Self-build 2 storey ICF extension and loft conversion
Discussion
As someone who doesn’t know when they’ve taken on something a little too much I am about halfway through extending my house and thought a build thread might be of interest.
I have done as much of the work as possible on this build and only used contractors where building regs stipulate it. I have done plenty of DIY in the past but I’m not in the trade.
Planning
I purchased a piece of software called Arcon Evo and set to drawing up the plans. It’s a really good bit of software and mostly intuitive to use. These are screenshots of the plans I submitted in Nov-19.
The plan is to go from this:
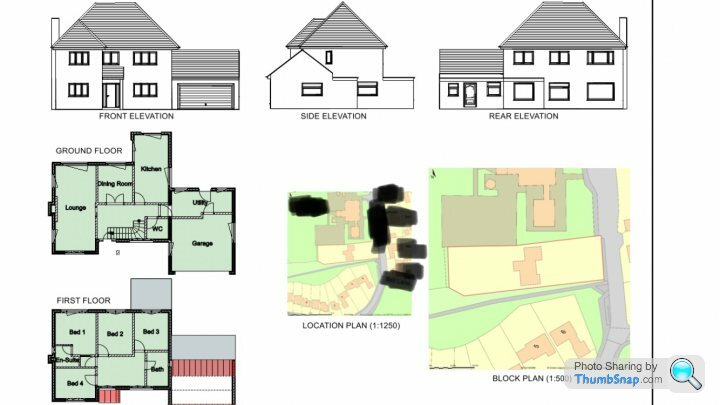
To this:
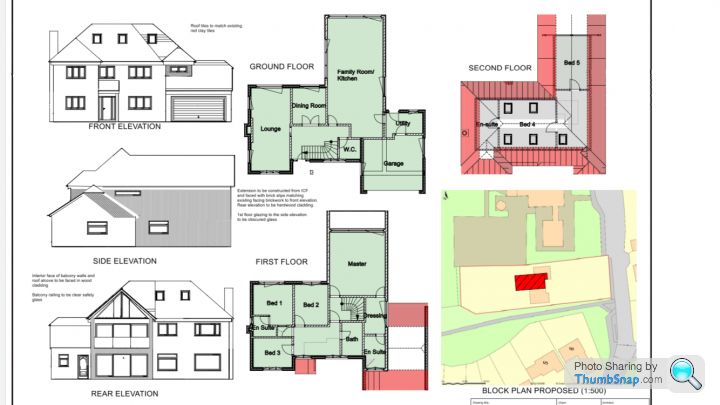
The plan was to start in March/April 2020.
But first we had to move the boiler, which we did in January. It was originally located in the corner of the utility room next to the kitchen. This would be in the middle of the new kitchen. Clearly January is an ideal time to be replacing your heating system...
I have done as much of the work as possible on this build and only used contractors where building regs stipulate it. I have done plenty of DIY in the past but I’m not in the trade.
Planning
I purchased a piece of software called Arcon Evo and set to drawing up the plans. It’s a really good bit of software and mostly intuitive to use. These are screenshots of the plans I submitted in Nov-19.
The plan is to go from this:
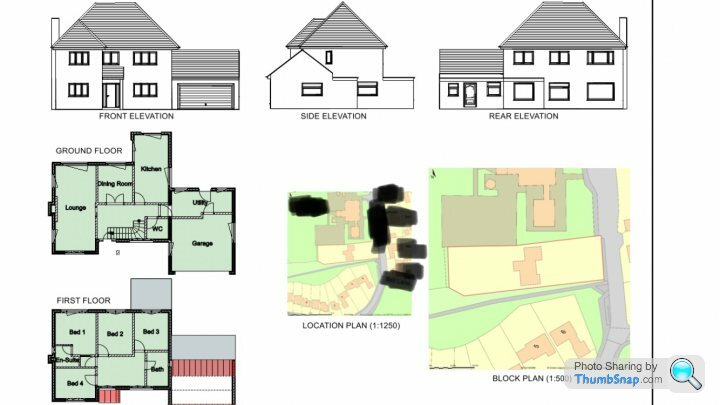
To this:
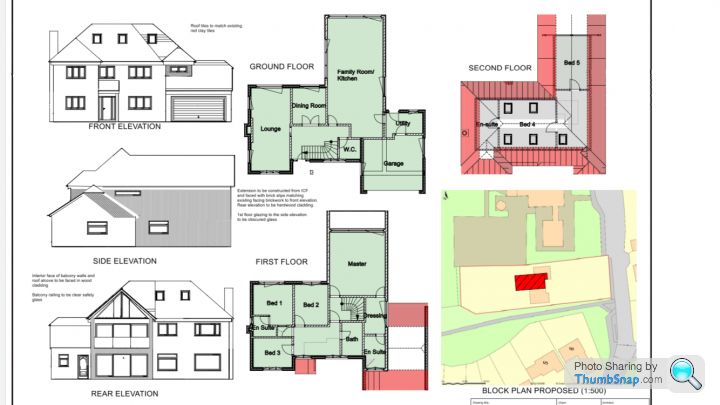
The plan was to start in March/April 2020.
But first we had to move the boiler, which we did in January. It was originally located in the corner of the utility room next to the kitchen. This would be in the middle of the new kitchen. Clearly January is an ideal time to be replacing your heating system...
We’re on oil here so limited in choices of replacements . The old system was a traditional gravity fed one with the tank in the corner of the bedroom above the kitchen. This has to go as well.
I opted for a Grant utility boiler and a pressurised system co located with a 300L tank.
I ran all the new pipe work to the new location and replaced all the old rads (those that wouldn’t be rendered obsolete in the new extension at least).
Then the plumber come and did his magic in connecting it all together...
Old stuff before weigh in, managed to get £100 back for that little lot!
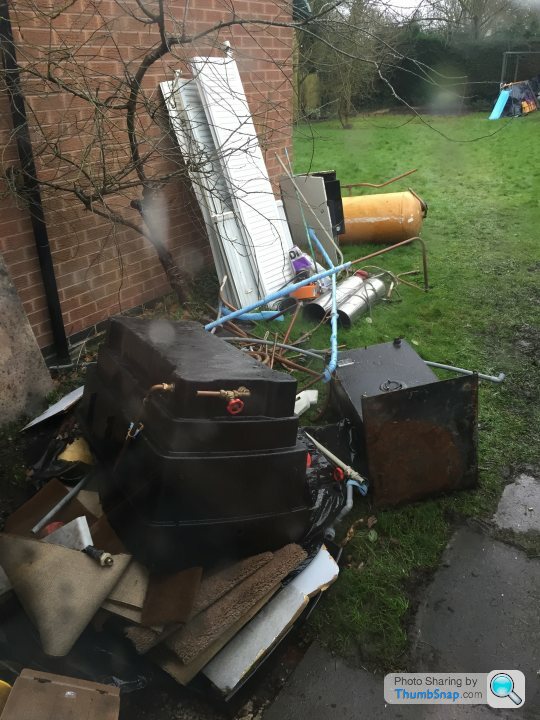
Old Boiler location:
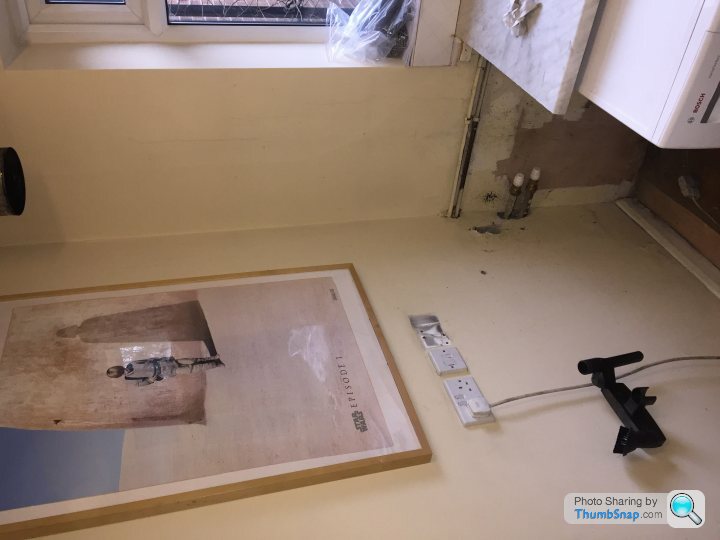
New boiler and tank part way through install:
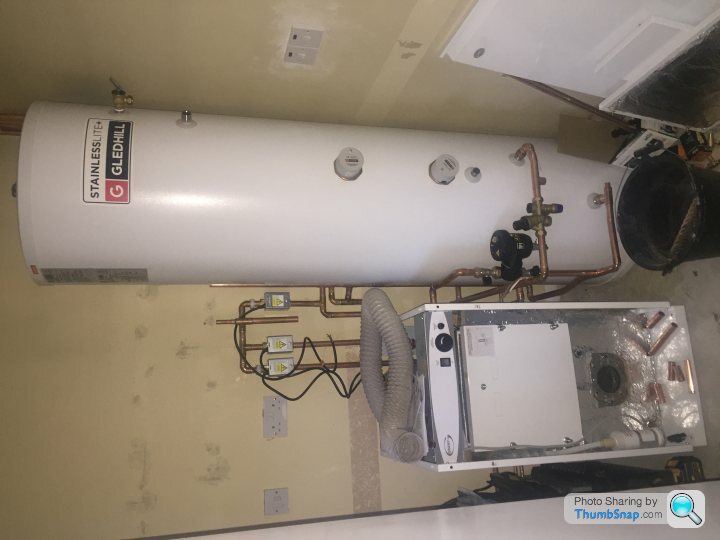
And finished:
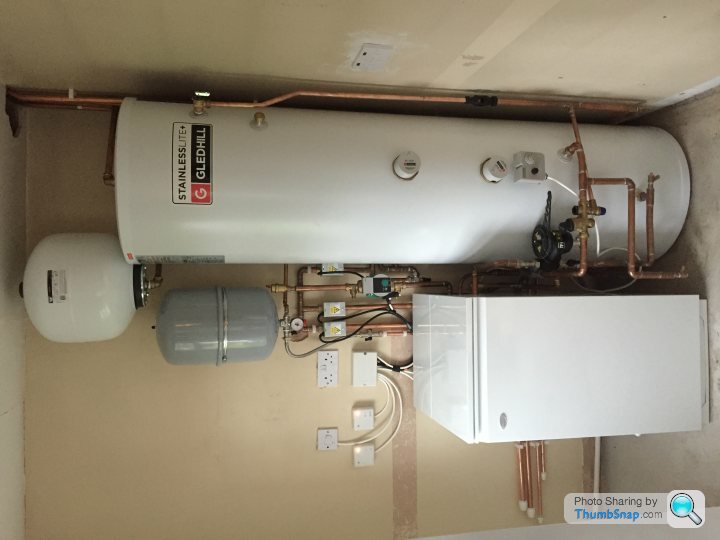
Nothing standing in the way of starting now, let’s get going...
I opted for a Grant utility boiler and a pressurised system co located with a 300L tank.
I ran all the new pipe work to the new location and replaced all the old rads (those that wouldn’t be rendered obsolete in the new extension at least).
Then the plumber come and did his magic in connecting it all together...
Old stuff before weigh in, managed to get £100 back for that little lot!
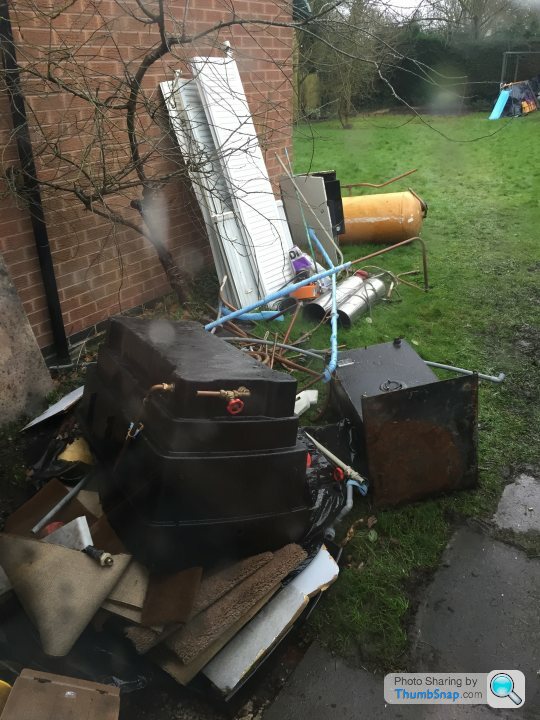
Old Boiler location:
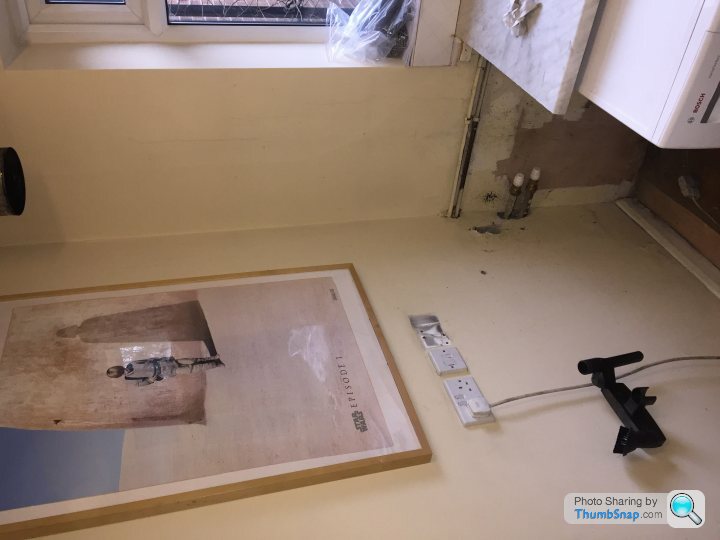
New boiler and tank part way through install:
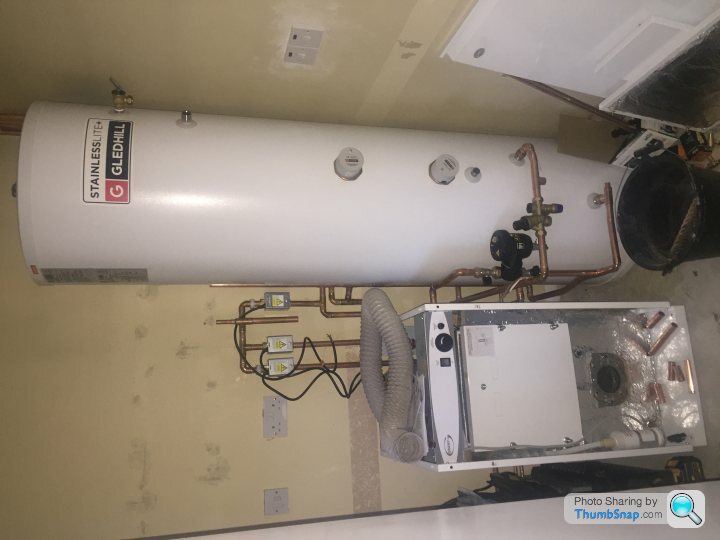
And finished:
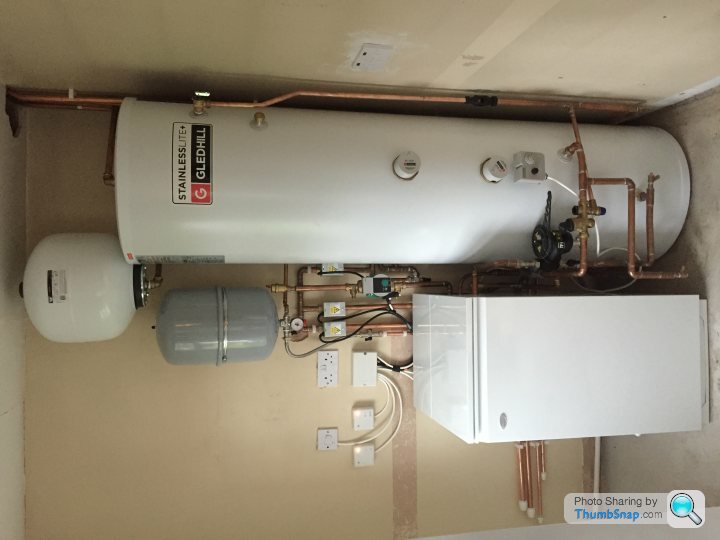
Nothing standing in the way of starting now, let’s get going...
First thing was find somewhere for all the stuff in the garage. Our initial idea was to get a shipping container for the front garden. After considering how we’d feel looking out the front at a container all day we hit upon the idea of getting a summer house for the back garden instead.
So in February I got on with building this:
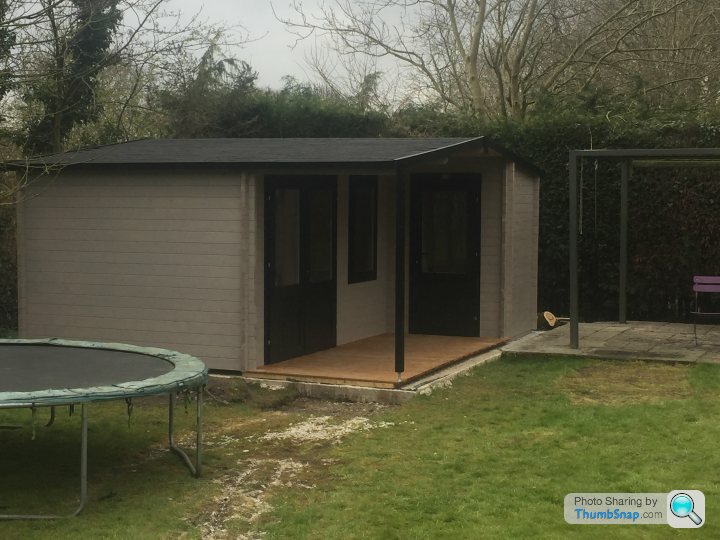
And then we stuffed it to the rafters with crap.
Now for the main house...
So in February I got on with building this:
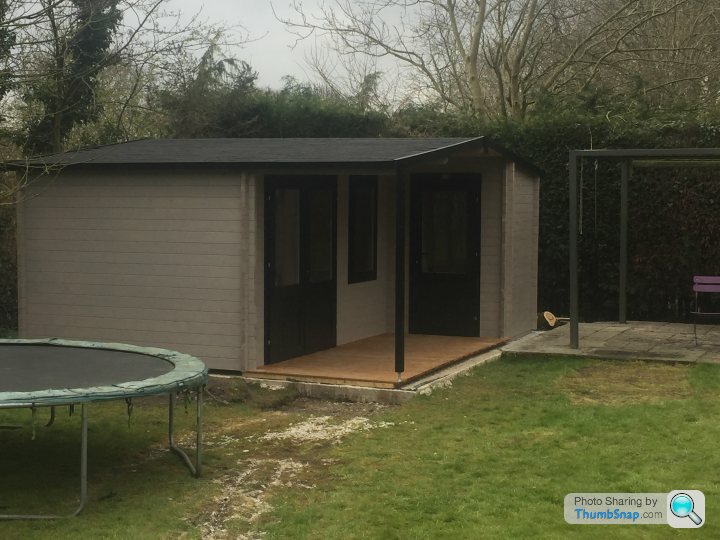
And then we stuffed it to the rafters with crap.
Now for the main house...
Now into March and getting things sorted to start the main works annnnd COVID, damn!
Not to waste the time at home and the Easter holidays I needed something to do that wasn’t breaking ground (couldn’t get a mini digger as everywhere was shut).
Fortunately I had already stockpiled a substantial amount of 225x47 T26 timber off a friend as a result of a bodged order on his extension so decided to tackle the garage roof. This raised the apex and got rid of the flat roof at the back.
Before shot
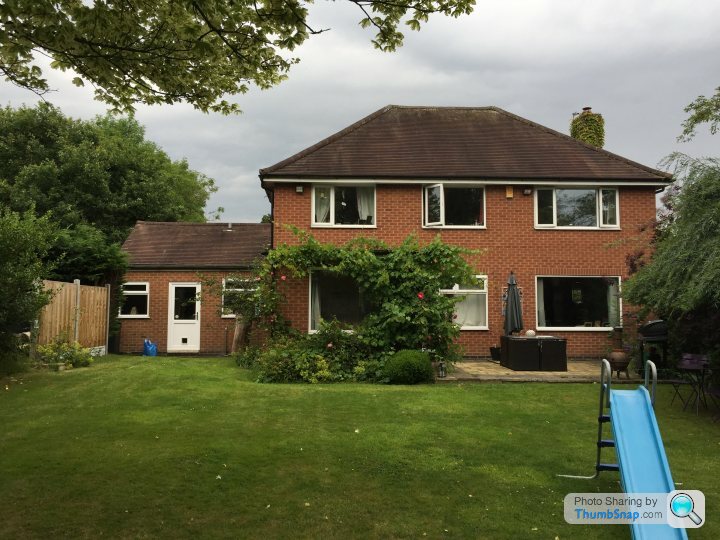
Old tiles off and new rafters up
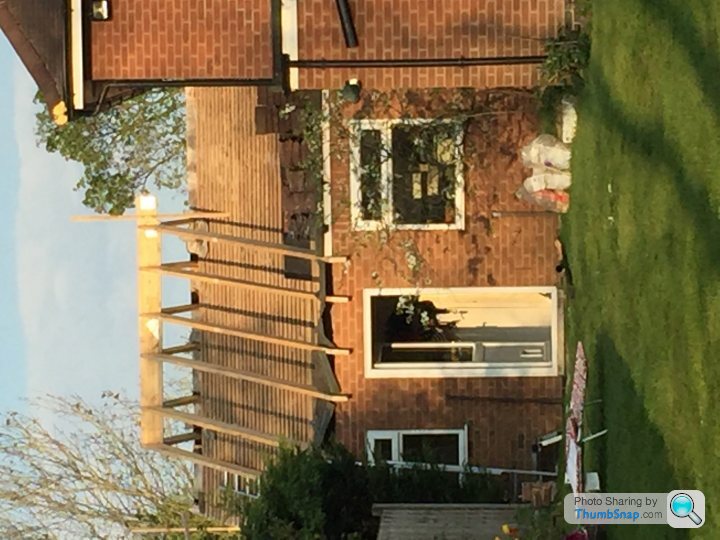
Felted and battened
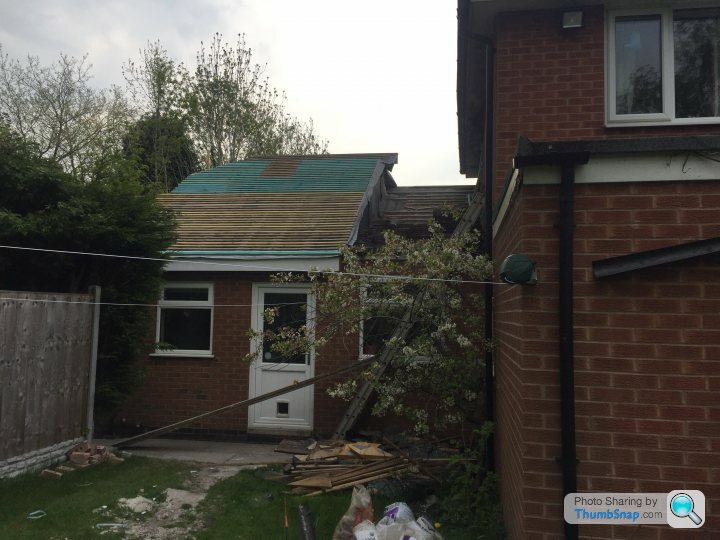
Tiled
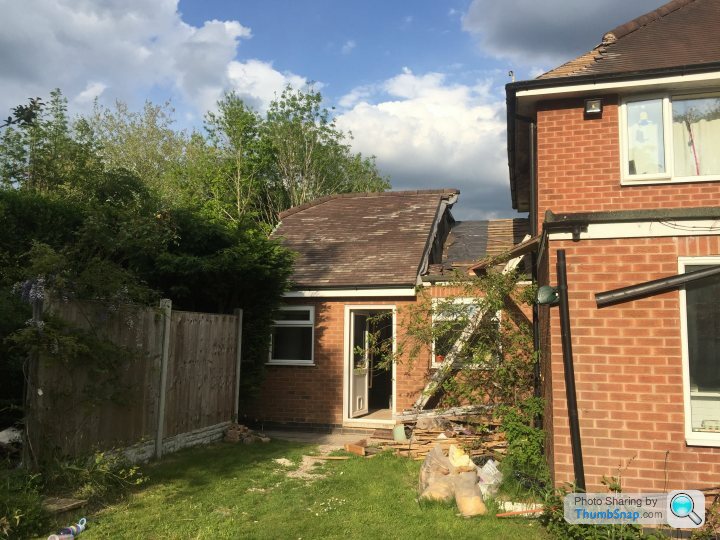
Still in lockdown so what to do next...
