Electronic PAS Pump PWM Control - Anyone Done It?
Discussion
If anyone has fitted an electric PAS pump to a TVR and controlled the speed of it how did you do it? Also, was it worth doing in terms of steering feel & driving experience?
Due to ongoing faff with Parts for TVRs (who are actually being very helpful) getting a woodruff key and PAS adaptor that fits the latest batch of new AJP V8 water/Oil/PAS pump shafts they've had made is proving somewhat difficult. Over the weekend I fitted what seems to be the go to electric replacement pump from a Saxo and it works fine. The logic being I wont have to worry about any of the mechanical PAS stuff and I cna get the engine back in my Cerb. I began wondering about using an Arduino or similar to provide speed sensitive PWM control. I'm happy with the Arduino coding but where I could do with some advice is what to use to control the power supply to a motor that draws maybe 50A. Simply a MOSFET? Or is a driver required to get a useful PWM frequency, in which case has someone found a nice PCB with a driver IC that will cope?
Due to ongoing faff with Parts for TVRs (who are actually being very helpful) getting a woodruff key and PAS adaptor that fits the latest batch of new AJP V8 water/Oil/PAS pump shafts they've had made is proving somewhat difficult. Over the weekend I fitted what seems to be the go to electric replacement pump from a Saxo and it works fine. The logic being I wont have to worry about any of the mechanical PAS stuff and I cna get the engine back in my Cerb. I began wondering about using an Arduino or similar to provide speed sensitive PWM control. I'm happy with the Arduino coding but where I could do with some advice is what to use to control the power supply to a motor that draws maybe 50A. Simply a MOSFET? Or is a driver required to get a useful PWM frequency, in which case has someone found a nice PCB with a driver IC that will cope?
Penelope Stopit said:
Isn't pressure control simpler?
PAS hydraulics are "open spool" systems, there is no pressure until it's required, the fluid simply goes round in circles doing nothing. As the driver puts in a handwheel torque, the shuttle valve in the rack opens as the transfer torsion bar deflects, to allow flow to enter one side or other of the racks piston (depending if your are turning left or right obvs). The more the driver torques the handwheel, the more the torsion bvar deflects, the more fluid can enter the piston. Now, because the flow can no longer go "straight through" the spool valve without restriction and back to the pump inlet, the flow is effectively increasingly deadheaded against the rack piston, so pressure builds at this point as flow drops. At some point the rack moves, the piston moves and the torsion bar in the spool valve gets untwisted a bit, shutting down the flow the piston.By finely tuning all the responses of the various mechanical and hydraulic virtual springs and dampers a natural feeling of assistance can be generated.
[img] https://bullittautomotive.com/wp-content/uploads/2...
Before we moved to purely electrical assistance (an electric motor driving a lead screw that pushes the rack left or right) we used Electro Hydrualic PAS (EHPAS). Here an electric motor replaced the engine driven power steering pump. This reduced parasitic energy wasted in fluid friction when we didn't need it, which in a road car, is actually most of the time. In EHPAS, the speed of the pump is mapped to respond to two primary control functions:
Road speed: The faster the car is going, the less the pumps speed, because at high speeds you don't move the steering wheels through sharp angles (mostly), ie you never need to do a 3 point turn at ninety....
