Wide bonnet conversion ?
Discussion
Hi Guys...
Before I ask my question, can I firstly state that I do understand that suppliers, traders, and the great professional support network that Tvr has, need to make a living, & charge accordingly for their products and services.
My question is not asking for any details or their specific product(s).
What I am asking is simple....
Whilst I am plodding my way through of the total restoration of my S3, I might as well do a 'wide open bonnet' conversion.
Fact based on this photo...
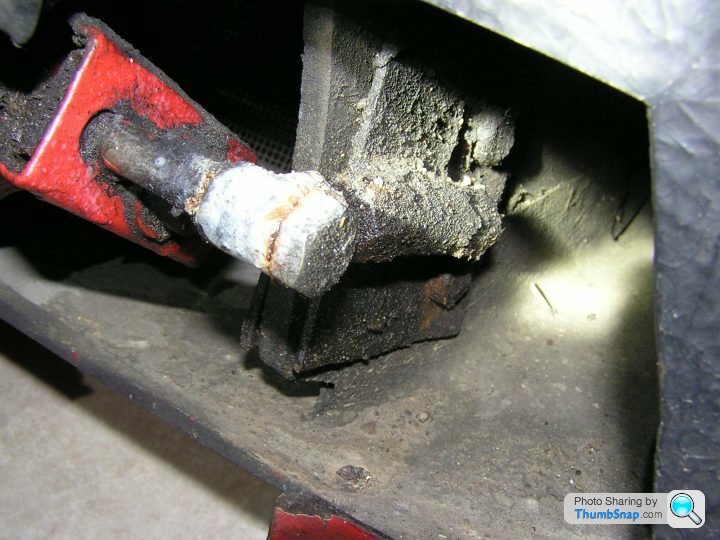
The pivot point can be clearly seen to be just inside the wheel arch (looking fore/aft) and approx level with the lower valance (looking up/down). So its no wonder that any bodywork in front of that pivot point will rotate down to the ground.
From the few wide bonnet photos I have seen on PH, the principal of the conversion is simply to move the pivot point.
See the example below...
As I said above, I don't want anyone to give me any design detail(s) of one (or more) of specific designs of the required support metalwork.
All I am asking is, if anyone is prepared to offer a basic diagram/drawing giving where the new pivot point is ?
Such as...That on the plywood board, from the side view. Something like 3" from the back edge, and 2" above the inside of the valance/plywood bonded joint.
Or a photo would do, with a rule, giving a scale.
I know it won't be that accurate, plus there's all of the S build variables to consider.
I've thought about that, and I think I can build in some adjustability.
Cheers in anticipation. TerryB
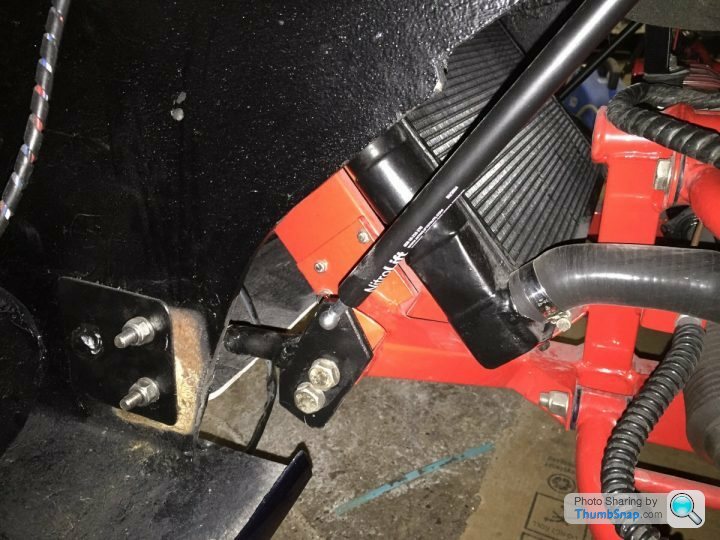
Before I ask my question, can I firstly state that I do understand that suppliers, traders, and the great professional support network that Tvr has, need to make a living, & charge accordingly for their products and services.
My question is not asking for any details or their specific product(s).
What I am asking is simple....
Whilst I am plodding my way through of the total restoration of my S3, I might as well do a 'wide open bonnet' conversion.
Fact based on this photo...