Not to waste the time at home and the Easter holidays I needed something to do that wasn’t breaking ground (couldn’t get a mini digger as everywhere was shut).
Fortunately I had already stockpiled a substantial amount of 225x47 T26 timber off a friend as a result of a bodged order on his extension so decided to tackle the garage roof. This raised the apex and got rid of the flat roof at the back.
Before shot
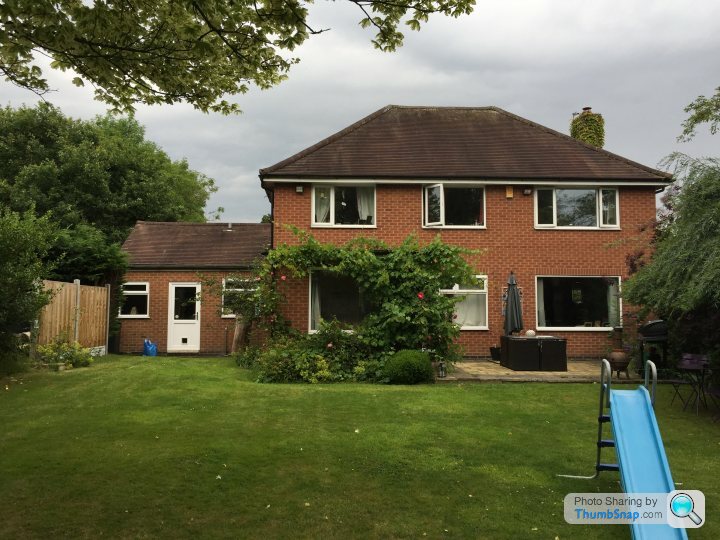
Old tiles off and new rafters up
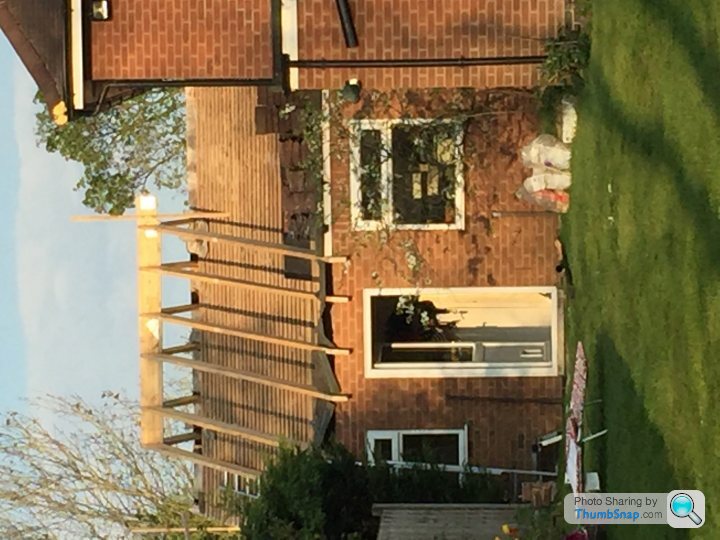
Felted and battened
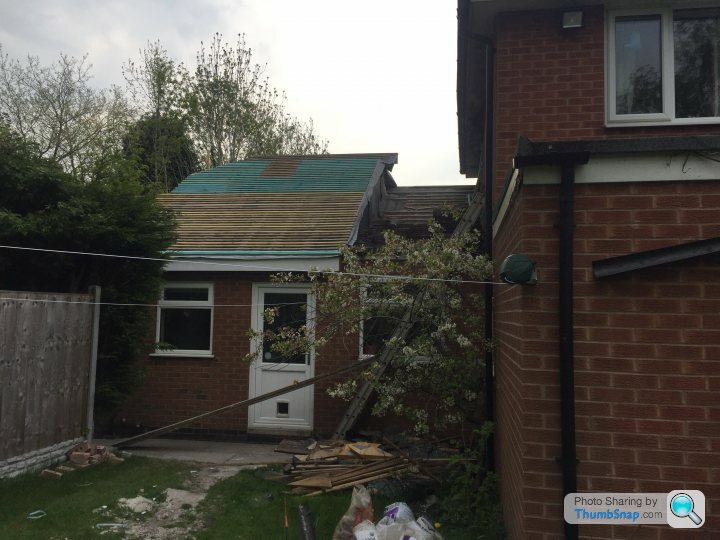
Tiled
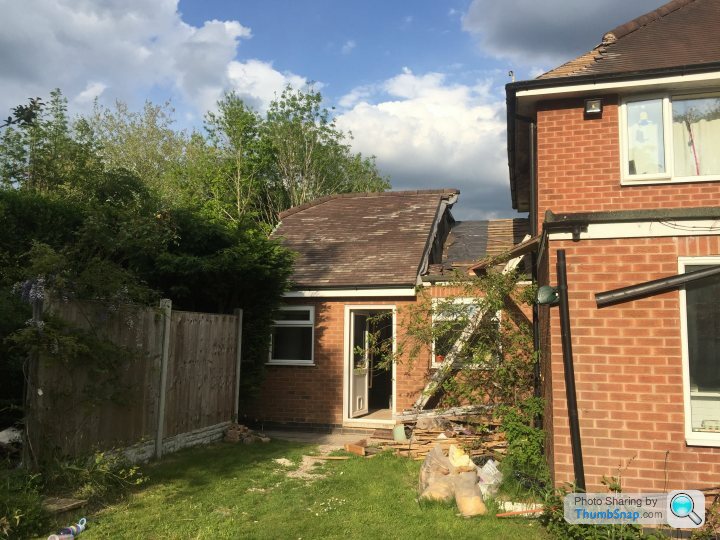
Still in lockdown so what to do next...
Knock down the old kitchen “extension” - it’s not an extension but part of the original house but it looks like an extension.
Got the crowbars and hammers out and got to work:
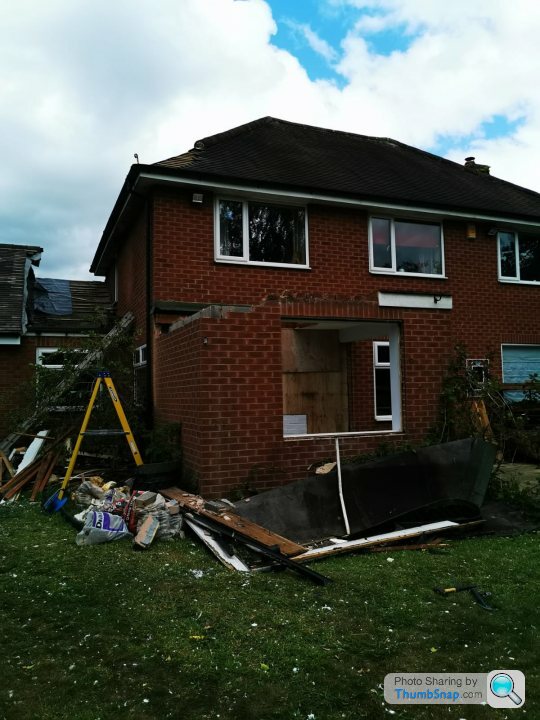
Found this monster of an abandoned wasps nest in the old roof. This is just half of it...
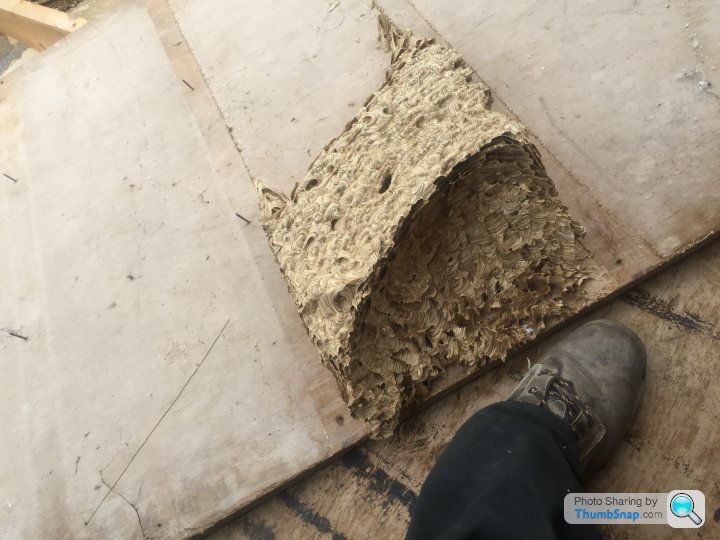
Kitchen reduced to rubble
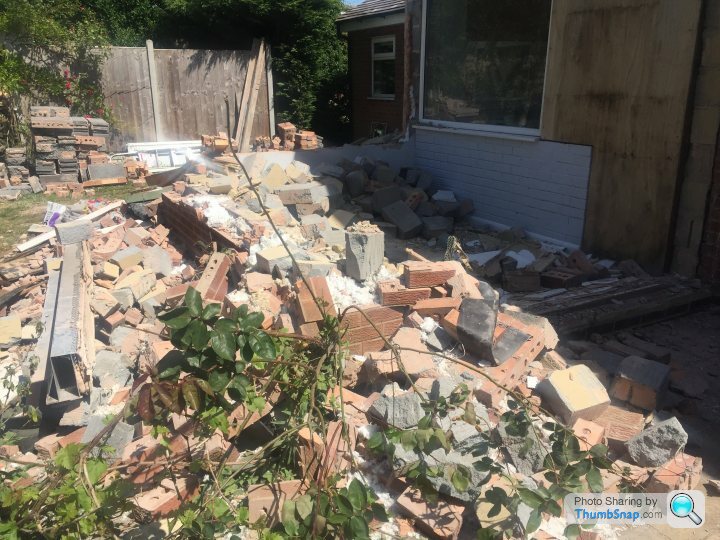
Next job was to break up the slab and see how deep the brickwork goes on the foundations...
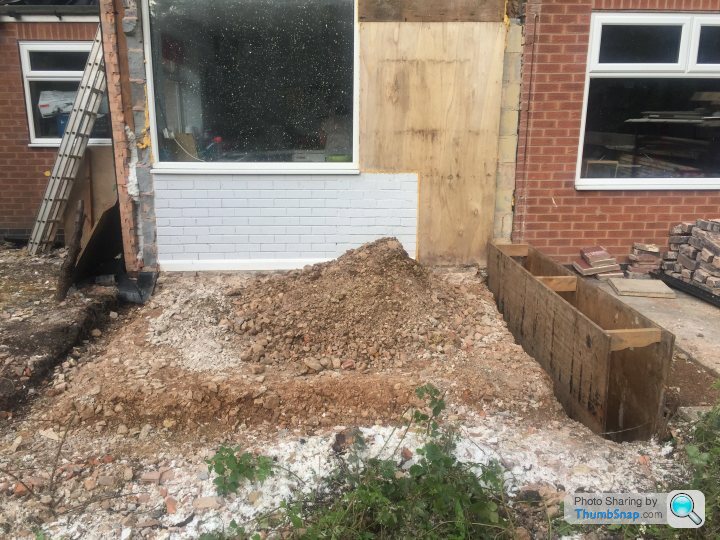
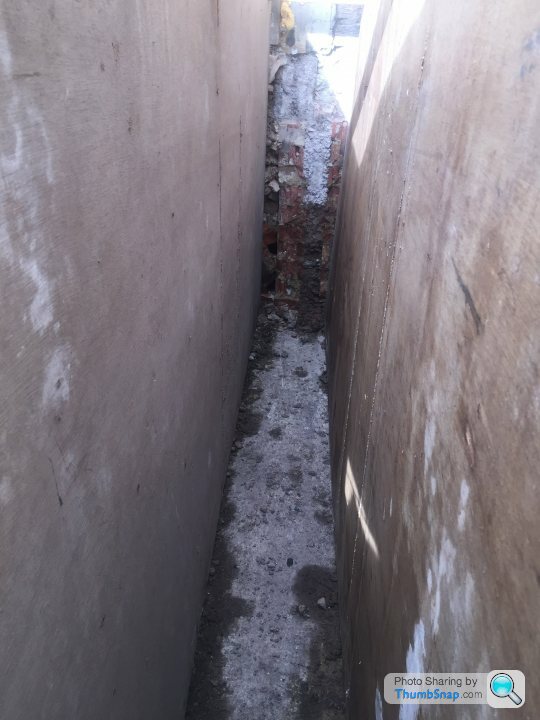
13 courses below DPC! Then an 8 inch trench fill of concrete below that. Fortunately the building inspector was happy for me to leave the old concrete in place and fill on top.
Got the crowbars and hammers out and got to work:
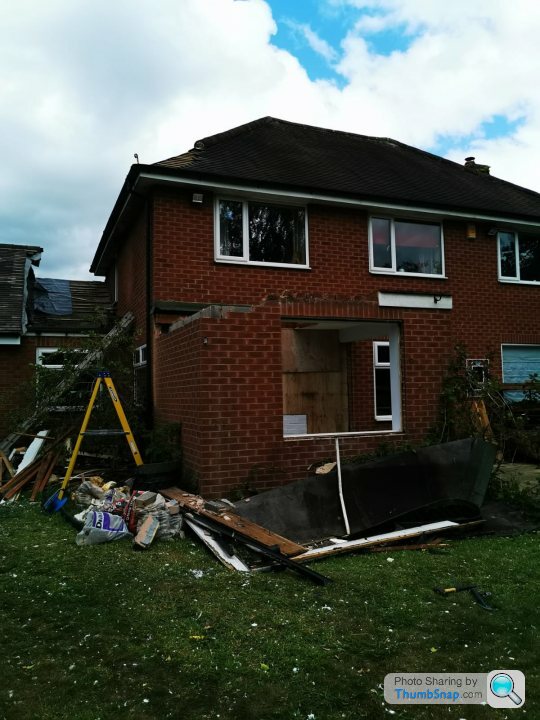
Found this monster of an abandoned wasps nest in the old roof. This is just half of it...
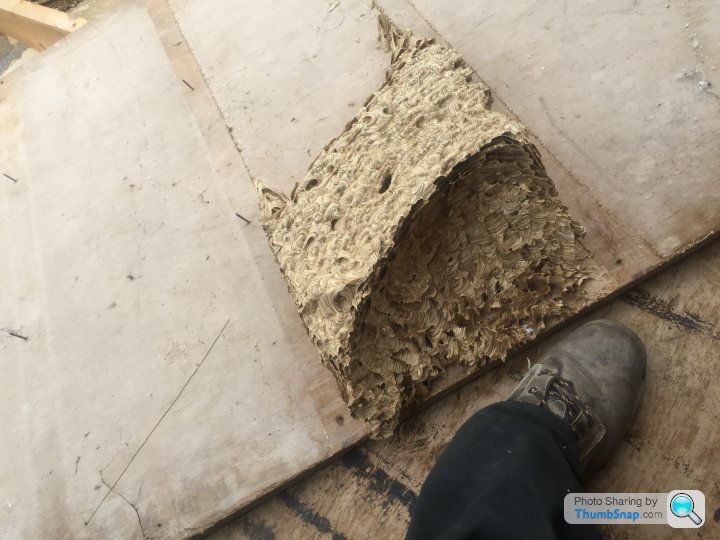
Kitchen reduced to rubble
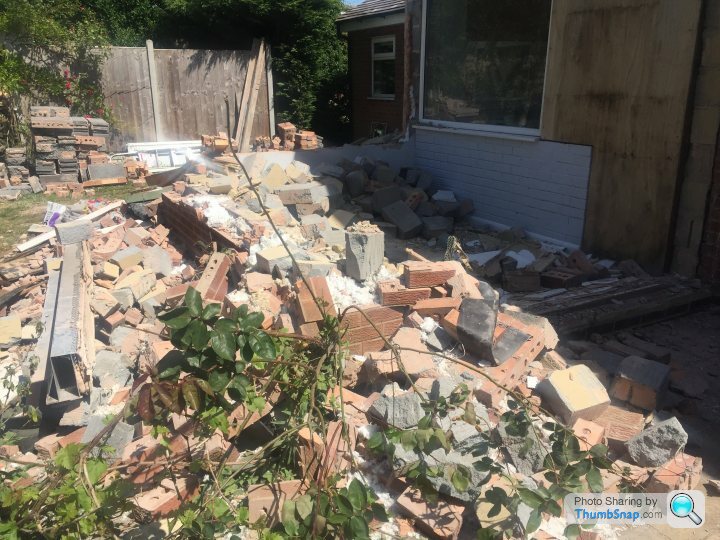
Next job was to break up the slab and see how deep the brickwork goes on the foundations...
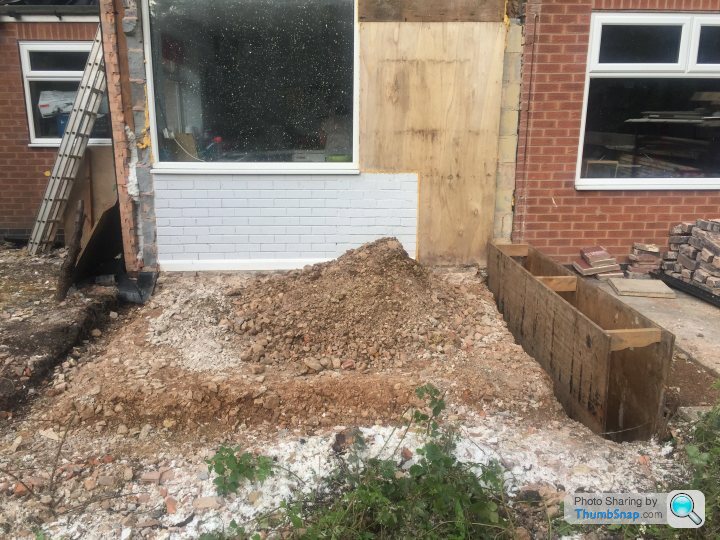
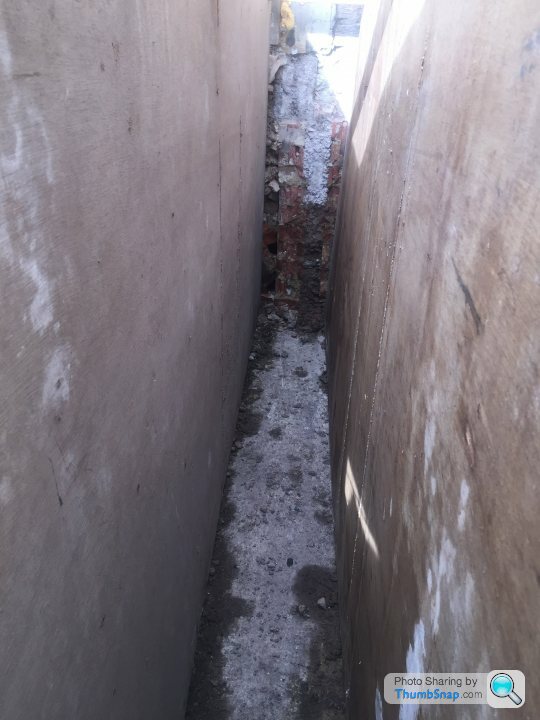
13 courses below DPC! Then an 8 inch trench fill of concrete below that. Fortunately the building inspector was happy for me to leave the old concrete in place and fill on top.
During the kitchen demolition the lockdown eased and things started to move again. The IVF wall bits turned up (ordered before COVID was a thing):
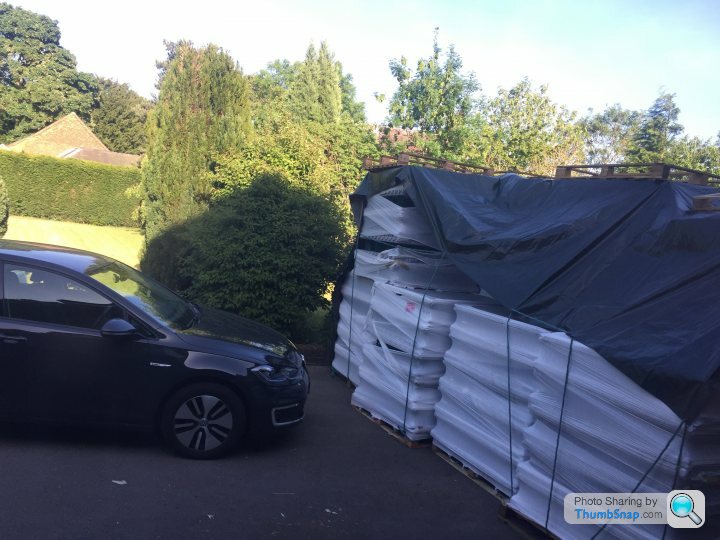
It would be under that tarp for a little while!
