Pssst! Wanna buy a Mosquito bomber?
Discussion
For sale at approx. US $6.9 million, 1944 DEHAVILLAND MOSQUITO B IV, serial number DZ542...
https://silodrome.com/de-havilland-mosquito-projec...
https://www.platinumfighters.com/inventory/1944-de...
https://silodrome.com/de-havilland-mosquito-projec...
https://www.platinumfighters.com/inventory/1944-de...
Dr Jekyll said:
'Offering the aircraft as a complete ready to fly example' sounds like you get the finished aircraft for your 6.9 million.
I initially thought it was a project, but it does seem like they are offering the opportunity to buy the complete aircraft when it is finished. Wonder if there are time stipulations included as part of the contract.SpunkyGlory said:
Dr Jekyll said:
'Offering the aircraft as a complete ready to fly example' sounds like you get the finished aircraft for your 6.9 million.
I initially thought it was a project, but it does seem like they are offering the opportunity to buy the complete aircraft when it is finished. Wonder if there are time stipulations included as part of the contract.ianrb said:
SpunkyGlory said:
Dr Jekyll said:
'Offering the aircraft as a complete ready to fly example' sounds like you get the finished aircraft for your 6.9 million.
I initially thought it was a project, but it does seem like they are offering the opportunity to buy the complete aircraft when it is finished. Wonder if there are time stipulations included as part of the contract.Health and safety rules, political correctness gone mad, in my day etc, rant ramble mutter mutter.........
ianrb said:
SpunkyGlory said:
Dr Jekyll said:
'Offering the aircraft as a complete ready to fly example' sounds like you get the finished aircraft for your 6.9 million.
I initially thought it was a project, but it does seem like they are offering the opportunity to buy the complete aircraft when it is finished. Wonder if there are time stipulations included as part of the contract.Dr Jekyll said:
The first prototype was built in about 6 months!
Health and safety rules, political correctness gone mad, in my day etc, rant ramble mutter mutter.........
More to do with the number of people involved. Back then, they had armies of people working on these aircraft. Now you have a team of around 4 or 5. Also, modern built replacement parts often have to be hand made which takes time - and often a fair amount of research might be needed to find out exactly how some old comp[onents were made and what materials were used.Health and safety rules, political correctness gone mad, in my day etc, rant ramble mutter mutter.........
Putting together a warbird today is more of an archaeological project than a construction project - especially if it's an aircraft of which there are few (or possibly none) of to be able to copy and the original drawings, jigs and tooling long since lost.
Eric Mc said:
Dr Jekyll said:
The first prototype was built in about 6 months!
Health and safety rules, political correctness gone mad, in my day etc, rant ramble mutter mutter.........
More to do with the number of people involved. Back then, they had armies of people working on these aircraft. Now you have a team of around 4 or 5. Also, modern built replacement parts often have to be hand made which takes time - and often a fair amount of research might be neeed to find out exactly how some old comp[onents were made and what materials were used.Health and safety rules, political correctness gone mad, in my day etc, rant ramble mutter mutter.........
Putting together a warbird today is more of an archaeological project than a construction project - especially if it's an aircraft of which there are few (or possibly none) of to be able to copy and the original drawings, jigs and tooling long since lost.
The next two they did, the ex-IWM T.3 TV959 for Paul Allen, and the FB.6 PZ474 for Rod Lewis, but now owned by Charles Somers both took about 3.5/4 years to do, so 30 months to finish this B.IV is about given the work already done on it for Pathfinder Group before they switched projects.
Volare said:
I knew the mosquito was made out of wood but I didn't realise to what extent and how it actually looked, that is incredible, like a giant model.