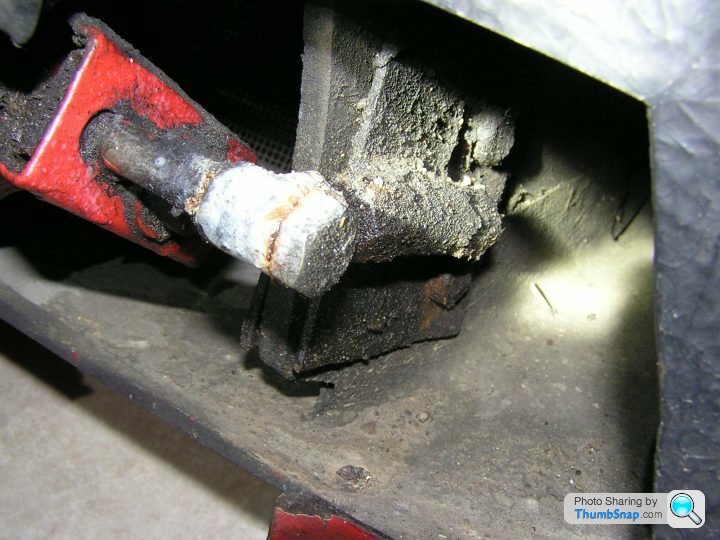
The pivot point can be clearly seen to be just inside the wheel arch (looking fore/aft) and approx level with the lower valance (looking up/down). So its no wonder that any bodywork in front of that pivot point will rotate down to the ground.
From the few wide bonnet photos I have seen on PH, the principal of the conversion is simply to move the pivot point.
See the example below...
As I said above, I don't want anyone to give me any design detail(s) of one (or more) of specific designs of the required support metalwork.
All I am asking is, if anyone is prepared to offer a basic diagram/drawing giving where the new pivot point is ?
Such as...That on the plywood board, from the side view. Something like 3" from the back edge, and 2" above the inside of the valance/plywood bonded joint.
Or a photo would do, with a rule, giving a scale.
I know it won't be that accurate, plus there's all of the S build variables to consider.
I've thought about that, and I think I can build in some adjustability.
Cheers in anticipation. TerryB
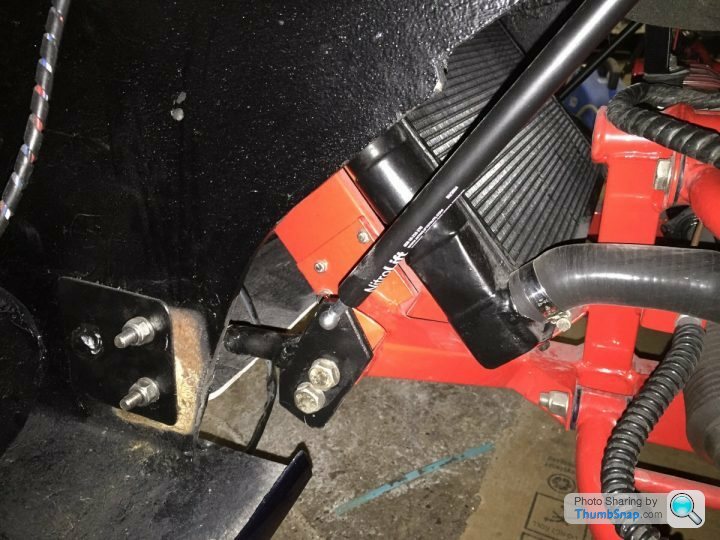
Hi Terry. Been working on this myself. I am not going to tell you how I have done it until it has proved itself on test however! So far however everything works as hoped. As you say the pivot is too far back. However a couple of conversions I have seen move it too far forward. Out with the drawing board then! I came up with the optimum position to be moving the pivot 59mm forward and 4mm higher! Far too accurate for a TVR I know. I had the dimensions from 2 other cars and there was little difference except for ride height.
With those dimensions, a pretty standard ride height and with a bonnet with the secondary lights underneath I get 90degree opening and good clearance both under the open bonnet and between the bonnet and chassis front cross member.
With those dimensions, a pretty standard ride height and with a bonnet with the secondary lights underneath I get 90degree opening and good clearance both under the open bonnet and between the bonnet and chassis front cross member.
greymrj said:
....With those dimensions, a pretty standard ride height and with a bonnet with the secondary lights underneath I get 90degree opening and good clearance both under the open bonnet and between the bonnet and chassis front cross member.