I eventually got my hands on a digger in early July and groundwork’s commenced in anger:
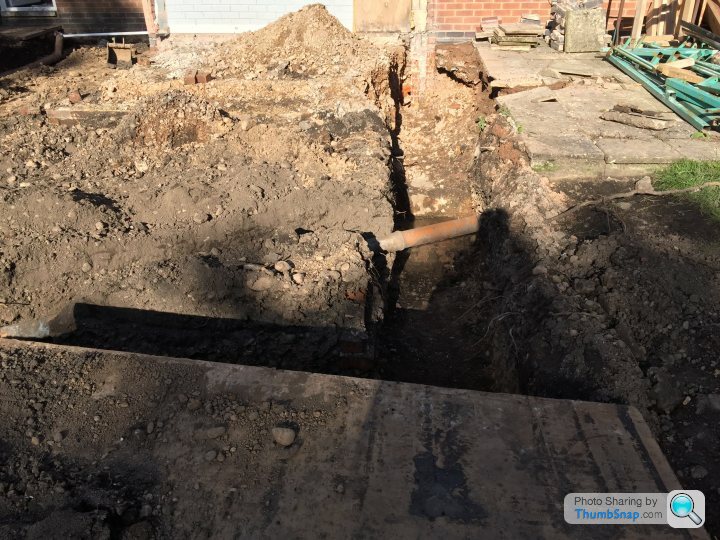
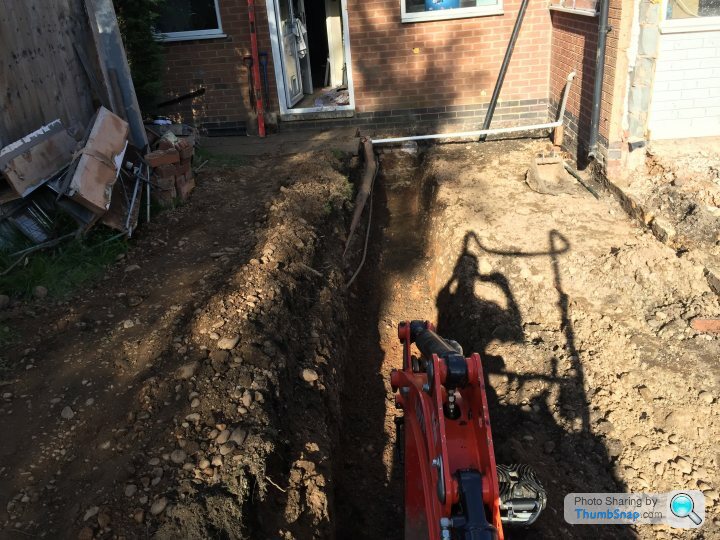
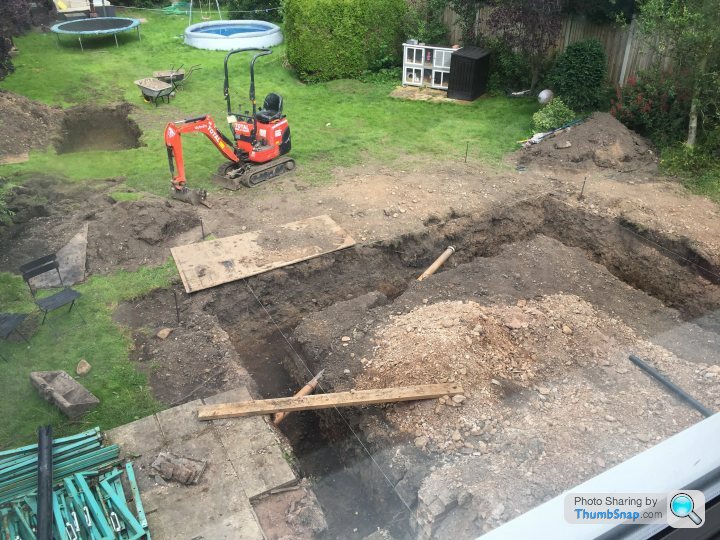
The soil pipe passing through it is the soil waste from our old en-suite. I knew it was there and that I’d have to go over it but as it drains to my own septic tank I don’t need to worry about water company permissions. It was also fortunate we did build across it as we found that it had been poorly laid originally and had a dip just before it passed into the top trench and a blockage was forming. A quick cut out, insert new pipe and reset of the fall should hopefully mean no future problems.
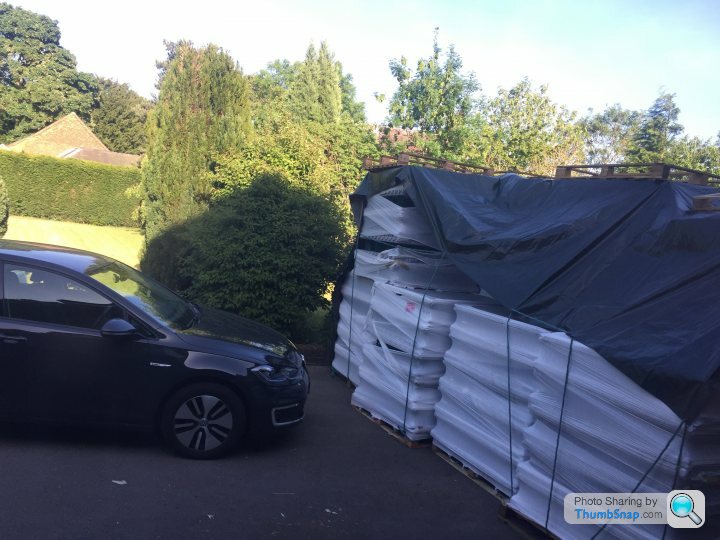
It would be under that tarp for a little while!
I eventually got my hands on a digger in early July and groundwork’s commenced in anger:
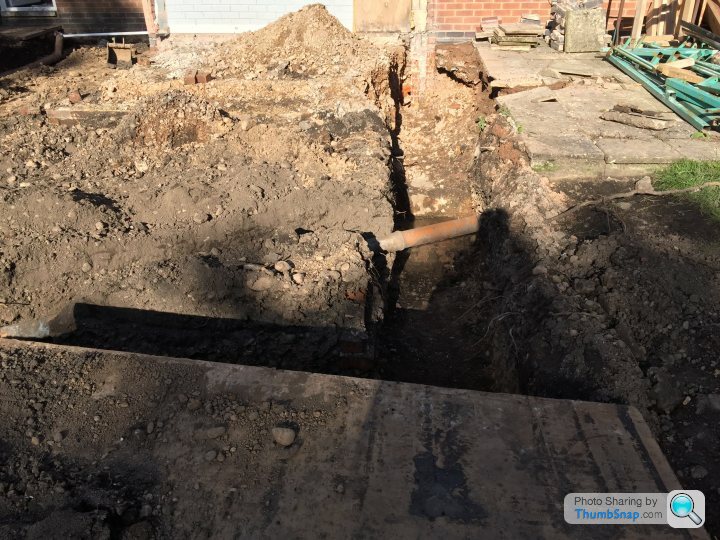
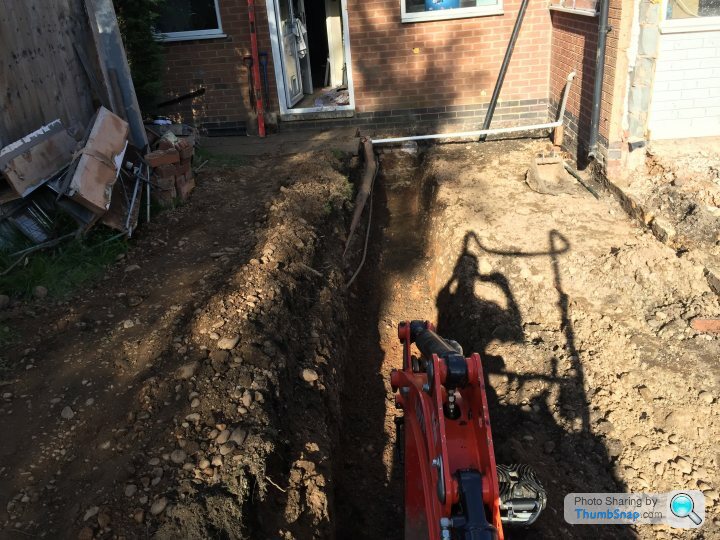
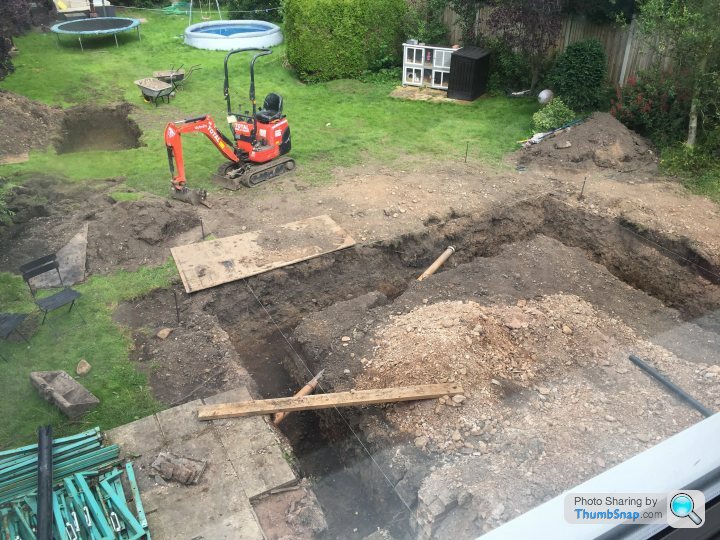
The soil pipe passing through it is the soil waste from our old en-suite. I knew it was there and that I’d have to go over it but as it drains to my own septic tank I don’t need to worry about water company permissions. It was also fortunate we did build across it as we found that it had been poorly laid originally and had a dip just before it passed into the top trench and a blockage was forming. A quick cut out, insert new pipe and reset of the fall should hopefully mean no future problems.
paulrockliffe said:
Awesome!
I've been DIYing a loft conversion for two years now, so my main thoughts are; has he realised how much he's bitten off yet?
I got to that stage doing the main roof - thinking Jesus this is massive what am I doing. I’ve started now though so no where else to go but forward! This was plain sailing up to here by comparison.I've been DIYing a loft conversion for two years now, so my main thoughts are; has he realised how much he's bitten off yet?
Time for some concrete.
My original plan was to chute it through the garage from the chute on the truck and then a couple of homemade troughs into the footings but once the concrete truck turned up we soon realised this wouldn’t work. Fortunately we managed to find a concrete boom pump on its way back from another job and they saved my bacon. And to be fair a hell of a lot of time and effort. I’ve used the same pump guys for all the concrete pumping since then so they’ve had their reward for helping me out of a tight spot.
Up and over we go
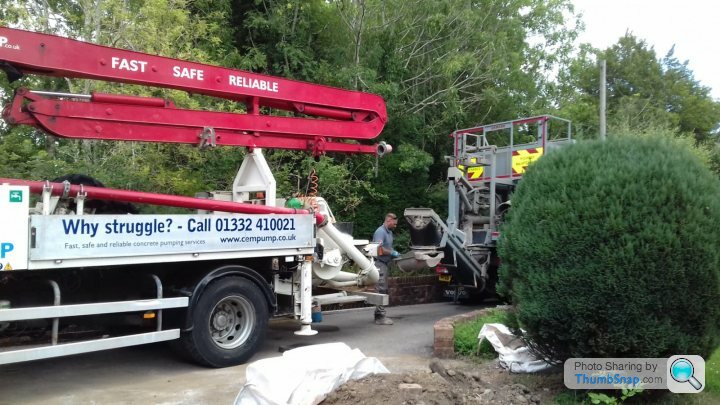
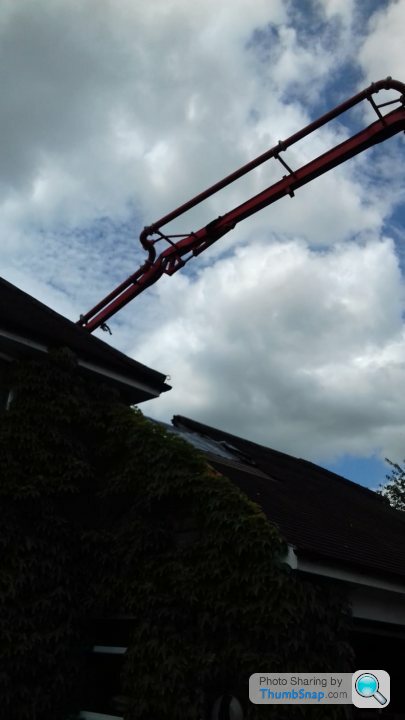
All poured and rods in to take the below ground courses of ICF.
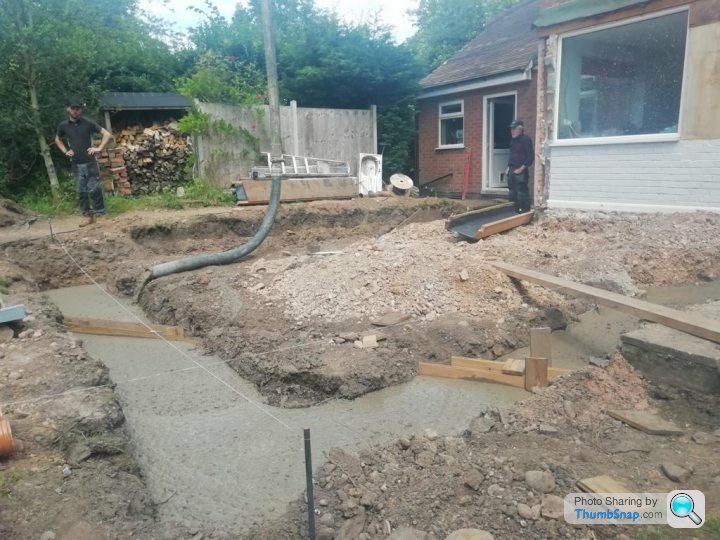
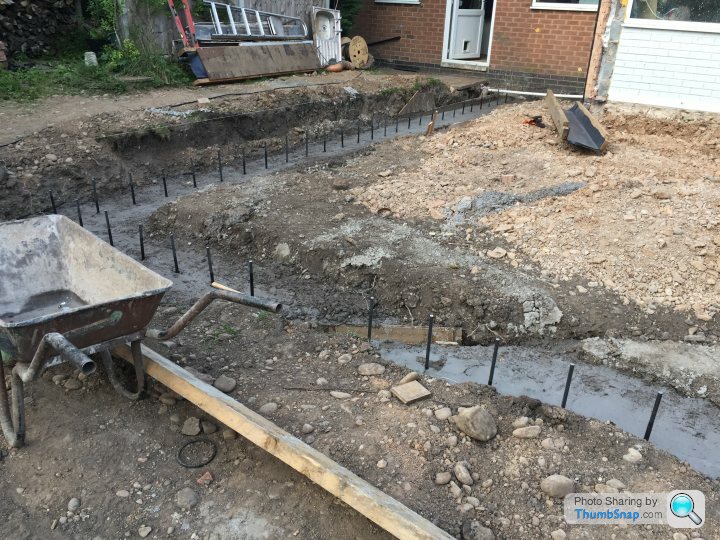
My original plan was to chute it through the garage from the chute on the truck and then a couple of homemade troughs into the footings but once the concrete truck turned up we soon realised this wouldn’t work. Fortunately we managed to find a concrete boom pump on its way back from another job and they saved my bacon. And to be fair a hell of a lot of time and effort. I’ve used the same pump guys for all the concrete pumping since then so they’ve had their reward for helping me out of a tight spot.
Up and over we go
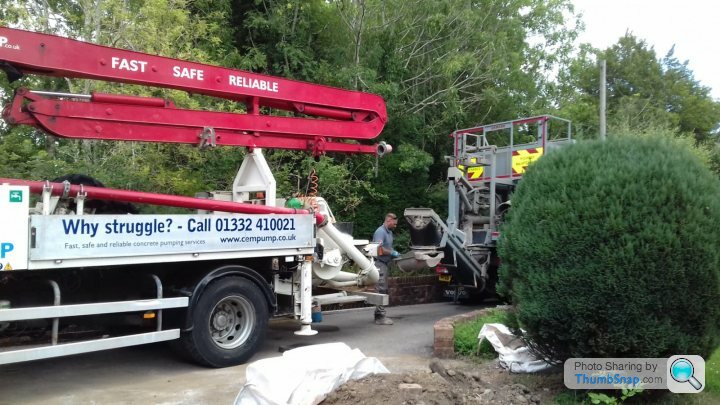
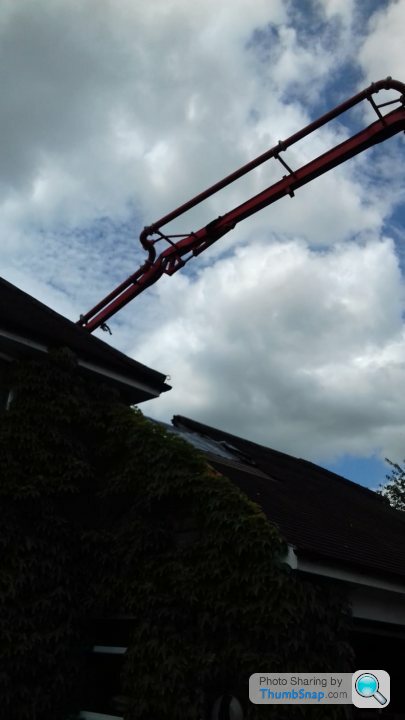
All poured and rods in to take the below ground courses of ICF.
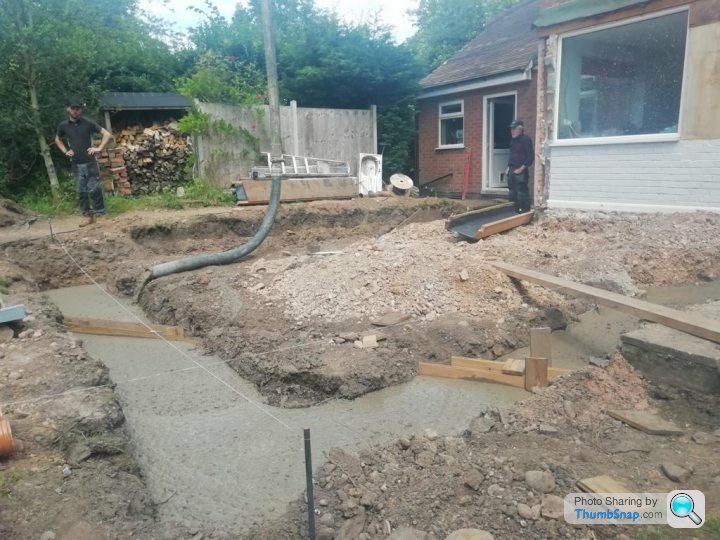
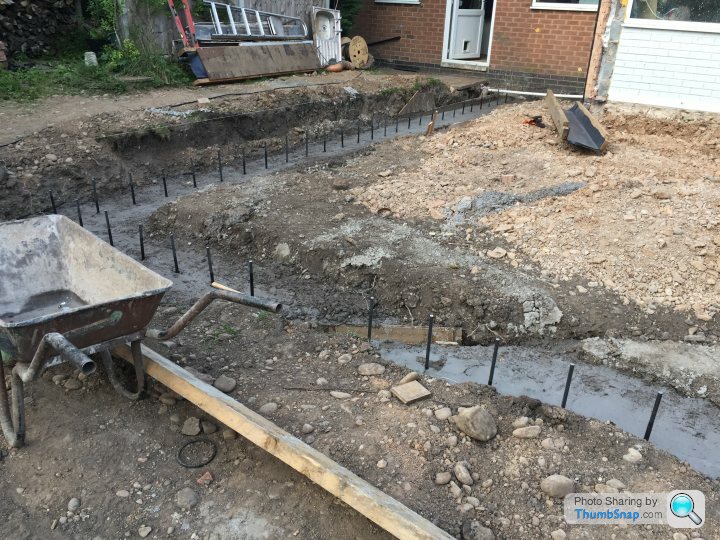
The ground floor walls took me two days to put up. It then took a further two weeks to tie in all the structural elements.
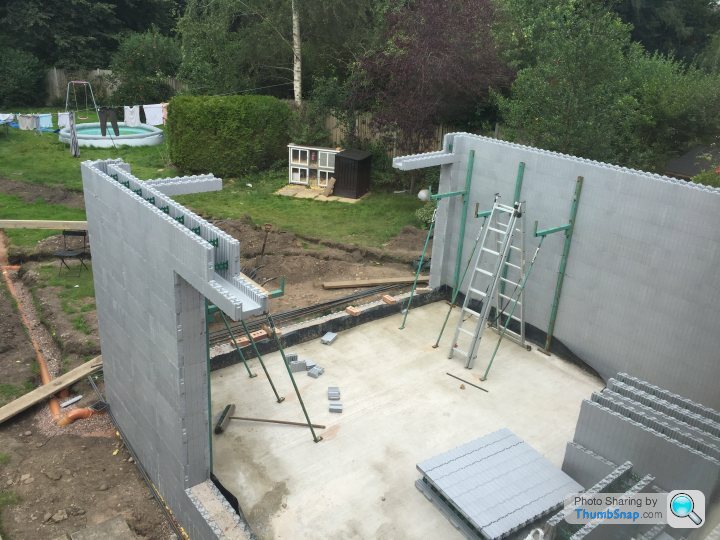
Then had to get these little steels into the garage to support the first floor. They need to go in now so that the end of the longest beam is cast into the concrete we’ll pour for the ground floor.
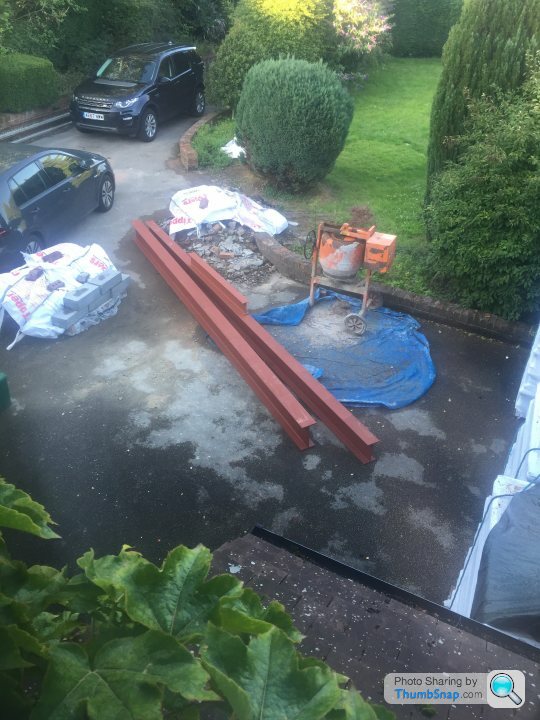
5 mates and 2 genies made short work of it and we had them in place in a little under two hours.
Pics are a few weeks on with first couple of courses of blocks concreted on top
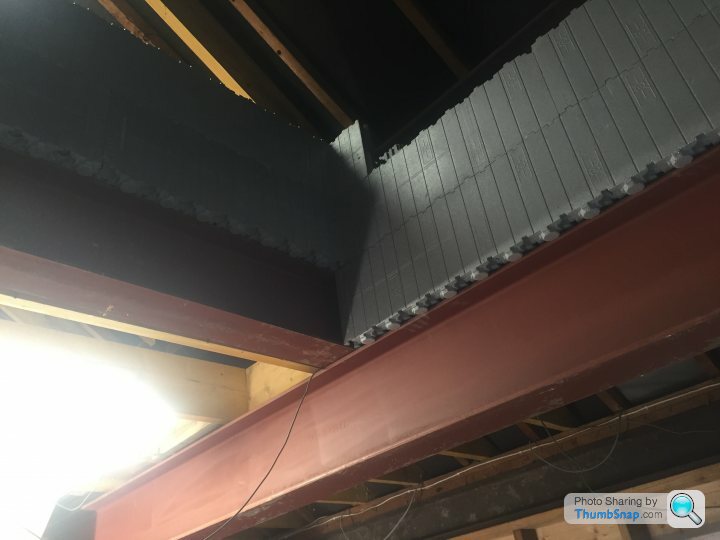
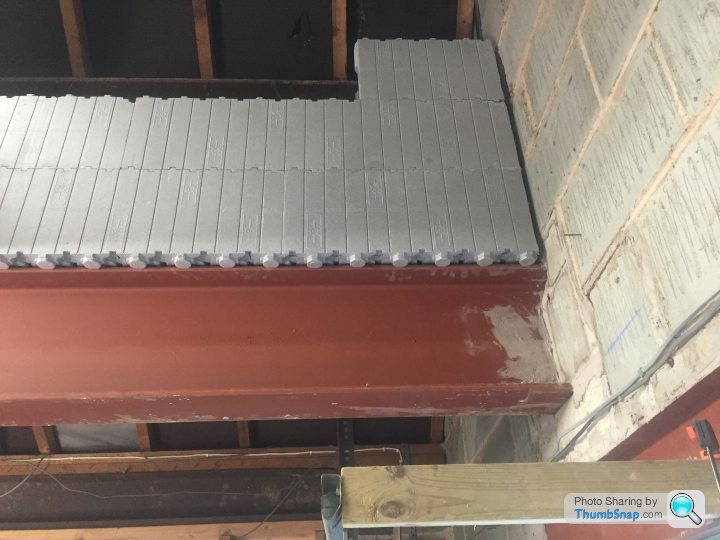
These were the only steels I needed on the project as all the other openings I cast the beams in concrete around rebar designed by a SE.
