What MIG welder?
Discussion
I am looking for a MIG welder that is sufficient to be able to weld 38mm mild steel tubing for a chassis repair. There are a wide variety of used MIGs on eBay, but which one is ok?
http://www.ebay.co.uk/itm/NEW-Welding-machine-weld...
http://www.ebay.co.uk/itm/PX-TO-CLEAR-CLOOS-GLC-25...
http://www.ebay.co.uk/itm/Cebora-Gasless-Mig-Welde...
http://www.ebay.co.uk/itm/MULTIPROCESS-INVERTER-WE...
Single phase, three phase, 160amp, 190amp.... I just want to practice welding, and then have a go at sorting my chassis.
All I do know is, I don't want a gasless MIG. Apparently they are s
t 
Any constructive help greatly appreciated.
Regards
Cad
http://www.ebay.co.uk/itm/NEW-Welding-machine-weld...
http://www.ebay.co.uk/itm/PX-TO-CLEAR-CLOOS-GLC-25...
http://www.ebay.co.uk/itm/Cebora-Gasless-Mig-Welde...
http://www.ebay.co.uk/itm/MULTIPROCESS-INVERTER-WE...
Single phase, three phase, 160amp, 190amp.... I just want to practice welding, and then have a go at sorting my chassis.
All I do know is, I don't want a gasless MIG. Apparently they are s


Any constructive help greatly appreciated.
Regards
Cad
Firstly, of greater importance than the tube diameter is the thickness.
Secondly, you do not need 3-phase, in fact you haven't a 3-phase socket in your house, so would then need a converter, which costs as much as the welder again.
Thirdly, you do not want gasless, they are simply not as good for anything structural.
What you want I suspect is a 100 - 130 amp gas mig, then the answer to a couple of questions will help narrow the search down.
Is it something you will keep & use again?
What is your budget?
A quick look on the bay that is e came up with this, which should be a good starter mig.
http://www.ebay.co.uk/itm/Sealey-130Amp-Mig-Welder...
Secondly, you do not need 3-phase, in fact you haven't a 3-phase socket in your house, so would then need a converter, which costs as much as the welder again.
Thirdly, you do not want gasless, they are simply not as good for anything structural.
What you want I suspect is a 100 - 130 amp gas mig, then the answer to a couple of questions will help narrow the search down.
Is it something you will keep & use again?
What is your budget?
A quick look on the bay that is e came up with this, which should be a good starter mig.
http://www.ebay.co.uk/itm/Sealey-130Amp-Mig-Welder...
Edited by andyiley on Thursday 26th February 08:29
Andy, thanks for the reply.
The tube as standard from TVR is 2mm thick. But I may rebuild with 3mm. The sections will be cut, a smaller diameter tube will be sleeved inside the existing chassis tube, and inside the new tube. Can you seam weld with the MIG you suggested? Not that I even know yet what seam welding is. I'm assuming it's a run of weld, not blobs..
The welder is something I can see myself keeping. But even if for some reason I didn't, I could move it on via eBay.
My budget is up to the £200ish mark.
Cheers
Cad
The tube as standard from TVR is 2mm thick. But I may rebuild with 3mm. The sections will be cut, a smaller diameter tube will be sleeved inside the existing chassis tube, and inside the new tube. Can you seam weld with the MIG you suggested? Not that I even know yet what seam welding is. I'm assuming it's a run of weld, not blobs..
The welder is something I can see myself keeping. But even if for some reason I didn't, I could move it on via eBay.
My budget is up to the £200ish mark.
Cheers
Cad
caduceus said:
Andy, thanks for the reply.
The tube as standard from TVR is 2mm thick. But I may rebuild with 3mm. The sections will be cut, a smaller diameter tube will be sleeved inside the existing chassis tube, and inside the new tube. Can you seam weld with the MIG you suggested? Not that I even know yet what seam welding is. I'm assuming it's a run of weld, not blobs..
The welder is something I can see myself keeping. But even if for some reason I didn't, I could move it on via eBay.
My budget is up to the £200ish mark.
Cheers
Cad
Seam welding is exactly that, and any mig will seam weld, the trick is to only weld to good steel with clean bright surfaces a good quality angle grinder is vital in this.The tube as standard from TVR is 2mm thick. But I may rebuild with 3mm. The sections will be cut, a smaller diameter tube will be sleeved inside the existing chassis tube, and inside the new tube. Can you seam weld with the MIG you suggested? Not that I even know yet what seam welding is. I'm assuming it's a run of weld, not blobs..
The welder is something I can see myself keeping. But even if for some reason I didn't, I could move it on via eBay.
My budget is up to the £200ish mark.
Cheers
Cad
2mm and even 3mm is fine with a 130 amp welder, the biggest thing to look for is good controls allowing different settings, and a good duty ratio (time on over time off) as that lets you weld for long times.
If I was welding structural tube (as I have before) I would sleeve internally and externally and drill 4 x large holes through the outer skin of each to plug weld through also.
andyiley said:
and a good duty ratio (time on over time off) as that lets you weld for long times.

