Welding for power steering
Discussion
I have finally started converting my S2 to power steering, drawing on the wisdom of this site and Facebook. I would be grateful for advice how to join the top end Granada UJ to the lower end Subaru UJ. I also need to extend the length. I am using 25.4 mm OD x 5mm WT cold drawn seamless tube. Which is a slip fit on the 15.2mm Subaru shaft and can be opened out at the other end to 16mm to give a snug slip fit on the Granada shaft. I don’t fancy relying on just a fillet weld round the end of the tube. I would like some arrangement which can still turn the steering even if the weld fails.
I have considered drilling 10 mm holes in the tube and using these to plug weld to the shaft (as well as welding round the end) or cutting a V into the end of the pipe and using this to fillet weld to the shaft.
Does anyone have an opinion on these options or a better idea? All thoughts very gratefully received.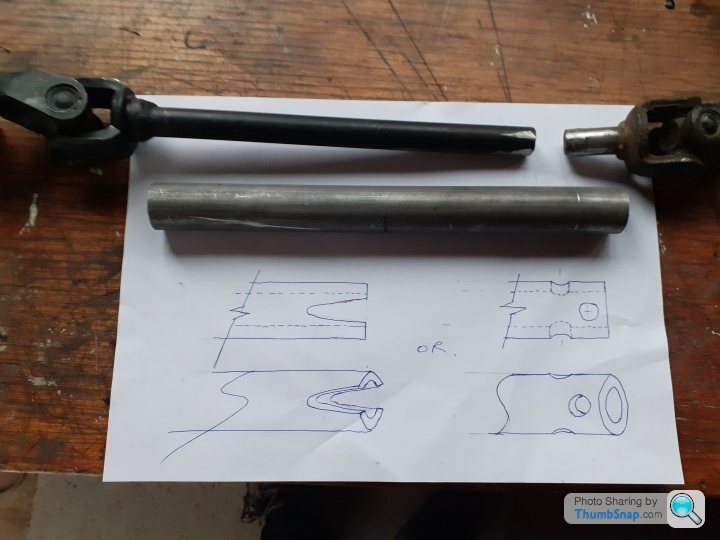
I have considered drilling 10 mm holes in the tube and using these to plug weld to the shaft (as well as welding round the end) or cutting a V into the end of the pipe and using this to fillet weld to the shaft.
Does anyone have an opinion on these options or a better idea? All thoughts very gratefully received.
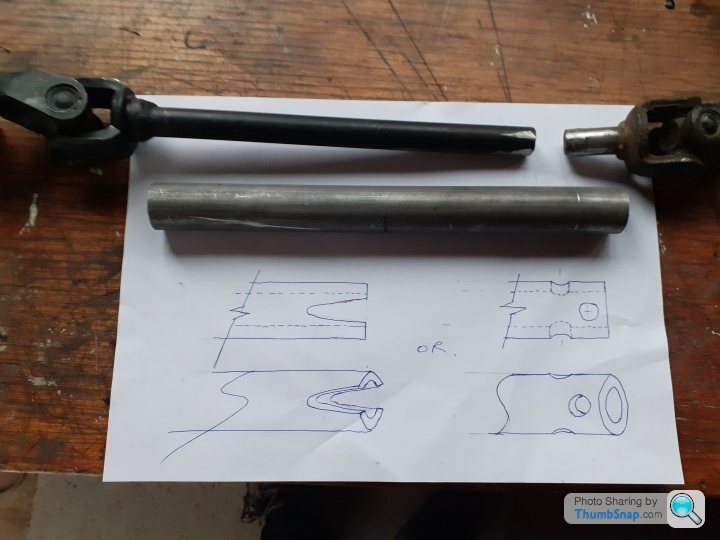
8mm pin but drilled off centre so it just takes a notch out of the shaft, Should the weld fail which it obviously shouldn't if you proper penetration, the pin will be enough to stop saft spinning but won't significantly weaken the shaft.
personally I wouldn't use the Subaru UJ. I would (did) use the Ford Ka joint as others have done and grind, machine, file the pinion shaft to a matching 17mm hex.
Thank you for the idea of a cotter arrangement, I hadn't thought of that. I decided to use the Subaru UJ because I had it with the rack and because, from reading other peoples experiences, shortening the pinion shaft to fit the Ka UJ makes it clash with the chassis requiring "percussive adjustment". I am having to work in a very confined space with nowhere to put any parts I remove such as the bonnet or exhaust etc, so trying to get room to swing a hammer would be a problem. The last thing that decided me is that a friend of mine is a coded welder working on high pressure pipework. So I will have confidence in the weld.
If you have a professional welder doing the job then the tubular section will be the strongest part, far stronger than the solid section. He will ensure it isn't overheated while welding. He will probably want to do an annular weld at the joint and 3 plug welds through each overlap. I would NOT introduce anything which could potentially be a stress raising point.
Have a look at a modern collapsible column and how they are constructed.
I just looked in the Car Builder Solutions catalogue to see if they had anything about adjusting steering columns and found this, no personal experience but may be of interest to someone:
https://www.carbuilder.com/uk/collapsible-steering...
Have a look at a modern collapsible column and how they are constructed.
I just looked in the Car Builder Solutions catalogue to see if they had anything about adjusting steering columns and found this, no personal experience but may be of interest to someone:
https://www.carbuilder.com/uk/collapsible-steering...
Hi, you could use the same sliding clamp as on the steering of many cars, plus on the vixen. The shaft has a flat machined on, the tube has a corresponding slot, then a clamp goes over the both. Bit like a cotter pin in principle, but parts are available. Once clamped, a bolt tightens onto the flat.
Drilling a hole through not good imho.
But, worth bearing in mind that weld is holding your whole chassis and suspension together. It is extremely well understood old tech. So, if you know the exact length you want I wouldn’t be scared of weld, let a professional do it but it will work.
If you want variable length use the sliding fit as described.
Best
Nic
Drilling a hole through not good imho.
But, worth bearing in mind that weld is holding your whole chassis and suspension together. It is extremely well understood old tech. So, if you know the exact length you want I wouldn’t be scared of weld, let a professional do it but it will work.
If you want variable length use the sliding fit as described.
Best
Nic
Gassing Station | S Series | Top of Page | What's New | My Stuff