Treating surface rust on my van
Discussion
My Transit showed feint rust patches along the cills and wing edges last year so i sanded, primed and sprayed.
This year they are all back, so I guess I need to go back further to bare metal instead of trusting rustoleum.
No probs - I have all the tools.
My question is, to take it back to metal do I use a wire wheel/brush, or a flapper disk? I have a feeling the flapper might be too much?
Any other tips? other than sanding priming, painting.? Is there something else I should spray under the primer.
This is no beauty contest, its my working van - I just want to stop the rot before it gets worse.
I did try youtube but as always , the videos seem to be more about the "presenters" than the actual job.

This year they are all back, so I guess I need to go back further to bare metal instead of trusting rustoleum.
No probs - I have all the tools.
My question is, to take it back to metal do I use a wire wheel/brush, or a flapper disk? I have a feeling the flapper might be too much?
Any other tips? other than sanding priming, painting.? Is there something else I should spray under the primer.
This is no beauty contest, its my working van - I just want to stop the rot before it gets worse.
I did try youtube but as always , the videos seem to be more about the "presenters" than the actual job.

I like Bilt Hamber products so I'd try their Hydrate 80 once you're back to bare metal.
Use regular sanding discs, no need for flapper discs and wire brushes are not the right tool for bodywork.
May have to treat the inside of the panel too. I'd again use Hydrate 80 and then Dynax UB or S50 for cavities.
Got to weigh up whether it's worth it though, if it's as visible as it is then it's likely to be much worse than it first appears.
Use regular sanding discs, no need for flapper discs and wire brushes are not the right tool for bodywork.
May have to treat the inside of the panel too. I'd again use Hydrate 80 and then Dynax UB or S50 for cavities.
Got to weigh up whether it's worth it though, if it's as visible as it is then it's likely to be much worse than it first appears.
Brillaint - thanks for that.
Yeah - she was a bargain at £2k a few years ago and I use her a lot (mostly lugging my dirtbike about but also collecting materials for my business) - 160k miles and runs sweetly. I keep on top of the spannering but bodywork is fairly new to me. I can weld too (not great, but I can!).
She failed her MOT last year on corroded brake line bits - was inexpensive to get it sorted, and I replaced a leaf that had snapped! Other than that she normally gets minimal to no advisories. So worth persevering - I can't justify a new van.
Yeah - she was a bargain at £2k a few years ago and I use her a lot (mostly lugging my dirtbike about but also collecting materials for my business) - 160k miles and runs sweetly. I keep on top of the spannering but bodywork is fairly new to me. I can weld too (not great, but I can!).
She failed her MOT last year on corroded brake line bits - was inexpensive to get it sorted, and I replaced a leaf that had snapped! Other than that she normally gets minimal to no advisories. So worth persevering - I can't justify a new van.
That's coming through from the inside - you're wasting your time by sanding it back from the outside
You could try cleaning out the crap and mud inside the arches and treat that side, which might slow it down a bit, but in reality you'll be chasing that for ever until you get it cut out and repaired properly
You could try cleaning out the crap and mud inside the arches and treat that side, which might slow it down a bit, but in reality you'll be chasing that for ever until you get it cut out and repaired properly
I'd more inclined to look at a more permanent solution.
I've seen more powerful acidic rust removal type products rather than converters which never work.
https://www.rust.co.uk/product/cat/diy-vehicle-res...
I've seen more powerful acidic rust removal type products rather than converters which never work.
https://www.rust.co.uk/product/cat/diy-vehicle-res...
Edited by Belle427 on Saturday 8th April 07:17
Common issue with Transits & I've seen loads with corroded front & rear arches.
Issue with rear arches is the lip where the inner & outer skins join. Penetration of the join results in the lip blowing apart & damp on the inside of the panels will help perforation.
Not helped by the lack of decent anti corrosion protection when they were built.
I would suggest using a fine wire brush on a drill.
NOT the coarse twisted wire type more usually used on an angle grinder
Go carefully without excessive pressure & take your time.
This will remove paint & surface rust without removing good metal as sanding discs will do.
In areas where the metal is badly corroded you may find there's not a lot left - the rust circles in your pic are common for perforation of the panel - & you'll have holes but at least you will have a better idea of the extent of the damage.
If the panel is perforated & you intend to try & repair it you will need to treat both sides or it will simply reappear.