Handwheel velocity: The faster the driver is turning the handwheel, the faster the pump spins, because the pump must always move MORE oil than the racks piston is consuming
The classic TRW EHPAS pumps have mostly been hacked years ago now. It did it back in 2013 for one project:
https://www.youtube.com/watch?v=tFH1XMlEj4Y
hoofa said:
A better solution is to fit a epas in the steering column and dump the hydraulics , can be made speed sensitive and can be programmed to yourrequired assistance level 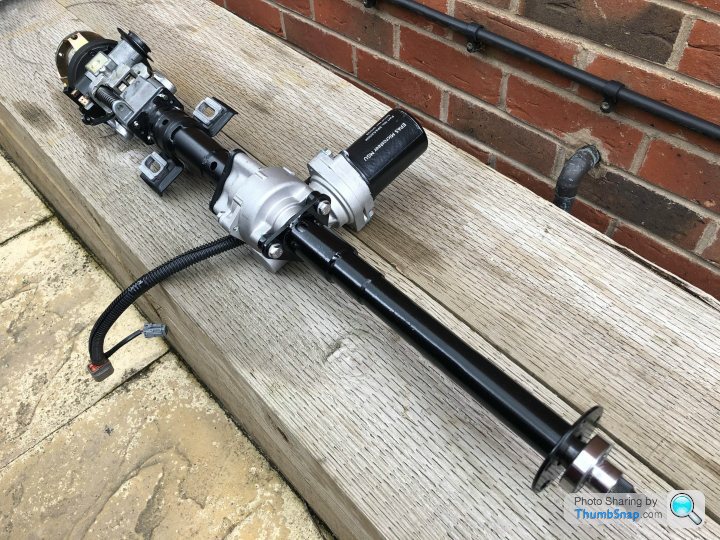
This old Corsa electric column works but it's pretty poor imo because of two factors: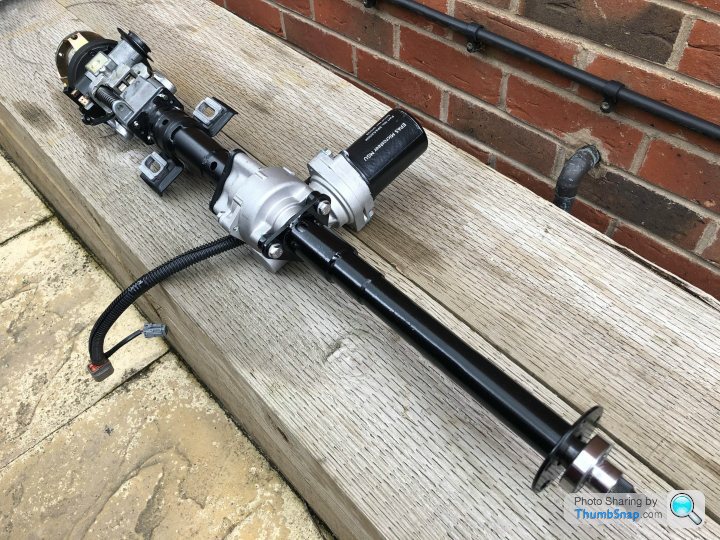
1) the column has a high inertia low torque motor geared to it, meaning that motor's inertia is coupled to the column. This really ruins any steering feel you might have had. It can also cause really werid juddery operation where the inertia of the motor gets coupled into that of the rack and road wheels, especially as you are reacting the roadwheel lateral loads into the scuttle area of a car made out of glue and string and never designed to take torsional loads at this point. Hit a ot hole, bump or other road irregularity under significant load and the oscillations that can occur can be frightening.....
2) it's a really low power solution, designed for a small shopping car with small tyres and about 4 turns lock to lock. On a performance car the motor is nowhere near powerful enough to keep up with assistance during high handwheel rates, ie when you really need it to save the day, that dreaded feeling old crappy cars used to have as you'd flail at the wheel in a tankslapper and as the tail went left then right the handwheel loads would climb, and climb and climb, until you were so far 'behind the car' you may have well not as bothered to try to catch it and just nailed the brakes immediately instead....
So yes, it will help with reducing parking handwheel peak loads, but that's about it. It's NOT (imo) a performance car assistance system really
CerbWill said:
Penelope Stopit said:
Isn't pressure control simpler?
No idea. How might I achieve that?I have ideas. Most of them are crap, so please elaborate if there's a better way of doing things.
https://continentalhydraulics.com/products/valves/...
https://continentalhydraulics.com/product_items/ve...
https://continentalhydraulics.com/download/601/ver...
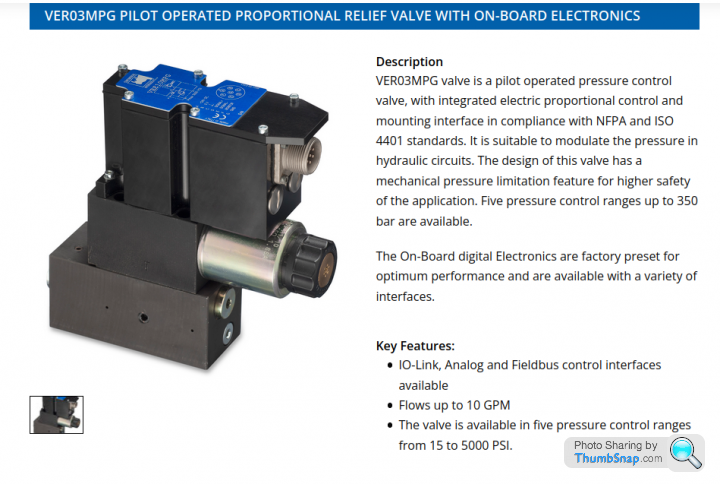
hoofa said:
It’s not a corsa column, dce electronics epas and epas controller , seams fine to me and better feel than the pas rack. Each to their own I guess
DCE took the TRW corsa D EPAS column and got a copy made, that's what there system is!Edited by hoofa on Monday 10th January 22:23
Edited by hoofa on Monday 10th January 22:24
Penelope Stopit said:
CerbWill said:
Penelope Stopit said:
Isn't pressure control simpler?
