How to turn a ring?
Discussion
I'm trying to turn a ring from the end of this 25mm diameter brass rod. The plan was to go in from the end about 5mm, then in from the side until the ring separated.
However none of the cutting tools I've got will do it. This one is the closest but they're all too deep so the lower part fouls on the work. I've tried every angle I an think of to no avail. What's the secret?
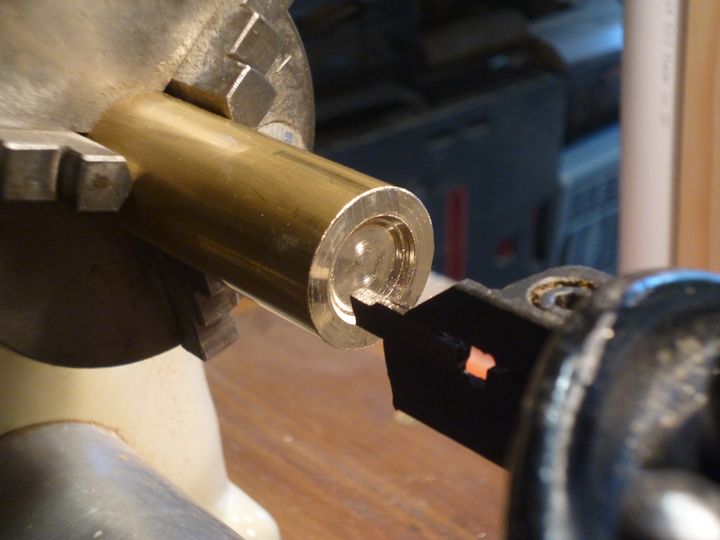
However none of the cutting tools I've got will do it. This one is the closest but they're all too deep so the lower part fouls on the work. I've tried every angle I an think of to no avail. What's the secret?
Simpo Two said:
I'm trying to turn a ring from the end of this 25mm diameter brass rod. The plan was to go in from the end about 5mm, then in from the side until the ring separated.
However none of the cutting tools I've got will do it. This one is the closest but they're all too deep so the lower part fouls on the work. I've tried every angle I an think of to no avail. What's the secret?
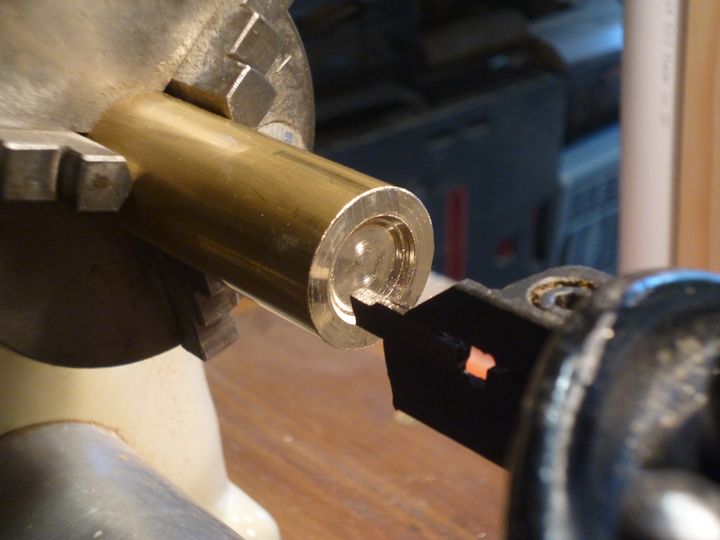
A drill, then a boring tool if the drill isn't big enough and the boring tool is small enough. Ideally, drill then ream. A parting tool won't work.However none of the cutting tools I've got will do it. This one is the closest but they're all too deep so the lower part fouls on the work. I've tried every angle I an think of to no avail. What's the secret?
Tickle said:
A drill, then a boring tool if the drill isn't big enough and the boring tool is small enough. Ideally, drill then ream.
The biggest drill I have is about 10mm...Super Sonic said:
The interestingly named 'boring bar'.