Did you have too cut anything out of the back edge of the valance to clear the chassis?No, it was one of my design criteria that I should not have to cut the bonnet. I get the bonnet vertical and clear. That is with a V8 bonnet. There does have to be a limiter of course to stop the bonnet going right over and wrecking the lot! I will upload one pic, I really dont want to do any more until it is back one the road and I can test that aspect properly. 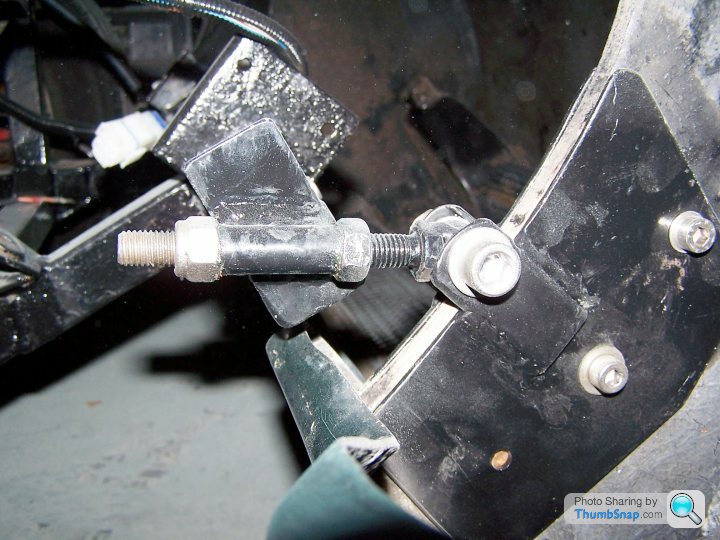
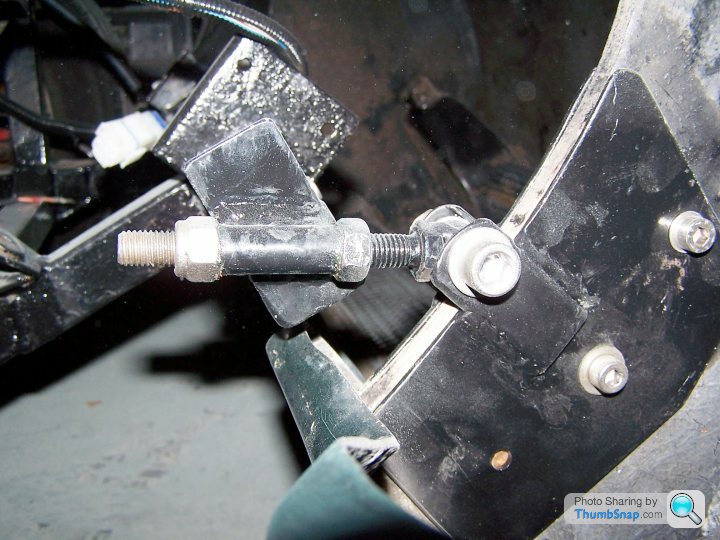
Did this a while ago. The pivot point was extended 180mm forward.
The plates that bolt to the ply web moved to the inside of the web and 100mm of the valance was removed to clear the new chassis extenders.
Capri tailgate struts limit bonnet opening and take some weight when near closed as the change in centres makes a surprising difference.
Photo taken from in front of the rad with bonnet open.
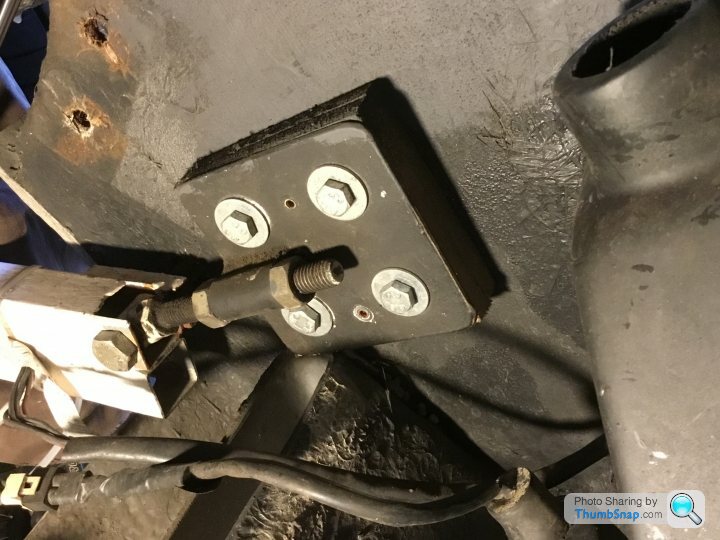
The plates that bolt to the ply web moved to the inside of the web and 100mm of the valance was removed to clear the new chassis extenders.
Capri tailgate struts limit bonnet opening and take some weight when near closed as the change in centres makes a surprising difference.
Photo taken from in front of the rad with bonnet open.