I built a Tamiya 1:72 model a few years back that was meant to show the basic materials and wooden sheet orientations used in its construction: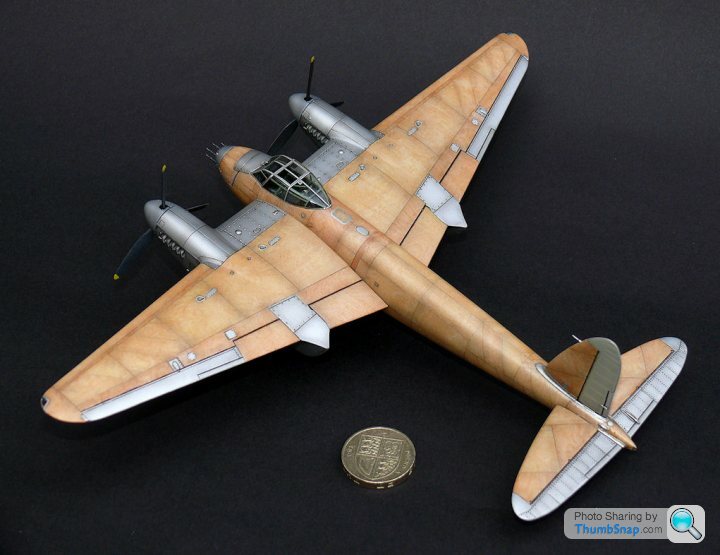
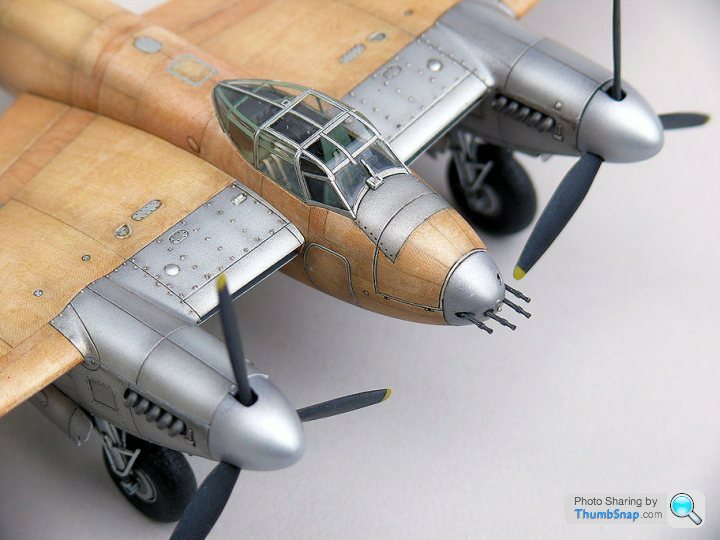
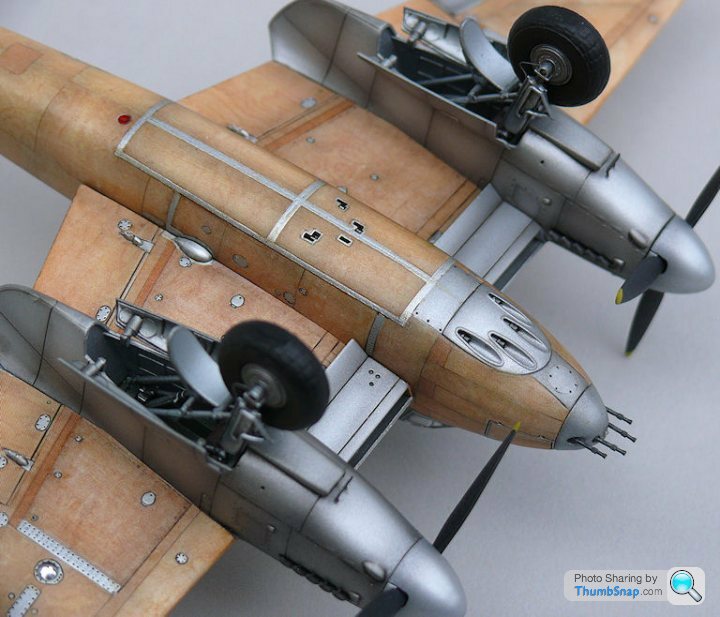
It's construction was even more 'special' in that the fuselage was built in 2 halves (vertical split line the whole length of the fuselage).
Each half was then fitted out with all the wiring, pipework and control cables before the 2 halves were glued together which made production easier and faster.
Each half was then fitted out with all the wiring, pipework and control cables before the 2 halves were glued together which made production easier and faster.
Steve_D said:
It's construction was even more 'special' in that the fuselage was built in 2 halves (vertical split line the whole length of the fuselage).
Each half was then fitted out with all the wiring, pipework and control cables before the 2 halves were glued together which made production easier and faster.
