Why do electricicty generating windmills have 3 blades?
Discussion
If they had two blades, the blades would need to be longer to achieve the same power output.
Longer blades = taller mast = stability issues and other problems.
It is a compromise. Less blades are more efficient due to turblance issues, but require a larger radius for a given power output.
Vice versa, that is why some prop planes have two, three or four blade props. They usually use more blades and smaller diameter props to stop them hitting the ground! The trade off is efficiency.
Longer blades = taller mast = stability issues and other problems.
It is a compromise. Less blades are more efficient due to turblance issues, but require a larger radius for a given power output.
Vice versa, that is why some prop planes have two, three or four blade props. They usually use more blades and smaller diameter props to stop them hitting the ground! The trade off is efficiency.
There are some interesting papers discussing aerofoil section and swept area, especially in regard to wind turbines.
A casual thought is "if we are trying to capture the wind, why don't turbines have more blades to fill up the capture area a bit more"??
However, the critical fact is the ratio of velocities between blade speed that is perpendicular to the wind direction and wind speed! It turns out that vortex effects and trailing aerodynamic phenomina mean a high open area blade design (ie, just 3 long blades) is in fact the most efficient way of capturing the momentum energy of the passing air.
ie:

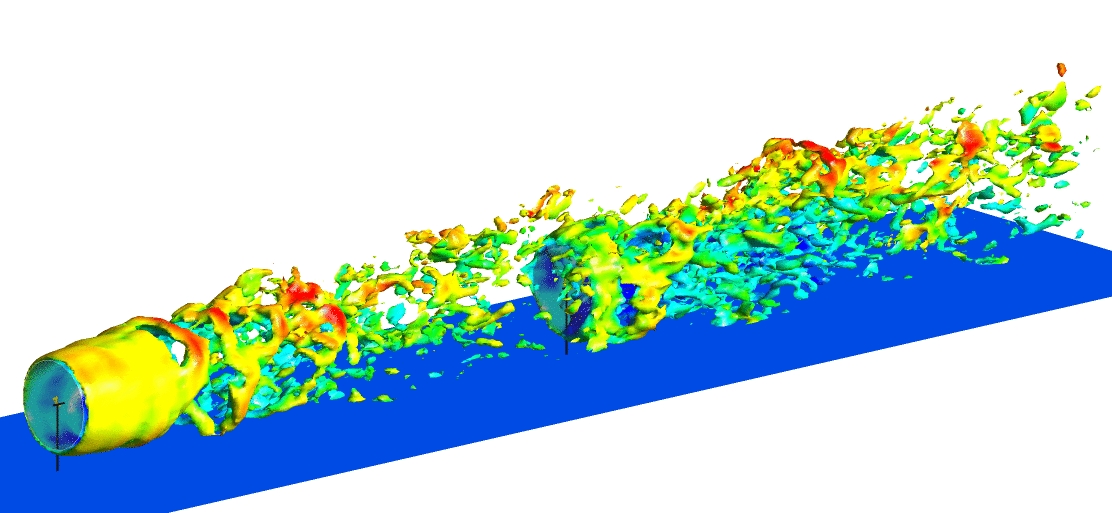
In all cases (aeroplane or wind turbine) you need to get your blade tip speed close to supersonic for max power, but an aeroplane is generally going forwards at say 300mph, whereas the wind is generally blowing at less than 100mph. As such, blade area vs swept area is biased to suit the prevailing speed ratio.
A casual thought is "if we are trying to capture the wind, why don't turbines have more blades to fill up the capture area a bit more"??
However, the critical fact is the ratio of velocities between blade speed that is perpendicular to the wind direction and wind speed! It turns out that vortex effects and trailing aerodynamic phenomina mean a high open area blade design (ie, just 3 long blades) is in fact the most efficient way of capturing the momentum energy of the passing air.
ie:

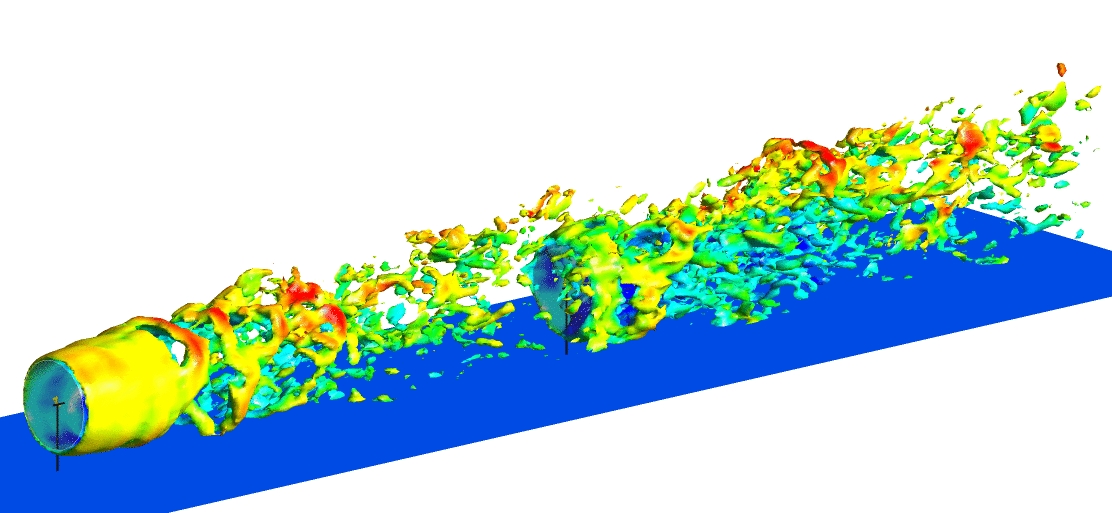
In all cases (aeroplane or wind turbine) you need to get your blade tip speed close to supersonic for max power, but an aeroplane is generally going forwards at say 300mph, whereas the wind is generally blowing at less than 100mph. As such, blade area vs swept area is biased to suit the prevailing speed ratio.
Edited by anonymous-user on Tuesday 11th August 10:45
Slightly off topic, but those CFD images looks like the cell growth away from the turbines is excessive and there appears to be some large cells within the tip vortices which maybe a problem if they're trying to pedict turbulent behaviour. There's been a lot of work done at Liverpool uni on the vortex breakdown aft of the turbines, particularly in respect of operating aircraft in the vicinity of them and several cases of wake encounters have been reported by the CAA.
Some of the latest work has shown that predicting where the tip vortices breakdown is dependant on the mesh density as you'd expect, and coarser meshes significantly underestimate the distance which the turbulence propagates. This is due to some of the small scale, high frequency turbulent structures that are smaller than the cell size being numerically damped out in the simulation. One of the guys in my office was generating meshes with sub millimetre cells and cell counts of nearly three billion!! In comparison my meshes for frigate sized ships average 8 to 20 million.
TL;DR CFD is complex, but the pictures look pretty...
Some of the latest work has shown that predicting where the tip vortices breakdown is dependant on the mesh density as you'd expect, and coarser meshes significantly underestimate the distance which the turbulence propagates. This is due to some of the small scale, high frequency turbulent structures that are smaller than the cell size being numerically damped out in the simulation. One of the guys in my office was generating meshes with sub millimetre cells and cell counts of nearly three billion!! In comparison my meshes for frigate sized ships average 8 to 20 million.
TL;DR CFD is complex, but the pictures look pretty...
This is fascinating. Not a topic that has kept me awake at nights but I too had always vaguely assumed that the more the merrier.
The early Spitfires had two blades but later versions went up to about 5 I believe (CBA to check). Presumably because the engine got more powerful but 10' high landing gear was a bit impractical.......
The early Spitfires had two blades but later versions went up to about 5 I believe (CBA to check). Presumably because the engine got more powerful but 10' high landing gear was a bit impractical.......
Long blades generally provide a better 'grab' on the passing air. As in they have a better lift to drag ratio, hence why gliders will have long thin wings/blades as opposed to short fat ones.
So length of the blade is a factor for efficiency.
The other factor that has been pointed out is that the longer the blade the higher it has to be mounted off the ground.
And there is a trade-off between how much support and strength has to be built in to the overall turbine in order to keep it safe from gusts and direction change of wind flow.
And the more strength you build in to a system, it generally results in more weight.
The more weight you have in the system the more force required to overcome inertia in order to get/keep the blades moving in a constantly changing velocity of wind.
So length of the blade is a factor for efficiency.
The other factor that has been pointed out is that the longer the blade the higher it has to be mounted off the ground.
And there is a trade-off between how much support and strength has to be built in to the overall turbine in order to keep it safe from gusts and direction change of wind flow.
And the more strength you build in to a system, it generally results in more weight.
The more weight you have in the system the more force required to overcome inertia in order to get/keep the blades moving in a constantly changing velocity of wind.
Dogwatch said:
The early Spitfires had two blades but later versions went up to about 5 I believe (CBA to check). Presumably because the engine got more powerful but 10' high landing gear was a bit impractical.......
Yep, from about 950hp to 2,000hp. And technology advanced too, eg metal blades and constant speed mechanisms.tapkaJohnD said:
So those multi-bladed, complete-circle wind mill water pumps, so favoured on prairie farms in Westerns, are no good?
Well doggone! That low-down, no-good son of a snake sold me a bummer!
John (not Wayne)
Actually, quite the opposite!Well doggone! That low-down, no-good son of a snake sold me a bummer!
John (not Wayne)
The less the difference between blade rotation speed (perpendicular to the wind direction) and the wind speed itself, then more static blade area you need to capture the energy!
Those old style water pumps like this:

Revolve slowly (otherwise they would fly apart!). Hence the effective angle of the thrust vector is much closer to the basic direction of the wind, and so you need lots of blade area to capture the energy. On a high speed wing, the cord can be kept thin, because the effective swept area is much larger as the velocity vector is really virtually parallel to the blades themselves (and perpendicular to the wind direction)
Gassing Station | Science! | Top of Page | What's New | My Stuff