5-Axis machine making a V-8 aluminum block
Discussion
Talking of alloy block machinging, I walked into a specialist garage here and to my amazement found these alloy E type blocks on the shelf - three of them! They were made here in the same factory as the Honda 300cc-6 I wrote about in another thread. Amazing. Oh, that's a GT40 gearbox casing underneath too.


looks like that could be crosthwaite and gardiner, they can pretty much recreate anything.
think they build aluminium blocks for etypes.
even auto unions, as john gardiner told the germans after they suggested using modern v6 in the silver arrows recreation, just sign the cheque and tell us how big you want the swatstikas!!
a legend, fine Engineer, a great loss the vintage car world RIP.
think they build aluminium blocks for etypes.
even auto unions, as john gardiner told the germans after they suggested using modern v6 in the silver arrows recreation, just sign the cheque and tell us how big you want the swatstikas!!
a legend, fine Engineer, a great loss the vintage car world RIP.
I always find this amazing in the classic car world, I wouldn't have thought there was enough of a market for two manufacturers of alloy e type block, i here they're pretty pointless for road use, I also hear thy're not cheap either.
A similar thing with the Maserati 250f alot of which are in museum and about 40 of which have been built. But the historic scene is so big that between a number of specialists you could build an exact replica off the shelf!! many of which produce the same parts.
I just don't understand how these companies make money, when the market is so small and un-monopolised especially when the cost of replicating part can be astromonical.
Must be a labour of love
A similar thing with the Maserati 250f alot of which are in museum and about 40 of which have been built. But the historic scene is so big that between a number of specialists you could build an exact replica off the shelf!! many of which produce the same parts.
I just don't understand how these companies make money, when the market is so small and un-monopolised especially when the cost of replicating part can be astromonical.
Must be a labour of love
jagman21 said:
I
I just don't understand how these companies make money, when the market is so small and un-monopolised especially when the cost of replicating part can be astromonical.
Must be a labour of love
Try taking a look at the Crosthwaite & Gardiner catalogue the prices are as you same astronomical so I guess they don't need to sell too many. I guess they also save up orders till they have a few to make and then produce a small batch. I just don't understand how these companies make money, when the market is so small and un-monopolised especially when the cost of replicating part can be astromonical.
Must be a labour of love
You are probably right it's probably also a labour of love. Look at how many people lovingly recreate the most obscure bits for their cherished classic when buying a repro part would be easier, quicker and cheaper... but it wouldn't be so much fun.
I saw a full light weight wide angle head Crosthwaite & Gardiner engine sitting on a pallet recently. It looked really nice. I know the dry sump on it's worth about £4500 +VAT, I believe they sell cranks up to about 20K... but it did look nice.
The amazing people from crosthwaite and gardiner also build replica maserati birdcage engine, i've heard that a group of owners from the states decided to pool together to cover the tooling/production costs, this meant they could also race them with fia papers without the risk of blowing a valuable orginal engine. Glad they werent of the disposition of thinking, hell, stick a crate turbo-hemi in it. itll go like stink! like those vulgur hot rods and customs!!
Another curious by-product is that because of better modern casting and machining methods, they are more reliable and more powerful. A new Hall & Hall engine will have about 10hp on an orginal 250f engine.
Another curious by-product is that because of better modern casting and machining methods, they are more reliable and more powerful. A new Hall & Hall engine will have about 10hp on an orginal 250f engine.
An alloy block E type engine from Crosthwaite and Gardiner is £37,000 including the fuel injection at the moment. I am half way through building an FIA papered car and from experience can say just how expensive some of the parts cost. £3,000 for the steering rack alone for example, and £4,000 for the wheels without tyres. Then there's the individual suspension items........ However, when you look at the quality of some of the items you can understand just where the cost comes from so well made are they. Here's a photo of the steering rack for example, correct even down to the part numbers.
