They Said it Couldn't be Done...
Discussion
Well, they may still be right but looking at how the bits are fitting together it might just be possible. This is a section from an MGB folding hood and I can make it fit and tilt.
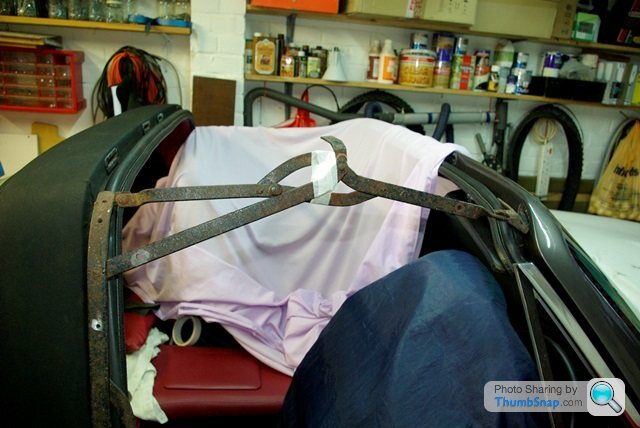
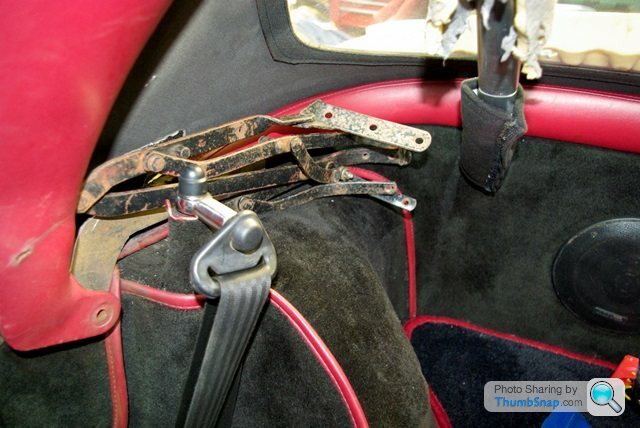
To move on to the next step I need two scrap targa panels (to make the header rail) and the moulding which fits inside the rear seam on the standard hood. Anyone got some scrap bits kicking about?
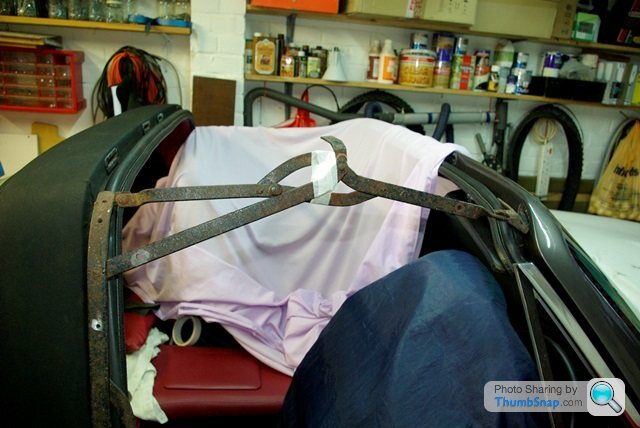
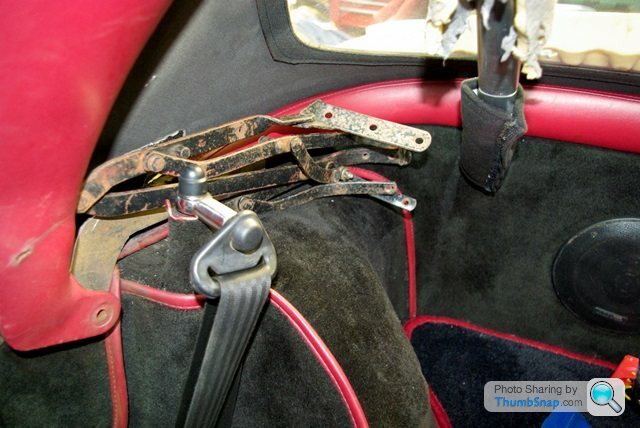
To move on to the next step I need two scrap targa panels (to make the header rail) and the moulding which fits inside the rear seam on the standard hood. Anyone got some scrap bits kicking about?
