Retrorockets, space and movement, muse of the day.
Discussion
Was wondering 
On earth 'Every Action has an Equal and Opposite Reaction', so whatever the forces applied are also returned likewise.
In Space i believe is pretty much a vacuum? So how do retrorockets work if their is nothing for the energy released to push on to propel the object away from the retrorockets forces.
Often in films you see a Spaceman who gets pushed off his craft and floats forevermore unless he fires a jet in the opposite direction but again without anything in a vacuum to push off i don't get it.
I know I'm wrong but whats happens to make this correct?

On earth 'Every Action has an Equal and Opposite Reaction', so whatever the forces applied are also returned likewise.
In Space i believe is pretty much a vacuum? So how do retrorockets work if their is nothing for the energy released to push on to propel the object away from the retrorockets forces.
Often in films you see a Spaceman who gets pushed off his craft and floats forevermore unless he fires a jet in the opposite direction but again without anything in a vacuum to push off i don't get it.
I know I'm wrong but whats happens to make this correct?
TheEnd said:
It's the rocket exhaust, so the rocket spews out crap in one direction, and the rocket goes the other way.
This is where things like ion engines come in handy, as your craft needs to carry plenty of stuff to push out the opposite direct to get it moving.
What he said; the method isn't important, it's the mass flow in a direction opposite to the desired direction of travel, as demostrated in the space flight documentary "Wall-E".This is where things like ion engines come in handy, as your craft needs to carry plenty of stuff to push out the opposite direct to get it moving.
If I'm not mistaken, in a rocket engine, the force is mostly produced by the expanding gasses pushing against the inside of the bell-shaped nozzle, rather than simply being a case of spewing mass out one way and hence moving the other, (though that will have a small effect as well). The bell is shaped differently for different applications (i.e. the ambient pressure mentioned by MT), so the shape of a nozzle for a first stage engine is quite different to one designed to work in vacuum.
As others have said, the reason why rockets work is that the high pressure gas inside the engine wants equalise the pressure with the atmosphere outside, and if you can make this happen at high speed then combined with the mass of the gas flowing out you will create thrust regardless of the external pressure. When the first speed boat powered by a water jet was created, the designers (not engineers) thought that the jet needed to be underwater to 'push' against something. In reality all they did was slow down the speed of the water jet and create less thrust, when the jet was lifted clear of the water the boats actually went a lot faster as the jet was now exhausting into air which has a lower viscosity and density than water. As the speed of the water jet is higher and since thrust is a product of mass and speed of the jet, the boats could go faster.
The flow through a rocket nozzle is actually quite complex, the shape of the nozzle is very important. The first half of a rocket nozzle is a convergent section, again as most people know if you blow down a tube that gets narrower, like the lid from a Biro, then you will create a high speed jet of air, as the gas expands through the nozzle the pressure starts to drop and the flow accelerates. However in a rocket engine at some point this flow reaches Mach 1 and the flow now becomes 'choked' and a shockwave occurs and when high speed flow travels through a shockwave the speed of the flow drops. Now the behaviour of supersonic flows can be very strange, previously where subsonic flow would accelerate down a duct that gets progressively narrower a supersonic flow will actually decelerate and where a subsonic flow would slow down in a diverging duct, a supersonic flow now speeds up. So at the point in a rocket nozzle, where the flow reaches Mach 1, if you now expand the nozzle into a divergent duct the gas will continue to accelerate and the pressure of the gas leaving the nozzle should be the same as the ambient pressure for maximum performance. If the nozzle continues to expand and the pressure of the efflux drops below the ambient pressure then you have over-expansion and shock waves occur, efficiency drops etc.
As the design of the nozzle is largely based on the ambient pressure in which the rocket will operate, rockets traveling through the atmosphere often have to pass though a large variation in atmospheric pressure, from sea level to tens of miles before jettisoning a stage. Some of the Apollo launches show quite nicely the effect of operating a nozzle well away from it's design condition where the flow is massively under-expanded, the picture below shows the first stage at lift off and the pressure within the flow from the nozzles is close to the ambient pressure, while at altitude the pressure of the gas leaving the nozzles is the same at sea level, but the atmospheric pressure has dropped considerably and the exhaust plume continues to expand after leaving the nozzle.