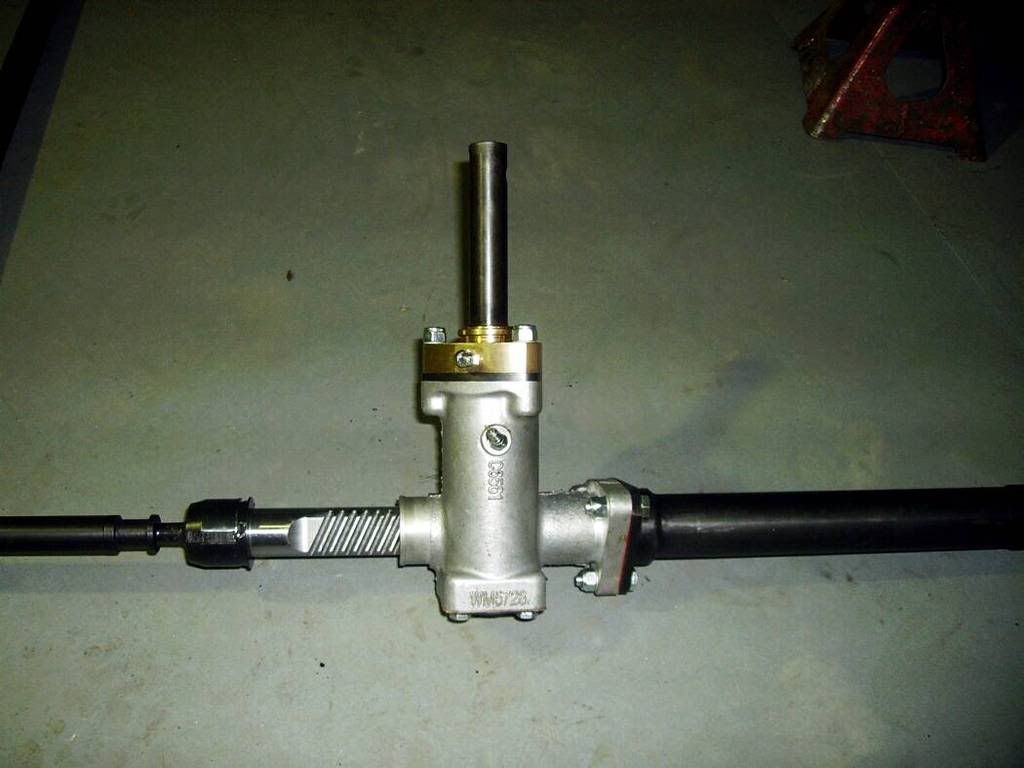
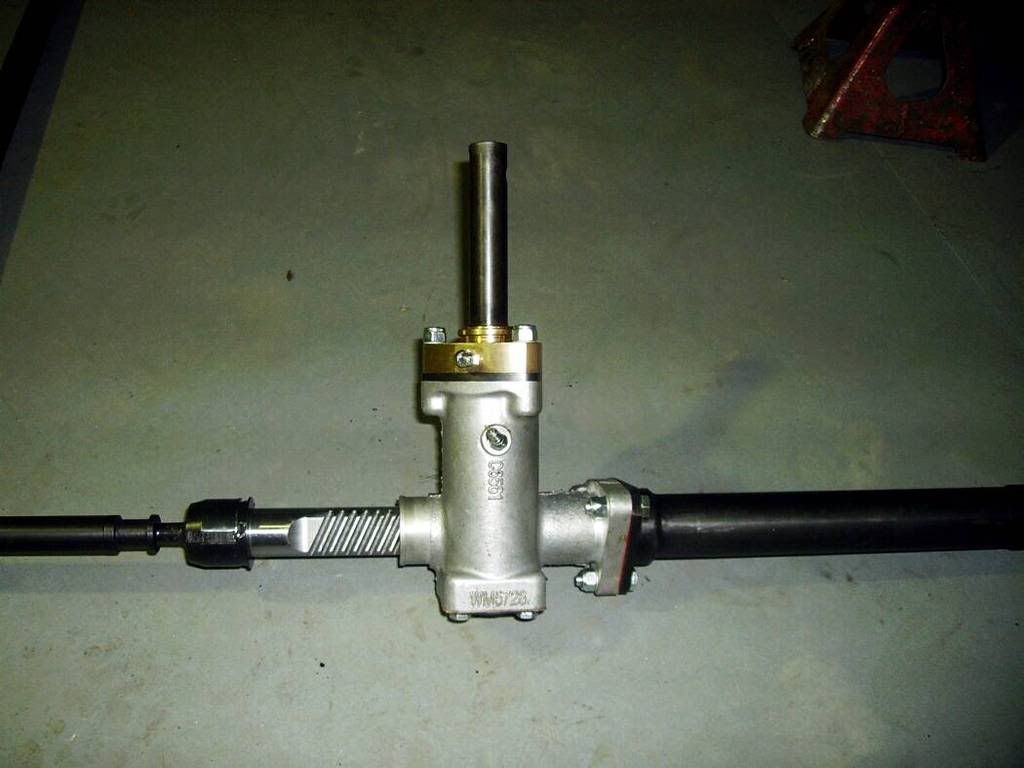
jagman21 said:
The amazing people from crosthwaite and gardiner also build replica maserati birdcage engine, i've heard that a group of owners from the states decided to pool together to cover the tooling/production costs, this meant they could also race them with fia papers without the risk of blowing a valuable orginal engine.