I would consider using a section of 2x1 or 4x2 wood, a jigsaw, plane and sander to make the front and rear bar patterns. Relatively cheap, can be filled and resanded as you go to correct mistakes and allows you to prove the concept. Once done can also then be used to make a mould for the fibreglass final product
mep12345 said:
I would consider using a section of 2x1 or 4x2 wood,...... Once done can also then be used to make a mould for the fibreglass final product
That's plan 'B', although I was going to use marine ply. I'm waiting for the local wood yard to have some off-cuts because it's something like £50 for an 8' x 4' sheet.TvrJohn said:
....Consider making these headers, or templates from steel strip following the profiles
Good idea, but beyond my skills I'm afraid. I've never done any glass fibre moulding either.I've worked out how to make a new upright bar and which part of the MGB frame to keep and bolted them together. I now need to put the driver's window back in to get the spacing correct. So, at the moment anyway, it's still looking more possible than not. The big question mark at the moment though is how low will the assembly sit once it's folded back.
v8s4me said:
That's plan 'B', although I was going to use marine ply. I'm waiting for the local wood yard to have some off-cuts because it's something like £50 for an 8' x 4' sheet.
For a "mock up" (no, that shouldn't be a c) I'd use the cheapest ply available (reclamation yard?), or as you shouldn't need a full sheet, depending how many mock ups you make, buy a sheet of 6mm ply and laminate it up to whatever thickness you need? Here is a Mazda MX5 hood frame in the car.
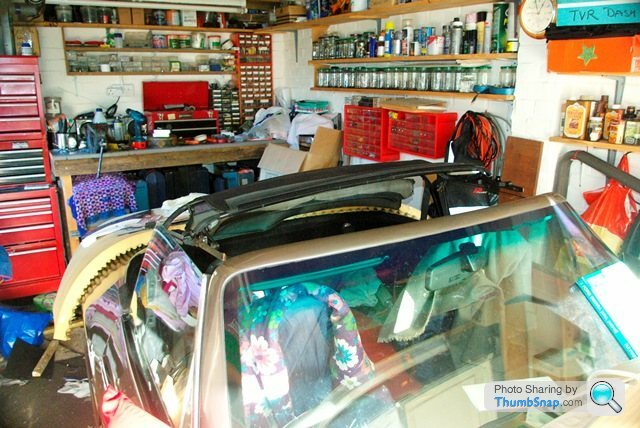
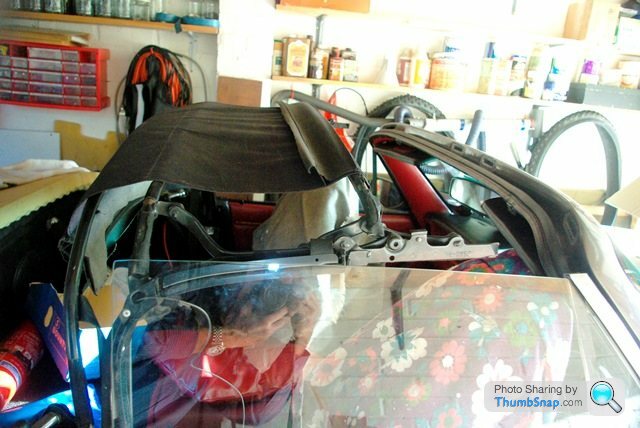
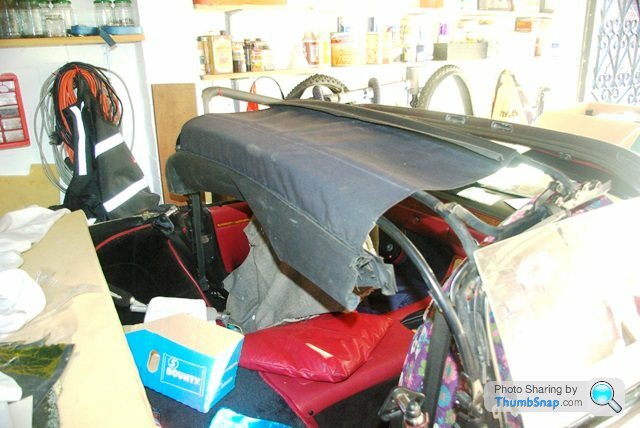
The key dimensions appear to be about right ie width, height and "reach" from the main hoop to the top of the screen and it does fold quite neatly onto the parcel shelf. However the design of the seat belt mounting posts will always make this part of the fit a compromise.