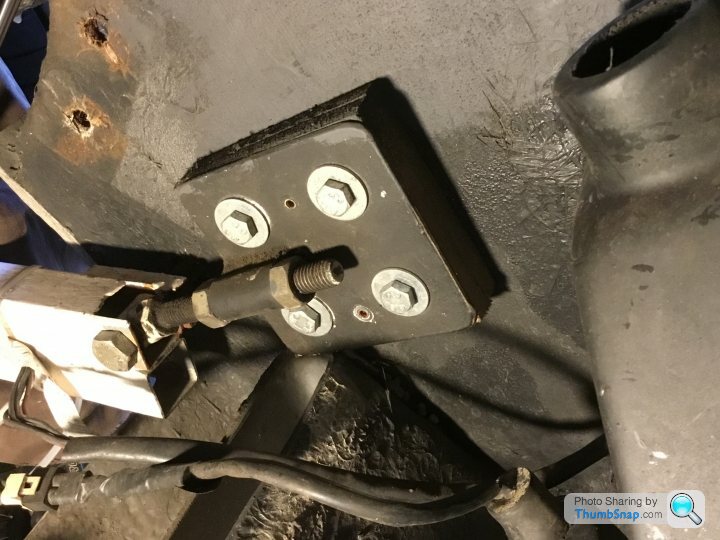
Edited by Alan461 on Monday 7th May 18:41
Hi guys...
Sorry for not using your real names, I don't know them unless it's added to your reply.
I really like the design and info provided by greymjr (great work), but many thanks to all of you.
I'm not quite ready to refit my bonnet yet (as part of my resto), but as it's been kindly stored away in my neighbours garage for 18mths, I thought its about time he had the space back (plus a few hints were recently dropped). So it might be a garden ornament for a couple of weeks... But dont tell her indoors !!!
I have started fabricating the new support ironwork, and bought a couple of rose joints etc. So once I have completed another couple of fabricating jobs on the Jag V6 engine, I can offer up the bonnet into the closed position, to get the new pivot point marked, then 'glue' the new ironwork together..... Tick √
TerryB.
Sorry for not using your real names, I don't know them unless it's added to your reply.
I really like the design and info provided by greymjr (great work), but many thanks to all of you.
I'm not quite ready to refit my bonnet yet (as part of my resto), but as it's been kindly stored away in my neighbours garage for 18mths, I thought its about time he had the space back (plus a few hints were recently dropped). So it might be a garden ornament for a couple of weeks... But dont tell her indoors !!!
I have started fabricating the new support ironwork, and bought a couple of rose joints etc. So once I have completed another couple of fabricating jobs on the Jag V6 engine, I can offer up the bonnet into the closed position, to get the new pivot point marked, then 'glue' the new ironwork together..... Tick √
TerryB.
I have now completed making, and fitted my new iron ware (as per greymjr style) but with the pivot point just encroaching into the ply boarding (it just worked out that way). Trust me, to do it on one of the hottest days this year, when cutting, grinding, & welding isn't a fun thing to do. I have yet to fine tune it for looks & locking, but that'll be much later on. I think I will be cutting about 10mm off the lower valance, but just where the square section chassis short tubes are (what the hinge pin used to secure to), as it just hits them. After that I'll add a hydraulic strut as a front stop. Got a pair somewhere in my chaotic garage !!
For anyone contemplating doing a conversion, just be aware (as if you didn't already know) that all cars are slightly different, in this case where the ply boarding is, so no matter how skilled you make a design, you had better build in some form of adjustability !!
TerryB
For anyone contemplating doing a conversion, just be aware (as if you didn't already know) that all cars are slightly different, in this case where the ply boarding is, so no matter how skilled you make a design, you had better build in some form of adjustability !!
TerryB
Yes, all done, that's excepting a coat of blue paint !
Like you (greymrj) all I did in effect was to flip the assembly 180o. So now the tube is welded to a right angle piece of unistrut, which in turn bolts to the original thin wall box section chassis extension. That gives the up/down adjustments. The long threaded hinge pin gives the fore/aft adjustments.
It was 50/50 planning/good luck as to where the lower bonnet vent edge ended up in relation to the floor. It would just about touch the floor if it were uncontrolled. So I happened to have a new pair of surplus hydraulic boot struts that I fitted. Their maximum length now dictates the full open position. But when the bonnet is closed and the release catch is pulled, the bonnet would shoot open propelled by the struts at some speed. So I have now fitted a short dog lead strap safety tether....
Just in case I forget to hold the bonnet !
T.