That was the reason behind the D-Type engine I saw, they had a scare racing with the original engine and decided as backup plan made sense.jagman21 said:
Another curious by-product is that because of better modern casting and machining methods, they are more reliable and more powerful. A new Hall & Hall engine will have about 10hp on an orginal 250f engine.
Do you read Octane?In last months edition (58) Tony Dron had a lovely analogy using 7 hammers to talk about originals, recreations, reproductions etc...
I thought it summed things up very well.
lowdrag said:
An alloy block E type engine from Crosthwaite and Gardiner is £37,000 including the fuel injection at the moment. I am half way through building an FIA papered car and from experience can say just how expensive some of the parts cost. £3,000 for the steering rack alone for example, and £4,000 for the wheels without tyres. Then there's the individual suspension items........ However, when you look at the quality of some of the items you can understand just where the cost comes from so well made are they. Here's a photo of the steering rack for example, correct even down to the part numbers.
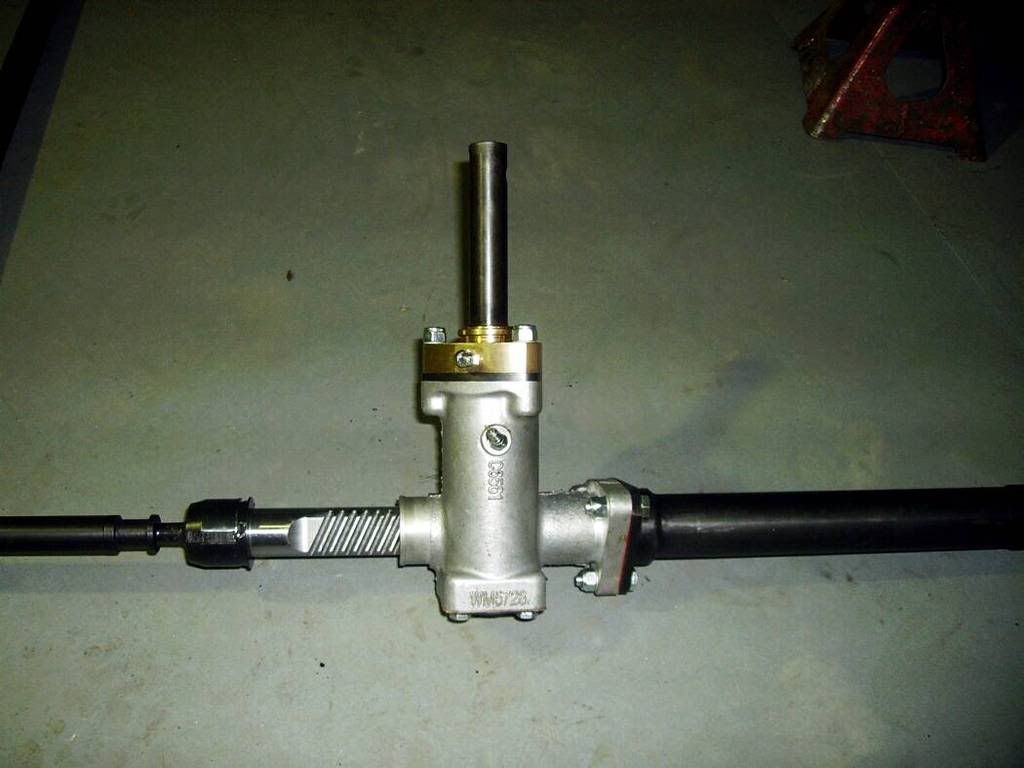
Considering some of the rubbish people blow thousands on to hang on their wall or put on a side board, that steering rack is a bargain, just as a pience of art. It looks beautiful.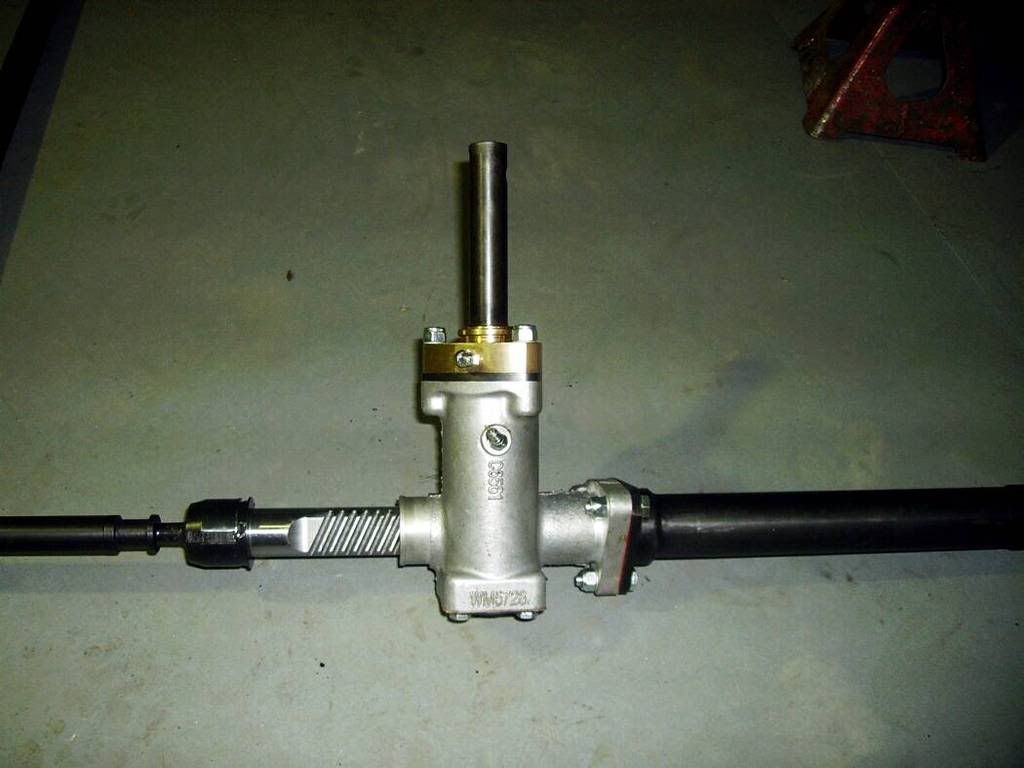
lowdrag,
Its a beautiful piece and clearly well engineered and machined.
But its not alot for £3000, a piece of cast metal which is then machined by an engineer.
Considering one of those crate yank engines could be bought for a similar price. Think of how many parts in a v8.
Suppose that may be a by-product of mass manufacturing.
Don't get me wrong i appreciate fine engineering, but i am feeling these niche parts seem to be very poor value for money. Maybe they can charge these prices because thier clients tend to be well-heeled and loyal?
Its a beautiful piece and clearly well engineered and machined.
But its not alot for £3000, a piece of cast metal which is then machined by an engineer.
Considering one of those crate yank engines could be bought for a similar price. Think of how many parts in a v8.
Suppose that may be a by-product of mass manufacturing.