The problems are:
1. Getting the pivot point in the correct place.
2. Fabricating the header rail (yes still stuck on this one, lots of complicated curves).
3. Finding the moulding to attach the hood to the body (now I've got this off I can see it won't
be possible to make one from layers of thin ply because of its shape).
This does look a more practical solution than the MGB one I was trying earlier.
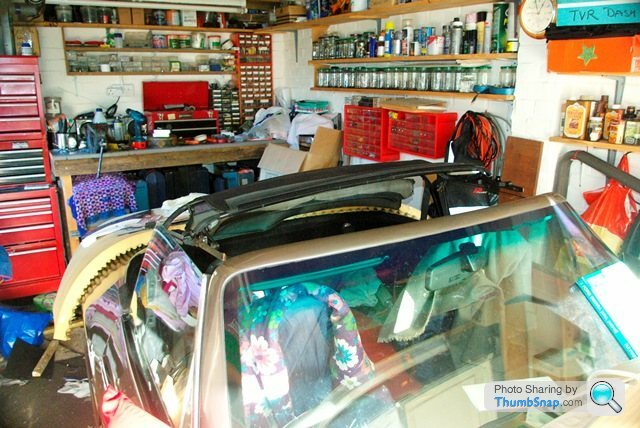
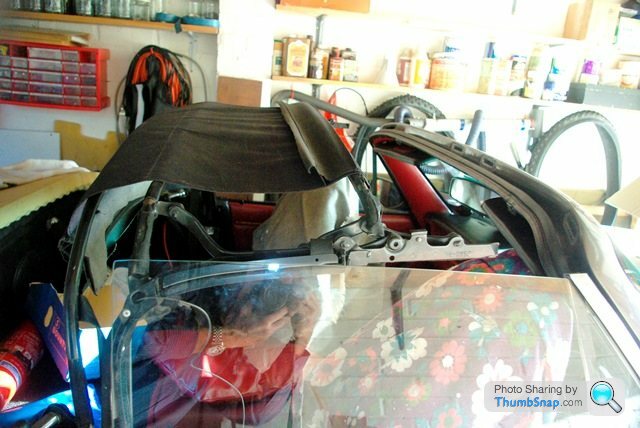
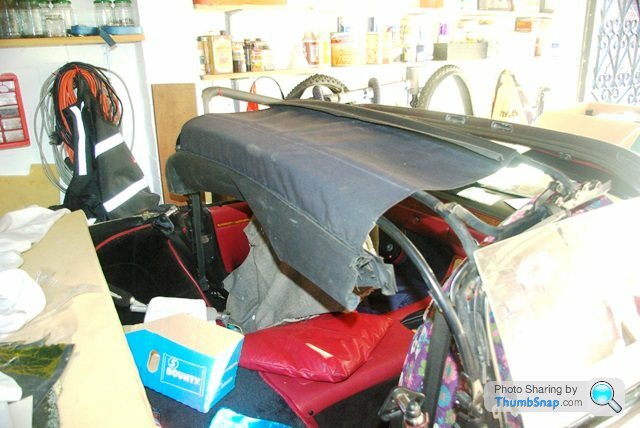
The key dimensions appear to be about right ie width, height and "reach" from the main hoop to the top of the screen and it does fold quite neatly onto the parcel shelf. However the design of the seat belt mounting posts will always make this part of the fit a compromise.
The problems are:
1. Getting the pivot point in the correct place.
2. Fabricating the header rail (yes still stuck on this one, lots of complicated curves).
3. Finding the moulding to attach the hood to the body (now I've got this off I can see it won't
be possible to make one from layers of thin ply because of its shape).
This does look a more practical solution than the MGB one I was trying earlier.
I've re-used the Mazda pivots, but reversed the sides, and moved the pivot point
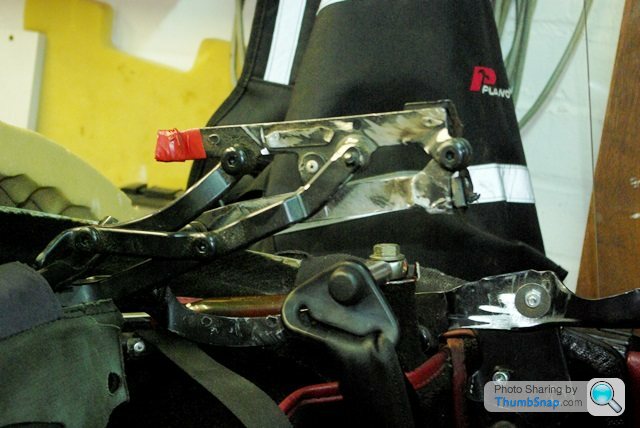
So now it goes up...