Something like this
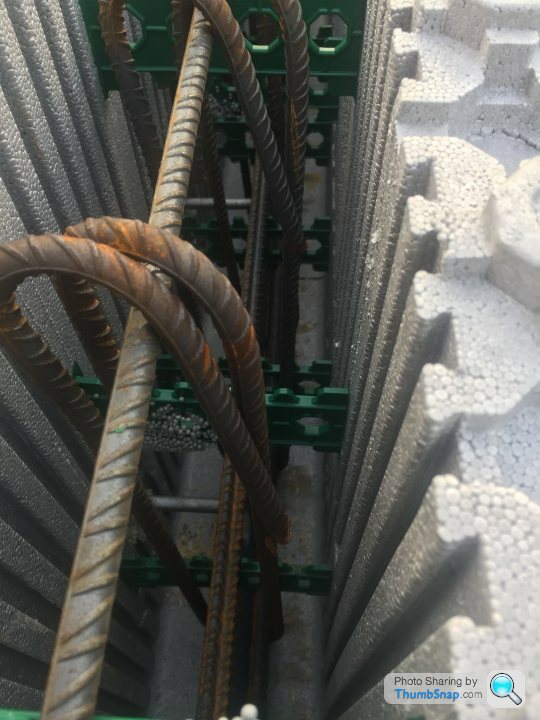
I then had the balcony to construct. This is an insulated base supported by concrete reinforced beams at 750mm centres with a rebar grid on top. This took a little while to finish
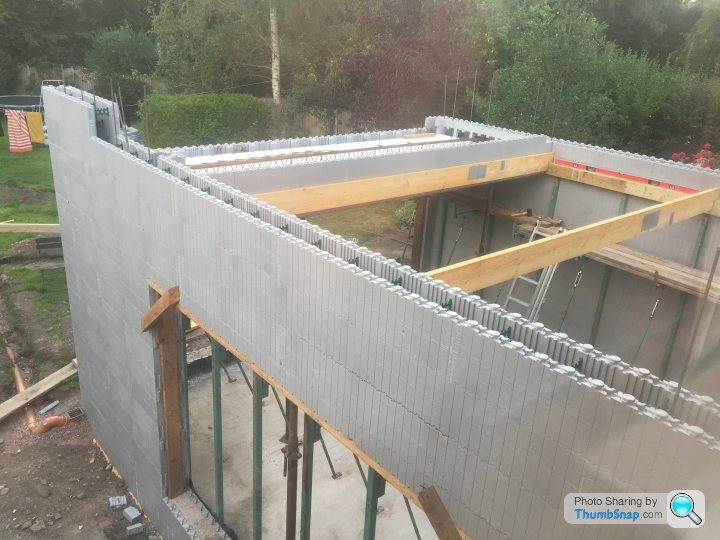
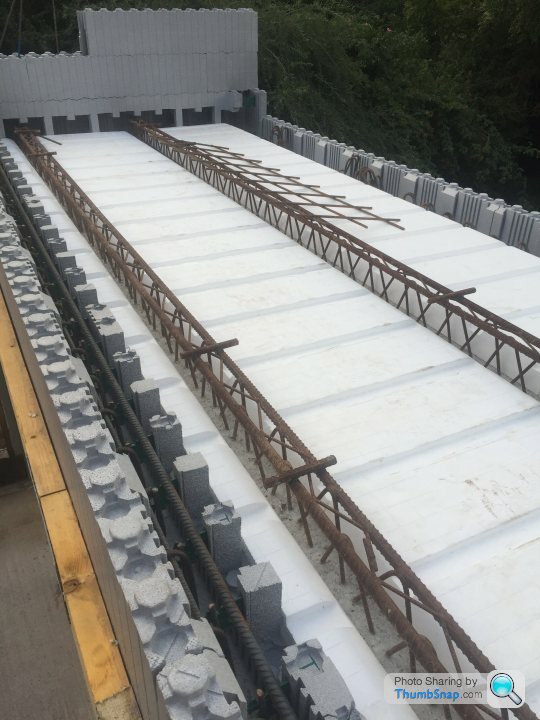
Then I put up the wall plates to support the floor beams, which will be top chord hung posi joists.. The wall plates are secured by J bolts hooked around a central rebar and then cast into the concrete.
These things are never moving!
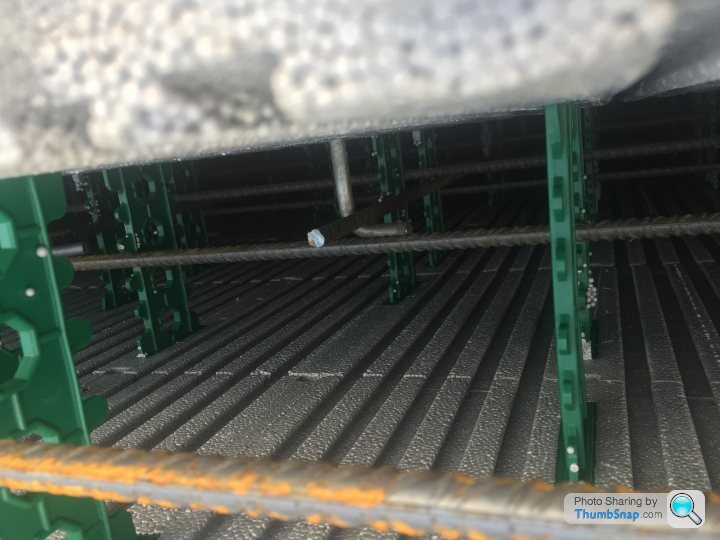
Prepare some bracing and then ready for first pour.
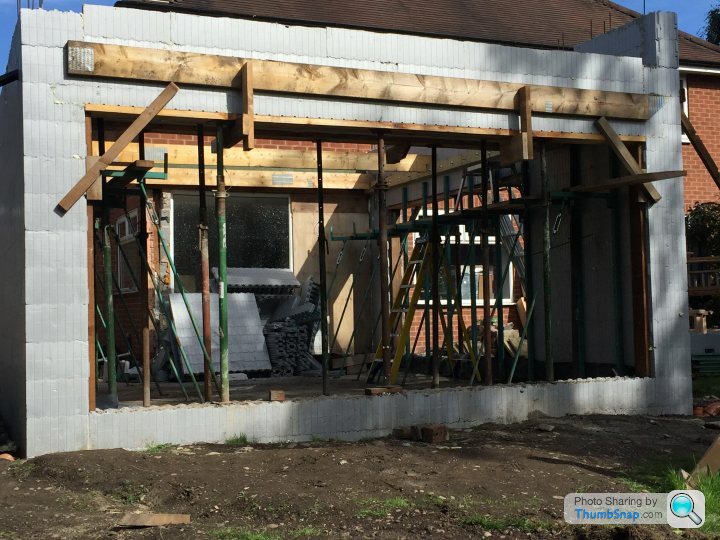
I don’t have any pics of the pours as I was too busy running around making sure everything went where it was supposed to. Fortunately it all went off without too much of a hitch, well once we’d sorted the concrete mix to be less stoney and able to be pumped smoothly.
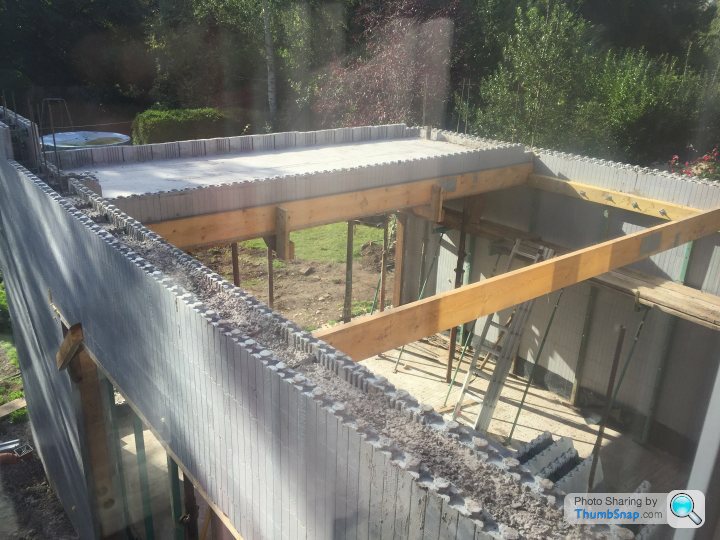
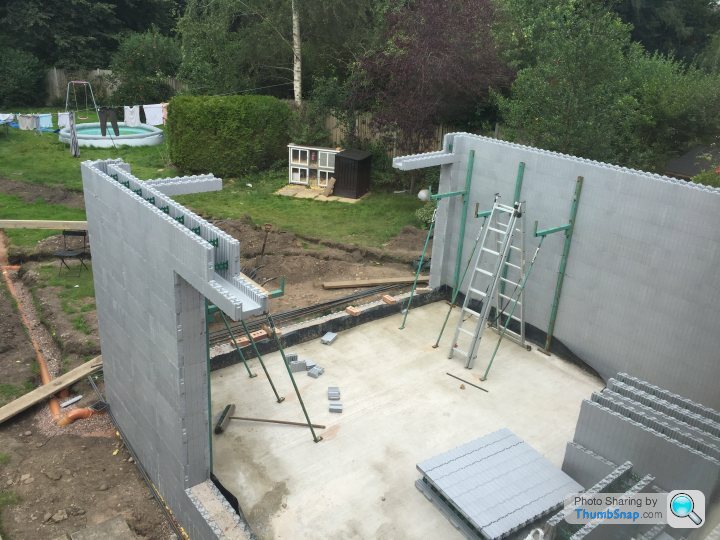
Then had to get these little steels into the garage to support the first floor. They need to go in now so that the end of the longest beam is cast into the concrete we’ll pour for the ground floor.
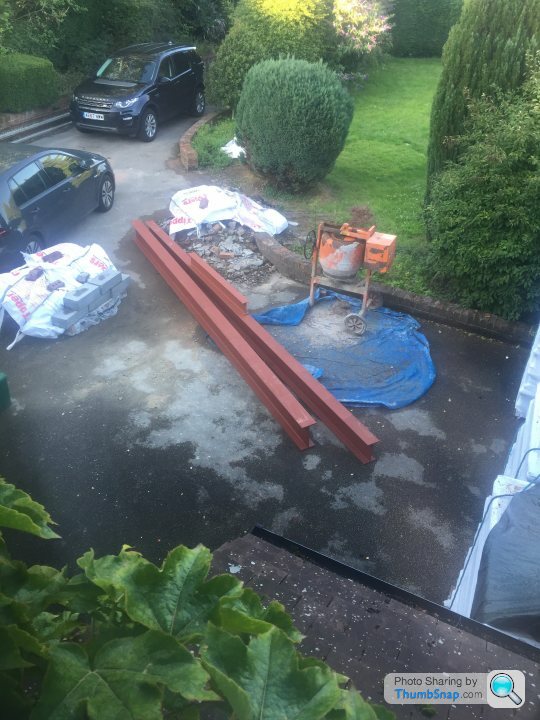
5 mates and 2 genies made short work of it and we had them in place in a little under two hours.
Pics are a few weeks on with first couple of courses of blocks concreted on top
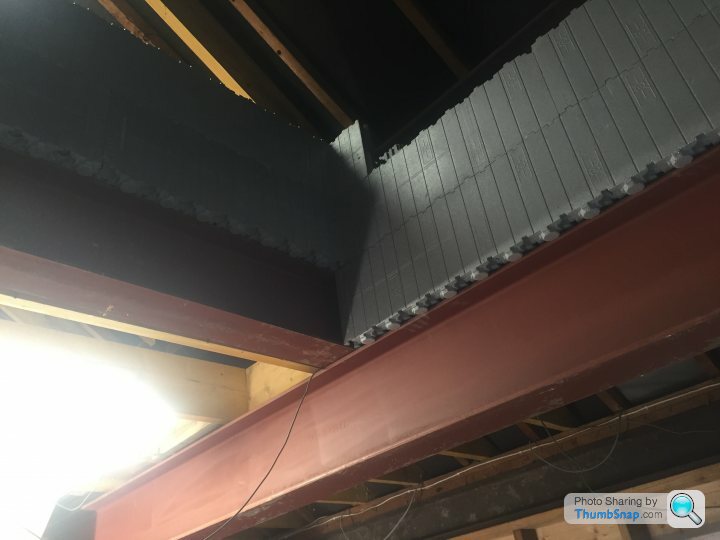
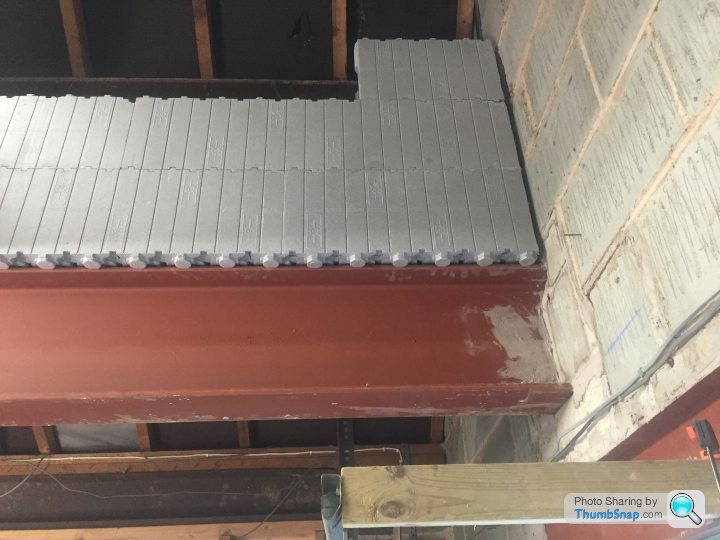
These were the only steels I needed on the project as all the other openings I cast the beams in concrete around rebar designed by a SE.
Something like this
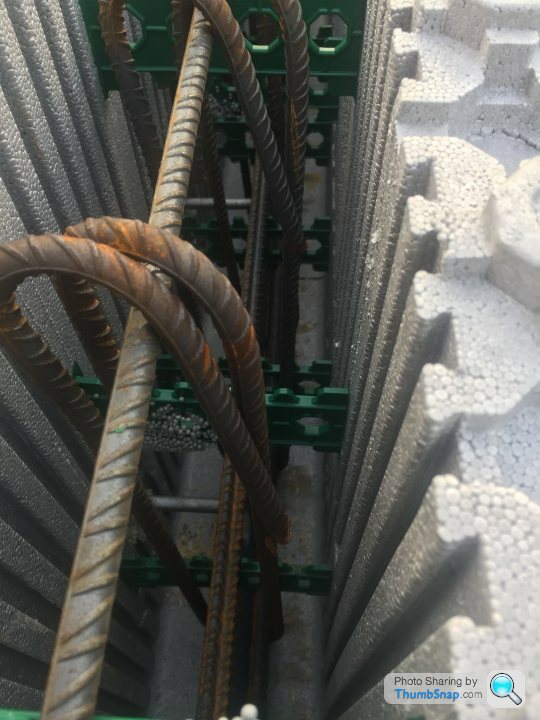
I then had the balcony to construct. This is an insulated base supported by concrete reinforced beams at 750mm centres with a rebar grid on top. This took a little while to finish
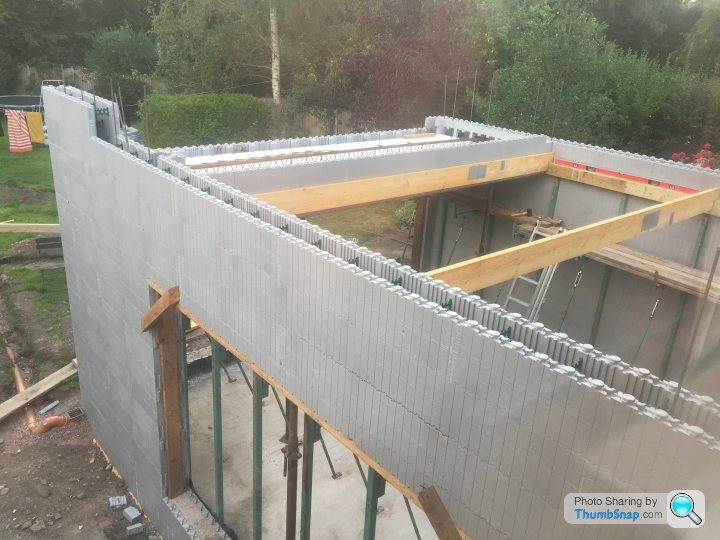
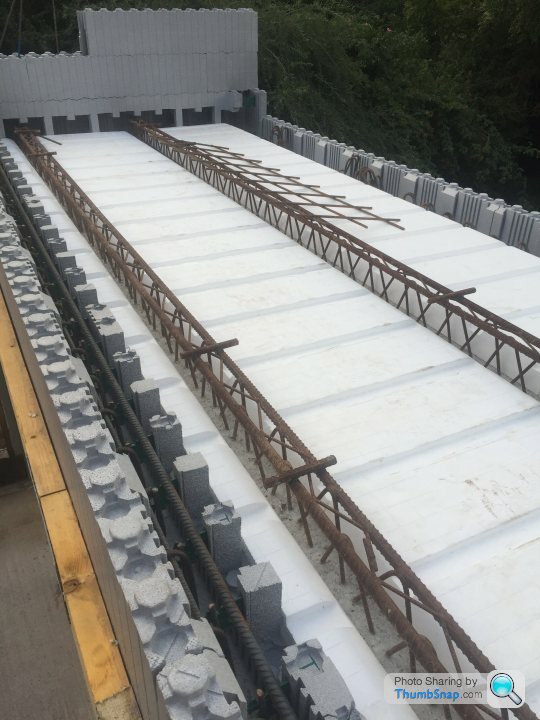
Then I put up the wall plates to support the floor beams, which will be top chord hung posi joists.. The wall plates are secured by J bolts hooked around a central rebar and then cast into the concrete.
These things are never moving!
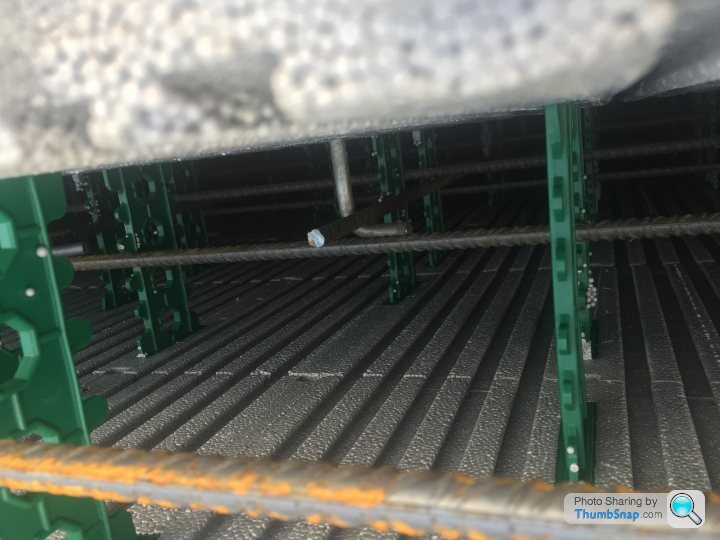
Prepare some bracing and then ready for first pour.
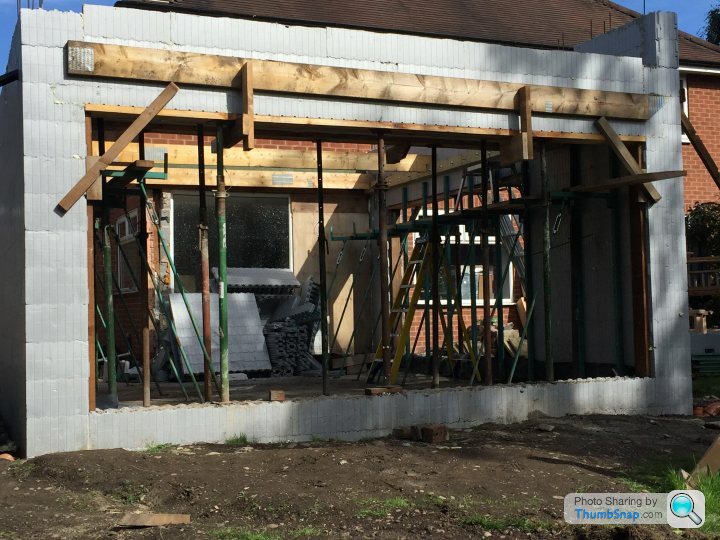
I don’t have any pics of the pours as I was too busy running around making sure everything went where it was supposed to. Fortunately it all went off without too much of a hitch, well once we’d sorted the concrete mix to be less stoney and able to be pumped smoothly.
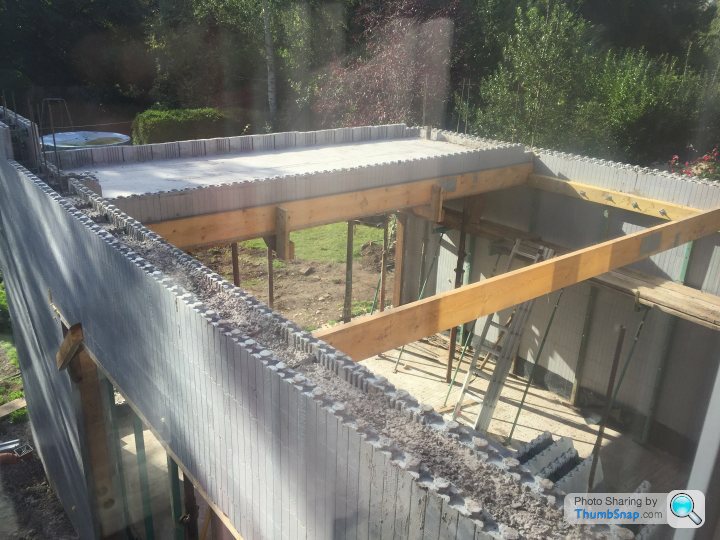
The ground floor ceiling joists went in next and I also cut the ICF blocks at the front and back of the balcony flush with the slab
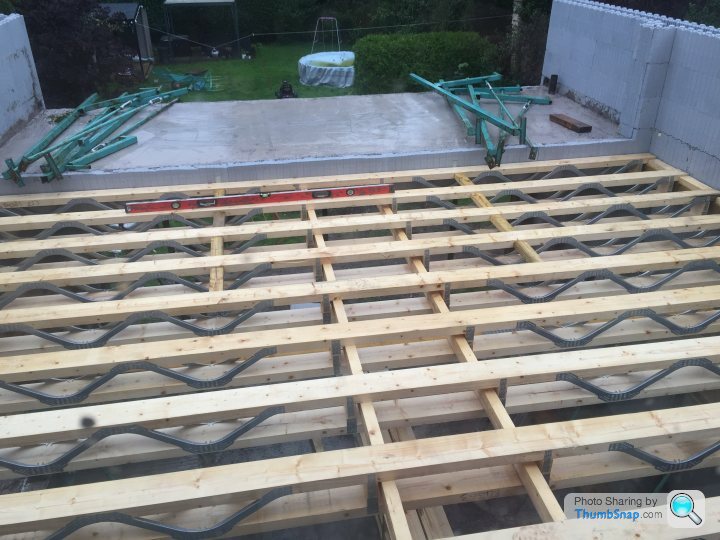
That gave me something to work from then to get the first floor walls built.