It's long and thin and has it's front clearance curved back.
Thanks, I'll have a look.It's long and thin and has it's front clearance curved back.
ecs said:
If your lathe has a tailstock then you could use a drill bit to bore the internal diameter, then cut the ring off with a parting tool..
It does, but I'd need to buy a 21mm drill for one job.If this was wood it would be easy, I could do it on a minute with a pointed scraper!
Edited by Simpo Two on Friday 1st November 11:26
OK, I just looked on Amazon for boring bars and I actually have some. I tried them earlier but they're no good as the cutter is set down too low and the underneath bit fouls the work.
Perhaps buy this one and then pack it up on the toolpost?
Like https://www.amazon.co.uk/SCLCR06-Turning-Holder-CC...
Perhaps buy this one and then pack it up on the toolpost?
Like https://www.amazon.co.uk/SCLCR06-Turning-Holder-CC...
Edited by Simpo Two on Friday 1st November 11:33
Update - I have a brass ring!
From this post I learned that the cutting tools with a round shank are for boring. What didn't make sens to me was that the height of the cutter was about 8mm lower than the other tools in the box, so the edge was well below the centre line and the chunk of tool under the cutter fouled the work. I found a spare piece of metal just the right height to get the cutter where I wanted it, and it just fitted in the preliminary hole I'd made.
The only oddity from there was that it refused to cut a parallel sided hole; the inner end was always slightly smaller. I presume that's because an ML8 is really a wood lathe so the bed isn't as rigid as on a dedicated metal lathe.