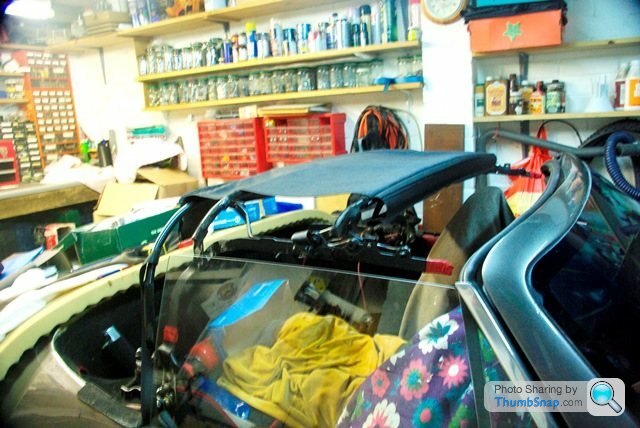
...and folds neatly back down again...
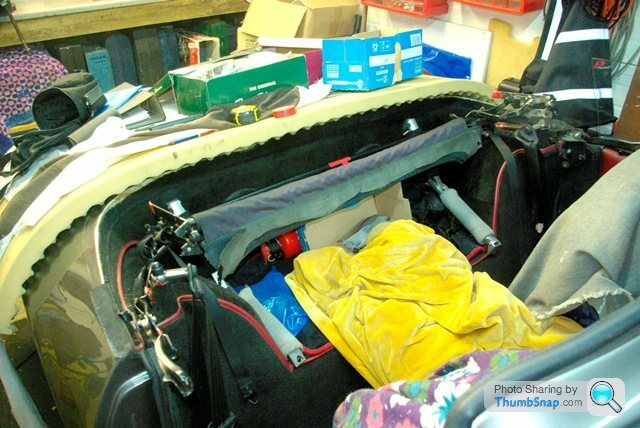
Now the appeal for help! Can anyone out there who is clever with glass fibre make me a continuous header rail, or make a mould so I can have a go at layering it up myself?
Thanks in advance.
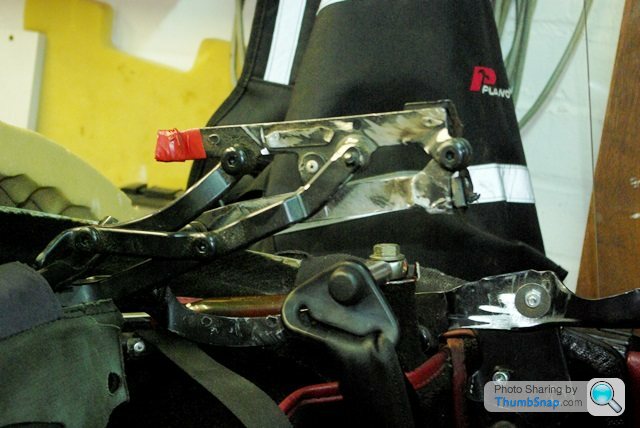
So now it goes up...
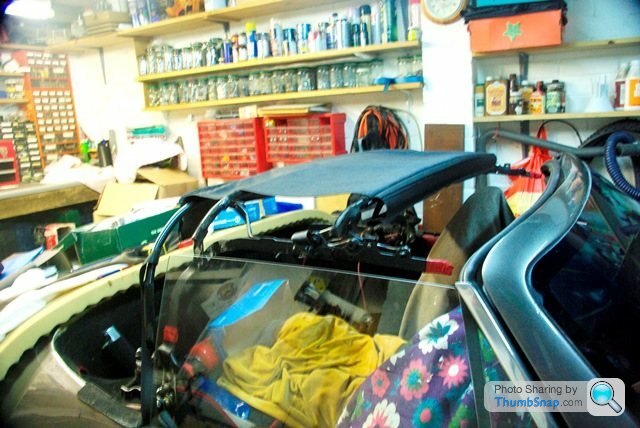
...and folds neatly back down again...