No idea. How might I achieve that?I have ideas. Most of them are crap, so please elaborate if there's a better way of doing things.
https://continentalhydraulics.com/products/valves/...
https://continentalhydraulics.com/product_items/ve...
https://continentalhydraulics.com/download/601/ver...
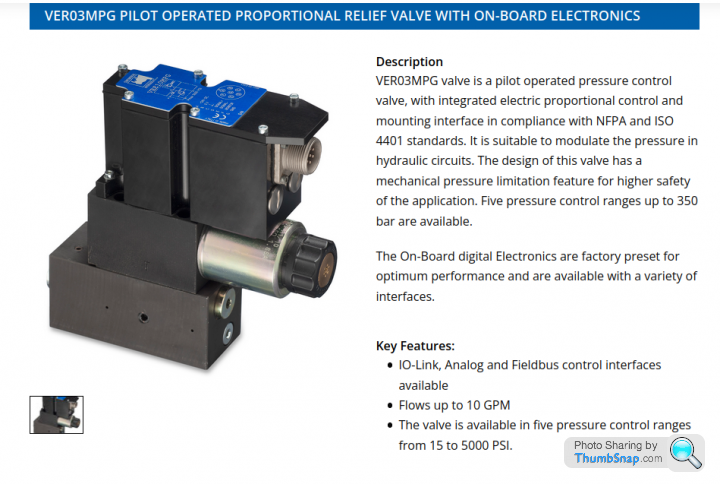
CerbWill said:
If anyone has fitted an electric PAS pump to a TVR and controlled the speed of it how did you do it? Also, was it worth doing in terms of steering feel & driving experience?
Due to ongoing faff with Parts for TVRs (who are actually being very helpful) getting a woodruff key and PAS adaptor that fits the latest batch of new AJP V8 water/Oil/PAS pump shafts they've had made is proving somewhat difficult. Over the weekend I fitted what seems to be the go to electric replacement pump from a Saxo and it works fine. The logic being I wont have to worry about any of the mechanical PAS stuff and I cna get the engine back in my Cerb. I began wondering about using an Arduino or similar to provide speed sensitive PWM control. I'm happy with the Arduino coding but where I could do with some advice is what to use to control the power supply to a motor that draws maybe 50A. Simply a MOSFET? Or is a driver required to get a useful PWM frequency, in which case has someone found a nice PCB with a driver IC that will cope?
Have you seen these?Due to ongoing faff with Parts for TVRs (who are actually being very helpful) getting a woodruff key and PAS adaptor that fits the latest batch of new AJP V8 water/Oil/PAS pump shafts they've had made is proving somewhat difficult. Over the weekend I fitted what seems to be the go to electric replacement pump from a Saxo and it works fine. The logic being I wont have to worry about any of the mechanical PAS stuff and I cna get the engine back in my Cerb. I began wondering about using an Arduino or similar to provide speed sensitive PWM control. I'm happy with the Arduino coding but where I could do with some advice is what to use to control the power supply to a motor that draws maybe 50A. Simply a MOSFET? Or is a driver required to get a useful PWM frequency, in which case has someone found a nice PCB with a driver IC that will cope?
I Like
https://www.ebay.com/itm/144295678709?_trkparms=am...
