Tamiya Avante build thread
Discussion
... With some upgrades
YR titanium bolts
IMG_8149-Enhanced-NR by Chris, on Flickr
The sorting box that comes with the YR bolts only has 6 sections, which is pointless.
I used some double sides tape on a piece of card to sort them by size and keep them in place.
The Ti grub screws (x5) were purchased separately.
IMG_2830 by Chris, on Flickr
IMG_8159-Enhanced-NR by Chris, on Flickr
As many before me have done so, the motor pinion needs to be reversed on an aftermarket motor so that it is placed in the position specified by the instructions.
I've used a titanium grub screw, justifying its cost in my own mind on the basis that it's a rotating mass. The lighter the grub screw is , the less imbalanced it will be...
IMG_8166-Enhanced-NR by Chris, on Flickr
IMG_8168 by Chris, on Flickr
Part of Step 3 - seal the chassis edges with super glue. This is the before picture.
IMG_8171-Enhanced-NR by Chris, on Flickr
After sealing the chassis edges with super glue. I'm not going to lie, this was a pain in the butt. I managed to keep the glue where it was supposed to be, but even just tidying the edges up with a cotton bud and acetone took around 3 hours.
I washed the pieces in dish soap and used a carnauba wax afterwards
IMG_8174-Enhanced-NR by Chris, on Flickr
YR titanium bolts

The sorting box that comes with the YR bolts only has 6 sections, which is pointless.
I used some double sides tape on a piece of card to sort them by size and keep them in place.
The Ti grub screws (x5) were purchased separately.


As many before me have done so, the motor pinion needs to be reversed on an aftermarket motor so that it is placed in the position specified by the instructions.
I've used a titanium grub screw, justifying its cost in my own mind on the basis that it's a rotating mass. The lighter the grub screw is , the less imbalanced it will be...


Part of Step 3 - seal the chassis edges with super glue. This is the before picture.

After sealing the chassis edges with super glue. I'm not going to lie, this was a pain in the butt. I managed to keep the glue where it was supposed to be, but even just tidying the edges up with a cotton bud and acetone took around 3 hours.
I washed the pieces in dish soap and used a carnauba wax afterwards

Stupidly expensive bearings...
IMG_8186 by Chris, on Flickr
Rear gearbox casing mounted to the lower chassis, using ti hex bolts, not the nasty kit ones.
IMG_8183-Enhanced-NR by Chris, on Flickr
IMG_8179-Enhanced-NR by Chris, on Flickr
I did note that the pin hole through BA10 (not shown in the photo) wasn't perfectly centred.
IMG_8191-Enhanced-NR by Chris, on Flickr
Step 7
This highlighted an issue beyond the faffing I've been doing over the YR Ti screws and equating those to the Tamiya screws.
The Acer Racing bearings I have are for a 2011 Avante which uses the open diffs and the earlier type Steering set.
Meaning that where the 2011 uses a total of 4 850 type bearings, the black edition needs 16. 4 extra in the ball diffs and 8 in the racing steering set.
Making a decision on where to use the 4x850 (PB2) bearing was made easy in the end as I'd fitted 1 in Step 4 and meaning I had 3 left.
I could've fished it out and used the 4 4 on the ball diffs but I suspect I may end up changing them for the torque biasing (gear) diffs from a 2011 Avante.
And I can't use them in the steering set as I have 4 where 8 are needed.
So the remaining 3 are going in the driveline.
IMG_8203 by Chris, on Flickr
IMG_8212 by Chris, on Flickr
As part of Step 8 I used some kitchen scales to set up the ball diffs. The masking tape around the allen key is a reference point so that I could set the distance between the CL of the diff and the edge of the scale, giving a consistent leverage distance.
I used an arbitrary figure of 200g downward force on the scales when slowly rotating the crown wheel.
I did it by feel initially and 1 diff was 300g where the other produced 130g. I'm hoping this might help with the issues people have reported about these diff being difficult to set up.
IMG_8207 by Chris, on Flickr

Rear gearbox casing mounted to the lower chassis, using ti hex bolts, not the nasty kit ones.


I did note that the pin hole through BA10 (not shown in the photo) wasn't perfectly centred.