The proper solution is to cut out the affected metal to decent metal & weld new metal in.
It's a good idea when washing the vehicle to thoroughly do the arch lips as they usually have a good build up of road dirt with plenty of added salt during the winter for good measure.
This then sits, stays damp, & accelerates corrosion.
I usually put on a leather welding glove & use my fingers together with the hosepipe to clean it off & it's surprising just how quickly it builds up again.
Issue with rear arches is the lip where the inner & outer skins join. Penetration of the join results in the lip blowing apart & damp on the inside of the panels will help perforation.
Not helped by the lack of decent anti corrosion protection when they were built.
I would suggest using a fine wire brush on a drill.
NOT the coarse twisted wire type more usually used on an angle grinder
Go carefully without excessive pressure & take your time.
This will remove paint & surface rust without removing good metal as sanding discs will do.
In areas where the metal is badly corroded you may find there's not a lot left - the rust circles in your pic are common for perforation of the panel - & you'll have holes but at least you will have a better idea of the extent of the damage.
If the panel is perforated & you intend to try & repair it you will need to treat both sides or it will simply reappear.
The proper solution is to cut out the affected metal to decent metal & weld new metal in.
It's a good idea when washing the vehicle to thoroughly do the arch lips as they usually have a good build up of road dirt with plenty of added salt during the winter for good measure.
This then sits, stays damp, & accelerates corrosion.
I usually put on a leather welding glove & use my fingers together with the hosepipe to clean it off & it's surprising just how quickly it builds up again.
I have a 2010 Fiesta which I bought as an MOT fail due to corrosion at the rear of the sills. The rust was just starting to get to the wheel arch lip too. Once I had welded up the holes, I sprayed half a litre of dinitrol into each of the sills and between the skins of the the rear wheel arches. I used a compressor for this and sprayed enough that I could see it starting to weep out all along the seam at the base of the sill. That was last summer and none of the rust has got any worse now, at the end of a salty NE Scotland winter.
.....so my advice is treat the surface rust as you were planning with wire brush attachment, then bilt-hamber deox gel to get into the pits, zinc primer and then top coat. To stop it coming back, very liberally apply a thin oily wax to the cavities and inner wheel arches and use a compressor to do this as it absolutely blasts the stuff in.