Don't get me wrong i appreciate fine engineering, but i am feeling these niche parts seem to be very poor value for money. Maybe they can charge these prices because thier clients tend to be well-heeled and loyal?
I think that we all know that here in the UK we are ripped off. An american friend was converting his XJ6 to a Chevy small block and the complete engine arrived two days after placing the order at a price we would consider peanuts. On the other hand I've been to specialist machine shops in the USA and there isn't (excepting the exchange rate at the moment) a great deal of difference in pricing. The steering rack, the torsion bars and other parts are low volume high tensile specialist parts which wil inevitably cost more than a Chevy V8 engine in proportion since they make X zillion engines a year as opposed to a one off machining of a steering rack every now and again. With modern computer lathes I guess there is a rip off element but there again someone had to set up the programme in the first place and then specify the steel used and so on. In the final analysis I don't really have any choice anyway since really there are only a handful of engineering shops in the country I'd trust with such a job. My life will literally depend on their workmanship.
lowdrag said:
I think that we all know that here in the UK we are ripped off. An american friend was converting his XJ6 to a Chevy small block and the complete engine arrived two days after placing the order at a price we would consider peanuts. On the other hand I've been to specialist machine shops in the USA and there isn't (excepting the exchange rate at the moment) a great deal of difference in pricing. The steering rack, the torsion bars and other parts are low volume high tensile specialist parts which wil inevitably cost more than a Chevy V8 engine in proportion since they make X zillion engines a year as opposed to a one off machining of a steering rack every now and again. With modern computer lathes I guess there is a rip off element but there again someone had to set up the programme in the first place and then specify the steel used and so on. In the final analysis I don't really have any choice anyway since really there are only a handful of engineering shops in the country I'd trust with such a job. My life will literally depend on their workmanship.