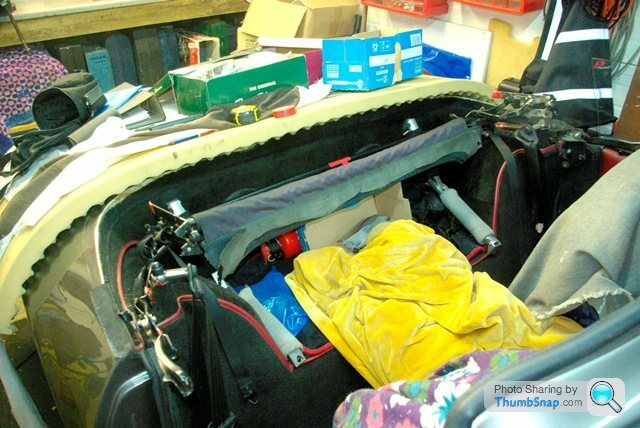
Now the appeal for help! Can anyone out there who is clever with glass fibre make me a continuous header rail, or make a mould so I can have a go at layering it up myself?
Thanks in advance.
Hi,
This is what I use to make small moulds, not cheep to make a good mould.
http://www.ebay.co.uk/itm/25mm-EXTRUDED-STYROFOAM-...
Alan
This is what I use to make small moulds, not cheep to make a good mould.
http://www.ebay.co.uk/itm/25mm-EXTRUDED-STYROFOAM-...
Alan
v8s4me said:
Now the appeal for help! Can anyone out there who is clever with glass fibre make me a continuous header rail, or make a mould so I can have a go at layering it up myself?
Thanks in advance.
Hi Joe,Thanks in advance.
Been puzzling over this.
Might sound crazy but you might try some bog for the header rail and use the car as a mould.
Take the rubber seal off the rear edge where it would meet the targas, mask off all the surfaces, pack out in leiu of the rubber seal and maybe put some tangs in the slots ready.
You might need something as a release agent, Maybe a couple of layers of tinfoil otherwise you might need a kango drill to get it free.
Put a layer of filler on, let it go off then add something structural like welding rods or strips of mesh as you build up the volume (Knitting needles might be good) and fill up to the final profile,
Take it off and sand back to suit.
If the thing hasn't enough strength it would do to take a mould from.
Feel free to ignore this nonsense, it's too cold in the garage and I haven't got a telly.
Failing this get some boatyard boys to help, they'll have so little work on this time of year you might get a very good price.
Enjoy

Well Santa has let me down badly! Bas
rd! I'll bet he's French. He says he's not bringing me a header rail so I'm fabricating one by laminating bits of plywood....
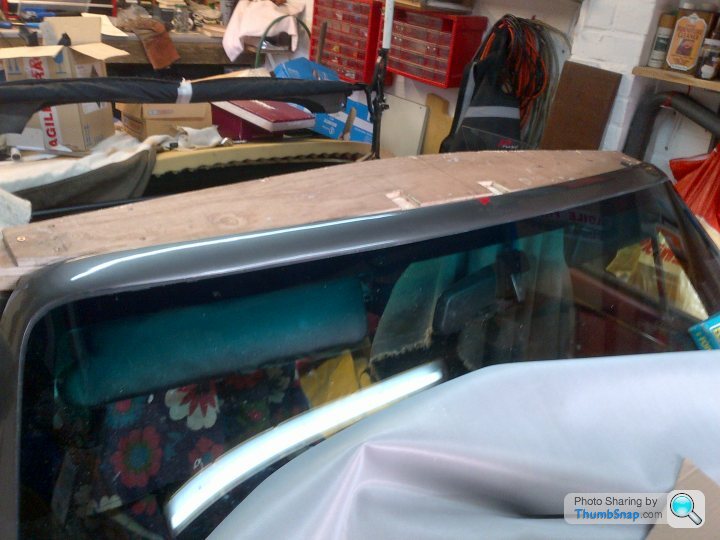
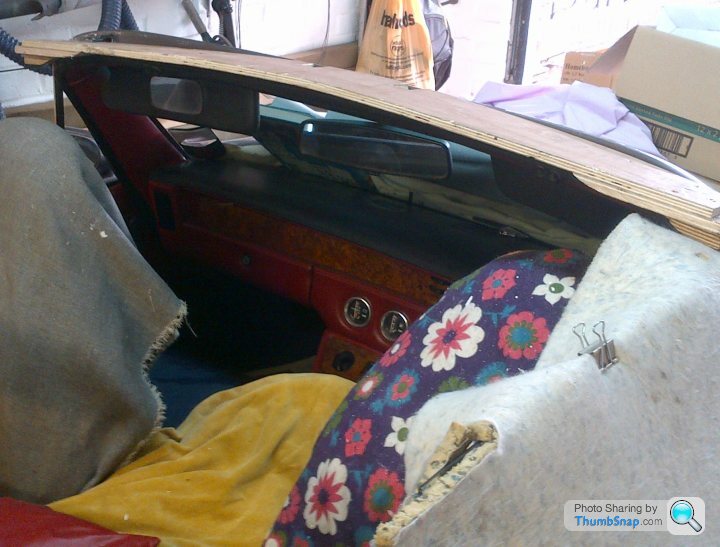
That's about all I can do now until the weekend because I'm asuming the neighbours probably wouldn't appreciate the sound of power tools over Christmas and the lady next door makes amazing fruit cake so I'm not jepordising that for anything. Yes, even my TVR!