Cheers all - as soon as we get a dry day im going to start removing paint (and perhaps metal) and see how far its gone. I've got myself the anti rust product linked above, loads of sand paper and wet and dry, primer, paint. I also have several tins of waxoyl let over from being a TVR owner :-)
I'll post up some pics when I've investigated further!
Much appreciated.
I'll post up some pics when I've investigated further!
Much appreciated.
So , here we are. Surface rust... my arse :-)
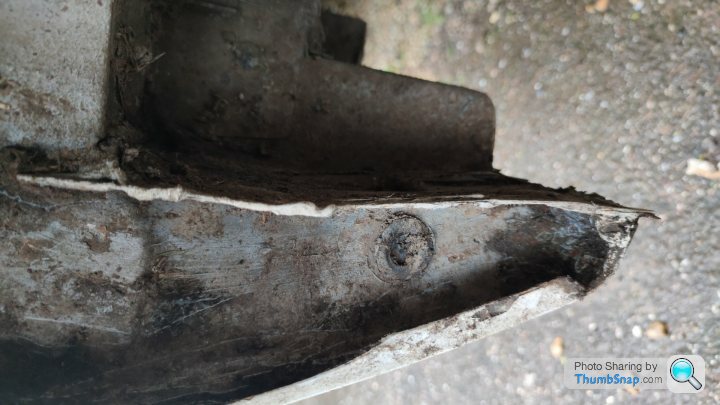
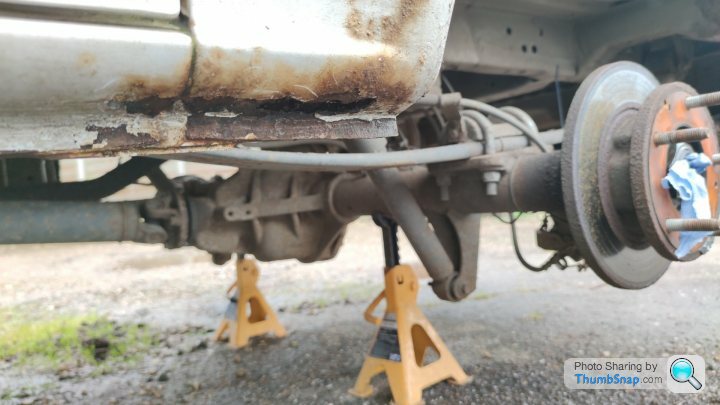
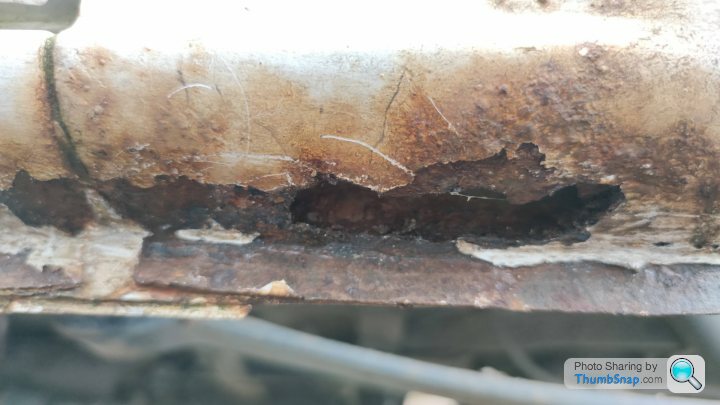
So I'm thinking along these lines.... bear in mind it's a 160k+van than cost me £2k and I've had for years, although , it IS useful to me, and it will cost a LOT mroe to replace. It's a MWB MHT too, so very useful - I can stand up in it. So whilst I want to prolong its life, there are limits as to how far I'll go, AND I really dont' care how it looks on the whole. Its a van.
I'm thinking either
a) take all the rust back to metal with my wire bruches etc, treat the cavity with bilt-hamber deox then line it with waxoil, then plug the hole with filler.
b) cut a small piece of steel sheet out, bent a lip on it, curve it, and then cut out the rust and weld the repair in. I'm a novice welder, though have a mig with a proper argo mix bottle, and have been taught how to weld thin steel (did a bike silencer).
Option b has to be better, but I'm on the fence regarding whether I have the skills to pull the welding off (what thicknness steel is usually used for the repair patch? new donar wings are over £100 which seems an expensive way to cut out quite a small part)
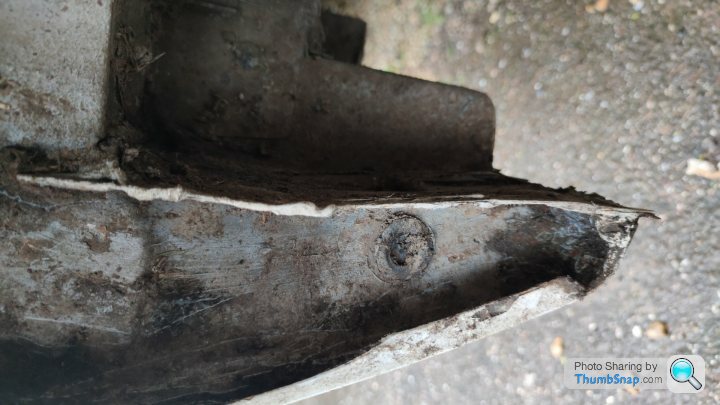
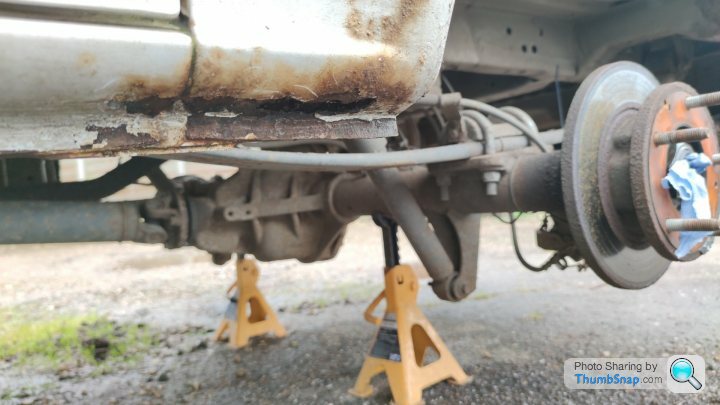
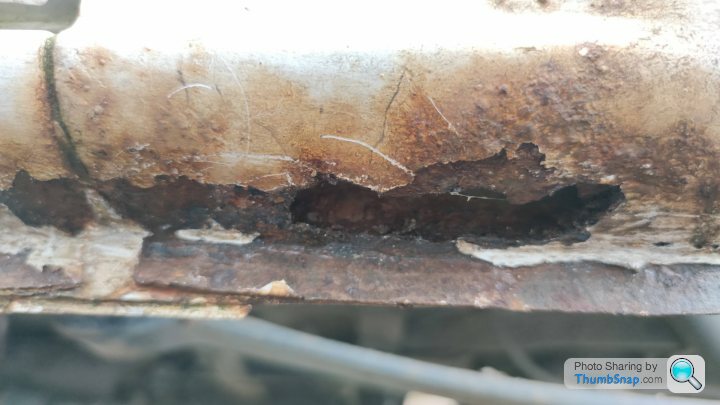
So I'm thinking along these lines.... bear in mind it's a 160k+van than cost me £2k and I've had for years, although , it IS useful to me, and it will cost a LOT mroe to replace. It's a MWB MHT too, so very useful - I can stand up in it. So whilst I want to prolong its life, there are limits as to how far I'll go, AND I really dont' care how it looks on the whole. Its a van.
I'm thinking either
a) take all the rust back to metal with my wire bruches etc, treat the cavity with bilt-hamber deox then line it with waxoil, then plug the hole with filler.
b) cut a small piece of steel sheet out, bent a lip on it, curve it, and then cut out the rust and weld the repair in. I'm a novice welder, though have a mig with a proper argo mix bottle, and have been taught how to weld thin steel (did a bike silencer).
Option b has to be better, but I'm on the fence regarding whether I have the skills to pull the welding off (what thicknness steel is usually used for the repair patch? new donar wings are over £100 which seems an expensive way to cut out quite a small part)