I guess in you case that as you want FIA papers for the car, you've got to be able to persuade their rep that the parts are as close to original as makes no difference.So it's not just yourself you've got to convince.
I think the issue here is that, are these specialist workshops holding owners to ransom?
I can fully understand that the production cost are going to wiegh heavily on the overall cost due to low volume, but even though it may require skill and craftsmenship(who aren't paid loads anyway) the process of replication of most parts isnt that complicated.
It would be interesting if someone from a specialised engineering firm such as c&g could comment.
But in my opinion the area could do with more competition to see how far prices could go down? This would improve quality and reduce price.
Actually, if that happened we'd get sub-standard parts being flooded in from china/india,leave it as it is, our engineers are the best, let them eat cake.
I can fully understand that the production cost are going to wiegh heavily on the overall cost due to low volume, but even though it may require skill and craftsmenship(who aren't paid loads anyway) the process of replication of most parts isnt that complicated.
It would be interesting if someone from a specialised engineering firm such as c&g could comment.
But in my opinion the area could do with more competition to see how far prices could go down? This would improve quality and reduce price.
Actually, if that happened we'd get sub-standard parts being flooded in from china/india,leave it as it is, our engineers are the best, let them eat cake.
Therein lies the rub. If you look at most replicas of C types for example, those produced by Realm or Proteus, their basis is a Mk 2 rear axle (4 ins wider than a C type) and Mk 2 running gear. To make a real C type the engineering company probably make about 5 steering racks a year, if that. No one is going to enter into competition at these figures since it just isn't worth it. My Lynx D type uses E type running gear, but to build a real D type copy, with full chassis and so on, is completely different and commensurately dearer. I found an RS Panels D type body shell here and sold it for £80,000 unpainted, dearer than the cost at the time of my Lynx D. The suspension of a D type front and back is £15,000 and the brakes many thousands too. No one builds FIA papered copies much so one off parts such as these are dear. Yes, perhaps we are being held to ransome somewhat but it's Hobsons choice - buy it or don't. I'm just glad someone does make them, that's all!
hmmm.. its got me thinking, looking back at how this thread started, could original parts be scanned digitally then a pattern machined, sent to a foundry to be cast, surely this would reduce the need for much of the craftmenship involved in pattern making process? and improve speed and vitally reduce cost.
They may even improve accuracy of replica parts, it could also mean that the information sent digitally to places such as eastern europe, where skills are plentiful and jobs now short. This is what the kirkham replica cobra has done (built in an old Mig jet fighter factory!!)
I don't know could this be done, profitably on a small scale?
They may even improve accuracy of replica parts, it could also mean that the information sent digitally to places such as eastern europe, where skills are plentiful and jobs now short. This is what the kirkham replica cobra has done (built in an old Mig jet fighter factory!!)
I don't know could this be done, profitably on a small scale?
This trick is probably old-hat by now, but a few years ago, the must-see demo at the shows for CNC machines was a lathe that makes a hexagon from a spinning bar. You see them load piece of circular bar stock, the chuck spins for a few seconds...once the the chuck's stopped, you notice a hexagon bar sitting there.
With regards to the likes of C+G's prices, one should always bear in mind that there are numerous 'hidden costs'. How many man-hours went into generating the blueprints for the recreation? I doubt they have access to original blueprints, and 'reverse-engineering' is massively time-consuming. How much work was put into figuring out the precise alloy / steel composition and then locating stock? How many prototypes were scrapped before a version that could be sold to the general public came about? Considering the low volumes involved, how much expensive kit has to be paid for and maintained, that might only get used occasionally, yet costs the earth?
It's also worth bearing in mind that the 'boutique' firms such as C+G live by their aftercare and support - a very different business model to that of the parts that are made in volume for mass consumption.
A starting point for a decent 5-axis machine is around £250K btw.