Step 7
This highlighted an issue beyond the faffing I've been doing over the YR Ti screws and equating those to the Tamiya screws.
The Acer Racing bearings I have are for a 2011 Avante which uses the open diffs and the earlier type Steering set.
Meaning that where the 2011 uses a total of 4 850 type bearings, the black edition needs 16. 4 extra in the ball diffs and 8 in the racing steering set.
Making a decision on where to use the 4x850 (PB2) bearing was made easy in the end as I'd fitted 1 in Step 4 and meaning I had 3 left.
I could've fished it out and used the 4 4 on the ball diffs but I suspect I may end up changing them for the torque biasing (gear) diffs from a 2011 Avante.
And I can't use them in the steering set as I have 4 where 8 are needed.
So the remaining 3 are going in the driveline.


As part of Step 8 I used some kitchen scales to set up the ball diffs. The masking tape around the allen key is a reference point so that I could set the distance between the CL of the diff and the edge of the scale, giving a consistent leverage distance.
I used an arbitrary figure of 200g downward force on the scales when slowly rotating the crown wheel.
I did it by feel initially and 1 diff was 300g where the other produced 130g. I'm hoping this might help with the issues people have reported about these diff being difficult to set up.

I've also sourced a set of gear diffs as spares from the original Avante.so I built them up. I have to admit, I think these are very nicely made and appear to be torque biasing diffs. I am tempted to use them, if only because I have a similar diff in my GTA.
IMG_8224-Enhanced-NR by Chris, on Flickr
IMG_8230-Enhanced-NR by Chris, on Flickr
IMG_8238-Enhanced-NR by Chris, on Flickr
IMG_8242-Enhanced-NR by Chris, on Flickr
Step 9 - Rear gearbox plate fitted from xtra speed. Seems to fit well and is nicely machined.
IMG_8251 by Chris, on Flickr




Step 9 - Rear gearbox plate fitted from xtra speed. Seems to fit well and is nicely machined.


And another alloy diff cover from xtra speed.

Step 11 calls for the construction of the rear traverse arms. These are constructed from a plastic end (E3) and a ball joint with a nut and a steel threaded bar.
I found an aluminium replacement for part E3 and made my own replacement for the steel tie rod from titanium bar. I also bought some titanium nuts in M3 and M4 sizes to replace the standard steel tamiya nuts.
I had to construct the standard part so that I could measure it and ensure that it was the correct length.
Step 11 calls for the construction of the rear traverse arms. These are constructed from a plastic end (E3) and a ball joint with a nut and a steel threaded bar.
I found an aluminium replacement for part E3 and made my own replacement for the steel tie rod from titanium bar. I also bought some titanium nuts in M3 and M4 sizes to replace the standard steel tamiya nuts.
I had to construct the standard part so that I could measure it and ensure that it was the correct length.

Cutting down the titanium rod to make replacements for part BB20 (4x26mm). By Hand. It took forever....

Completed parts fitted.

Step 12 - centre diff. The Black Edition part is shown in the back ground of the following pics. It's very basic or just a gear depending on the version you build.
The 2011 Avante (and the original I assume) uses a ball type centre diff. I identified the parts and I need to build one as a spare...
IMG_8315 by Chris, on Flickr
Centre diff
IMG_8316 by Chris, on Flickr
IMG_8324 by Chris, on Flickr
IMG_8337 by Chris, on Flickr
IMG_8345 by Chris, on Flickr
The 2011 Avante (and the original I assume) uses a ball type centre diff. I identified the parts and I need to build one as a spare...

Centre diff






The motor, with a 22t onion is ever so slightly touching the carbon chassis. I ordered some smaller gears to alleviate this issue.



This photo shows the 0.3mm of clearance around the end case of the motor with a 21t pinion fitted.

Motor refitted with a lovely strengthening plate. Note how the carbon has the same pitch and the weave is perfectly aligned with the OEM chassis. I was really pleased with this purchase.





Step 16 - Drive shafts built up with a titanium grub screw. I'm sure this will make all the difference.

Step 16 - Rear arms built up. I think the thread pitch is 0.7mm meaning that the 0.2mm shims equate to around 1/3 turn of adjustment. I'me tempted to revisit this as I think needed a 0.1mm shim to set it up properly.

Step 16 - driveshaft mounted in the hub carrier with bearings

Step 17 - Rear arm fitted. I'm dispointed with how much movement there is on the mounting points. I'm going to have to look at this and find a way to improve it.


After fitting the rear arms I noted the clearance (or lack of) between the motor and the rear ball joint. It's very tight and I'm concerned chassis flex may result in the ball joint binding up against the motor. I think a drop to a 20t motor pinion will solve this though.

Step 19 - Like Step 11, this requires the fabrication of titanium shafts (4x26mm) which I cut from a 100mm threaded bar. This was not easy.