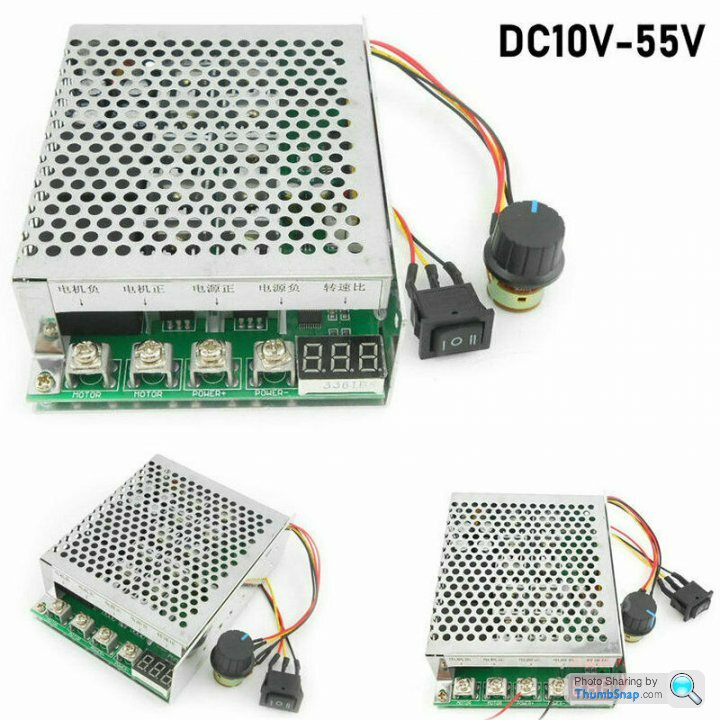
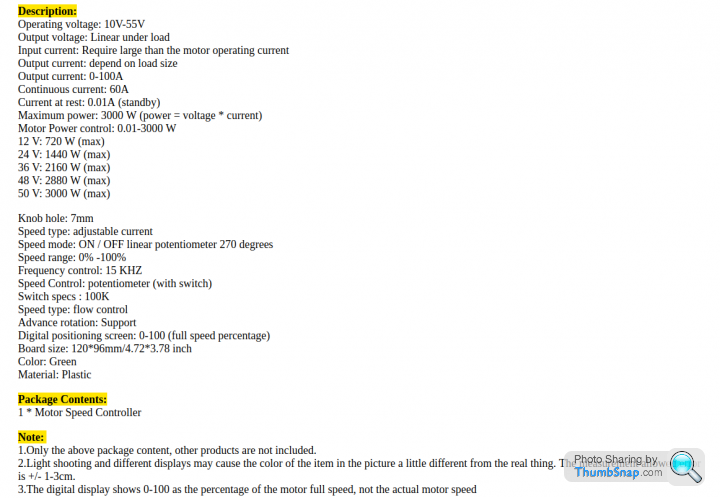
Max_Torque said:
hoofa said:
It’s not a corsa column, dce electronics epas and epas controller , seams fine to me and better feel than the pas rack. Each to their own I guess
DCE took the TRW corsa D EPAS column and got a copy made, that's what there system is!Edited by hoofa on Monday 10th January 22:23
Edited by hoofa on Monday 10th January 22:24
Thanks everyone for the contributions. I found a previous post from Max_Torque which puts the Saxo pump at 450W so 1 of those motor controllers could work. I'll have to think about where to fit it as it it's obviously not designed for an engine bay. I suppose I should think about the consequences of failure too.
GreenV8S said:
You seem to be taking on quite a challenging design problem to avoid what sounds like a trivial machining job.
True, sort of. The EHPAS conversion has been pretty popular on V8 Cerbs if the PAS woodruff key fails so I'm mildly surprised noone has controlled the power supply to the pump before. It also has the bonus of reducing the load on the woodruff key on the front of the shaft. If that one shears you lose the oil and water pumps as well and it's an engine out job to change that one.I did the first electric pump conversion on a cerb so I'll throw my 2p in
the reason I've never looked into varying the assistance is that it's not required in my opinion. The system by its very nature is variable in assistance ..
put little effort into the steering wheel (such as when travelling at speed) and the valving opens little giving not a lot of assistance
put a lot of effort into the steering wheel (such as at low speed / parking) and the valving opens more giving more assistance.
I don't deal with modern cars so can't comment if varying the speed of a hydraulic motor is something which happens in the mainstream but even my relatively modern vw has a mechanical pump, some pipes, and no obvious way of variably controlling system pressure from the pump.
It's over 20 years since I did the first electric pump conversions onto chims/griffs , and swapping out the cerb mechanical pump for electric* .. in none of those years has anyone ever asked me to vary the assistance somehow.
the reason I've never looked into varying the assistance is that it's not required in my opinion. The system by its very nature is variable in assistance ..
put little effort into the steering wheel (such as when travelling at speed) and the valving opens little giving not a lot of assistance
put a lot of effort into the steering wheel (such as at low speed / parking) and the valving opens more giving more assistance.
I don't deal with modern cars so can't comment if varying the speed of a hydraulic motor is something which happens in the mainstream but even my relatively modern vw has a mechanical pump, some pipes, and no obvious way of variably controlling system pressure from the pump.