andyiley said:
If I was welding structural tube (as I have before) I would sleeve internally and externally and drill 4 x large holes through the outer skin of each to plug weld through also.
Where exactly would these be? I'd need a diagram tbh. I have NO welding experience.caduceus said:
andyiley said:
and a good duty ratio (time on over time off) as that lets you weld for long times.

andyiley said:
If I was welding structural tube (as I have before) I would sleeve internally and externally and drill 4 x large holes through the outer skin of each to plug weld through also.
Where exactly would these be? I'd need a diagram tbh. I have NO welding experience.If you had a 40mm tube to join, you would drill 2 holes staggered at each end of the pipe, for arguments sake 12mm holes.
Then cut a length of pipe just under 40mm, say 100mm long. You then weld through the holes in the outer pipe to join it to the inner pipe, along with seam welding the joint of the pipe.
You then do the same with a pipe just over 40mm, with the same holes. You then seam weld both ends of the bigger sleeve, and weld through the holes to add further weld metal & strength.
You then have the strongest tubular repair possible.
Here's a pic of what andyiley is talking about.
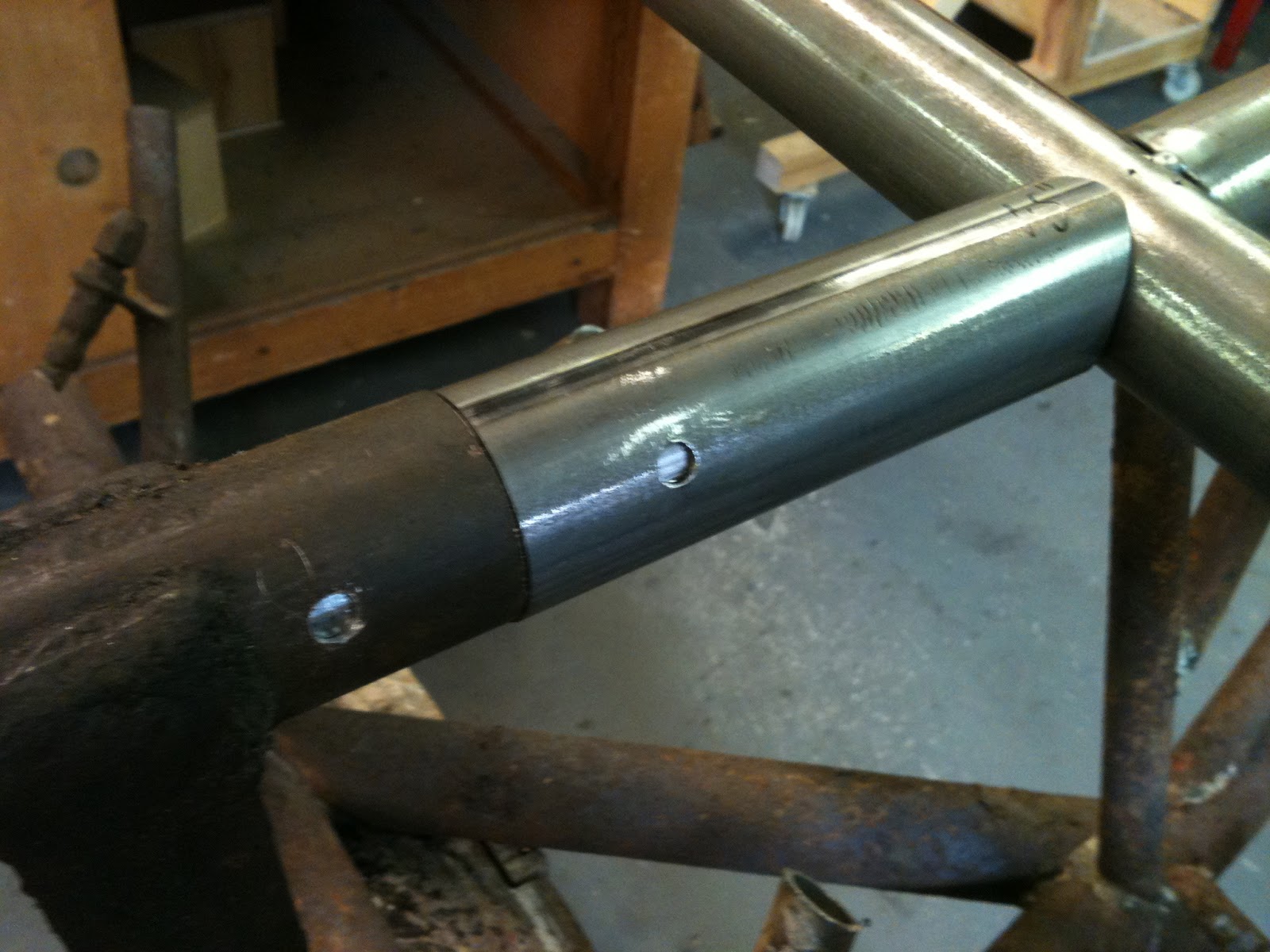
New tube being joined to old, a piece of tube has already been inserted, the hole in both ends would be filled with weld, and the joint itself welded. You don't normally just weld up the two edges at the joint as you see in that picture - you'd bevel the edges or leave a small gap between them that will be filled with weld. You do this to get the most penetration that you can.
In this pic you can see the insert has been plug welded to one of the tubes

