Anyone ever used silver solder or similar...
Discussion
...to join mild steel? I've come up with a design for a garden gate I want to make but I want the joints to be pretty much square. it's a geometric lattice design out of 2-3mm by 40 mm mild steel bar and I was thinking of half cutting the bar to form a mechanical spliced joint then silver soldering (or similar) the joints to hopefully produce a really low profile joint. I'm not sure this would be achievable with welding.
I intend to get the gate powder coated when done so jointing material melting temp is a consideration and I only have access to mapp gas.
Does this sound possible or is the mapp has likely to struggle to heat the bar to the right temp for "soldering"
I intend to get the gate powder coated when done so jointing material melting temp is a consideration and I only have access to mapp gas.
Does this sound possible or is the mapp has likely to struggle to heat the bar to the right temp for "soldering"
I wouldn't t be able to get in to grind the welds back so would have to do every one with a file.
Roughly speaking the gate would be formed of a random square grid layout with the largest square being around 120mm and the smallest around 60mm.
This old type setters tray gives a rough idea of my design thoughts
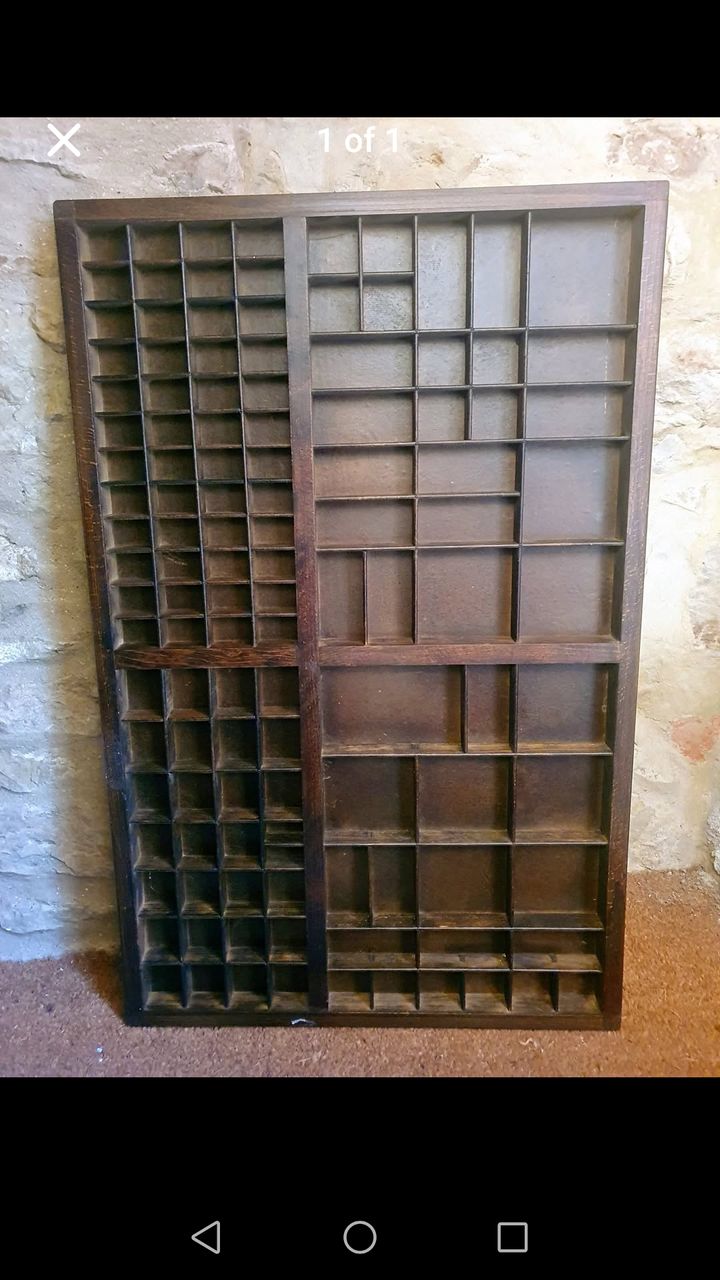
Roughly speaking the gate would be formed of a random square grid layout with the largest square being around 120mm and the smallest around 60mm.
This old type setters tray gives a rough idea of my design thoughts
allegro said:
I wouldn't t be able to get in to grind the welds back so would have to do every one with a file.
https://www.ebay.co.uk/itm/396360264011 will sort that way quicker than a hand file. (electric ones are available too)I'd suggest not getting overly-obsessive with perfect invisible joints, at the scale of a gate it won't be noticed as long as it looks consistent.
Using MAPP gas and solder I don’t think you’ll get the fine finish you’re looking for. But the real answer will be to have a go. The MAPP will heat a fairly large area which the silver solder will want to travel to. The beauty of TIG is a high heat in a very localised spot if needed. Autogenous means you won’t use filler rod. However, the fit and cleanliness will have to be excellent.
blueg33 said:
Isn’t this what brazing us for?