Happy Christmas every one!

PS the very nice lady at Woolies has been incredibly helpful by sending me samples of door and window seals and I can thoroughly recommend them if you need anything like that.

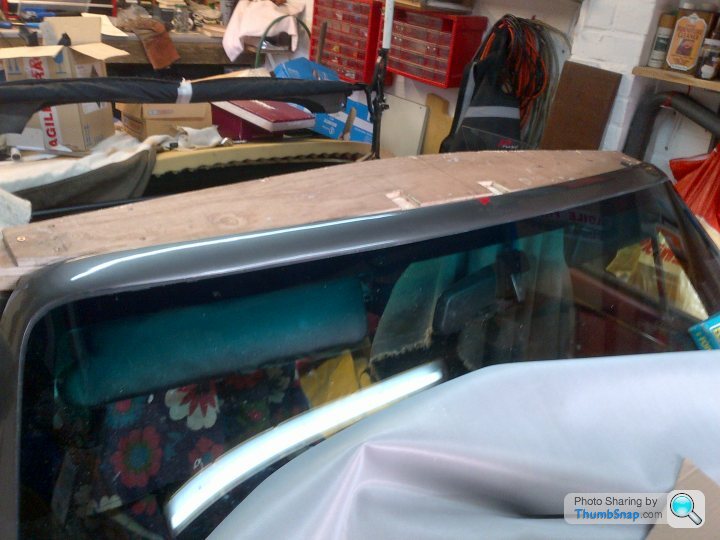
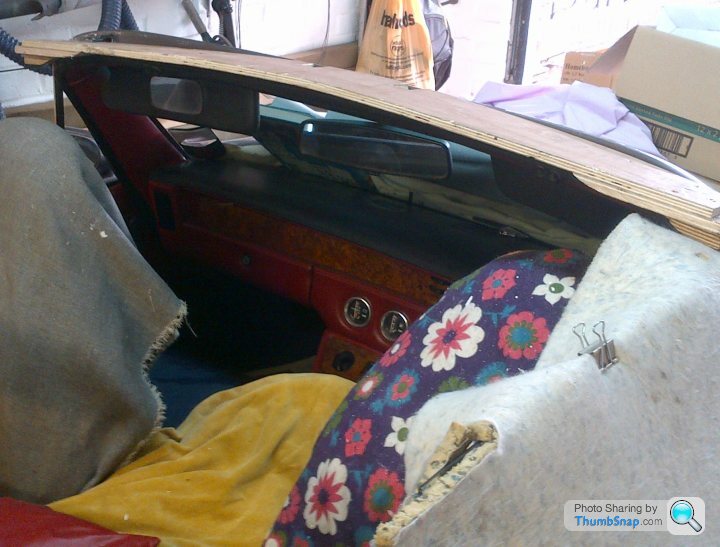
That's about all I can do now until the weekend because I'm asuming the neighbours probably wouldn't appreciate the sound of power tools over Christmas and the lady next door makes amazing fruit cake so I'm not jepordising that for anything. Yes, even my TVR!
Happy Christmas every one!


PS the very nice lady at Woolies has been incredibly helpful by sending me samples of door and window seals and I can thoroughly recommend them if you need anything like that.
A question for the glass-fibre wizards out there. Once I've got the profile I want can I cover it with a layer of GF matting just to smooth off the shape and give it a little bit of extra strength? It's going to be covered with the hood material so it doesn't have to be a mirror finish but it will have to be smooth and even so there are no unsightly lumps and bumps showing through the covering.
Gassing Station | S Series | Top of Page | What's New | My Stuff