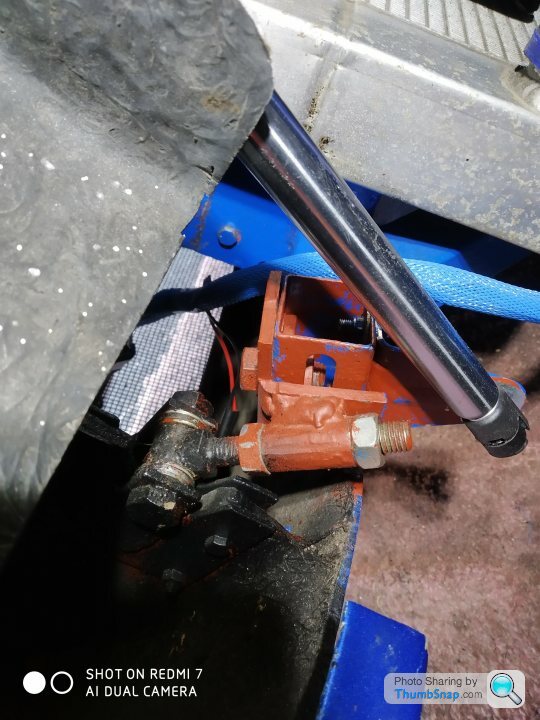
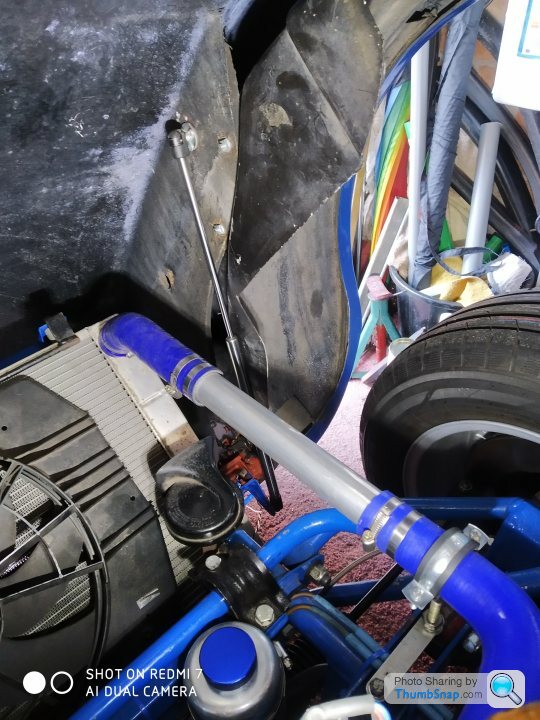
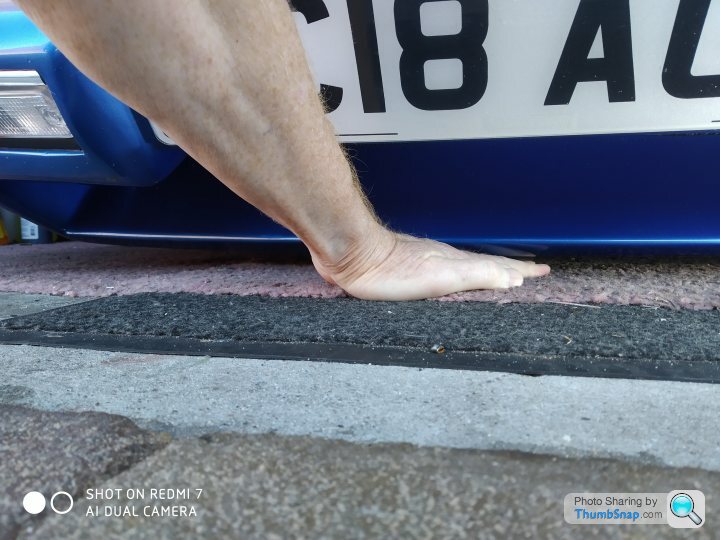
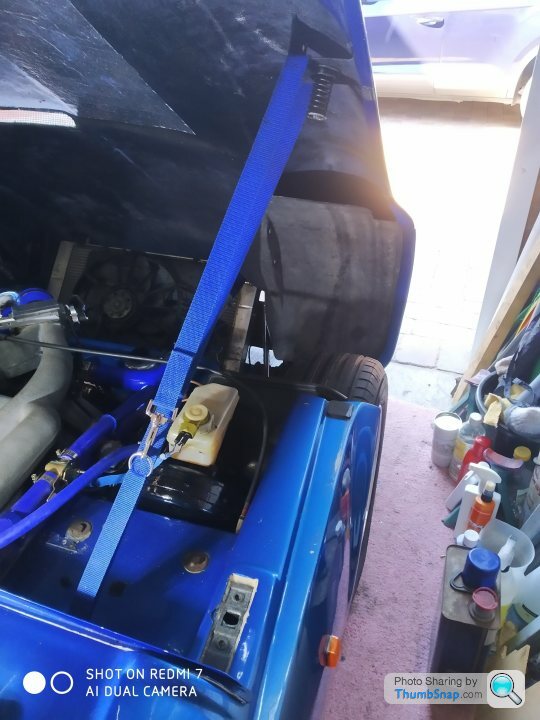
Like you (greymrj) all I did in effect was to flip the assembly 180o. So now the tube is welded to a right angle piece of unistrut, which in turn bolts to the original thin wall box section chassis extension. That gives the up/down adjustments. The long threaded hinge pin gives the fore/aft adjustments.