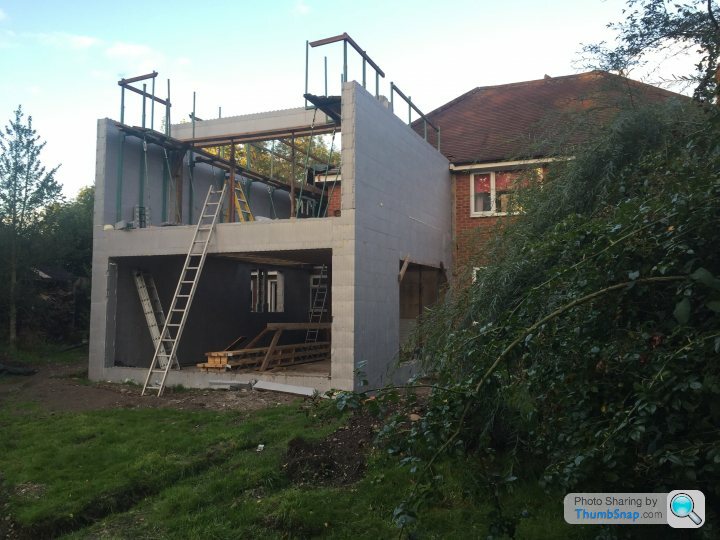
Had to open up the garage roof
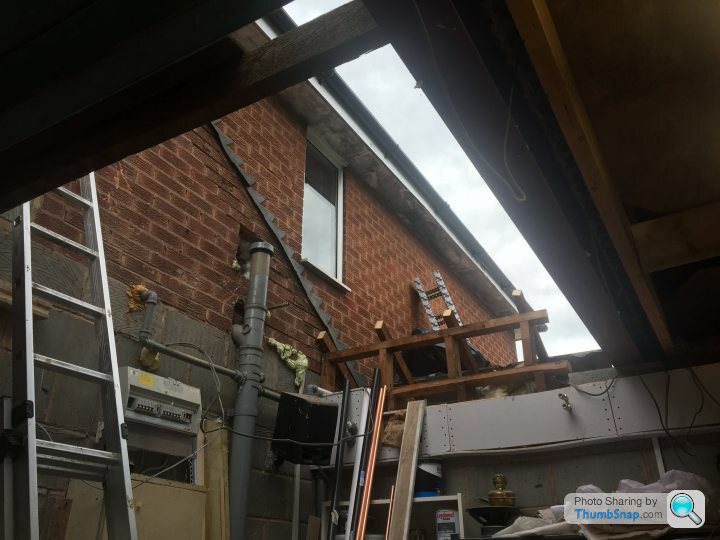
This lot went up a lot quicker than the ground floor. There was less structural stuff and I also had the benefit of one floors experience
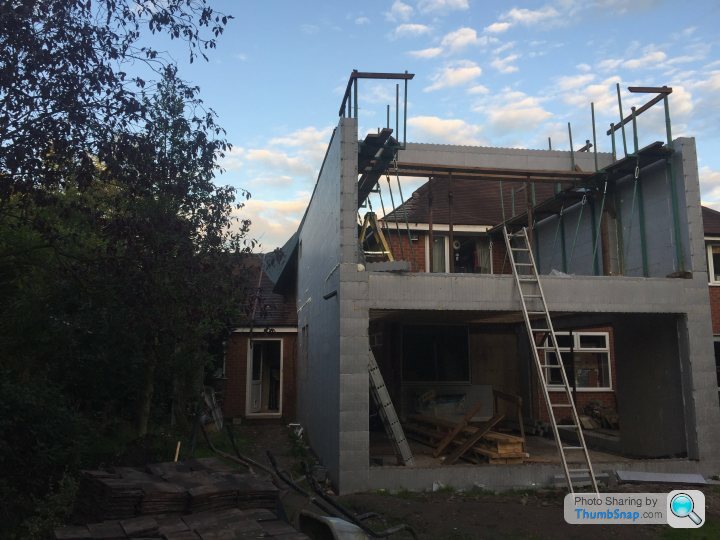
The first floor continues all the way down the side of the house and over the garage. I also had to construct this dormer on the front. This is later when i’d put some brick slips in place but more on that to come.
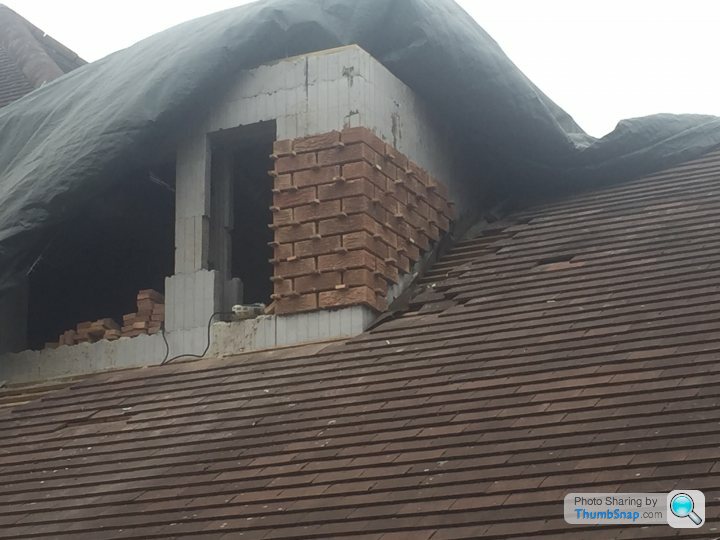
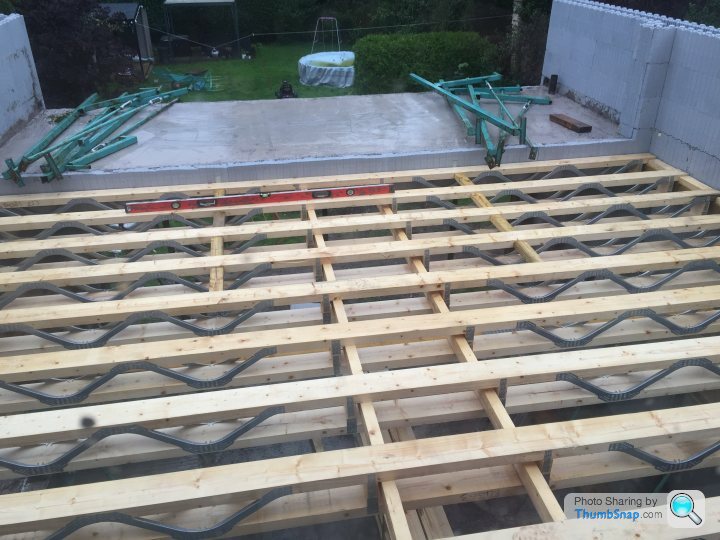
That gave me something to work from then to get the first floor walls built.
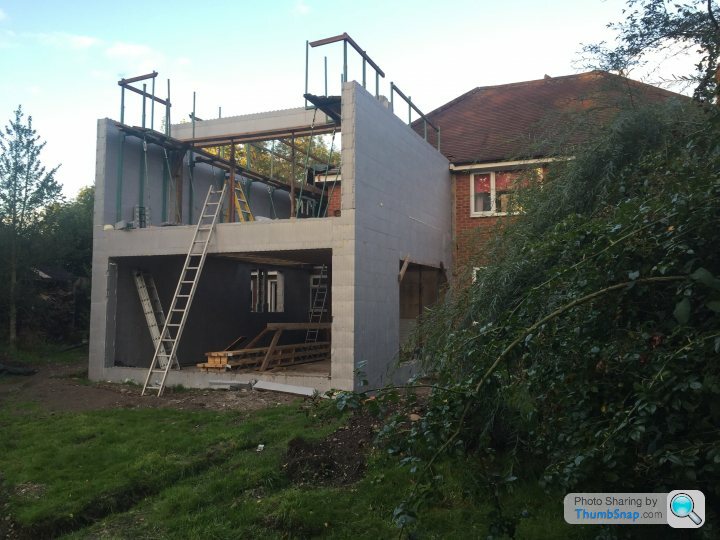
Had to open up the garage roof
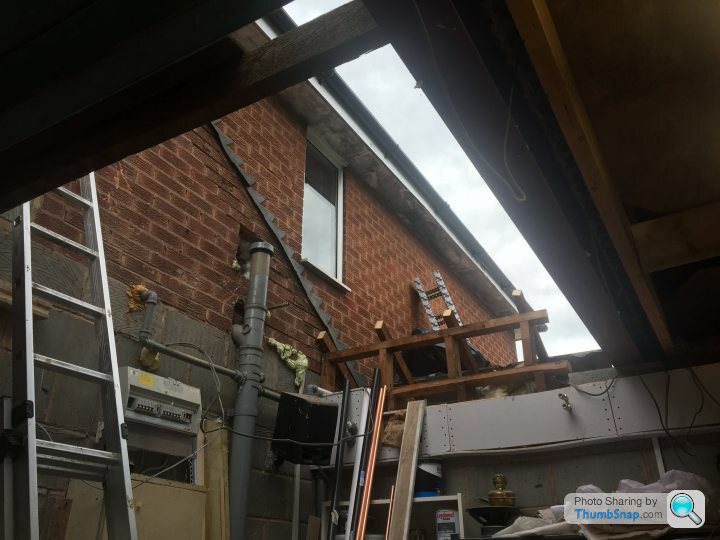
This lot went up a lot quicker than the ground floor. There was less structural stuff and I also had the benefit of one floors experience
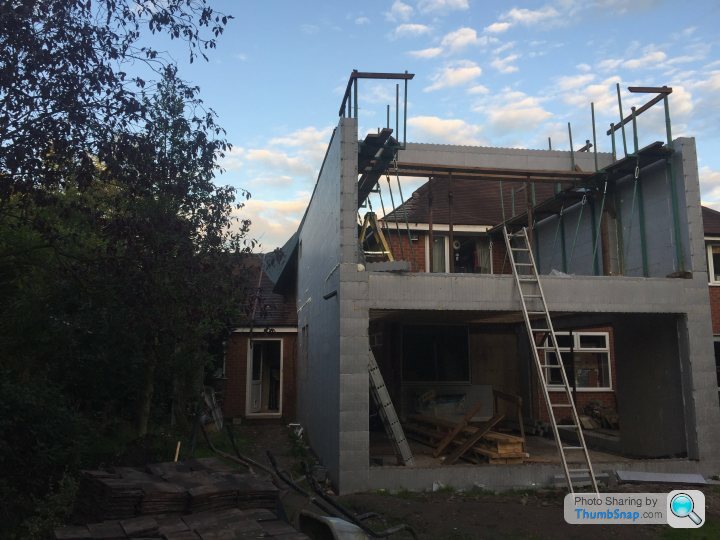
The first floor continues all the way down the side of the house and over the garage. I also had to construct this dormer on the front. This is later when i’d put some brick slips in place but more on that to come.
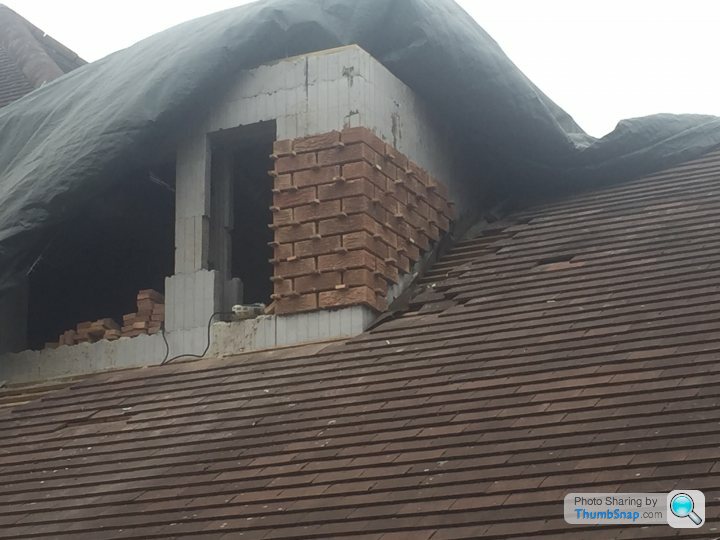
Second floor concrete pour then happened at the end of August. Almost had a burst but fortunately noticed the wall move a little and moved the boom elsewhere while we braced it up.
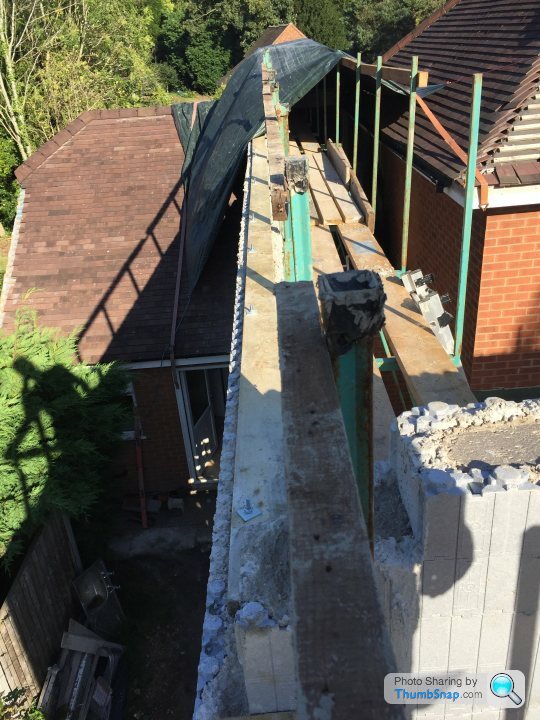
Wall plates were fitted to bolts cast into the wet concrete. They’re never moving again either!
Whilst waiting for the scaffold to come we had a little time to think through our choice of finish. The original plan was to face the walls with brick slips to match the existing house. However after much searching we couldn’t find a close enough match. From a good landing perspective I would still need to somehow do the front dormer but we had a little more scope on the back.
We decided on Siberian Larch cladding for the rear. I just had to figure out brick slips for the front. I’d kept a few bricks back from the kitchen demolition so out came the whizzer and I made my own...
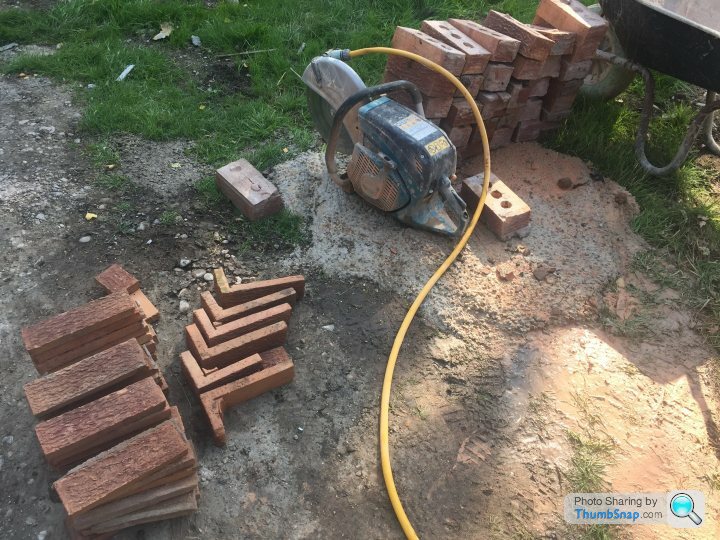
The corners were particularly interesting to cut! I managed to do enough to cover the front though.
Scaffold then went up in the first week of September and the mammoth job of the roof started.
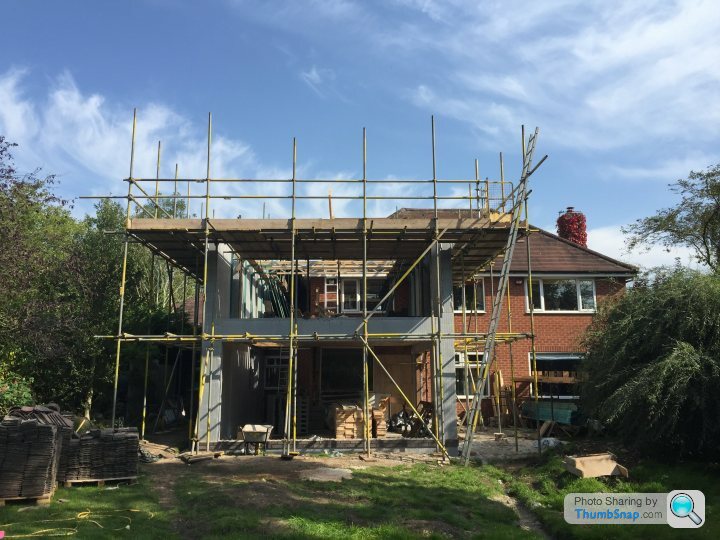
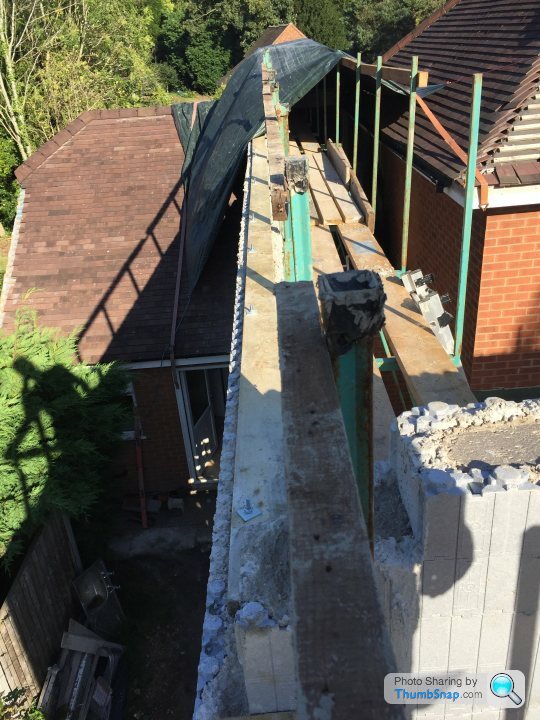
Wall plates were fitted to bolts cast into the wet concrete. They’re never moving again either!
Whilst waiting for the scaffold to come we had a little time to think through our choice of finish. The original plan was to face the walls with brick slips to match the existing house. However after much searching we couldn’t find a close enough match. From a good landing perspective I would still need to somehow do the front dormer but we had a little more scope on the back.
We decided on Siberian Larch cladding for the rear. I just had to figure out brick slips for the front. I’d kept a few bricks back from the kitchen demolition so out came the whizzer and I made my own...
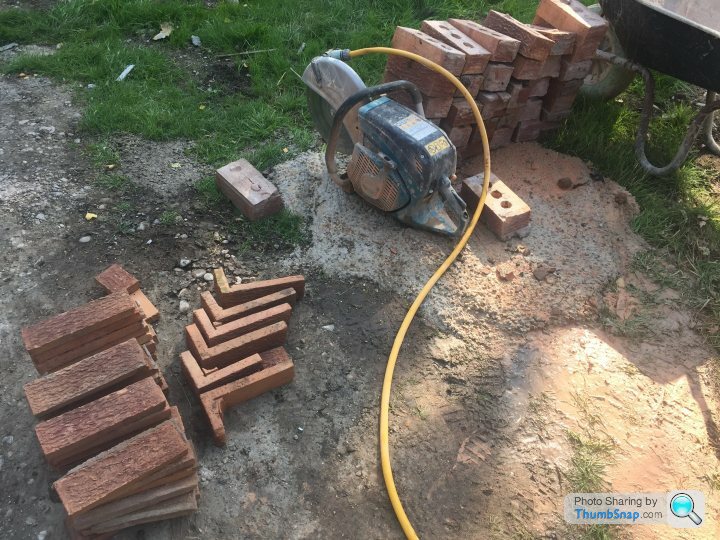
The corners were particularly interesting to cut! I managed to do enough to cover the front though.
Scaffold then went up in the first week of September and the mammoth job of the roof started.
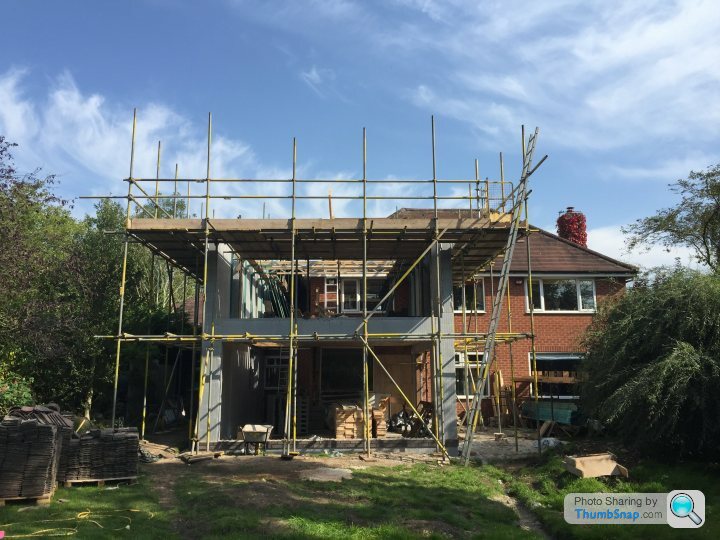
I decided to go for a cut roof to maximise available space inside. Also as the existing roof and new roof would be slightly different pitches 41deg on the old to 45deg on the new. This was to maximise headroom in the new bedroom above the extension.
First job was to get the timber ridge beam up and then 8x2 rafters. I’m a lot fitter and stronger than when I started this!
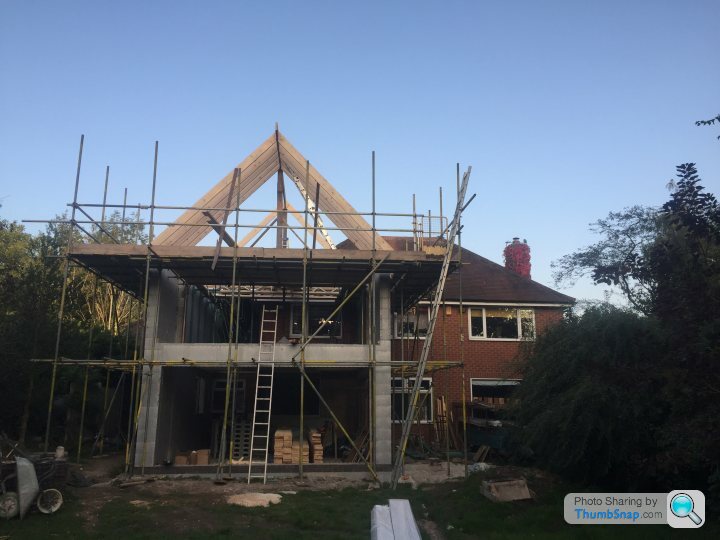
A few more rafters in the following day
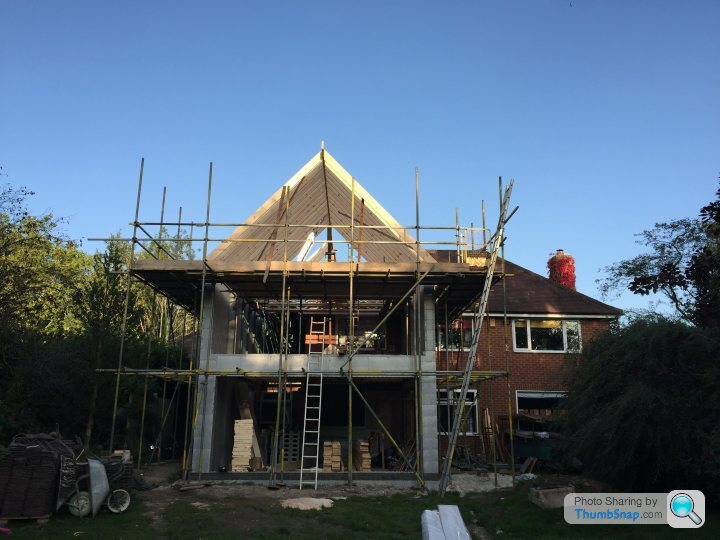
Then is was time to break into the house roof
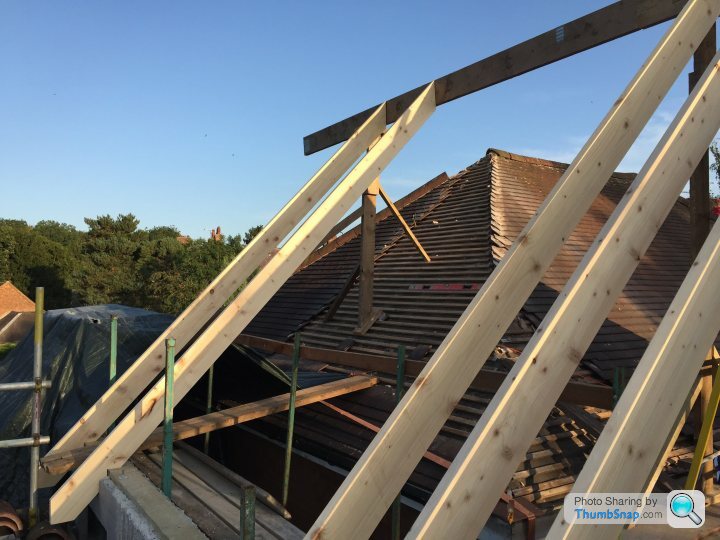

This clearly wasn’t a one man job and I had help from my Dad for a lot of this framing. He’s not a builder either but has taught me everything I know.