The point of doing this is it adds strength to the joint between the two outer tubes.
Here is another one, ready for the joint to be welded

Please spend some time over at www.mig-welding.co.uk. Heed the advice given there and in its forums too.
To be brutally honest, you need to up your budget. Even if you got a machine for £200 you need to get wire, a gas bottle, gloves, clamps, angle grinder, cutting & grinding discs and a helmet, easily budget £170 for that stuff. Cheapest way for gas is probably a hobbygas cylinder (no contract, you buy a bottle and pay for refills), the disposable ones from halfords etc won't last 5 minutes, the rest of the kit is needed to do the job.
Note: if you going to want to notch tubing to fit together (as in the far right of the first picture) you need some way to notch the tube neatly. You can buy specific tools for this, but they are expensive. This is the cheap way of doing it : http://www.frost.co.uk/tubing-notcher-hole-saw-set... . You can notch them with angle grinders and files, but it'll kill your productivity because it'll take so long and you'll end up with inferior fit.
Aside from that you aren't going to get a decent machine for £200, unless you go second hand. I would suggest you need a minimum of a 130 amp machine, preferably 150.
Avoid SIP machines, which are known to have poor wire feeds. You will also see many cheap chinese MIGs on ebay, you'll be amazed to hear there is a reason why they are cheap!
Clarke are at the lower end of the "stuff worth buying" market. The MIG welding forum will try and talk you in to a portamig, best sit down when you see the price ! They do have valid reasons for this suggestion but I think a Clarke will probably do you fine.
Do consider secondhand, stick to the bigger names. I'd like to see the machine work before forking out cash.
This could be a good by as long as it doesnt go crazy over the next day (currently £155)
http://www.ebay.co.uk/itm/Clarke-Mig-Welder-Turbo-...
New tube being joined to old, a piece of tube has already been inserted, the hole in both ends would be filled with weld, and the joint itself welded. You don't normally just weld up the two edges at the joint as you see in that picture - you'd bevel the edges or leave a small gap between them that will be filled with weld. You do this to get the most penetration that you can.
In this pic you can see the insert has been plug welded to one of the tubes

The point of doing this is it adds strength to the joint between the two outer tubes.
Here is another one, ready for the joint to be welded
Please spend some time over at www.mig-welding.co.uk. Heed the advice given there and in its forums too.
To be brutally honest, you need to up your budget. Even if you got a machine for £200 you need to get wire, a gas bottle, gloves, clamps, angle grinder, cutting & grinding discs and a helmet, easily budget £170 for that stuff. Cheapest way for gas is probably a hobbygas cylinder (no contract, you buy a bottle and pay for refills), the disposable ones from halfords etc won't last 5 minutes, the rest of the kit is needed to do the job.
Note: if you going to want to notch tubing to fit together (as in the far right of the first picture) you need some way to notch the tube neatly. You can buy specific tools for this, but they are expensive. This is the cheap way of doing it : http://www.frost.co.uk/tubing-notcher-hole-saw-set... . You can notch them with angle grinders and files, but it'll kill your productivity because it'll take so long and you'll end up with inferior fit.
Aside from that you aren't going to get a decent machine for £200, unless you go second hand. I would suggest you need a minimum of a 130 amp machine, preferably 150.
Avoid SIP machines, which are known to have poor wire feeds. You will also see many cheap chinese MIGs on ebay, you'll be amazed to hear there is a reason why they are cheap!
Clarke are at the lower end of the "stuff worth buying" market. The MIG welding forum will try and talk you in to a portamig, best sit down when you see the price ! They do have valid reasons for this suggestion but I think a Clarke will probably do you fine.
Do consider secondhand, stick to the bigger names. I'd like to see the machine work before forking out cash.
This could be a good by as long as it doesnt go crazy over the next day (currently £155)
http://www.ebay.co.uk/itm/Clarke-Mig-Welder-Turbo-...
Edited by Crafty_ on Thursday 26th February 22:12
If you need a mask, gloves etc, one of these bundles on evilbay will likely do just fine.
I bought one of the red ones a few years back and it has been great.
Comes with a few spares anti spatter lenses which you will need if you are welding under a car and you can't give yourself a flash.
Adding the link would be good wouldn't it.
http://www.ebay.co.uk/itm/Auto-Darkening-Solar-Wel...
I bought one of the red ones a few years back and it has been great.
Comes with a few spares anti spatter lenses which you will need if you are welding under a car and you can't give yourself a flash.
Adding the link would be good wouldn't it.