It was 50/50 planning/good luck as to where the lower bonnet vent edge ended up in relation to the floor. It would just about touch the floor if it were uncontrolled. So I happened to have a new pair of surplus hydraulic boot struts that I fitted. Their maximum length now dictates the full open position. But when the bonnet is closed and the release catch is pulled, the bonnet would shoot open propelled by the struts at some speed. So I have now fitted a short dog lead strap safety tether....
Just in case I forget to hold the bonnet !
T.
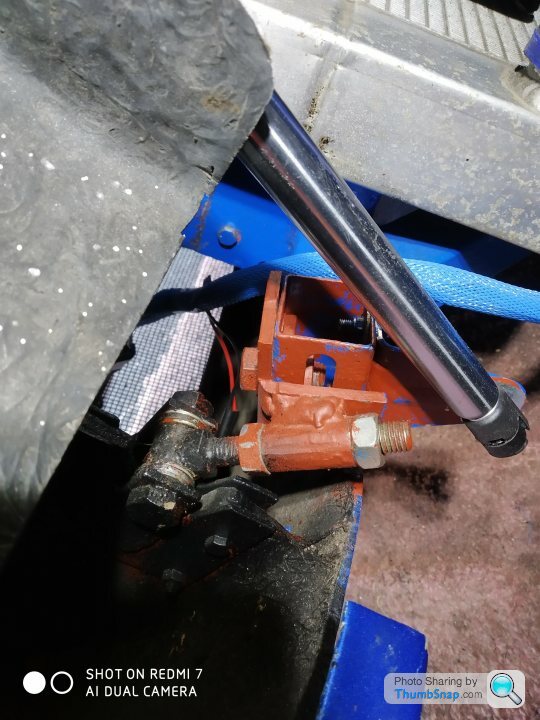
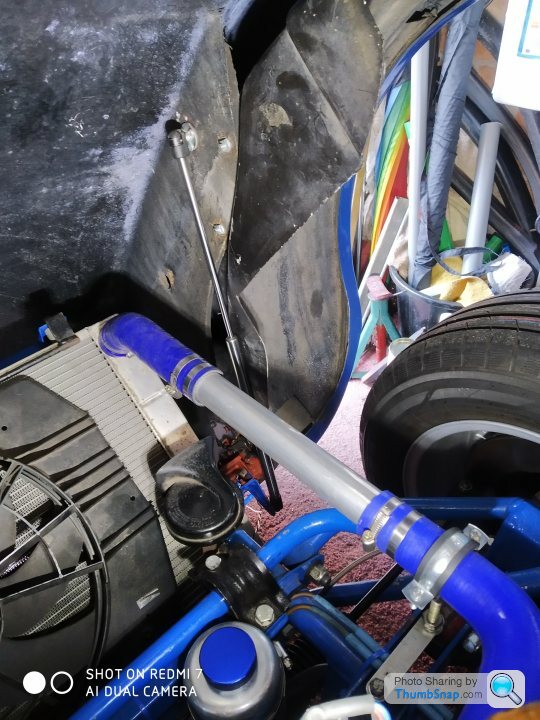
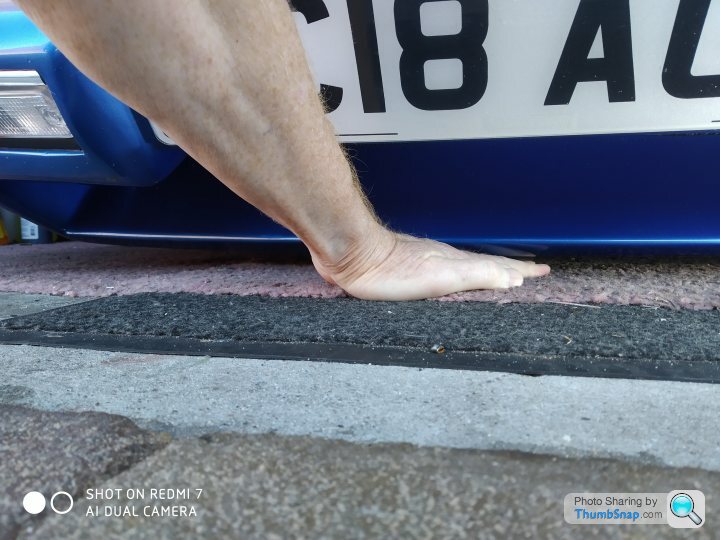
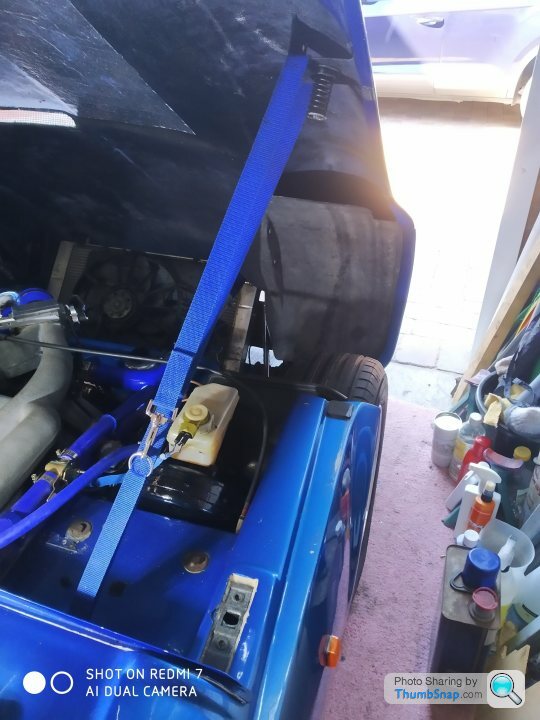
Edited by Blue 30 on Monday 20th September 11:13
Edited by Blue 30 on Monday 20th September 11:22
Yes, you are right. I had already thought of that but hesitating to 'kill' a pair of perfectly good struts. I'm sure there are some that have a gas release screw on them to reduce the push, but you only get one go at it. In fact I'm sure I have seen one with a shrader valve on it !