Anyway, I did the best I could, then used a file to put a curve on the front edge, followed by wet/dry down to 3000 grit. Then in with the parting tool from the front - it protested a remarkable amount even though I took it very slowly and added a bit of oil. And then - bingo! - the ring detached itself, bounced off the toolpost and straight down into the gap in the bed...
Now my chimney has the perfect base!
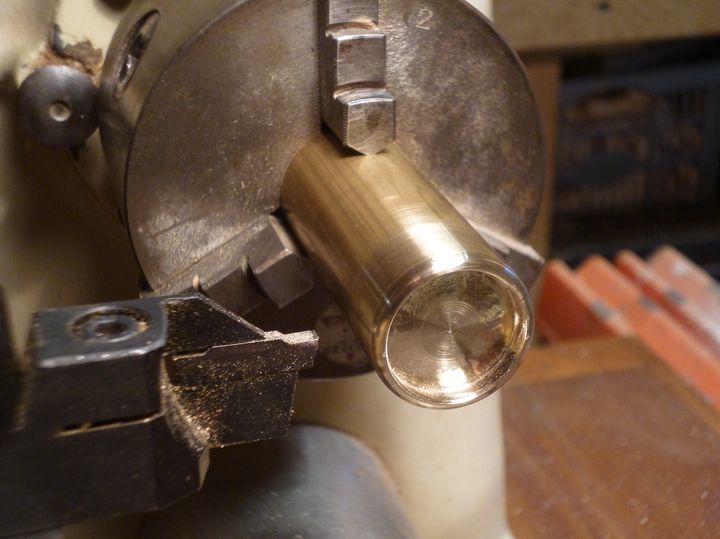
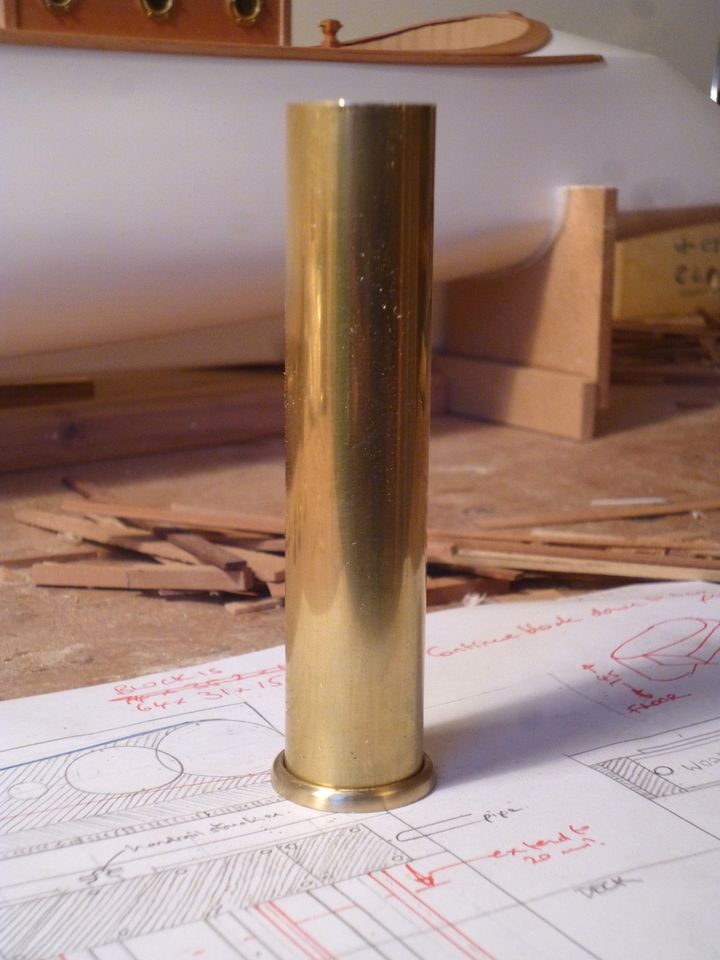
And after polishing, albeit out of focus...
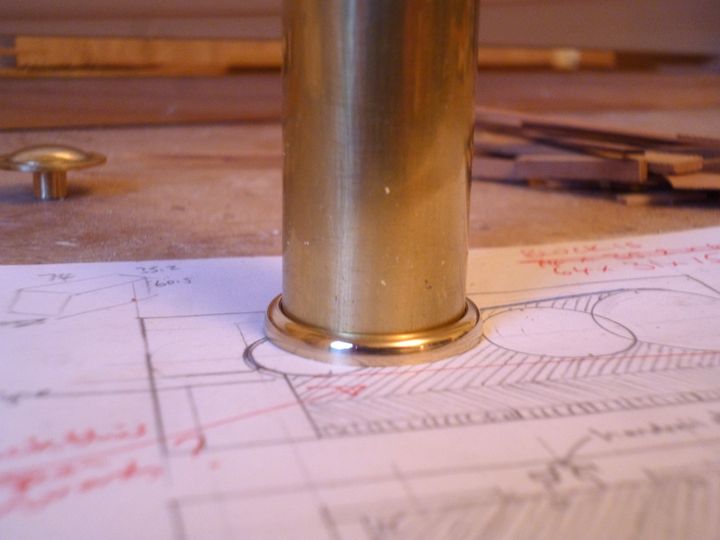
From this post I learned that the cutting tools with a round shank are for boring. What didn't make sens to me was that the height of the cutter was about 8mm lower than the other tools in the box, so the edge was well below the centre line and the chunk of tool under the cutter fouled the work. I found a spare piece of metal just the right height to get the cutter where I wanted it, and it just fitted in the preliminary hole I'd made.
The only oddity from there was that it refused to cut a parallel sided hole; the inner end was always slightly smaller. I presume that's because an ML8 is really a wood lathe so the bed isn't as rigid as on a dedicated metal lathe.
Anyway, I did the best I could, then used a file to put a curve on the front edge, followed by wet/dry down to 3000 grit. Then in with the parting tool from the front - it protested a remarkable amount even though I took it very slowly and added a bit of oil. And then - bingo! - the ring detached itself, bounced off the toolpost and straight down into the gap in the bed...
Now my chimney has the perfect base!
And after polishing, albeit out of focus...
Gassing Station | Homes, Gardens and DIY | Top of Page | What's New | My Stuff