http://www.ebay.co.uk/itm/Auto-Darkening-Solar-Wel...
Edited by longshot on Thursday 26th February 23:40
First off, thanks so much for all the replies gents. Much appreciated.
I've been watching MIG tutorials this evening and there's some informative stuff on youtube. Enjoyed watching it.
Thank you Andy and Crafty for the detailed descriptions. I'll look at them more tomorrow.
That Clarke MIG is now up to £207 already. So I assume it's going to be a lot more by auction end.
Will this one be adequate?
http://www.ebay.co.uk/itm/Sealey-SUPERMIG150-Profe...
Thanks again
Cad
I've been watching MIG tutorials this evening and there's some informative stuff on youtube. Enjoyed watching it.
Thank you Andy and Crafty for the detailed descriptions. I'll look at them more tomorrow.
That Clarke MIG is now up to £207 already. So I assume it's going to be a lot more by auction end.
Will this one be adequate?
http://www.ebay.co.uk/itm/Sealey-SUPERMIG150-Profe...
Thanks again
Cad
I have that exact model and it's an excellent unit. 100% duty cycle on the 30A setting (which is more than enough for 3mm steel), easy to set up and spares are readily available from MachineMart etc.
The only thing that isn't great is the regulator - it needs a very fine touch to get the right gas flow, a metered one for about £25 would be a wise investment.
The only thing that isn't great is the regulator - it needs a very fine touch to get the right gas flow, a metered one for about £25 would be a wise investment.
Krikkit said:
I have that exact model and it's an excellent unit. 100% duty cycle on the 30A setting (which is more than enough for 3mm steel), easy to set up and spares are readily available from MachineMart etc.
The only thing that isn't great is the regulator - it needs a very fine touch to get the right gas flow, a metered one for about £25 would be a wise investment.
The only thing that isn't great is the regulator - it needs a very fine touch to get the right gas flow, a metered one for about £25 would be a wise investment.
One like this? http://www.ebay.co.uk/itm/Flow-Meter-For-Welding-G...
Thanks for the advice. Appreciate it.
Cad
I've just been looking again at the http://www.ebay.co.uk/itm/Sealey-SUPERMIG150-Profe... and there only appears to be 4 power settings, which could be an issue. The setting I'd need for 3 or 4mm is going to be 'max' '2' on the Sealey 150. Which means the thermal cut out switch will be interrupting proceedings won't it?
I think I'm going to have to bite the bullet and go for the http://www.ebay.co.uk/itm/151070819775?_trksid=p20... which is £160 more
But, it's a good investment, and will save me money in the long run I imagine (keep telling myself this..)
If I'm wrong in assuming this could someone correct me pls
I think I'm going to have to bite the bullet and go for the http://www.ebay.co.uk/itm/151070819775?_trksid=p20... which is £160 more

But, it's a good investment, and will save me money in the long run I imagine (keep telling myself this..)
If I'm wrong in assuming this could someone correct me pls

No, it won't be cutting out all the time, it will let you weld for a couple of minutes constant & then demand a break, do you know how infrequently that will actually interrupt you? A few times an hour, it is not often you would actually do that.
I have welded 6mm thick steel with a 150 amp welder many times before with no issues, I have fitted 3mm steel to a car for a full cage and fitted a full cage with a 150amp welder without it ever cutting out in a full weekends welding with no problems.
Trust me 150amp is better than good enough for anything up to professional 24/7 use.
I have welded 6mm thick steel with a 150 amp welder many times before with no issues, I have fitted 3mm steel to a car for a full cage and fitted a full cage with a 150amp welder without it ever cutting out in a full weekends welding with no problems.
Trust me 150amp is better than good enough for anything up to professional 24/7 use.
the power selection is a good point, having only a few choices can make it a bit more difficult.
If you are at that sort of price point you open up a lot of other possibilities. I did suggest r-tech but they don't have a machine that fits budget that would be something I'd entertain.
I agree with the above, 150amp is going to do what you need all day long.
If you are at that sort of price point you open up a lot of other possibilities. I did suggest r-tech but they don't have a machine that fits budget that would be something I'd entertain.
I agree with the above, 150amp is going to do what you need all day long.
Edited by Crafty_ on Friday 27th February 17:05
Gassing Station | Home Mechanics | Top of Page | What's New | My Stuff