Step 20 - Front bumper built up with the ARB.
IMG_8619 by Chris, on Flickr
IMG_8625 by Chris, on Flickr
IMG_8634-2 by Chris, on Flickr
Step 21 - The YR racing titanium screw pack does include enough 3x10mm (BA1 in this case) screws so I've had to use the tamiya screws for this step. I've ordered some more screws so these will be replaced later.
IMG_8637-2 by Chris, on Flickr
Step 22 - Again, because I'm using replacement alloy parts and a titanium stud (rather than the steel tamiya part) to make these arms up, I did have to make the standard part so that I knew how long to make it.
You can see that the gap in one arm is slightly different to the other but the C/L spacing of the ends is correct .
IMG_8640 by Chris, on Flickr



Step 21 - The YR racing titanium screw pack does include enough 3x10mm (BA1 in this case) screws so I've had to use the tamiya screws for this step. I've ordered some more screws so these will be replaced later.

Step 22 - Again, because I'm using replacement alloy parts and a titanium stud (rather than the steel tamiya part) to make these arms up, I did have to make the standard part so that I knew how long to make it.
You can see that the gap in one arm is slightly different to the other but the C/L spacing of the ends is correct .



Step 23 - Titanium nut used on the ball end. I'm not sure this is entirely necessary as whilst the instructions call for a nut to be used (and thread lock) with the plastic part, the YR alloy hub is threaded. Consequently, I think the addition of a nut is redundant.

Step 23 - Definitely the best individual part in the kit.

Step 23 - I'm stuck with using the standard tamiya cross head screws as they have a shoulder that makes them specific to this application. I can't see a stainless or titanium alternative being available? Part is BB5.


Step 25 - More link rods built up with titanium studs and nuts



Step 26 - Replacement alloy parts and bearings that are probably no different to the standard bearings.



Step 26 - There was actually a hop up available for the track rods - a titanium shaft with left and right hand threads to allow for adjustment without removal, as per the standard part....

'm not keen on using plastic parts as track rod ends, so I bought some alloy replacements.
Stupidly, I didn't recognise that they won't fit as they're all right hand thread. Additionally, the ball joints have some movement in them, meaning I think the plastic part is probably the best choice, unless anyone can suggest an alternative?


Step 26 - steering "rack" fitted. And it was at this point I realised there was a problem. It was binding.

Step 26 - I removed the steering and realised that the alloy replacement part lack a recess for an M3 nut.
This was causing the screw head to bind against the upper chassis deck.
I assumed that the nut is not needed as the alloy part is threaded instead and removed it.
This solved the problem, but I think the alloy part needs to be recessed slightly to replicate the plastic part as the bolt head appears to stand further proud on the alloy part than it would on the plastic part.





generationx said:
Wow, awesomely comprehensive build, and thread, of this Tamiya classic! Loving your work, watching with relish! What are your plans for the body, wheels and tyres? Will this be run?
Thanks 
I have 3 bodys for it so I'm thinking box art per the original 88 Avante - I have a genuine sticker set from a Re Release (ReRe) and box art Black Edition.
As for the 3rd, I have a second driver figure, Senna helmet decals and JPS livery stickers, so black and gold. I also have a load of LED's, resistors and Off road style lights.
My plan is alongside the lights, to fit a titanium skin to the bottom and from bumper. There's a problem with this in that the bumper is nylon and I'm not sure how to attach (bond) the titanium sheet to it.
I also have a mini servo which I'm going to tie into the fwd/rev signal to give some form of (simulated) DRS for the rear wing.
I've also got some black edition style cnc'd wheels:


As well as big bore spring / damper units as well as the aeration type.
However, it's been a long time since I've built something like this so I'm not sure when I'll run out of patience / ability to pull all of that together.
Edited by Zombie on Wednesday 10th January 23:41
AlfaCool said:
Blumin heck, they have come on a long way since i built the Brat in the 80s
It's a re-release of a 1988 model, so even this is a 35 year old design. It wasn't well regarded in its day either.There's some scans of a Tamiya guide book I have below that is from period. It's too big to fit on my scanner which is why the top/bottom is chopped off...