T.
T.
Yes, drill the strut, carefully! Although mine has a mechanical limiter at the hinge which prevents it opening too much that is not enough. In any wind there is too much stress on the bonnet so I used a drilled gas strut mounted to the original bonnet stay which clips into the original bonnet stay hole in the bonnet. I went a stage further, (belt and braces!) drilled the outer tube of the strut and welded a nut on and fitted a turnbuckle so I can set the bonnet at any height I like. I just happen to live in a windy spot and dont want to take any risks with that big bonnet.
There is one original point about your design that I like. You have fitted it to the OUTSIDE of the original tube, that does bring the mounting much closer, laterally, to the ply webs and reduces the bending moment on the ply. That, from an engineering point of view, is better than mounting inside that tube.
There is one original point about your design that I like. You have fitted it to the OUTSIDE of the original tube, that does bring the mounting much closer, laterally, to the ply webs and reduces the bending moment on the ply. That, from an engineering point of view, is better than mounting inside that tube.
TO LEAVE THE EXISTING MOUNTING TUBE ON OR NOT? THAT IS THE QUESTION!!!
Most wide open designs use the existing 'vertical' mounting tube as the mounting for the new hinge. I have argued that this compromises the design of the new hinge system. Why? The design engineer in me decided to express itself!! So here goes.
1. It has been argues that it is best to keep it as you might want to return to original. That seems to me to be a nonsense (sorry!). Once you have the wide open bonnet why on earth would you ever consider returning it to original? Given the varieties in details of pretty well all the S cars I know, is originality of bonnet mounts ever going to be an issue?
2. On many cars, especially earlier ones where the box section appears to have been thinner, that box section has become deformed in one way or another. Some are bent, some are worn, I have seen two cars where one has been repaired and they are no longer identical. An imperfect mounting tube compromises the hinge design even further.
3. The pivot on all successful designs has moved forward ( I believe it is optimal at 59-60mm forward and 10-12mm lower than original). To achieve that while using the original 'vertical' tube means going up, forward and back down again, three sides of a 'square' while only the lower side is necessary. That compromises design.
4. The original tube is NOT vertical, it slopes back, so if you use it for vertical adjustment any such adjustment also alters the longitudinal adjustment which then needs to be adjusted elsewhere. Not optimal design!
5. The biggest structural design failing of the original hinges is that they are too far from the ply web, that puts a significant bending moment on the ply web. Those bonnets are heavy and much of the weight is at the front, add then the dynamic load as the car hits bumps and the bending load on the ply is severe. Many people with the original mounts will find the bar holding the pivot has bent down, that clearly shows the bending load. Anyone who has seen one of the ply panels break has seen how it is bent as it is ripped out. So, to me, it seems that the optimal design must move the mounting such that there is little or no BENDING load on the ply. The optimum position then is directly IN LINE with the ply. It is VERY difficult to achieve that using the existing 'vertical' tube. The distance between the tubes is considerably smaller than the distance between the webs. So using those tubes makes it very difficult to get the pivot in the optimal position behind the webs.
I rest my case!! If there are any engineering flaws in that please feel free to enlighten me, as kindly as possible please.
Most wide open designs use the existing 'vertical' mounting tube as the mounting for the new hinge. I have argued that this compromises the design of the new hinge system. Why? The design engineer in me decided to express itself!! So here goes.
1. It has been argues that it is best to keep it as you might want to return to original. That seems to me to be a nonsense (sorry!). Once you have the wide open bonnet why on earth would you ever consider returning it to original? Given the varieties in details of pretty well all the S cars I know, is originality of bonnet mounts ever going to be an issue?