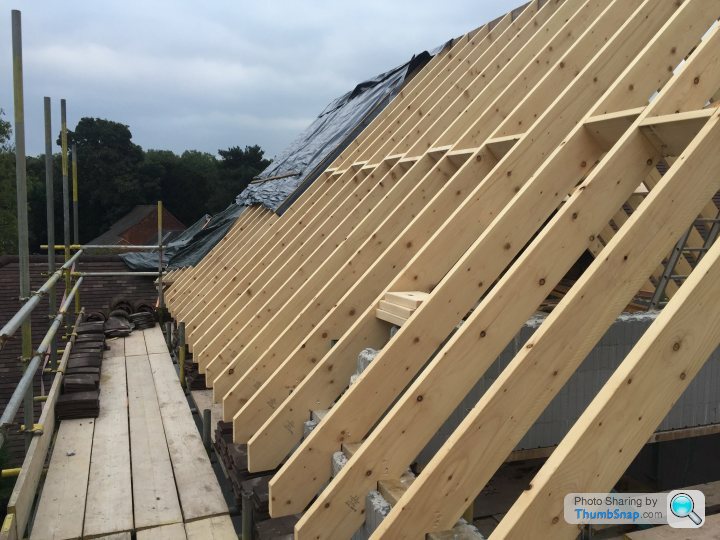
Roof framed and most noggins done. Temporary tarp over the existing house. Fortunately the weather stayed reasonably fine.
The floor wasn’t in at this point but that turned up and I lugged all of those up by myself and fitted them. If they’d have arrived a week earlier it would have made the roof a lot easier!
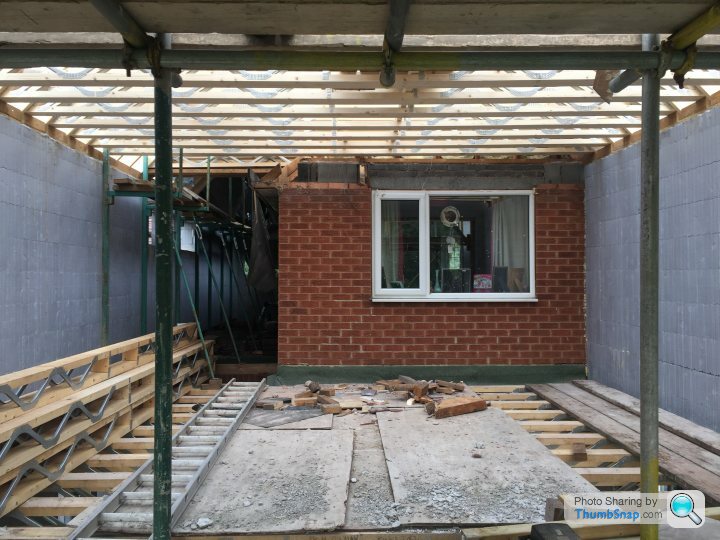
First job was to get the timber ridge beam up and then 8x2 rafters. I’m a lot fitter and stronger than when I started this!
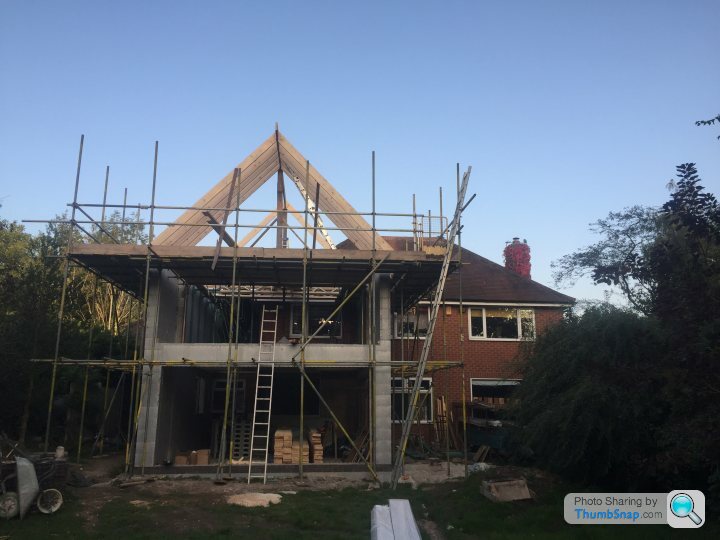
A few more rafters in the following day
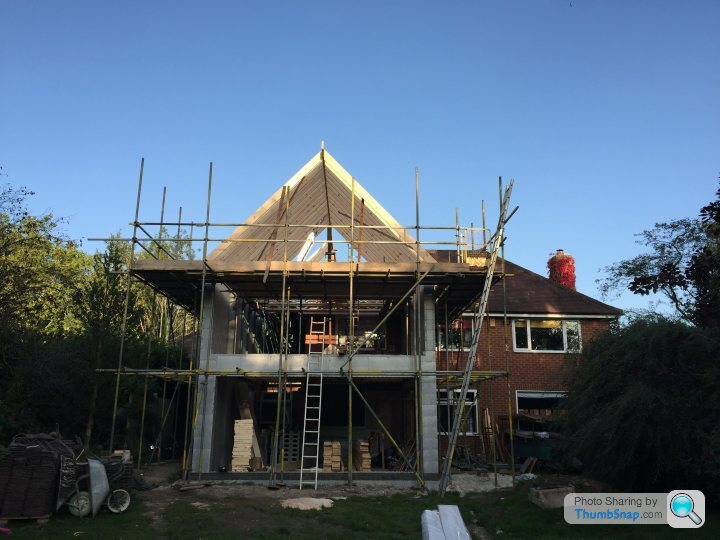
Then is was time to break into the house roof

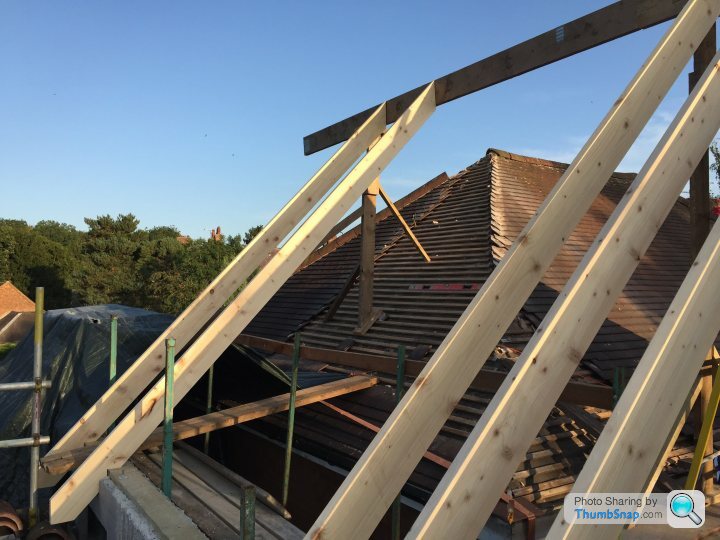

This clearly wasn’t a one man job and I had help from my Dad for a lot of this framing. He’s not a builder either but has taught me everything I know.
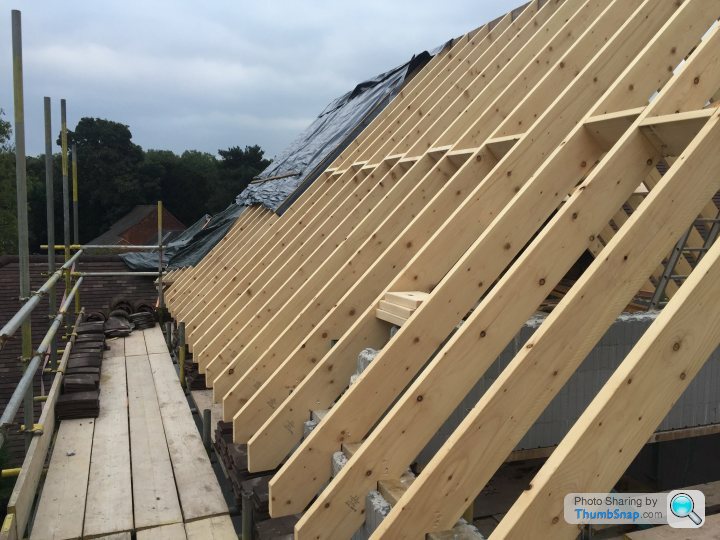
Roof framed and most noggins done. Temporary tarp over the existing house. Fortunately the weather stayed reasonably fine.
The floor wasn’t in at this point but that turned up and I lugged all of those up by myself and fitted them. If they’d have arrived a week earlier it would have made the roof a lot easier!
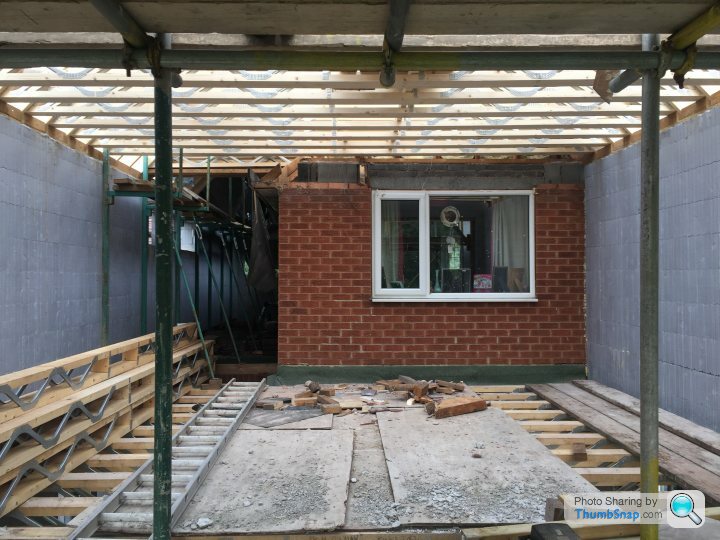
Time to felt and batten. As it is having clay tiles (acme sandstorm) it needs a gazillion battens. One every 65mm on a 4.5m long rafter that’s on a 14m long roof.
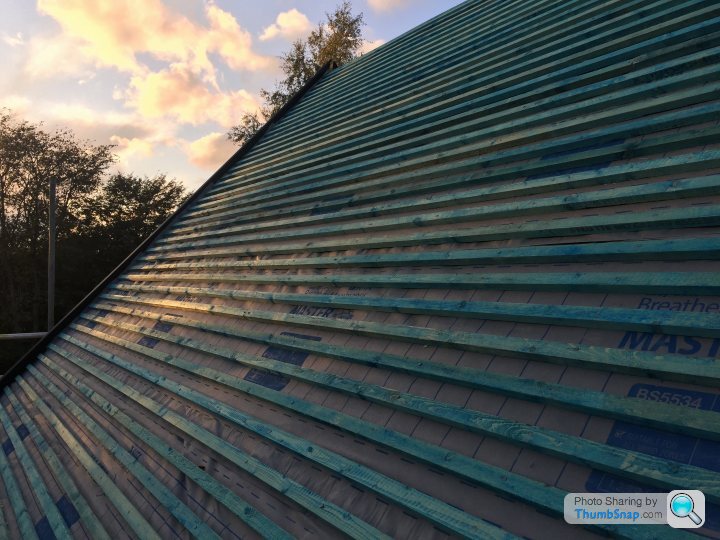
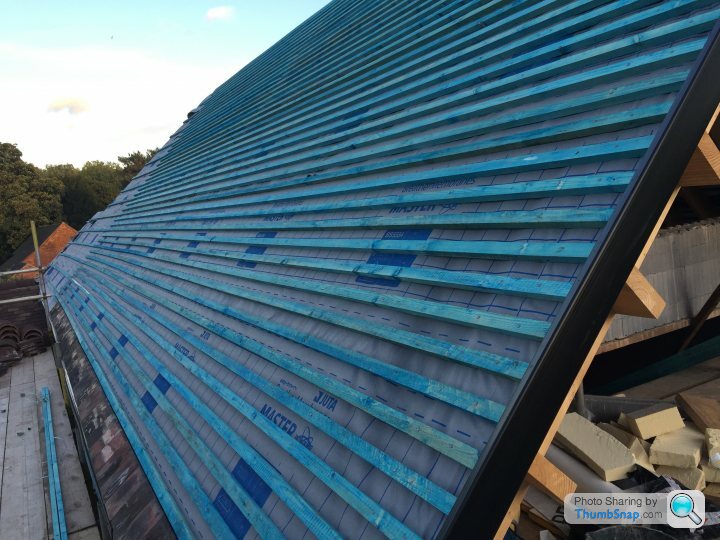
The view inside looking in
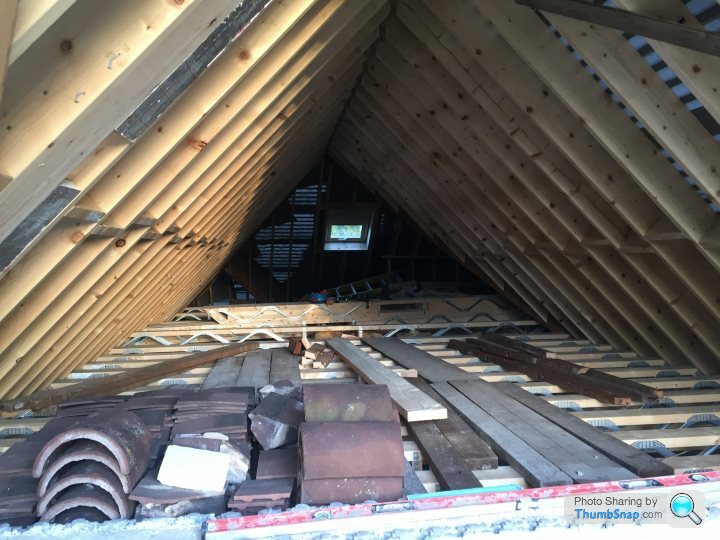
And looking out
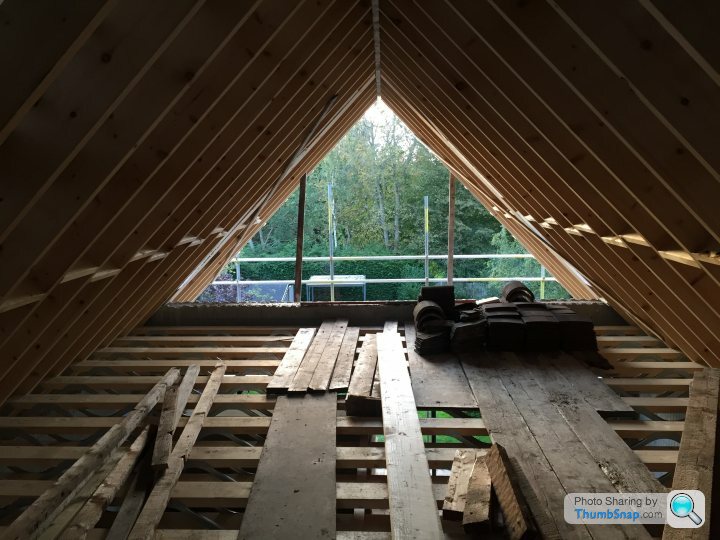
Time to tile the thing! First things first how to get 6000 tiles up on the scaffold. We looked at hiring a scaffold hoist at £150 for a week but a quick check on Amazon and we found one to buy for £85. It’s quite possibly the best £85 I’ve ever spent!
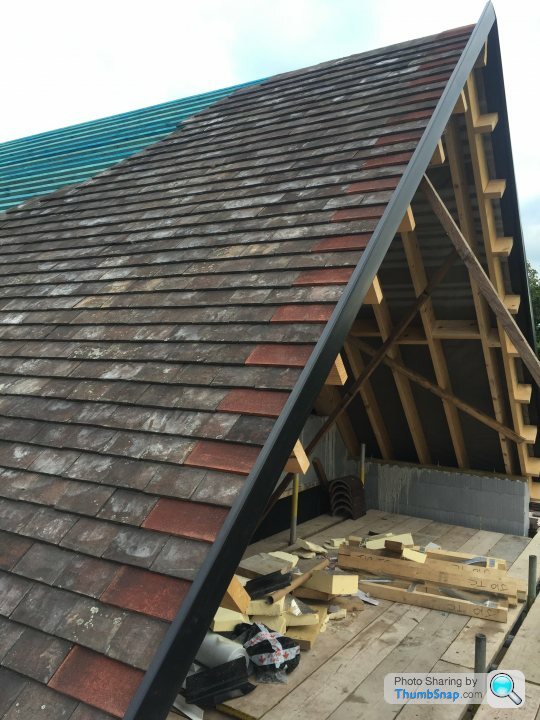
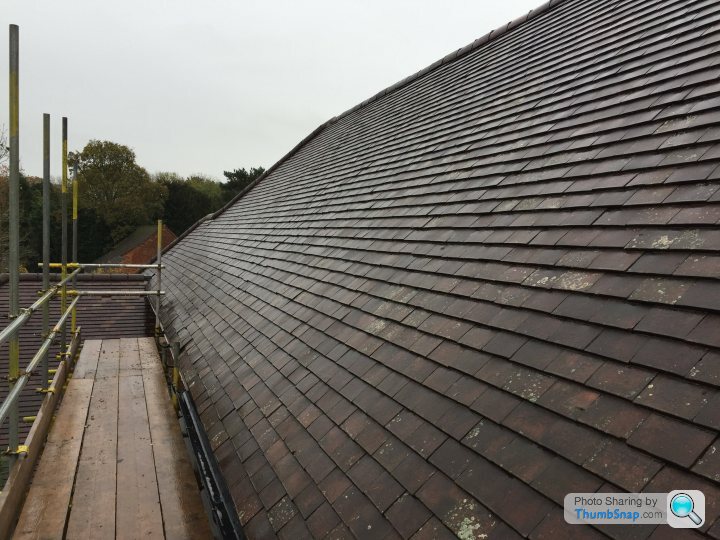
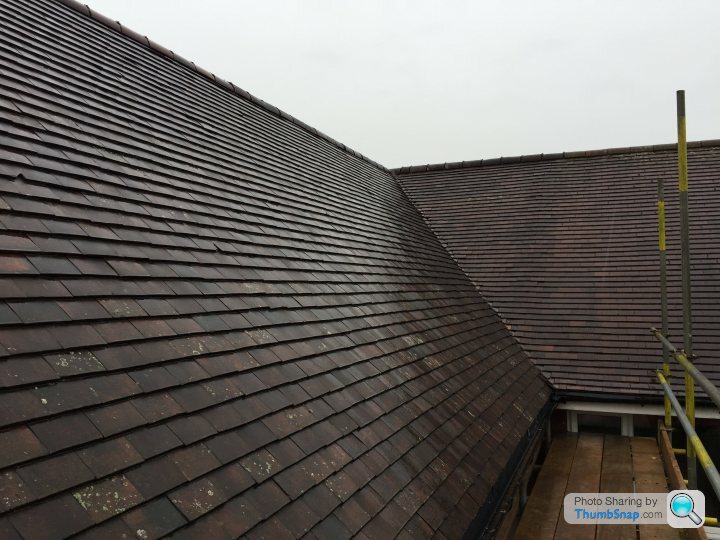
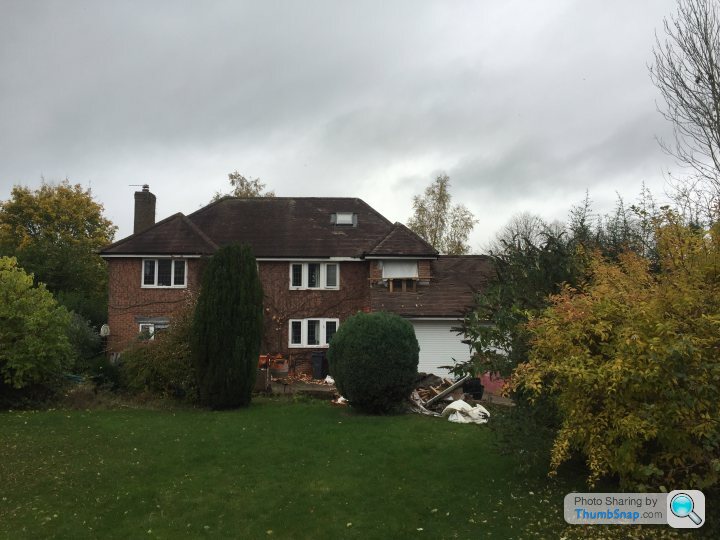
Roof done at last - that took almost 6 weeks to do!