TBH. I would look for an adhesive.
I think the O/P is looking to powdercoat for a final finish. Not sure there’s any adhesive up to that task. BTW, brazing can be done with TIG,which some would say is infinitely more controllable than traditional gas brazing ( which is quite a skill set on its own). But as above, if the fit is good, there should be no need for filler material in this case.TBH. I would look for an adhesive.
normalbloke said:
blueg33 said:
Isn’t this what brazing us for?
TBH. I would look for an adhesive.
I think the O/P is looking to powdercoat for a final finish. Not sure there’s any adhesive up to that task. BTW, brazing can be done with TIG,which some would say is infinitely more controllable than traditional gas brazing ( which is quite a skill set on its own). But as above, if the fit is good, there should be no need for filler material in this case.TBH. I would look for an adhesive.
Need to know a bit more about the design, like is the whole thing going to be thin steel so all the joints are structural or is there going to be an outer frame doing most/all of the work with the inner joints mostly just for retention?
Spliced joints will mostly hold it together but it's stopping it lozenging where the strength will matter if there isn't a frame.
As for jointing the soldering/brazing/limited welding could all work depending what job the joint is trying to do. If it's just to hold the bits together without any real load then you could just tack it at the outer faces & not worry about a full joint.
If you're committed to the solder/braze option it's possible but you'll probably spend a lot of time heating it all up with MAPP. Dip brazing was what actually came to mind but that's not really a DIY option. Or induction brazing though that kit isn't cheap either.
Bear in mind that this is a garden gate so while aiming for visual perfection is great, in reality anything that isn't glaringly clunky will never be noticed once coated & fitted.
Spliced joints will mostly hold it together but it's stopping it lozenging where the strength will matter if there isn't a frame.
As for jointing the soldering/brazing/limited welding could all work depending what job the joint is trying to do. If it's just to hold the bits together without any real load then you could just tack it at the outer faces & not worry about a full joint.
If you're committed to the solder/braze option it's possible but you'll probably spend a lot of time heating it all up with MAPP. Dip brazing was what actually came to mind but that's not really a DIY option. Or induction brazing though that kit isn't cheap either.
Bear in mind that this is a garden gate so while aiming for visual perfection is great, in reality anything that isn't glaringly clunky will never be noticed once coated & fitted.
There will be an outer frame, probably 40mm x 20mm box section. I have a friend who can fab that but his skills are a little agricultural. I don't have any welding gear but have done a little brass brazing with MAPP on a bicycle frame. Given the amount of joints my worry is going through a good few bottles just getting enough heat in the joint. Tacking the intersections might work but my world is fine tools and CNC and blobby welds would really upset me 

Bigger torch, bigger bottle, propane instead of MAPP? Don't have to mess around with a little Rothenberger for something as chunky as a steel gate and you're not too worried if you end up heating it more generally if you're doing a lot of joints on the same assembly.
Or you could just use structural adhesive for it, pretty easy to make it tidy. 3M Scotch-Weld range has some that will survive the whole powdercoat process including pre-cleaning and oven stages. Bearing in mind that if you're bonding instead of soldering/brazing/welding you could shift to using aluminium which might make lots of the fabrication a bit easier?
Or you could just use structural adhesive for it, pretty easy to make it tidy. 3M Scotch-Weld range has some that will survive the whole powdercoat process including pre-cleaning and oven stages. Bearing in mind that if you're bonding instead of soldering/brazing/welding you could shift to using aluminium which might make lots of the fabrication a bit easier?
Silver solder & brazing - you'd need a big torch to get enough heat in for the filler metal to flow as the frame would be a pretty big heat sink. Personally I wouldn't be going down that path.
It it were me I'd tig weld it. Wouldn't be too hard to get a pretty decent weld finish that'll mostly disappear once powdercoated, probably with only a little bit of cleanup needed on the welds. Or if you wanted to go the whole hog, tig will give you the cleanest start point before you start grinding & filing.
Or you could just spot weld the ends and then grind flush so there's no weld on the inside seams. Assuming the majority of the bits are for aesthetics rather than structural.
It it were me I'd tig weld it. Wouldn't be too hard to get a pretty decent weld finish that'll mostly disappear once powdercoated, probably with only a little bit of cleanup needed on the welds. Or if you wanted to go the whole hog, tig will give you the cleanest start point before you start grinding & filing.
Or you could just spot weld the ends and then grind flush so there's no weld on the inside seams. Assuming the majority of the bits are for aesthetics rather than structural.
Edited by Arnold Cunningham on Tuesday 15th April 12:55
Gassing Station | Homes, Gardens and DIY | Top of Page | What's New | My Stuff