It's over 20 years since I did the first electric pump conversions onto chims/griffs , and swapping out the cerb mechanical pump for electric* .. in none of those years has anyone ever asked me to vary the assistance somehow.
- I like to think the factory looked at my conversion and copied it for their own models later on, even using the same saxo pump
spitfire4v8 said:
I did the first electric pump conversion on a cerb so I'll throw my 2p in
the reason I've never looked into varying the assistance is that it's not required in my opinion. The system by its very nature is variable in assistance ..
put little effort into the steering wheel (such as when travelling at speed) and the valving opens little giving not a lot of assistance
put a lot of effort into the steering wheel (such as at low speed / parking) and the valving opens more giving more assistance.
I don't deal with modern cars so can't comment if varying the speed of a hydraulic motor is something which happens in the mainstream but even my relatively modern vw has a mechanical pump, some pipes, and no obvious way of variably controlling system pressure from the pump.
It's over 20 years since I did the first electric pump conversions onto chims/griffs , and swapping out the cerb mechanical pump for electric* .. in none of those years has anyone ever asked me to vary the assistance somehow.
Thanks Jools. If Cerbs you've converted drive OK I won't bother with PWM control.the reason I've never looked into varying the assistance is that it's not required in my opinion. The system by its very nature is variable in assistance ..
put little effort into the steering wheel (such as when travelling at speed) and the valving opens little giving not a lot of assistance
put a lot of effort into the steering wheel (such as at low speed / parking) and the valving opens more giving more assistance.
I don't deal with modern cars so can't comment if varying the speed of a hydraulic motor is something which happens in the mainstream but even my relatively modern vw has a mechanical pump, some pipes, and no obvious way of variably controlling system pressure from the pump.
It's over 20 years since I did the first electric pump conversions onto chims/griffs , and swapping out the cerb mechanical pump for electric* .. in none of those years has anyone ever asked me to vary the assistance somehow.
- I like to think the factory looked at my conversion and copied it for their own models later on, even using the same saxo pump
spitfire4v8 said:
I did the first electric pump conversion on a cerb so I'll throw my 2p in
the reason I've never looked into varying the assistance is that it's not required in my opinion. The system by its very nature is variable in assistance ..
put little effort into the steering wheel (such as when travelling at speed) and the valving opens little giving not a lot of assistance
put a lot of effort into the steering wheel (such as at low speed / parking) and the valving opens more giving more assistance.
I don't deal with modern cars so can't comment if varying the speed of a hydraulic motor is something which happens in the mainstream but even my relatively modern vw has a mechanical pump, some pipes, and no obvious way of variably controlling system pressure from the pump.
It's over 20 years since I did the first electric pump conversions onto chims/griffs , and swapping out the cerb mechanical pump for electric* .. in none of those years has anyone ever asked me to vary the assistance somehow.
As i've mentioned many times, because PAS is open spool, if you are not actually putting in a steering torque then there is no pressure in the system, the fluid is just being pump round and round in circles, effectively doing nothing. Yes, there are some losses caused by the hydrualic circuit losses, ie friction of the fluid traveling through the pipes etc, but for an aftermarket vehicle i don't think i'd worry about those.the reason I've never looked into varying the assistance is that it's not required in my opinion. The system by its very nature is variable in assistance ..
put little effort into the steering wheel (such as when travelling at speed) and the valving opens little giving not a lot of assistance
put a lot of effort into the steering wheel (such as at low speed / parking) and the valving opens more giving more assistance.
I don't deal with modern cars so can't comment if varying the speed of a hydraulic motor is something which happens in the mainstream but even my relatively modern vw has a mechanical pump, some pipes, and no obvious way of variably controlling system pressure from the pump.
It's over 20 years since I did the first electric pump conversions onto chims/griffs , and swapping out the cerb mechanical pump for electric* .. in none of those years has anyone ever asked me to vary the assistance somehow.
- I like to think the factory looked at my conversion and copied it for their own models later on, even using the same saxo pump
The OE's control the EHPAS pump speed because:
1) They are chasing every last watt of loss
2) they care about NVH (elecy pumps are noisy, especially with stop start, menaing the engine could be off)
3) they care about pump life, the more it runs, the faster (in time) it wears out
For an aftermarket vehicle i'm not sure i care enough about any of those things to make it worth the effort and potential un-reliability to add such measures?
Gassing Station | General TVR Stuff & Gossip | Top of Page | What's New | My Stuff