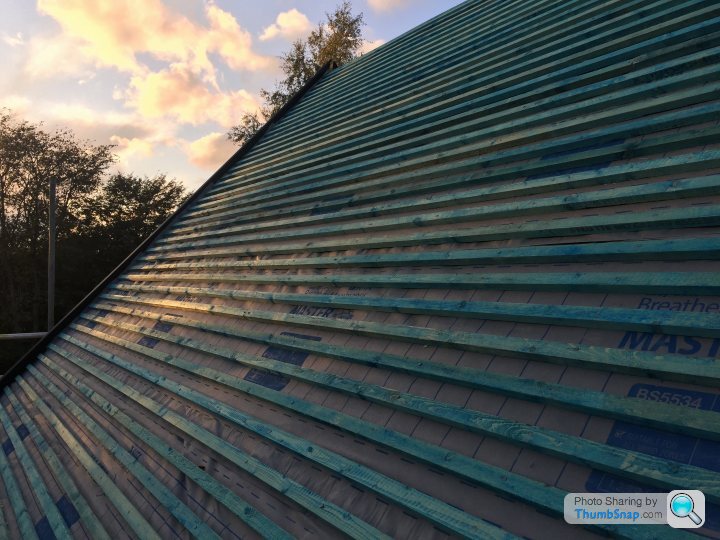
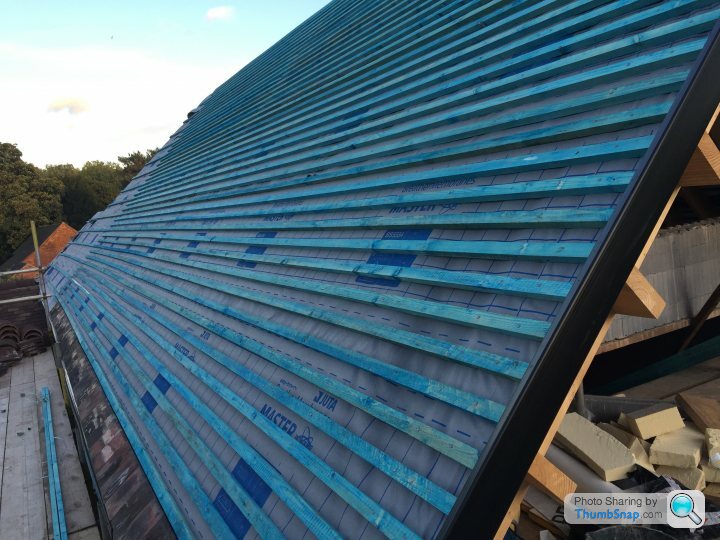
The view inside looking in
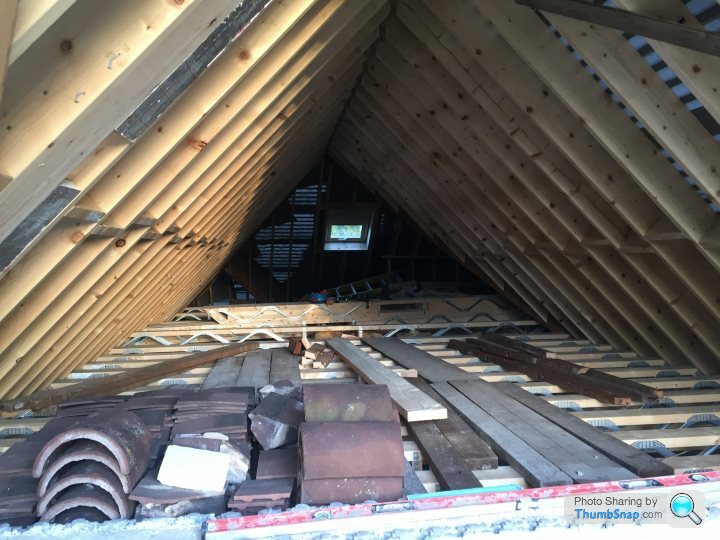
And looking out
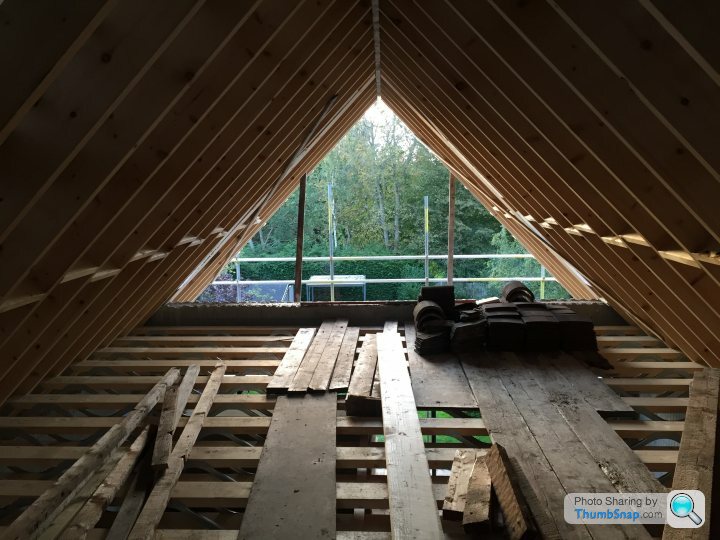
Time to tile the thing! First things first how to get 6000 tiles up on the scaffold. We looked at hiring a scaffold hoist at £150 for a week but a quick check on Amazon and we found one to buy for £85. It’s quite possibly the best £85 I’ve ever spent!
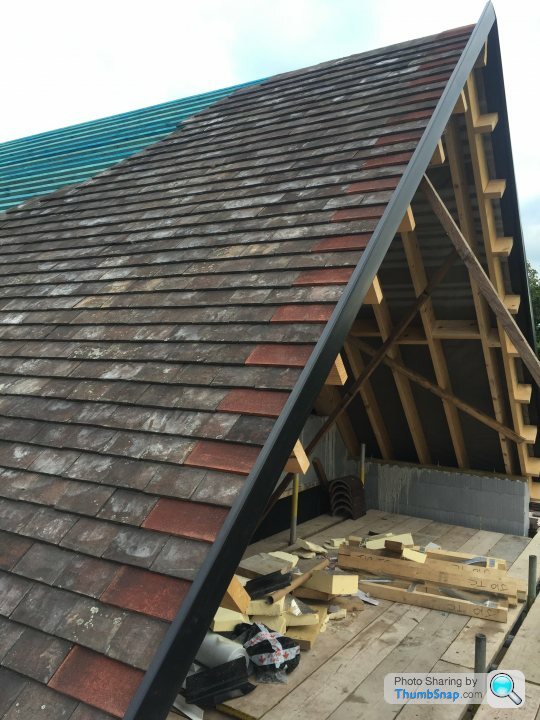
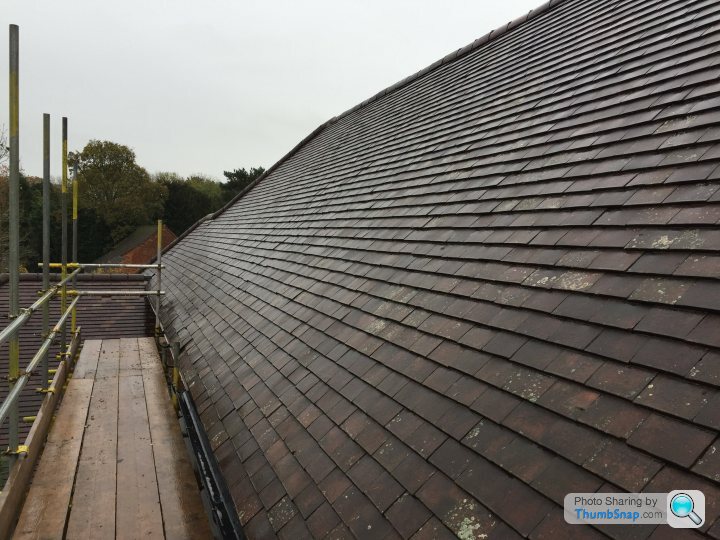
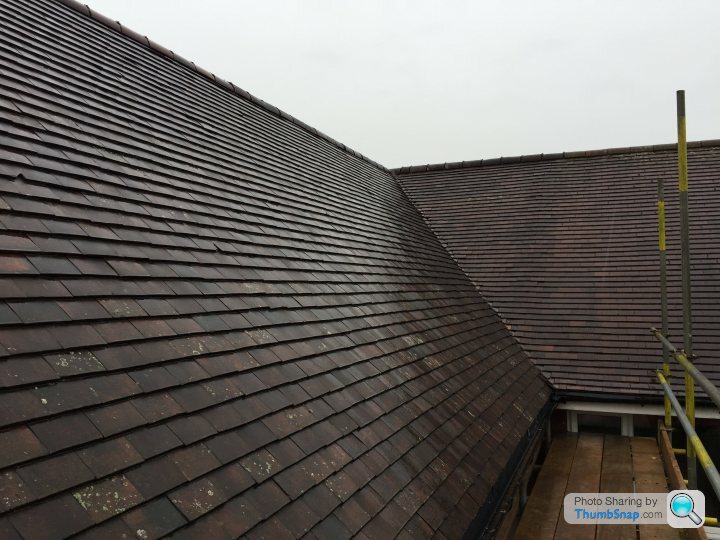
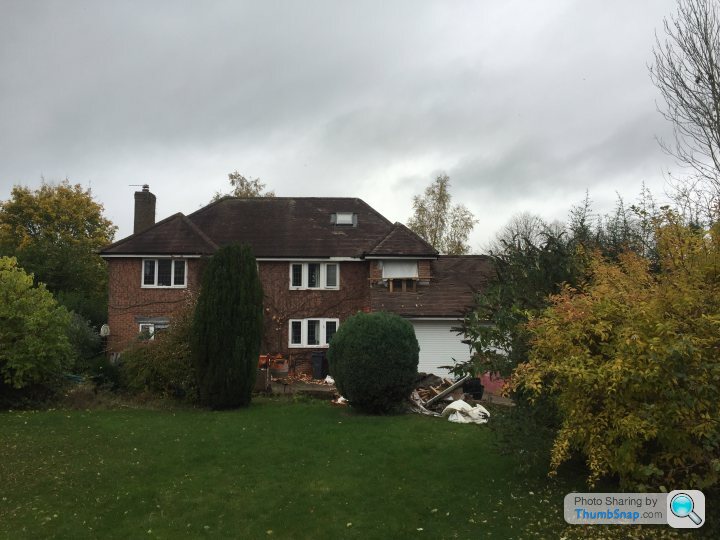
Roof done at last - that took almost 6 weeks to do!
Then it was a mad rush to get the final jobs done before the scaffold came down in late October.
Cladding on the underside of the balcony roof:

And the guttering and fascias
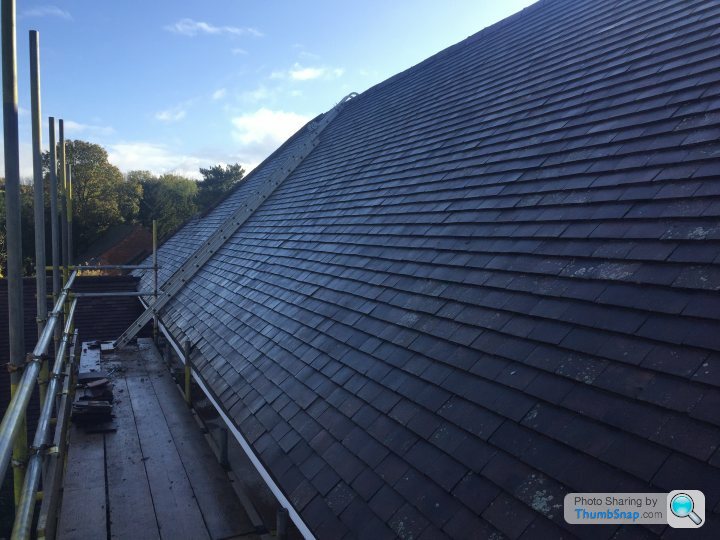
Finally I moved the flooring sheets on to their respective floors:
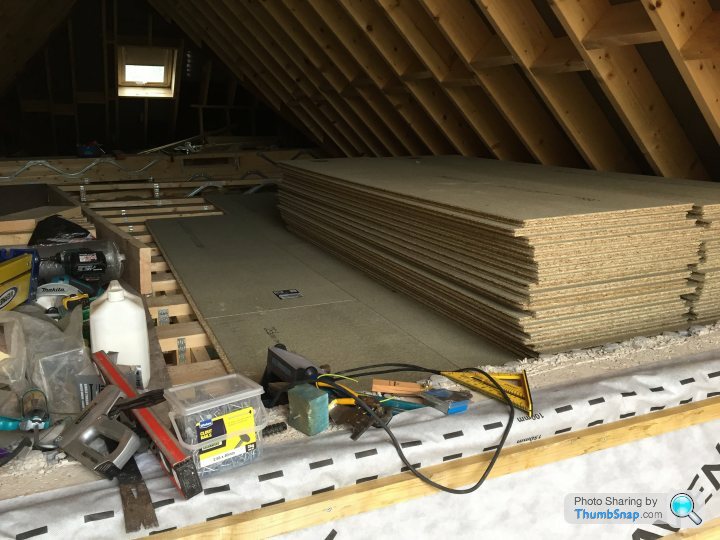
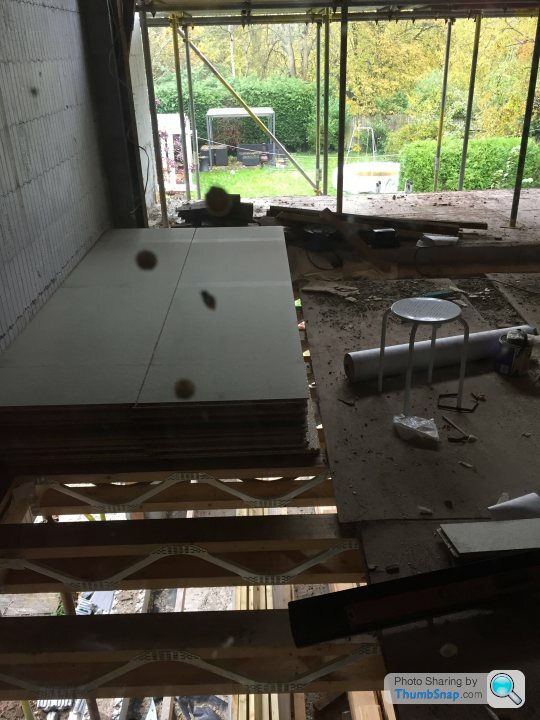
Then the scaffold came down and it looked enormous! It was at this point I stepped back and thought “f
k me” I made that!
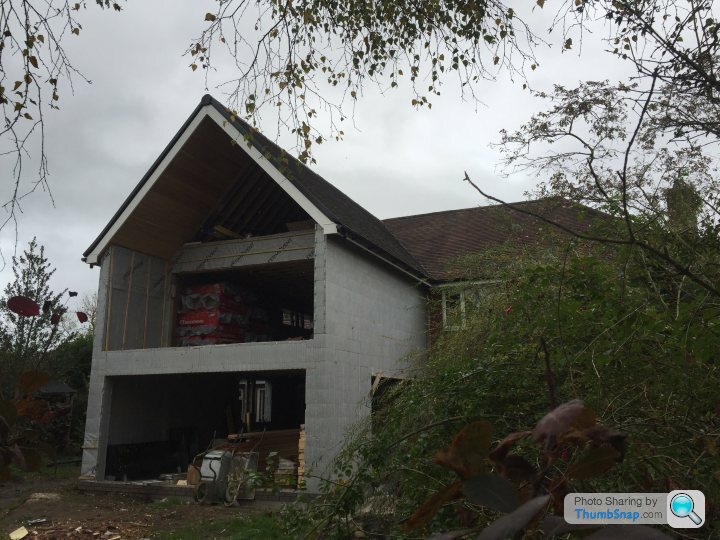
Cladding on the underside of the balcony roof:

And the guttering and fascias
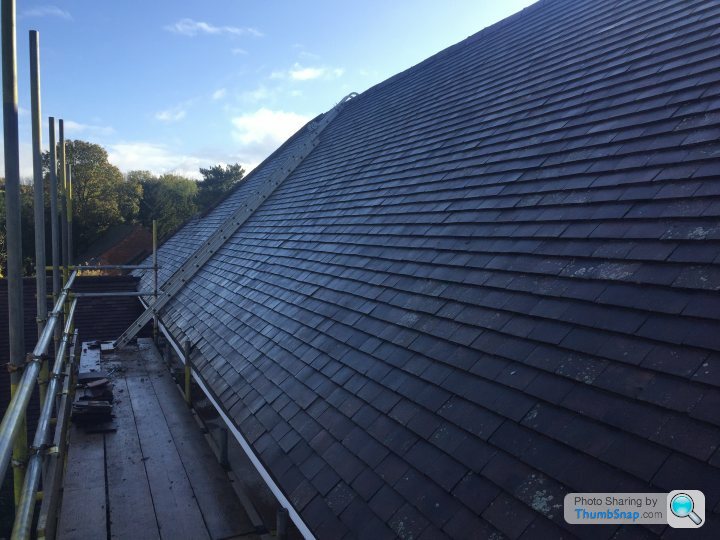
Finally I moved the flooring sheets on to their respective floors:
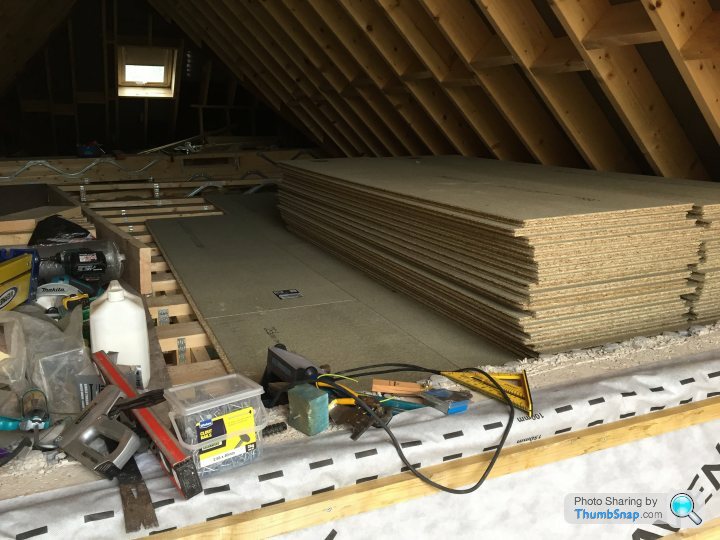
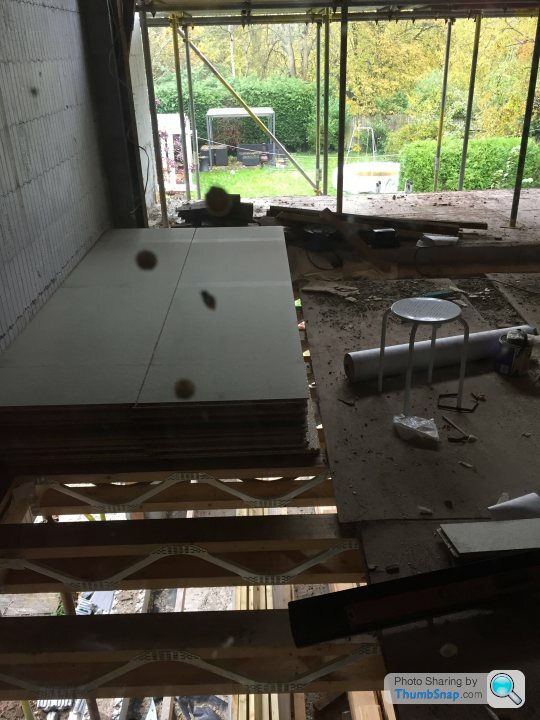
Then the scaffold came down and it looked enormous! It was at this point I stepped back and thought “f

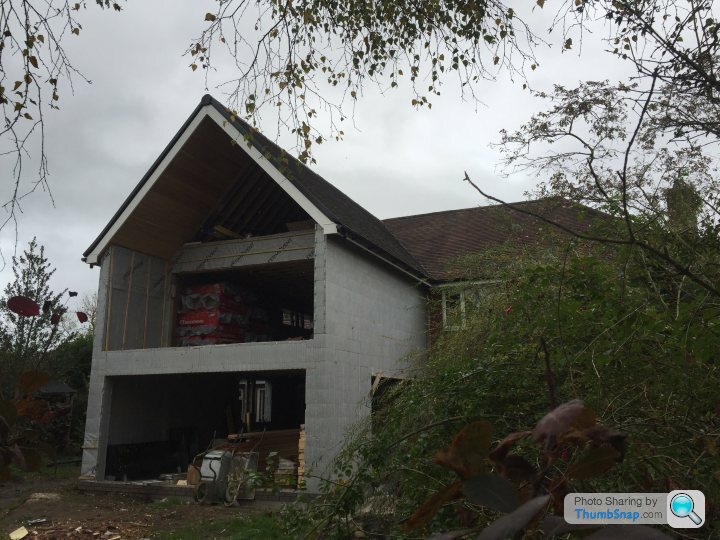
Next it was onto finishing the front ready for Windows and bifolds.
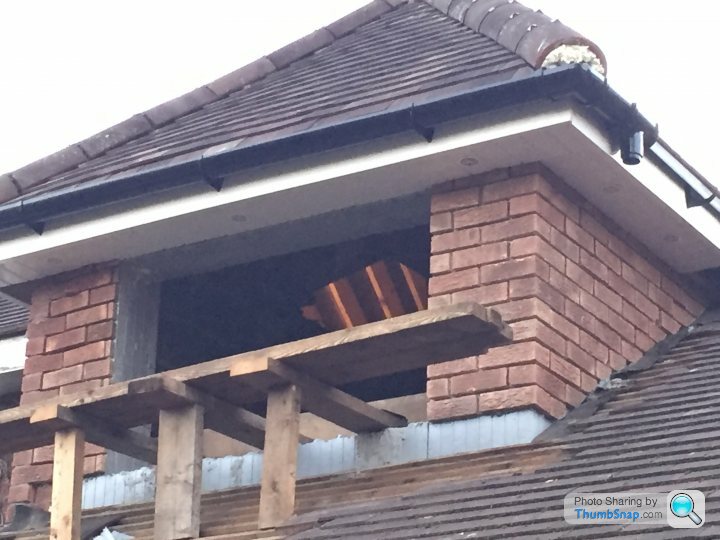
Note the Heath Robinson temporary platform. I managed to come off the garage roof whilst we were re-battening the dormer. A batten came loose as I was holding it and stood on the sloping garage roof. Fortunately I managed to keep my balance and ran down the roof backwards, jumped out at the end and landed on my feet
. Sensibly my dad wouldn’t let me back up there until I had something flat to work from.
Got it finished and the window fitted without further incident:
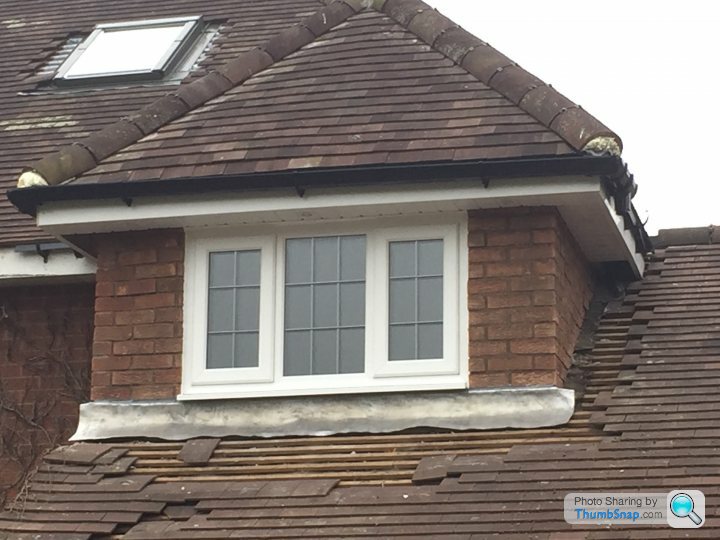
I’m out of tiles for now until I fit the remaining roof lights later this year. I should have enough over to finish tiling the garage roof.
Then it was the big bifolds round the back.
The ground floor was relatively straightforward. Me, Dad, Wifey, Eldest Daughter and BIL lifted them into place. The first floor one was a little trickier but we laid planks up-to the balcony and then, with a lot of help from my scaffold hoist (earning its way into my affections), we pushed and pulled it up.
Glass was then installed, with the exception of one panel that the manufacturer smashed loading it! We had to wait a while for the replacement.
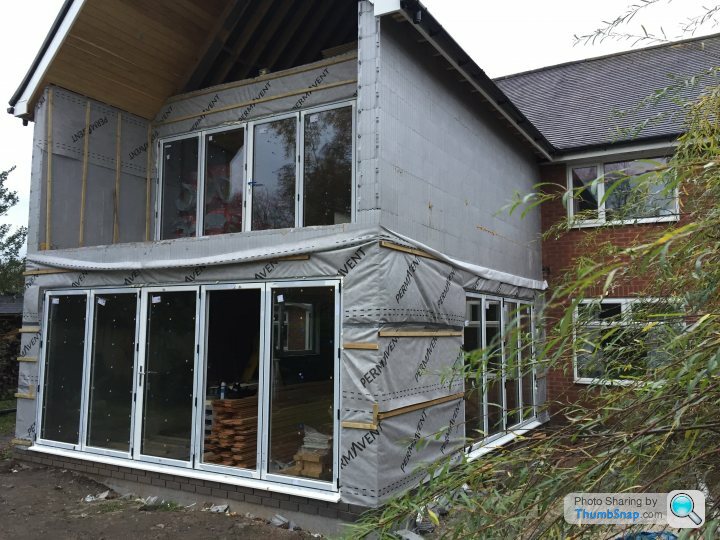
I had started to wrap the walls in membrane and batten ready for the cladding which had now arrived.