Yeah - but ----- I really like taking things on and learning. I give my R8 to a garage. The Van and my Yeti -that's my domain :-)
It's not about money. Well, not reasonably. Hence the half shafts are out - I'm replacing the discs and pads. And that nice new leaft spring? I put that in. Now that was fun and taught me why I have two bottle jacks and a trolley jack!
It's not about money. Well, not reasonably. Hence the half shafts are out - I'm replacing the discs and pads. And that nice new leaft spring? I put that in. Now that was fun and taught me why I have two bottle jacks and a trolley jack!
Go for option b.
You've got the welder.
Interesting link & will likely make the job easier.
Get some steel sheet from a local motor factors.
1mm cutting discs for the angle grinder
I also use the small reinforced discs on a dremel for areas I can't get a full size angle grinder into. Don't force them - esp no side pressure - & they are actually very good.
You've got the welder.
Interesting link & will likely make the job easier.
Get some steel sheet from a local motor factors.
1mm cutting discs for the angle grinder
I also use the small reinforced discs on a dremel for areas I can't get a full size angle grinder into. Don't force them - esp no side pressure - & they are actually very good.
I'll get the machines on it tomorrow and see what I've got to patch up. I have the fibre cutters for my drummer. Also 1mm slitters for my angle grinder.
The ebay wing part. It's galv so I'd have to grind the galv off all round the edges I believe? I've got some 1mm plain steel sheet. Let's see what cleaning and cutting reveals....
Watched a couple of yt tutorials and I feel more confident, especially seeing stitch welding between tacks. Reminded me how I did similar on the thin silencer. Moving the pool to fill holes. Well, expanding the pool with small touches.
The ebay wing part. It's galv so I'd have to grind the galv off all round the edges I believe? I've got some 1mm plain steel sheet. Let's see what cleaning and cutting reveals....
Watched a couple of yt tutorials and I feel more confident, especially seeing stitch welding between tacks. Reminded me how I did similar on the thin silencer. Moving the pool to fill holes. Well, expanding the pool with small touches.
OK, had a play - some more questions.
1) When I put the wire tools to the rust and it won't go back to smooth steel, always knobbly/shiney rust - that means there is rust behind right? So no point treating - it HAS to go - correct?
So my idea of a small patch where the hole is is kind out dead, and I'm better off buying the panel patch and replacing the whole area?