There has been some studies into a nozzle that is self compensating for changes in atmospheric pressure called an 'aerospike' but this has been largely limited to a couple of large scale tests at NASA and some small academic rockets. Since there has been a sort of resurgence of interest in single stage to orbit rockets, an aerospike would probably fit the bill.
The flow through a rocket nozzle is actually quite complex, the shape of the nozzle is very important. The first half of a rocket nozzle is a convergent section, again as most people know if you blow down a tube that gets narrower, like the lid from a Biro, then you will create a high speed jet of air, as the gas expands through the nozzle the pressure starts to drop and the flow accelerates. However in a rocket engine at some point this flow reaches Mach 1 and the flow now becomes 'choked' and a shockwave occurs and when high speed flow travels through a shockwave the speed of the flow drops. Now the behaviour of supersonic flows can be very strange, previously where subsonic flow would accelerate down a duct that gets progressively narrower a supersonic flow will actually decelerate and where a subsonic flow would slow down in a diverging duct, a supersonic flow now speeds up. So at the point in a rocket nozzle, where the flow reaches Mach 1, if you now expand the nozzle into a divergent duct the gas will continue to accelerate and the pressure of the gas leaving the nozzle should be the same as the ambient pressure for maximum performance. If the nozzle continues to expand and the pressure of the efflux drops below the ambient pressure then you have over-expansion and shock waves occur, efficiency drops etc.
As the design of the nozzle is largely based on the ambient pressure in which the rocket will operate, rockets traveling through the atmosphere often have to pass though a large variation in atmospheric pressure, from sea level to tens of miles before jettisoning a stage. Some of the Apollo launches show quite nicely the effect of operating a nozzle well away from it's design condition where the flow is massively under-expanded, the picture below shows the first stage at lift off and the pressure within the flow from the nozzles is close to the ambient pressure, while at altitude the pressure of the gas leaving the nozzles is the same at sea level, but the atmospheric pressure has dropped considerably and the exhaust plume continues to expand after leaving the nozzle.

There has been some studies into a nozzle that is self compensating for changes in atmospheric pressure called an 'aerospike' but this has been largely limited to a couple of large scale tests at NASA and some small academic rockets. Since there has been a sort of resurgence of interest in single stage to orbit rockets, an aerospike would probably fit the bill.
Rocket science is easy, 3D vector calculus is not... Although when in company who may confuse engineering with washing machine repair I have been known to use the title rocket scientist 
Along with jet engines I've built a few rockets in my time, both fuselages and motors (solid and hybrid). This is my largest rocket, just over 6' tall and on a K size motor will nudge Mach 2.
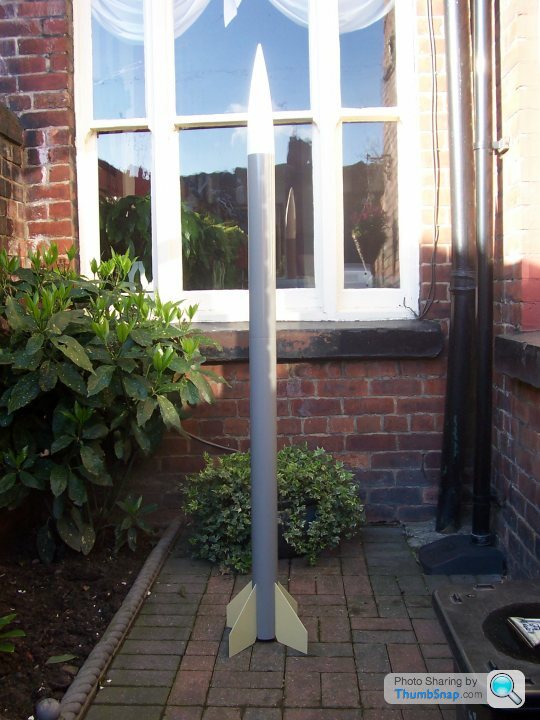
One of my smaller solid fuel test motors designed to operate on a mix of epoxy resin and potassium nitrate which needs a very high pressure for a stable burn and required some interesting testing during development.
