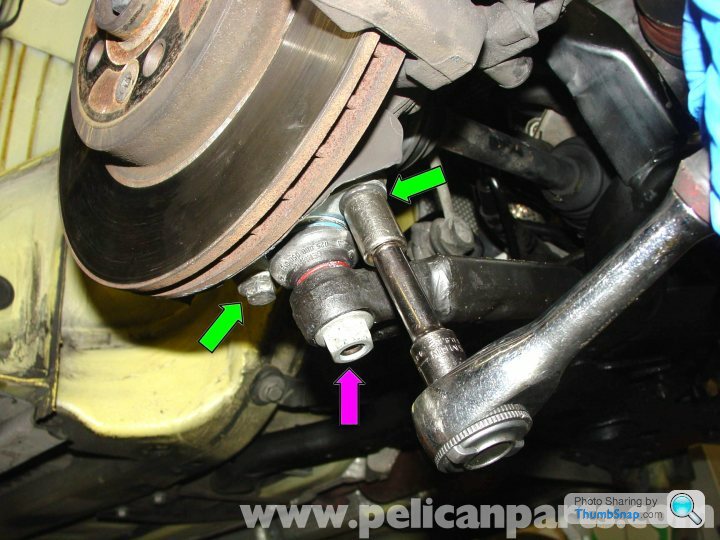
On an MX5/Exocet there is a 12mm bolt pinning the lower joint so it is in shear mode. Then another 12mm bolt stopping the joint from rotating.
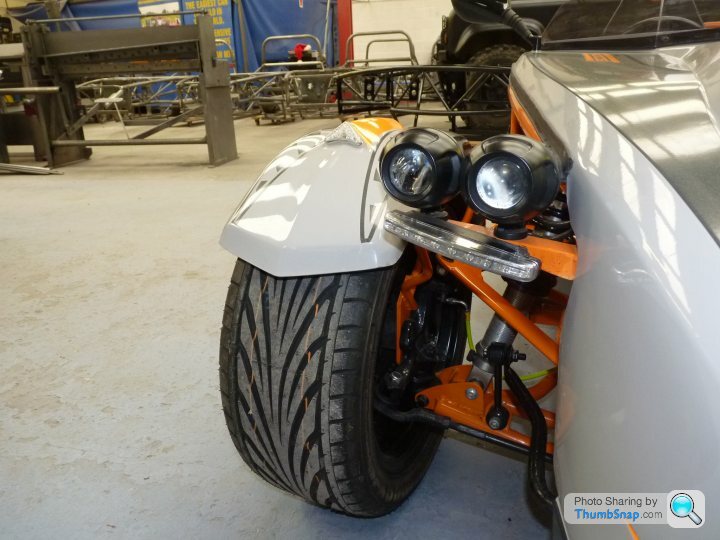
We need to consider where the load was intended to be applied by the original designer of the ball joint.
I am guessing that we don't hear of issues as kit cars tend not to do high miles and don't suffer the same level of fatigue that would be considered and designed around production tin tops. Kit cars do not carry the same mass on the ball joints so even upside down and fully loaded there appears to be no issue.
The lower ball joint is upside down on kit cars compared to the pictures below. The load on a Mini is on the top arm pushing it down not on the bottom one pushing it down against the ball fixings as we generally see on kit cars.