No probs. so I drill out the flange welds which are now visible (and plug weld them when fitting the new panel), and peel and cut off the outer skin. Question - where do I cut back to? The left line in the last photo below. I'm not sure whats at that far left "edge". Obv welding along a hidden line is preferable - just no idea really. Or simply slit a line straight down a cm in or so?
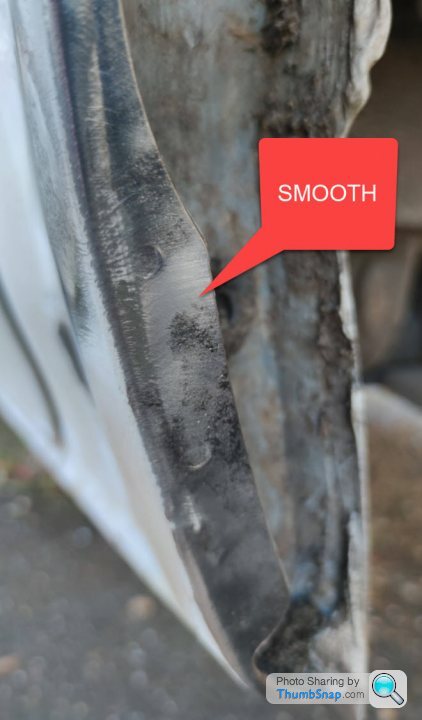
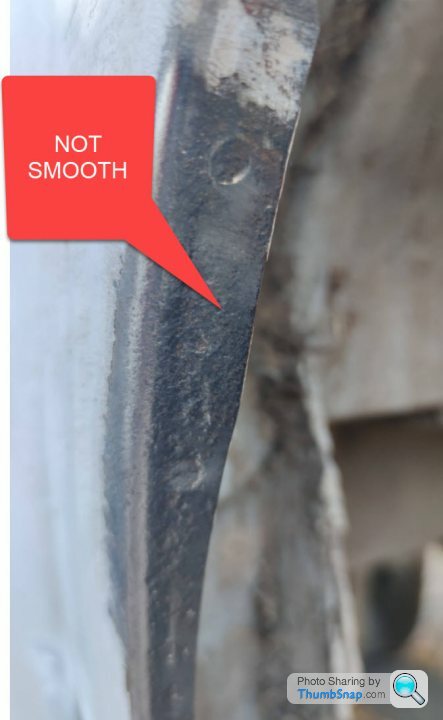
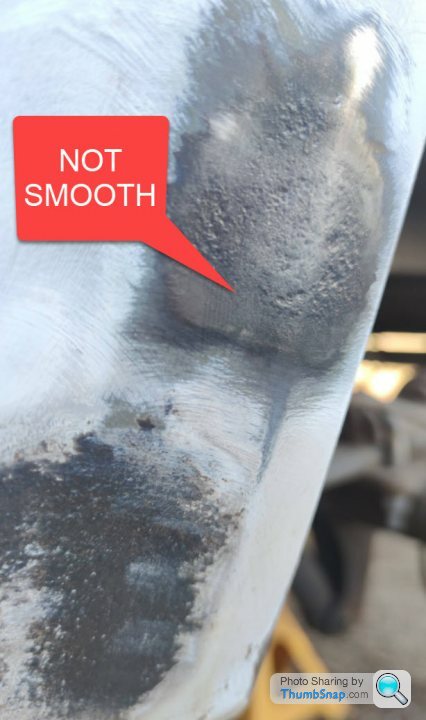
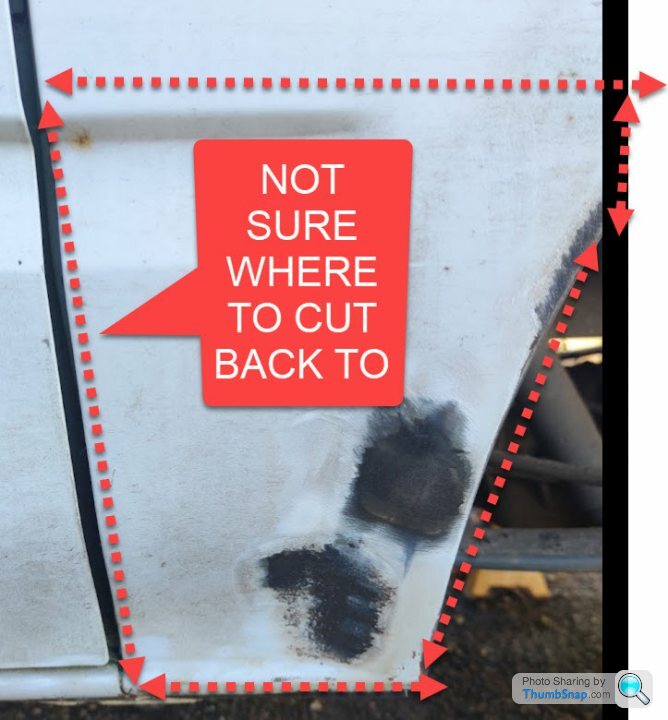
1) When I put the wire tools to the rust and it won't go back to smooth steel, always knobbly/shiney rust - that means there is rust behind right? So no point treating - it HAS to go - correct?