And the complete wing assembly was a single piece, which the then joined together fuselage assembly was lifted up and down onto the centre of the wing section.Each half was then fitted out with all the wiring, pipework and control cables before the 2 halves were glued together which made production easier and faster.
aeropilot said:
Avspecs went through all that with the first one they did, Jerry Yagan's KA114, which took 7 years to restore to airworthy.
The next two they did, the ex-IWM T.3 TV959 for Paul Allen, and the FB.6 PZ474 for Rod Lewis, but now owned by Charles Somers both took about 3.5/4 years to do, so 30 months to finish this B.IV is about given the work already done on it for Pathfinder Group before they switched projects.
Once you have one ground up restoration out of the way then the next get done quite a bit quicker - although you will always be hampered by the very small workforce available.The next two they did, the ex-IWM T.3 TV959 for Paul Allen, and the FB.6 PZ474 for Rod Lewis, but now owned by Charles Somers both took about 3.5/4 years to do, so 30 months to finish this B.IV is about given the work already done on it for Pathfinder Group before they switched projects.
Hawker Restorations is another company that have speeded up their work considerably since they started restoring Hawker Harts/Hinds almost 30 years ago. Once they had sorted out how the Hawker metal truss assembly system went togther, they were able to speed up their output considerable. It is the main reason why the number of airworthy Hurricanes has increased dramatically in the past couple of decades.
Steve_D said:
It's construction was even more 'special' in that the fuselage was built in 2 halves (vertical split line the whole length of the fuselage).
Each half was then fitted out with all the wiring, pipework and control cables before the 2 halves were glued together which made production easier and faster.
The Handley Page Hampden was built like that too.Each half was then fitted out with all the wiring, pipework and control cables before the 2 halves were glued together which made production easier and faster.
Eric Mc said:
More to do with the number of people involved. Back then, they had armies of people working on these aircraft. Now you have a team of around 4 or 5. Also, modern built replacement parts often have to be hand made which takes time - and often a fair amount of research might be needed to find out exactly how some old comp[onents were made and what materials were used.
Putting together a warbird today is more of an archaeological project than a construction project - especially if it's an aircraft of which there are few (or possibly none) of to be able to copy and the original drawings, jigs and tooling long since lost.
I’m guessing they’re built to a higher standard too?Putting together a warbird today is more of an archaeological project than a construction project - especially if it's an aircraft of which there are few (or possibly none) of to be able to copy and the original drawings, jigs and tooling long since lost.
Eric Mc said:
In most cases - yes.
They'll also have modern features added to ensure they comply with more modern safety and certification requirements.
Apart from some plug-in Nav aids, I can't think of too many additional modern safety and certification requirements on many of the more recent restored warbirds? Wartime stock config is usually the norm these days. Deviating too much from that usually creates more problems with CAA.They'll also have modern features added to ensure they comply with more modern safety and certification requirements.
It depends on the aircraft and the overseeing body who will grant the airworthiness.
I was reading an article in Aeroplane a few years ago about the restoration of an Ilyushin Il-2 Sturmovik in the US for a Russian customer. The US FAA insisted on a number of changes in order to grant them a licence. They were the first to restore a Sturmovik so they were the first modern group who encountered some of the production short-cuts that were taken during the war and which the FAA said were not acceptable for a current Certificate of Airworthiness. The main issues were exposed and rubbing control runs which needed to be sheathed to prevent wear.
For more common restorations - such as Spitfires or P-51s I expect that the certificating bodies are more comfortable with how these aircraft are put back together.
I was watching an episode of Warbird Restoration covering the one-off two seat Hurricane and they had to get a number of the modifications cleared before flight.
I was reading an article in Aeroplane a few years ago about the restoration of an Ilyushin Il-2 Sturmovik in the US for a Russian customer. The US FAA insisted on a number of changes in order to grant them a licence. They were the first to restore a Sturmovik so they were the first modern group who encountered some of the production short-cuts that were taken during the war and which the FAA said were not acceptable for a current Certificate of Airworthiness. The main issues were exposed and rubbing control runs which needed to be sheathed to prevent wear.
For more common restorations - such as Spitfires or P-51s I expect that the certificating bodies are more comfortable with how these aircraft are put back together.
I was watching an episode of Warbird Restoration covering the one-off two seat Hurricane and they had to get a number of the modifications cleared before flight.
Edited by Eric Mc on Thursday 27th October 10:58
Gassing Station | Boats, Planes & Trains | Top of Page | What's New | My Stuff