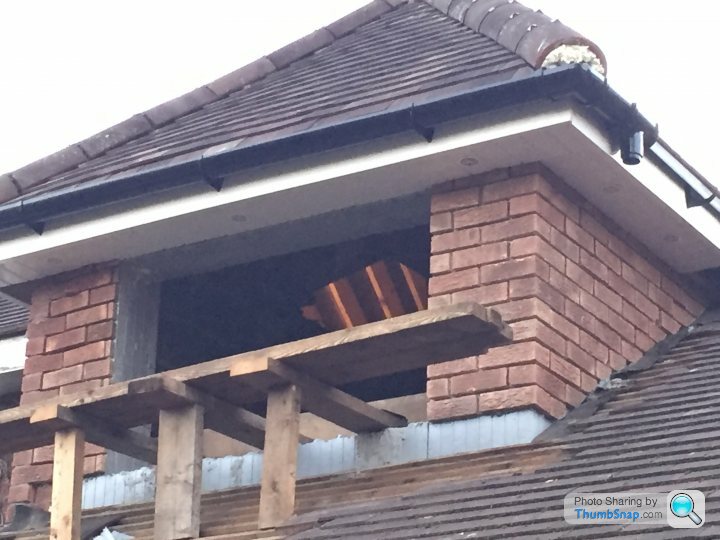
Note the Heath Robinson temporary platform. I managed to come off the garage roof whilst we were re-battening the dormer. A batten came loose as I was holding it and stood on the sloping garage roof. Fortunately I managed to keep my balance and ran down the roof backwards, jumped out at the end and landed on my feet

Got it finished and the window fitted without further incident:
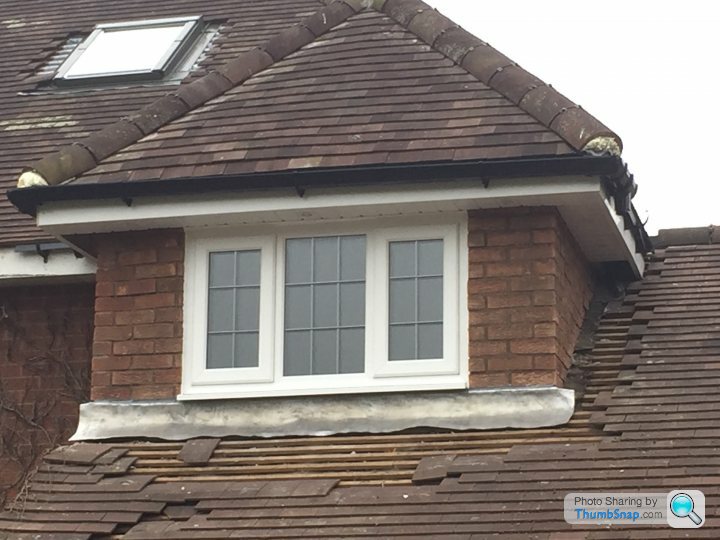
I’m out of tiles for now until I fit the remaining roof lights later this year. I should have enough over to finish tiling the garage roof.
Then it was the big bifolds round the back.
The ground floor was relatively straightforward. Me, Dad, Wifey, Eldest Daughter and BIL lifted them into place. The first floor one was a little trickier but we laid planks up-to the balcony and then, with a lot of help from my scaffold hoist (earning its way into my affections), we pushed and pulled it up.
Glass was then installed, with the exception of one panel that the manufacturer smashed loading it! We had to wait a while for the replacement.
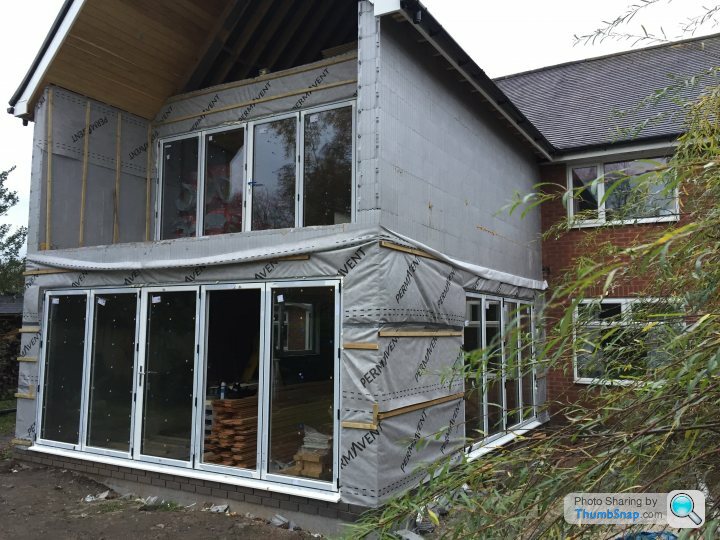
I had started to wrap the walls in membrane and batten ready for the cladding which had now arrived.
But before the floor was finished the balustrade went on the balcony
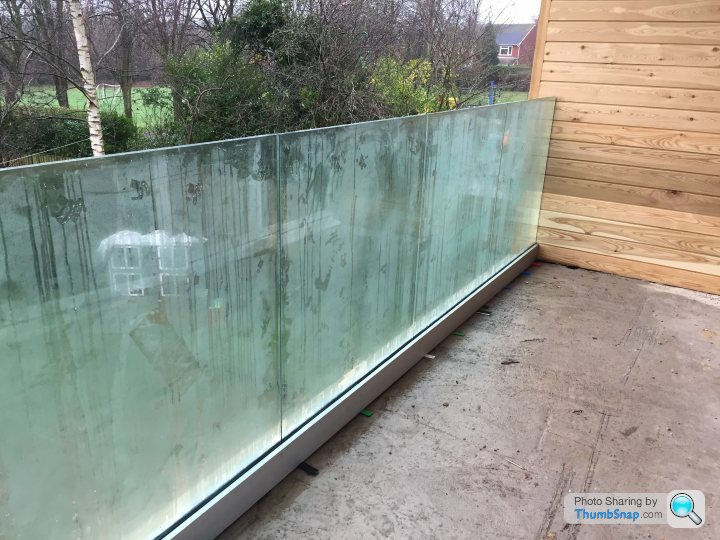
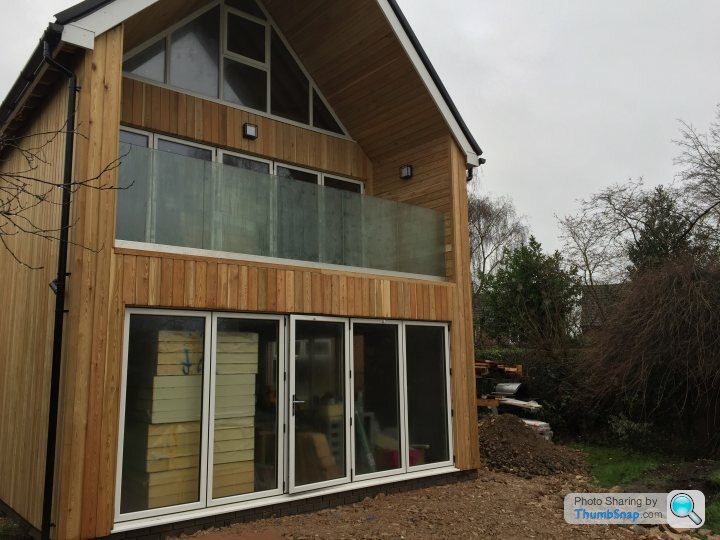
Although the panes of glass are under a metre wide and a metre and a bit high they weigh 70lgs each as they’re 21.5mm toughened laminated glass.
Then the insulation arrived:
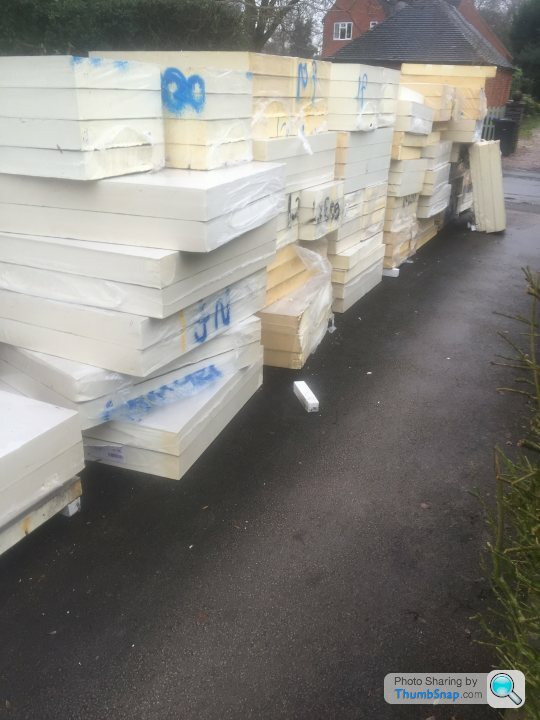
About a third of this is for the floor, the rest is for the loft.
Down and membrane on
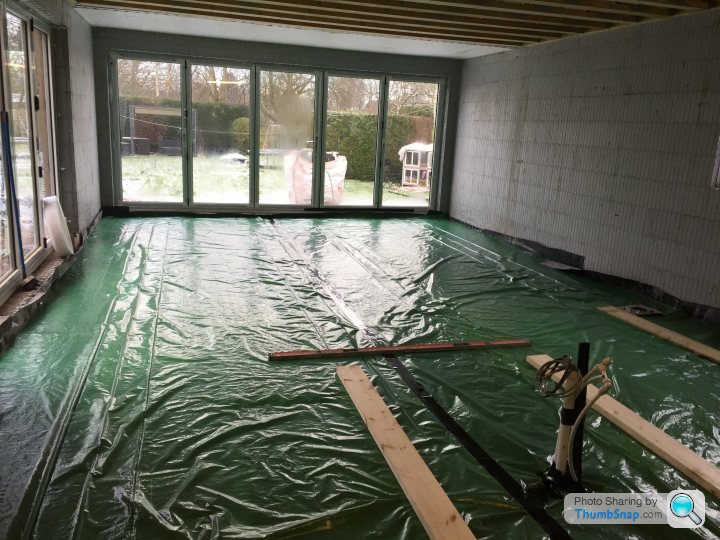
UFH pipes laid
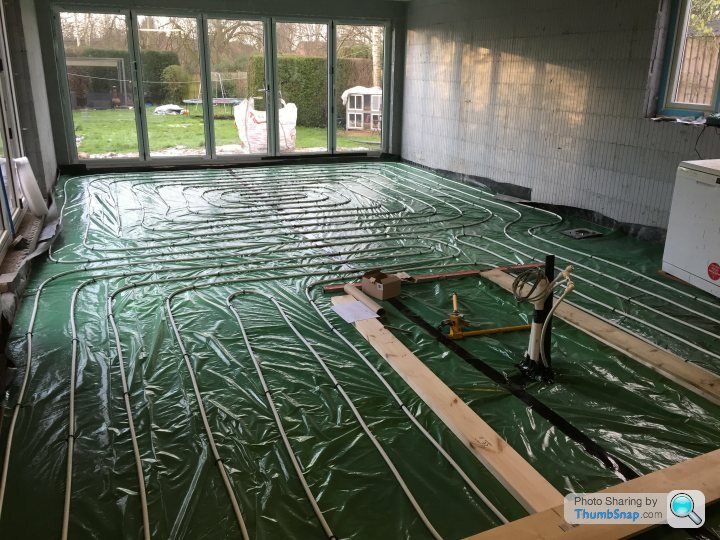
Screeding happened in early Jan and is one thing I didn’t do!
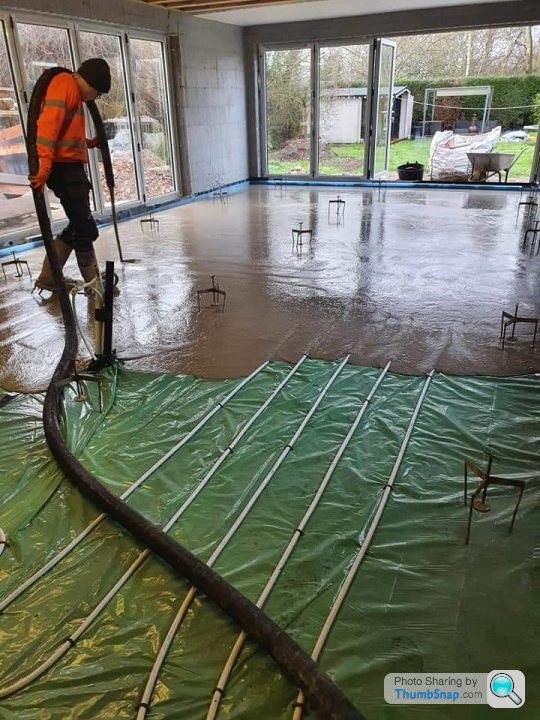
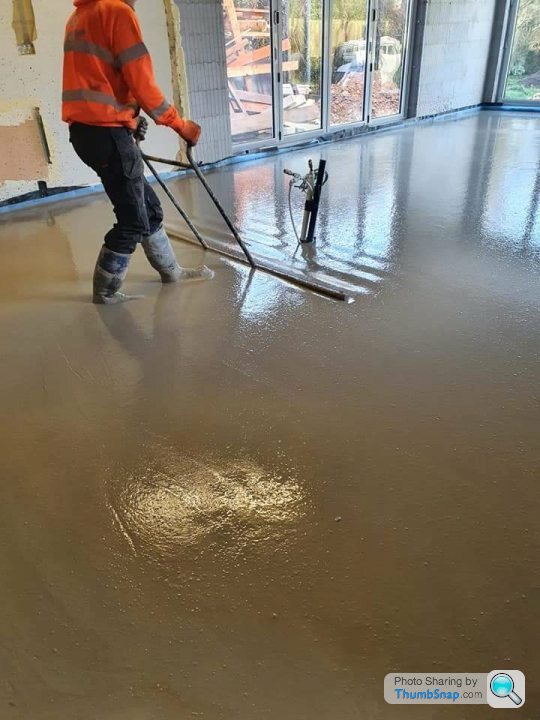
This type of screed dries in a third of the time of traditional screeds so I’ve managed to have the UFH on and tested. It’s now cooling again in preparation for tiling.
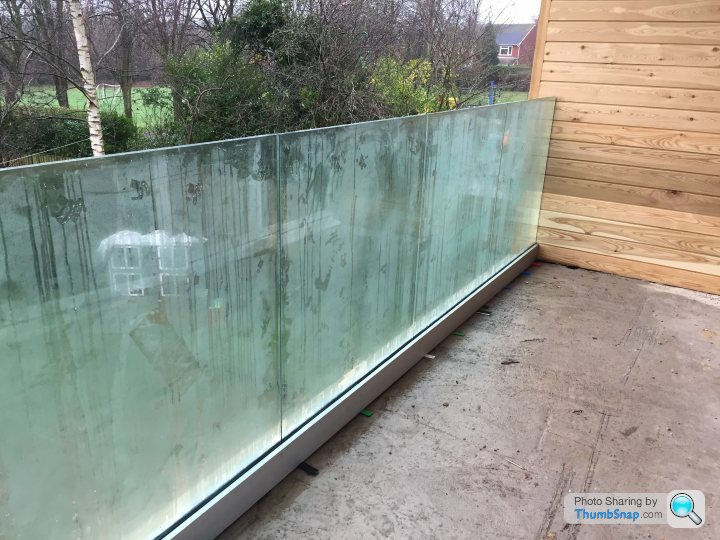
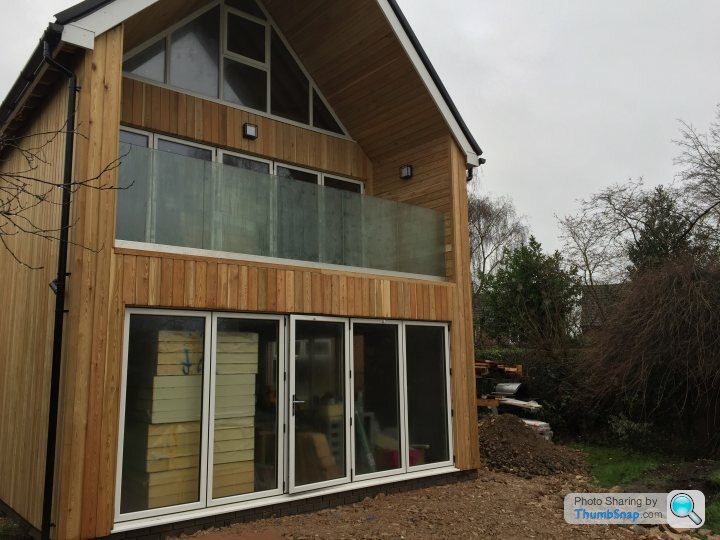
Although the panes of glass are under a metre wide and a metre and a bit high they weigh 70lgs each as they’re 21.5mm toughened laminated glass.
Then the insulation arrived:
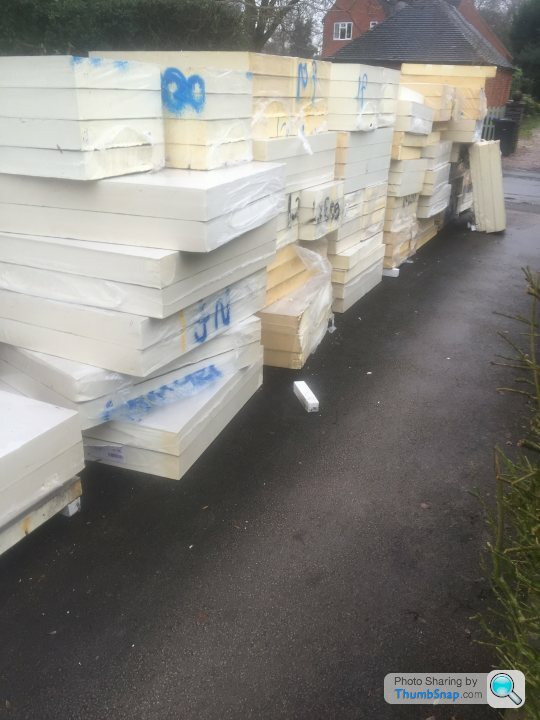
About a third of this is for the floor, the rest is for the loft.
Down and membrane on
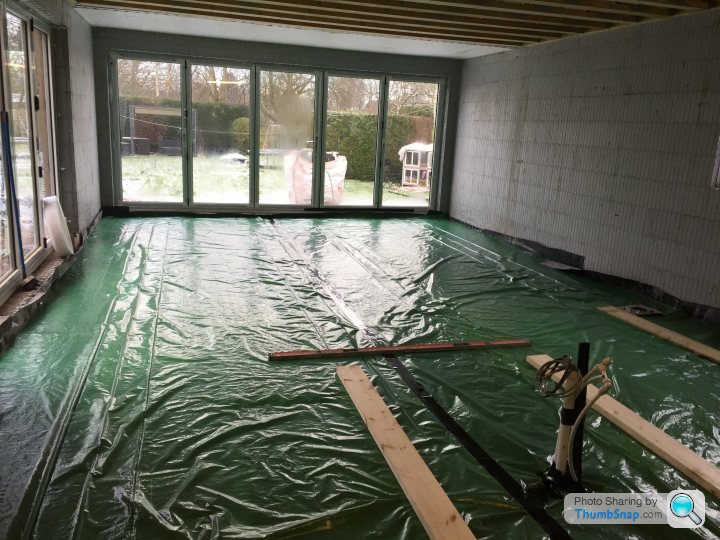
UFH pipes laid
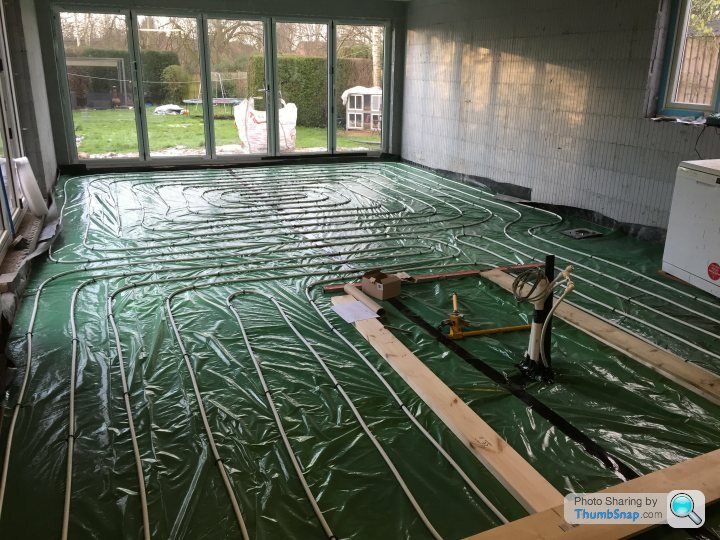
Screeding happened in early Jan and is one thing I didn’t do!
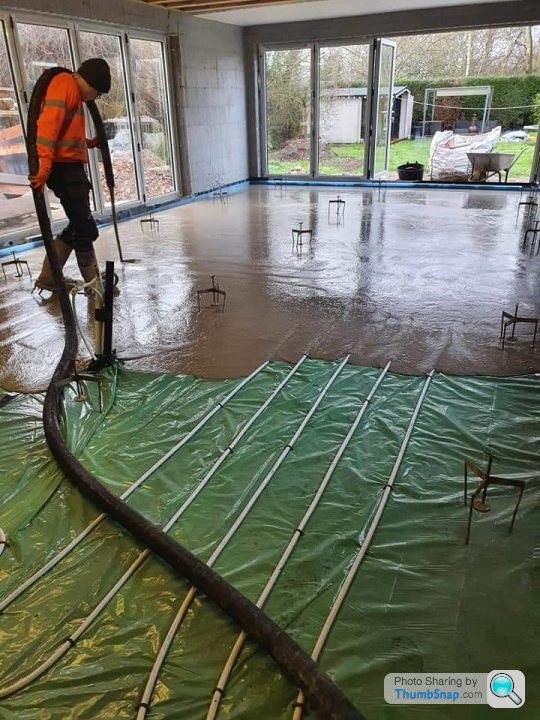
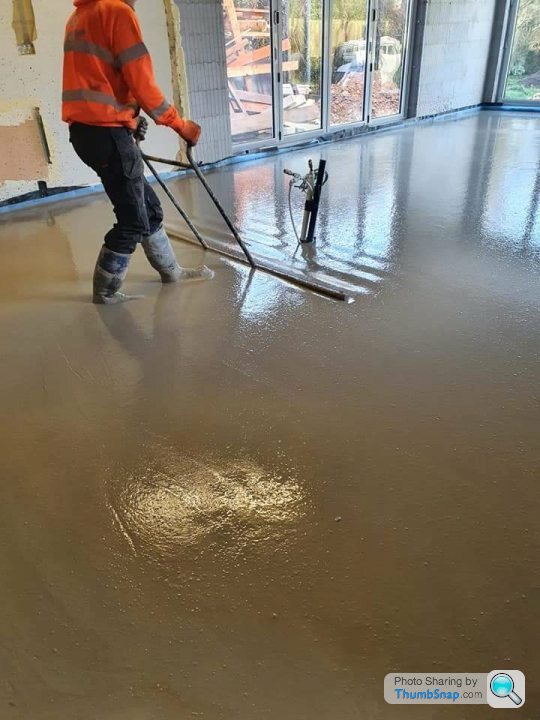
This type of screed dries in a third of the time of traditional screeds so I’ve managed to have the UFH on and tested. It’s now cooling again in preparation for tiling.
Gassing Station | Homes, Gardens and DIY | Top of Page | What's New | My Stuff