Wildfire said:
Great build! The Avante is my "grail" car, but I can never find the money to get one!
Thanks 
I picked up this one cheap as it was technically 2nd hand - NIB but the box had been opened.
Edited by Zombie on Wednesday 10th January 22:23
Edited by Zombie on Wednesday 10th January 23:42
Zombie said:
Thanks
. They were stupid expensive in the late 80's weren't they? I think the Thudershot I had as a kid retailed at £120 plus radio gear where as the Avante was £250 but you also needed a £250 CPR unit to run it as well as the radio gear.
I picked up this one cheap as it was technically 2nd hand - NIB but the box had been opened.
Build looks great plus the YR kit!
I picked up this one cheap as it was technically 2nd hand - NIB but the box had been opened.
Edited by Zombie on Wednesday 10th January 22:23
Edited by Zombie on Wednesday 10th January 23:42
I started a Manta Ray basher a while ago and committed to not buying another until I finished it. I had a Bear Hawk as a kid and now wish I hadn't trashed it. My mate had an Avante 2001, which was just the best thing I had ever seen.
I keep seeing the Avante and Black special come up on eBay and consider putting a bid in...
I wasn’t allowed a Rough Rider in circa 1980. Too expensive!! So when it was re-released about a decade ago (as the Buggy Champ) I threw EVERYTHING at it. Including a set of original decals, at ludicrous expense. (Tamiya wouldn’t pay the license fee to use the original stickers, so provided a set that looked similar, but were for imaginary parts suppliers rather than the genuine companies that appeared on the original model. And although reproduction original sticker sheets were available, the quality was poor, with fuzzy, out of register images!)
But I have one “observation”. Surely, using a grub screw of a material that’s significantly lighter than the material of the gear that it’s securing, will introduce a greater imbalance than a grub screw made of the same material? A significant issue in a part that must weigh at least a gram 😂
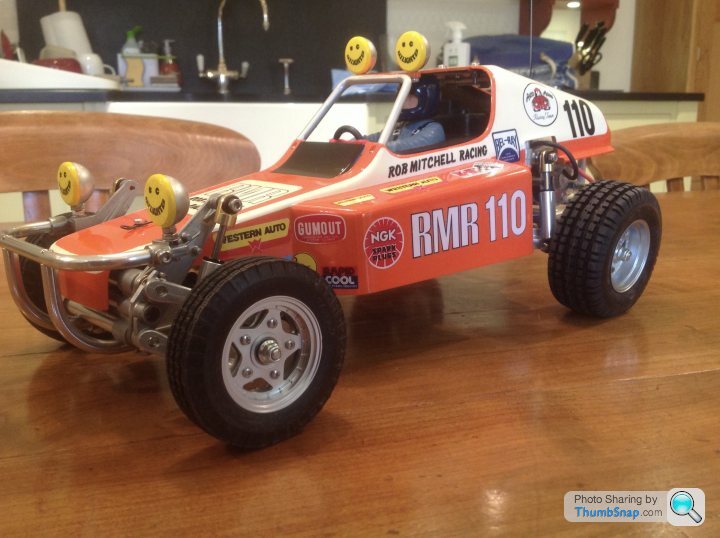
But I have one “observation”. Surely, using a grub screw of a material that’s significantly lighter than the material of the gear that it’s securing, will introduce a greater imbalance than a grub screw made of the same material? A significant issue in a part that must weigh at least a gram 😂
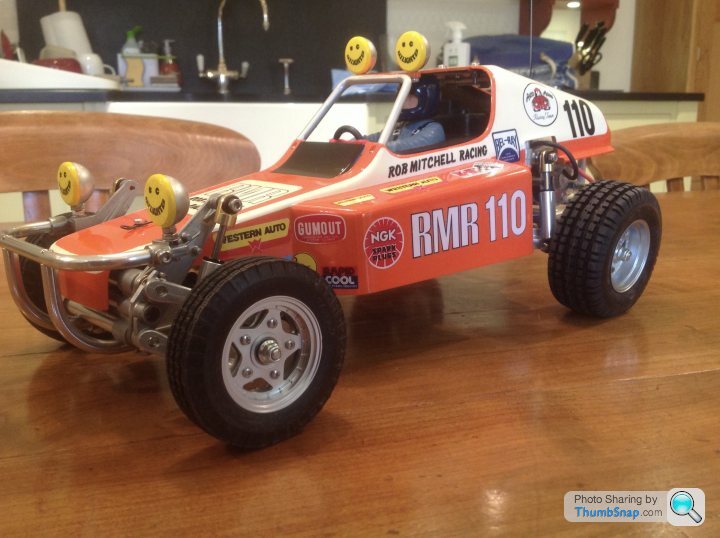
Gassing Station | Scale Models | Top of Page | What's New | My Stuff