Viking Longship from scratch
Discussion
So there I was in the supermarket the other day buying groceries. And I happened to see some lollipop sticks for sale.
A thought popped up from some undeveloped part of my brain - ‘I could build a Viking longship out of those’...
I should point out from the start that I have no knowledge or experience of model making, boat building or Viking longships. Or any tools or plans.
But how hard could it be?
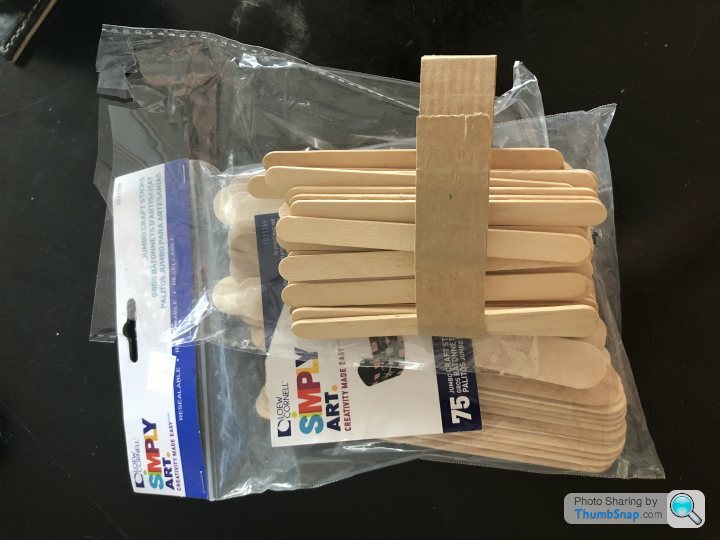
A thought popped up from some undeveloped part of my brain - ‘I could build a Viking longship out of those’...
I should point out from the start that I have no knowledge or experience of model making, boat building or Viking longships. Or any tools or plans.
But how hard could it be?
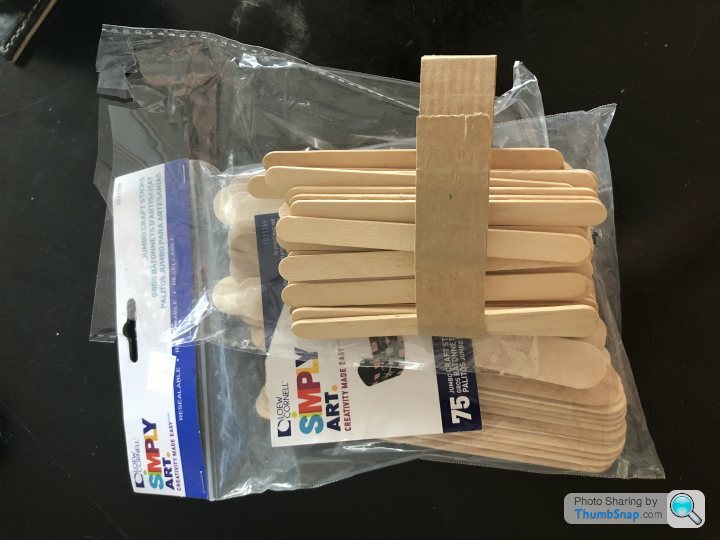
How hard can it be, right? After all they built those things from heavy tree trunks with axes. I was just going to use lollypop sticks which are a bit easier to manipulate.
From what I had read, they started building them from the keel up. Then they stuck some ribs to the keel to produce the basic hull shape, then they stuck the planks to the ribs.
So I would make some ribs and a keel.
From what I had read, they started building them from the keel up. Then they stuck some ribs to the keel to produce the basic hull shape, then they stuck the planks to the ribs.
So I would make some ribs and a keel.
Nice idea 
I was in Denmark 3 weeks ago looking at the real thing.
Apart from Copenhagen, my Danish (and extremely proud of his Viking ancestry) step-son took me to Roskilde to see the living ship Museum; they are actually building 'Viking' boats from scratch using copies of the original tools and skills handed down from those times.
https://www.vikingeskibsmuseet.dk/en/visit-the-mus...
There are chaps there who have been boat-building this way all their lives and hail from a long line of ancestors who were traditional boat-builders.
https://www.vikingeskibsmuseet.dk/en/professions/b...
I'm told one of the guys there uses no plans, no drawings at all. Expert and beautiful work.