2. On many cars, especially earlier ones where the box section appears to have been thinner, that box section has become deformed in one way or another. Some are bent, some are worn, I have seen two cars where one has been repaired and they are no longer identical. An imperfect mounting tube compromises the hinge design even further.
3. The pivot on all successful designs has moved forward ( I believe it is optimal at 59-60mm forward and 10-12mm lower than original). To achieve that while using the original 'vertical' tube means going up, forward and back down again, three sides of a 'square' while only the lower side is necessary. That compromises design.
4. The original tube is NOT vertical, it slopes back, so if you use it for vertical adjustment any such adjustment also alters the longitudinal adjustment which then needs to be adjusted elsewhere. Not optimal design!
5. The biggest structural design failing of the original hinges is that they are too far from the ply web, that puts a significant bending moment on the ply web. Those bonnets are heavy and much of the weight is at the front, add then the dynamic load as the car hits bumps and the bending load on the ply is severe. Many people with the original mounts will find the bar holding the pivot has bent down, that clearly shows the bending load. Anyone who has seen one of the ply panels break has seen how it is bent as it is ripped out. So, to me, it seems that the optimal design must move the mounting such that there is little or no BENDING load on the ply. The optimum position then is directly IN LINE with the ply. It is VERY difficult to achieve that using the existing 'vertical' tube. The distance between the tubes is considerably smaller than the distance between the webs. So using those tubes makes it very difficult to get the pivot in the optimal position behind the webs.
I rest my case!! If there are any engineering flaws in that please feel free to enlighten me, as kindly as possible please.
For completeness I am adding the design Tony Currie has used on his car. It uses the original mounting tube and moves the pivot forward and down*. I have seen it and it is a very tidy solution . Although, from a stress design point of view, the pivots are still too far away from the ply (as discussed above) the mountings Tony has used on the ply do spread the load better are well mounted.
(* I haven't checked how far this design moves the pivot forward and down to see how well it relates to other successful designs)
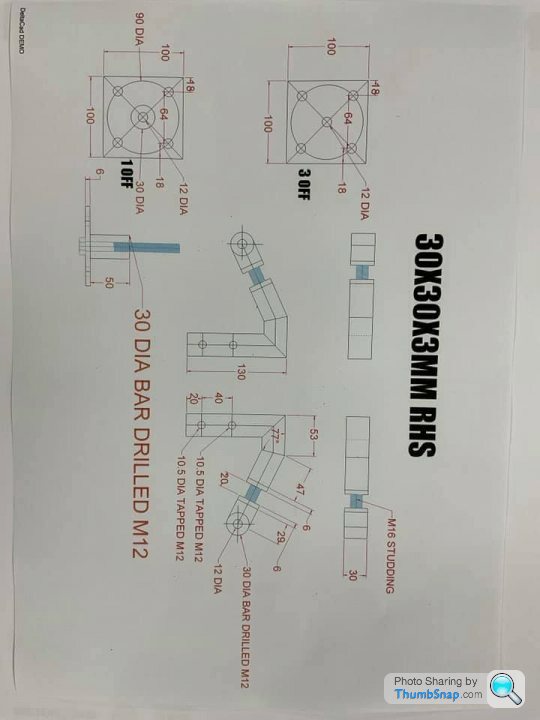
(* I haven't checked how far this design moves the pivot forward and down to see how well it relates to other successful designs)
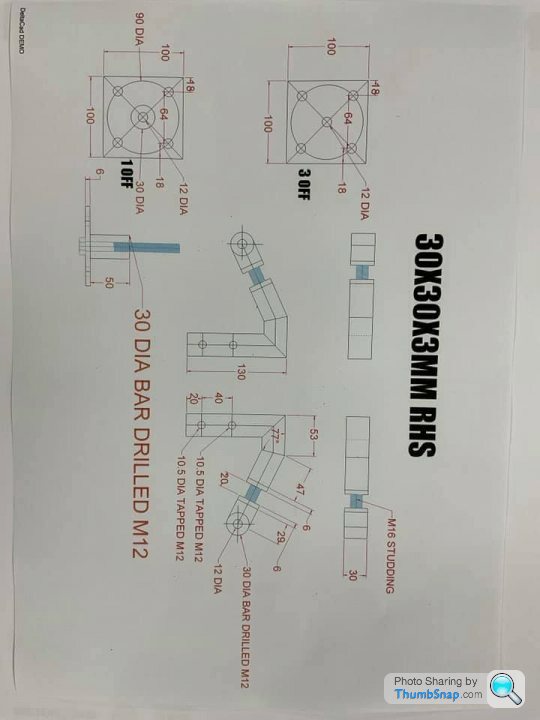
Gassing Station | S Series | Top of Page | What's New | My Stuff