So my idea of a small patch where the hole is is kind out dead, and I'm better off buying the panel patch and replacing the whole area?
No probs. so I drill out the flange welds which are now visible (and plug weld them when fitting the new panel), and peel and cut off the outer skin. Question - where do I cut back to? The left line in the last photo below. I'm not sure whats at that far left "edge". Obv welding along a hidden line is preferable - just no idea really. Or simply slit a line straight down a cm in or so?
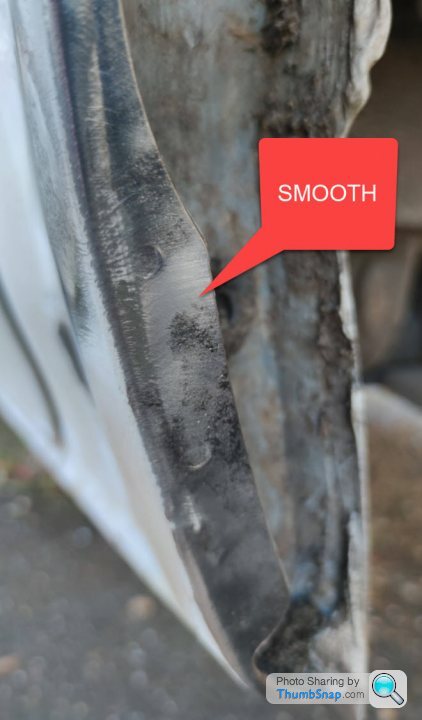
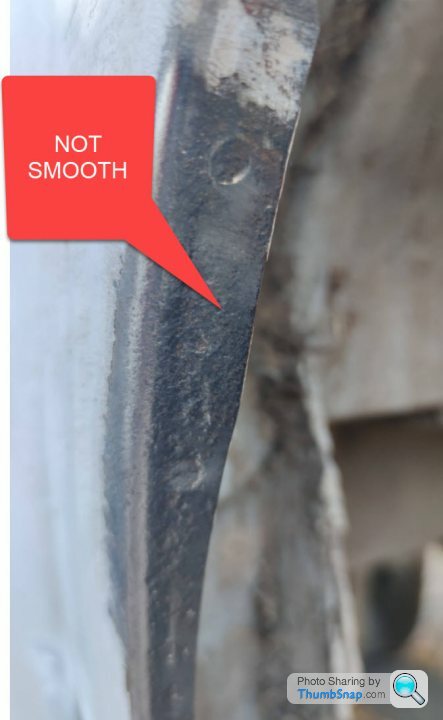
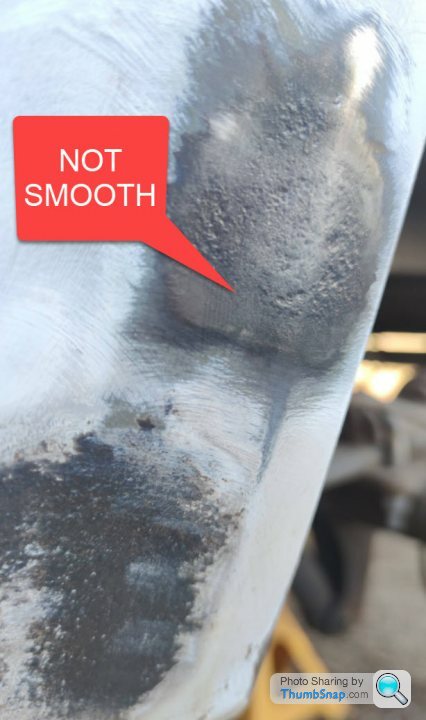
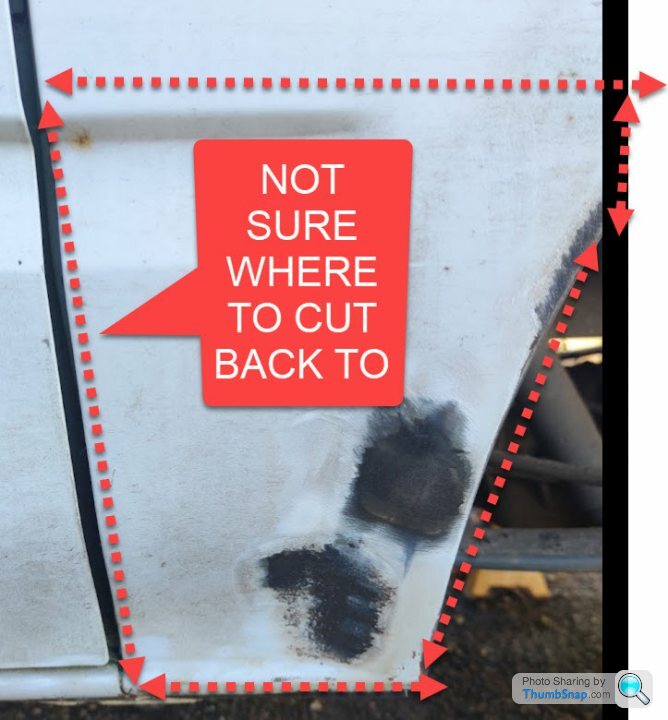
When the repair panel arrives compare it to the area it will be replacing & cut the body & new panel accordingly to deal with the problem areas.
You don't weld it over the existing area, cut the old panel. When I worked in a motor factor in the 70s we sold various 'cover sills' which were just welded on over the rusty remnants. Unsurprisingly these then rusted through from the inside.
Repair panels save an awful lot of faffing around trying to fabricate stuff & when I need to weld on my Classic Range Rover I see if YRM or Froggatts Easy on have a suitable item.
When you drill the spot welds & remove the old you'll probably be getting rid of a lot of those pitted areas in the arch.
These are designed to remove spot welds. Cuts the old panel & leaves a disc of the old panel & spot weld which you then grind flat.
Full set: www.machinemart.co.uk/p/clarke-cht685-spot-weld-cu...
But also available from ebay etc.
A weld through primer isn't a bad idea. I use U-Pol's Weld#2 zinc. https://u-pol.com/wp-content/uploads/UP0789-TDS.pd...