With regards to the likes of C+G's prices, one should always bear in mind that there are numerous 'hidden costs'. How many man-hours went into generating the blueprints for the recreation? I doubt they have access to original blueprints, and 'reverse-engineering' is massively time-consuming. How much work was put into figuring out the precise alloy / steel composition and then locating stock? How many prototypes were scrapped before a version that could be sold to the general public came about? Considering the low volumes involved, how much expensive kit has to be paid for and maintained, that might only get used occasionally, yet costs the earth?
It's also worth bearing in mind that the 'boutique' firms such as C+G live by their aftercare and support - a very different business model to that of the parts that are made in volume for mass consumption.
A starting point for a decent 5-axis machine is around £250K btw.
jagman21 said:
hmmm.. its got me thinking, looking back at how this thread started, could original parts be scanned digitally then a pattern machined, sent to a foundry to be cast, surely this would reduce the need for much of the craftmenship involved in pattern making process? and improve speed and vitally reduce cost.
They may even improve accuracy of replica parts, it could also mean that the information sent digitally to places such as eastern europe, where skills are plentiful and jobs now short. This is what the kirkham replica cobra has done (built in an old Mig jet fighter factory!!)
I don't know could this be done, profitably on a small scale?
Some high-tech machine shops have a robotic laser that maps out the profile of a part for the purpose of generating a blueprint. What you're talking about is perfectly feasible in terms of machining a lump of metal to resemble the original part. As I suggested before though, there are plenty of hidden criteria to be aware of - precise metal composition being one that's utterly crucial (once you know the composition, finding the metal stock can be easier said than done).They may even improve accuracy of replica parts, it could also mean that the information sent digitally to places such as eastern europe, where skills are plentiful and jobs now short. This is what the kirkham replica cobra has done (built in an old Mig jet fighter factory!!)
I don't know could this be done, profitably on a small scale?
When you bear in mind the general costs and overheads involved in maintaining the kind of machining facility needed to replicate such parts, the model only becomes workable if there’s considerable demand – unless you have the pockets of Bernie Ecclestone that is.
Replacement blocks, for example, may well be feasible to produce for popular classics such as MGs and Beetles - whether blocks are worth making commercially for Bugattis and Maseratis is a different issue...
Edited by flat16 on Saturday 29th March 21:31
The other major potential cost is in borrowing the original part in the first place. How did C&G know what they needed to do to make Lowdrag's new steering rack. Well I image they had to borrow a real C-Type and persuade the owner that they could take the whole thing to pieces and decide which pieces they wanted to go into business recreating. Now there there are not many C-types for them to copy. Many have had rather eventful lives. Many have probably been somewhat messed around with. So they'd likely need to find a really good example. They probably want to at least look at several. In the case of C&G they probably are experts on many of the cars they work with. Someone new trying to get into the field would probably need expert advise on what looks right etc...
Now the owners of these sample cars may have several reasons for getting involved with the project. In the case of the recent recreation of pre-war silver arrows, it was the factory that was paying for everything largely because they wanted to show the cars in use without risking the originals. So they would have supplied the original cars (and probably around the clock security) so they got the copies.
In most cases I'd guess the owners of the originals largely view their toys as investments. OK investments that are fun to play with but investments none the less. Borrowing the cars might well involve money as well as a massive level of trust. There might also be ongoing deals where by each copy is paid for. I don't know, I'm not lucky enough to have the sort of car they'd want to copy. But I somehow doubt that a new startup unknown company can just come along and borrow 2.5Million quids worth of car and just strip it down and make patterns for any part they fancy.
That all quite apart from the fact that people capable of making these things deserve to make a decent living.
Now the owners of these sample cars may have several reasons for getting involved with the project. In the case of the recent recreation of pre-war silver arrows, it was the factory that was paying for everything largely because they wanted to show the cars in use without risking the originals. So they would have supplied the original cars (and probably around the clock security) so they got the copies.
In most cases I'd guess the owners of the originals largely view their toys as investments. OK investments that are fun to play with but investments none the less. Borrowing the cars might well involve money as well as a massive level of trust. There might also be ongoing deals where by each copy is paid for. I don't know, I'm not lucky enough to have the sort of car they'd want to copy. But I somehow doubt that a new startup unknown company can just come along and borrow 2.5Million quids worth of car and just strip it down and make patterns for any part they fancy.
That all quite apart from the fact that people capable of making these things deserve to make a decent living.
Gassing Station | Classic Cars and Yesterday's Heroes | Top of Page | What's New | My Stuff