I was in Denmark 3 weeks ago looking at the real thing.
Apart from Copenhagen, my Danish (and extremely proud of his Viking ancestry) step-son took me to Roskilde to see the living ship Museum; they are actually building 'Viking' boats from scratch using copies of the original tools and skills handed down from those times.
https://www.vikingeskibsmuseet.dk/en/visit-the-mus...
There are chaps there who have been boat-building this way all their lives and hail from a long line of ancestors who were traditional boat-builders.
https://www.vikingeskibsmuseet.dk/en/professions/b...
I'm told one of the guys there uses no plans, no drawings at all. Expert and beautiful work.
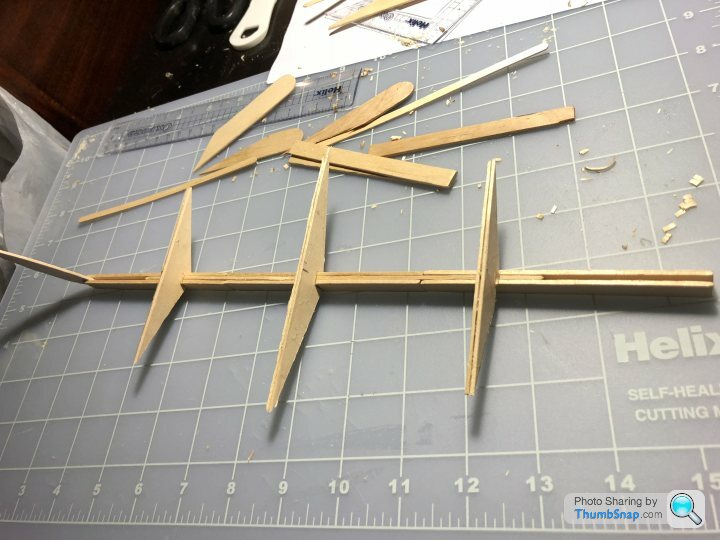
On fitting the ribs to the keel problem was immediately apparent. My ship was not so much long as round. It was more like a coracle.
I googled Viking longship length to beam ratios. Some might say I should have done this at the design stage. You would be right, but there was no design stage. According to Google, my ribs were too long even for the tubbiest Viking ship. I needed to weild the axe.
I am figuring out how to build this as I go along. One benefit of the project is that it has allowed me to buy some cool tools. I now own a Dremel. Yay!
Fitting the planks to the ribs proves be more difficult than I thought. The real ones were of course nailed. Mine is glued as it is to small for even the smallest nails.
I started by fitting a couple of planks to the keel. I believe this is the 'garbord'. I chose to fit them to a relatively straight part of the hull. The bit that is complicated is the next plank along - the one that fits to the stem or stern. This has to be very curved. In the real Longships pictured above, these planks impossibly curve in four directions at once. There was no way I was going to be able to replicate that. I settled for a straight stem rather than a flamboyantly curved on.
Real shipbuilders use a steam box to curve wood.
I tried to replicate that by using part of our vacuum cleaner hose stuck over the kettle spout, and putting the planks in that. That was not very good as the hose melted, the kitchen was full of steam and the effect on the plank's rigidity was minimal.
Then I read that wood could be bent in a microwave! So I soaked the planks in water, wrapped them it kitchen roll and blasted them in the microwave. This definitely had more effect than the kettle and was less hassle. To get the curve, it was necessary to microwave them, and then let them dry out while clamped into a curve shape.
Fitting the planks to the ribs proves be more difficult than I thought. The real ones were of course nailed. Mine is glued as it is to small for even the smallest nails.
I started by fitting a couple of planks to the keel. I believe this is the 'garbord'. I chose to fit them to a relatively straight part of the hull. The bit that is complicated is the next plank along - the one that fits to the stem or stern. This has to be very curved. In the real Longships pictured above, these planks impossibly curve in four directions at once. There was no way I was going to be able to replicate that. I settled for a straight stem rather than a flamboyantly curved on.
Real shipbuilders use a steam box to curve wood.
I tried to replicate that by using part of our vacuum cleaner hose stuck over the kettle spout, and putting the planks in that. That was not very good as the hose melted, the kitchen was full of steam and the effect on the plank's rigidity was minimal.
Then I read that wood could be bent in a microwave! So I soaked the planks in water, wrapped them it kitchen roll and blasted them in the microwave. This definitely had more effect than the kettle and was less hassle. To get the curve, it was necessary to microwave them, and then let them dry out while clamped into a curve shape.
This is more a research project into how to do it, rather than actually doing it. That is what I am telling myself so I don't feel too bad when it is crap.
Spent ages thinking about whether to join the planks 'carvel' style (planks meet edge on) or 'clinker / lapstrake' style (planks overlap). Carvel seems easier as the boards can fit flush to the ribs. But real Viking longships were clinker built. I decided to go clinker.

I am not doing the intricate clinker style ribs though.
Spent ages thinking about whether to join the planks 'carvel' style (planks meet edge on) or 'clinker / lapstrake' style (planks overlap). Carvel seems easier as the boards can fit flush to the ribs. But real Viking longships were clinker built. I decided to go clinker.

I am not doing the intricate clinker style ribs though.
dr_gn said:
I would imagine carvel would be easy for the straight bits, not so easy on the compound curved bits.
Clinker seems inherently stronger, as the average thickness of the hull is greater, each plank secures the one below it, and the plank to plank joint is much stronger. I read somewhere one that there could be a hydrodynamic advantage too - the uneven hull creates less drag. It seems to have so many advantages I wonder why it fell out of fashion?
Ayahuasca said:
dr_gn said:
I would imagine carvel would be easy for the straight bits, not so easy on the compound curved bits.
Clinker seems inherently stronger, as the average thickness of the hull is greater, each plank secures the one below it, and the plank to plank joint is much stronger. I read somewhere one that there could be a hydrodynamic advantage too - the uneven hull creates less drag. It seems to have so many advantages I wonder why it fell out of fashion?
Gassing Station | Scale Models | Top of Page | What's New | My Stuff