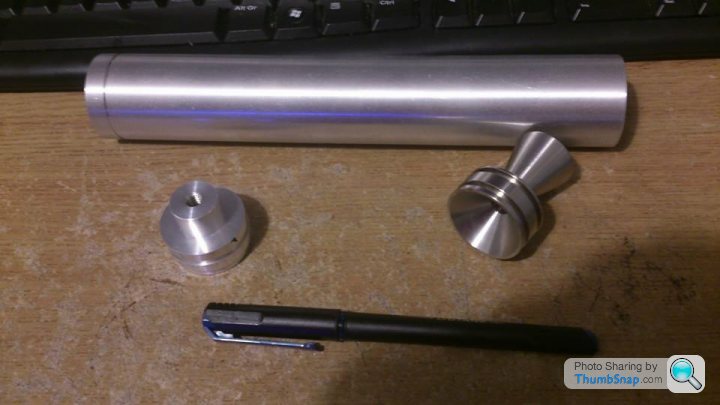

Along with jet engines I've built a few rockets in my time, both fuselages and motors (solid and hybrid). This is my largest rocket, just over 6' tall and on a K size motor will nudge Mach 2.
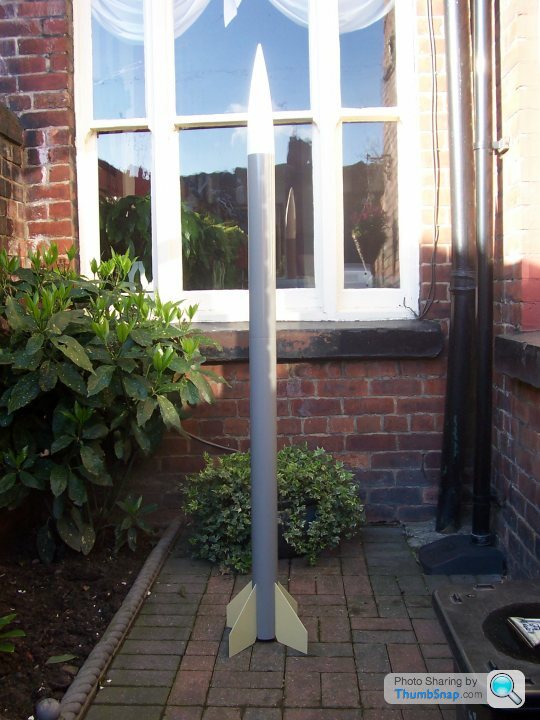
One of my smaller solid fuel test motors designed to operate on a mix of epoxy resin and potassium nitrate which needs a very high pressure for a stable burn and required some interesting testing during development.
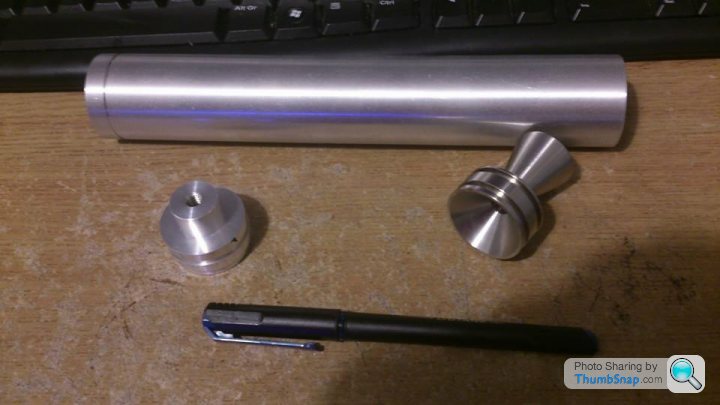
One of the other more prosaic determinants of nozzle size during design, particularly of solid motors, is overall rocket/missile diameter.
Often missile rocket motors have under expanded nozzles as the motor only burns for the first 2 or 3 seconds of flight and thereafter the missile coasts. A nozzle bigger than the missile's body diameter would be pure drag for the majority of the flight, so the thrust penalty of an under expanded nozzle during boost is offset by the aerodynamic gain during coast.
In space aerodynamic drag isn't an issue (though nozzle mass is) so you can have optimum expansion in your nozzle and so they appear to be much bigger than those you would see on an air-to-air missile.
Often missile rocket motors have under expanded nozzles as the motor only burns for the first 2 or 3 seconds of flight and thereafter the missile coasts. A nozzle bigger than the missile's body diameter would be pure drag for the majority of the flight, so the thrust penalty of an under expanded nozzle during boost is offset by the aerodynamic gain during coast.
In space aerodynamic drag isn't an issue (though nozzle mass is) so you can have optimum expansion in your nozzle and so they appear to be much bigger than those you would see on an air-to-air missile.
Gassing Station | Science! | Top of Page | What's New | My Stuff