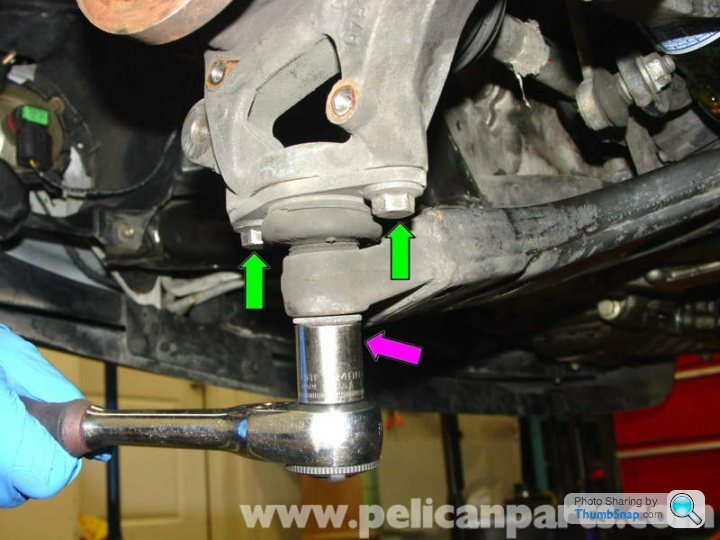
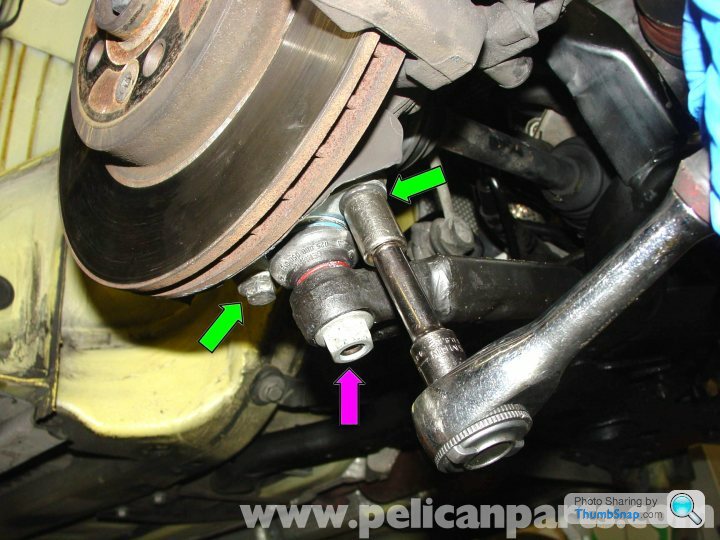
On an MX5/Exocet there is a 12mm bolt pinning the lower joint so it is in shear mode. Then another 12mm bolt stopping the joint from rotating.
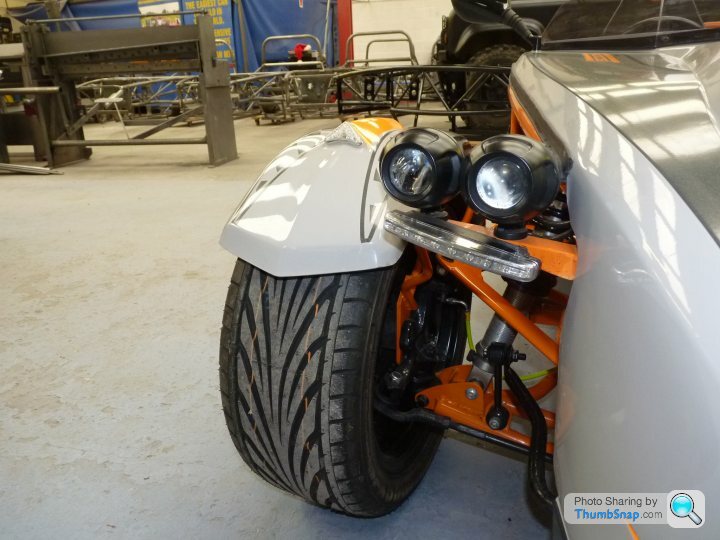
Mr2Mike said:
In the Maxi the heavily loaded ball joint is on the upper wishbone, and is therefore loaded in compression only. The joint on the lower wishbone sees no pull-out forces. This is why they are not a good choice for a conventional double wishbone style suspension like the 7 has. OTOH the Cortina balljoint is designed to be used in this position.
Oops, my bad! Thought it was the other way round. In my defence, its probably 40 years since I last touched a Maxi or anything BL.Apologies for the duff information.
Edited by Chris-S on Thursday 7th December 13:03
Gassing Station | Kit Cars | Top of Page | What's New | My Stuff