If the pitting is on the surface with no perforation then treat & paint.
If it's perforated then you'll need to remove & weld in new steel.
ETA I'm probably stating the obvious but to avoid any confusion you don't need to use the whole repair panel. Little point in removing sound original bodywork.
You don't weld it over the existing area, cut the old panel. When I worked in a motor factor in the 70s we sold various 'cover sills' which were just welded on over the rusty remnants. Unsurprisingly these then rusted through from the inside.
Repair panels save an awful lot of faffing around trying to fabricate stuff & when I need to weld on my Classic Range Rover I see if YRM or Froggatts Easy on have a suitable item.
When you drill the spot welds & remove the old you'll probably be getting rid of a lot of those pitted areas in the arch.
These are designed to remove spot welds. Cuts the old panel & leaves a disc of the old panel & spot weld which you then grind flat.
Full set: www.machinemart.co.uk/p/clarke-cht685-spot-weld-cu...
But also available from ebay etc.
A weld through primer isn't a bad idea. I use U-Pol's Weld#2 zinc. https://u-pol.com/wp-content/uploads/UP0789-TDS.pd...
If the pitting is on the surface with no perforation then treat & paint.
If it's perforated then you'll need to remove & weld in new steel.
ETA I'm probably stating the obvious but to avoid any confusion you don't need to use the whole repair panel. Little point in removing sound original bodywork.
Edited by paintman on Saturday 15th April 12:20
Gassing Station | Bodywork & Detailing | Top of Page | What's New | My Stuff